Standardized data exchange: Key to achieving a smart factory
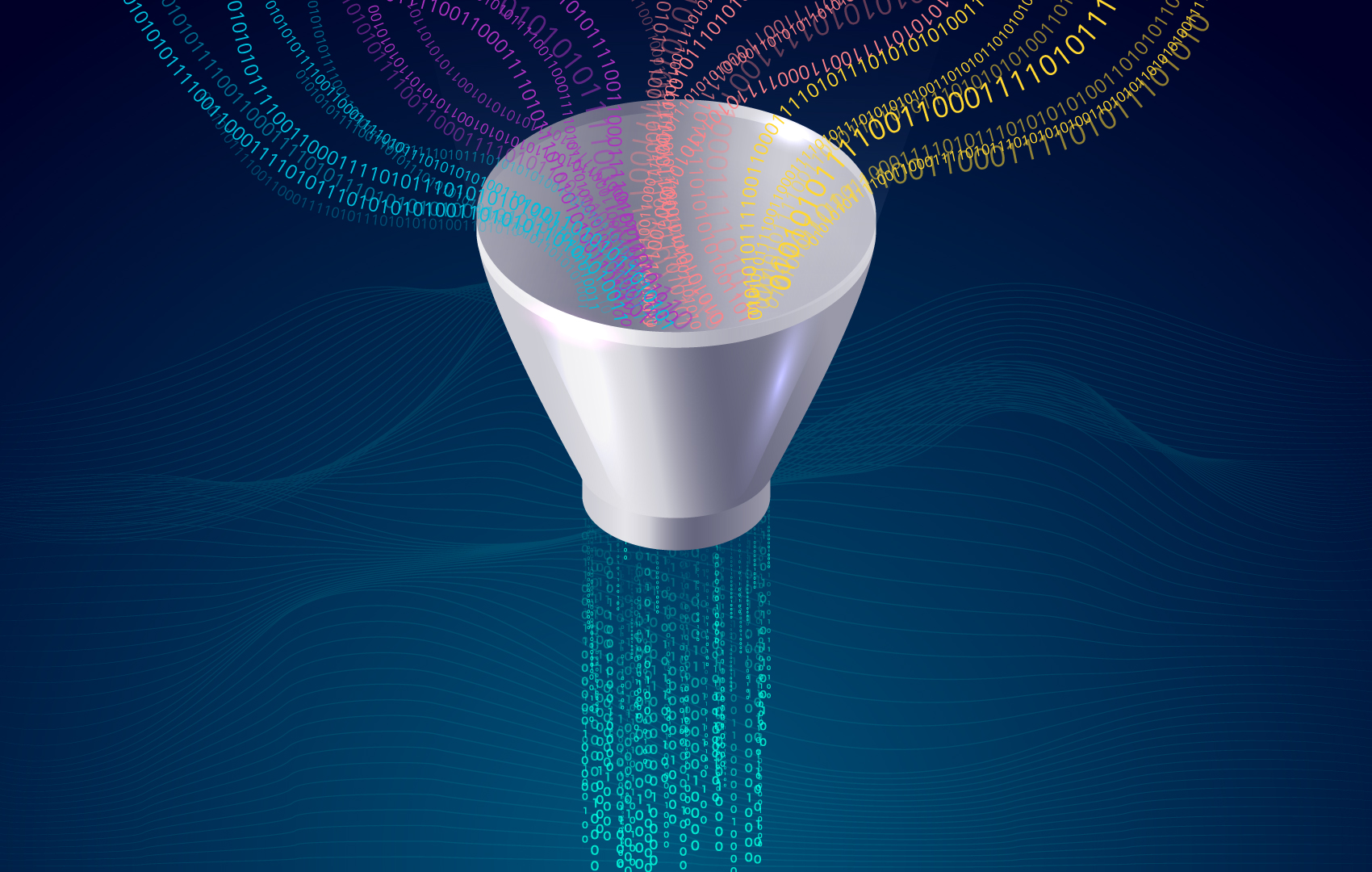
Learn about the technology infrastructure needed to unify data across PCB design, process engineering and production – explained in our new whitepaper.
Fast-churning market demand for new and differentiated products means increasing pressure to succeed with high-mix, low-volume manufacturing. Electronics manufacturers must respond quickly to product changes, while maintaining high quality and preserving their margins.
To achieve all that, they must be able to see and understand all data in real time, throughout the PCB assembly process. It’s a tall challenge, made even more challenging by inconsistent data formats, fragmented interfaces, data silos and lack of machine control.
That’s exactly where standardized data exchange can make the difference. An integrated data exchange and communication protocol for design, process and manufacturing is critical to meeting market demand and harnessing the breakthrough strengths of the smart factory. These strengths include the capacity to create a digital twin and accurately predict key performance characteristics before investing in physical prototypes and production assets.
ODB++ family: a complete digital twin of the electronics manufacturing flow
With the ODB++ family, Siemens has created the technology infrastructure to unify data throughout the PCB assembly process from design, to process engineering and production. Originally developed for intelligent design data, the ODB++ family has been expanded to provide a complete, end-to-end digital solution covering design, process and manufacturing information flows.
This new whitepaper breaks the data standardization issue down, explaining how to accurately predict key performance characteristics before investing in physical prototypes and production assets. It also details how to create a comprehensive digital twin for each stage of the PCB assembly process using existing software such as CAD, PCB assembly collateral and manufacturing IoT.
With standardized data formats, electronics manufacturers gain access to accurate, reliable, controlled data that helps to optimize new products and processes at an early stage and implement machine-agnostic process planning. They can collect and analyze real production and product performance data and feed it back into development, further optimizing their products and processes.