How technology can lower utility and equipment costs
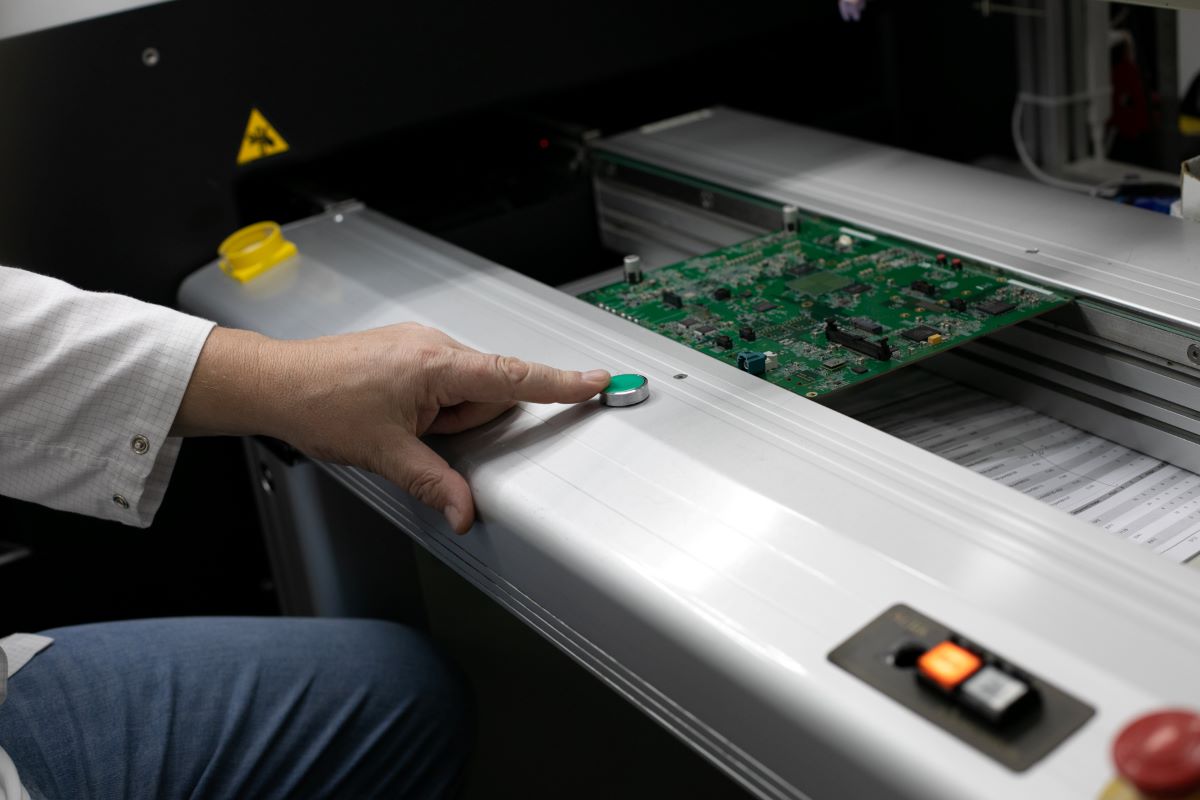
Electronics manufacturers can no longer afford to overlook the rising cost of energy consumption.
The electricity consumption of manufacturing equipment is rarely perceived as a major manufacturing cost—materials and components, manufacturing equipment costs, and production personnel salaries are traditionally considered the main cost concerns for a company. But is that true? Statistics show that in 2022, the cost of energy grew significantly, resulting in a higher cost of production for all products. Companies can no longer afford to ignore their electricity consumption.
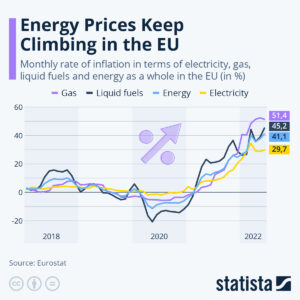
Multinational companies have a variety of options for optimization. They generally have a dedicated annual budget that allows them to invest in more efficient equipment—both with regards to productivity and to energy efficiency, which has become more of a focus given the rise in costs. SMBs, on the other hand, have a much smaller budget for investment and they can’t upgrade equipment as often as the larger companies. Without new equipment, they often struggle to optimize energy consumption.
Improving OEE is another way for SMBs to optimize utility costs. OEE is usually defined as the availability, performance and quality of the product.
- Availability is defined as run time within the total operating time.
- Performance is the actual speed of production, compared to the theoretical or planned speed.
- Quality is defined as the number of good products within the total number of products produced.
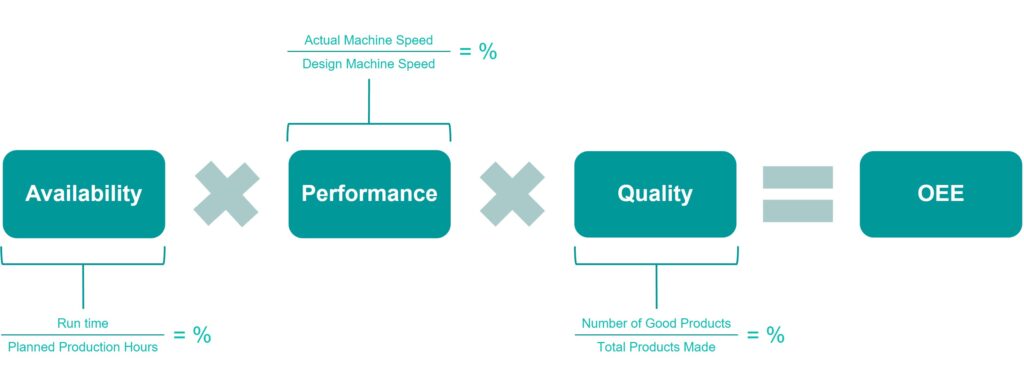
In the past, the factory OEE for a high-mix, low-to-medium-volume manufacturer was usually 20% to 25%. Yet last year, the OEE target for most manufacturers was 30% to 40%—an average increase of 10% to 16% in production efficiency.
How can SMBs meet these new targets and maintain quality and a reasonable profit margin, while still offering a competitive price for their products? One of the keys to improving OEE is tracking essential production data like changeover time, error time, production time, bottleneck equipment, material shortage and supply.
Since that translates into a tremendous amount of data, advanced MES (Manufacturing Execution System) software has become critical to collecting, managing and interpreting equipment data. It can also provide a deep analysis of all KPIs to help manufacturers make the right decisions quickly, and in doing so, improve OEE.
For example, changes in reflow oven energy consumption do not have a significant impact on the quality of a product. However, with a higher FPY, the energy consumption per unit shipped is lower. Similarly, if one manufacturing line becomes unavailable, fewer product units are produced while ancillary services in the factory (such as air conditioning and lighting) continue as usual. Therefore, the amount of energy consumed per product produced increases.
Advanced software like Opcenter Execution Electronics from Siemens allows manufacturers to access all information required from shopfloor production at a glance and pinpoint areas for improvement. They can see why certain material is blocking production or is not available, feed the production line in time with appropriate materials, identify the weak points in the changeover, find the root cause of a problem, and even conduct predictive maintenance. This allows them to identify problems in real time, and improve overall energy efficiency.
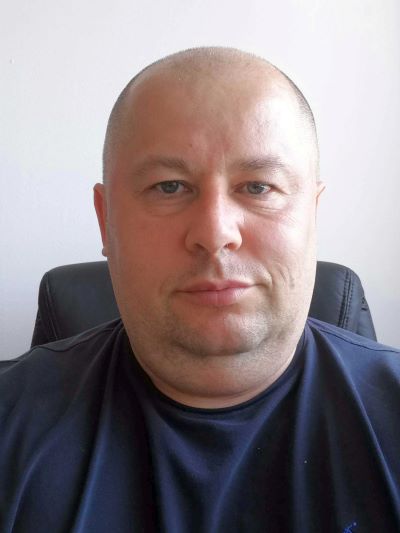
Marius Stepanescu is the Technical Director at ICCO EMT, a Romanian electronics manufacturer offering PCB production and assembly services in Europe and the Romanian market, where he leads the engineering team.