Advanced machine engineering – virtual machine simulation and commissioning (podcast transcript – part 3)
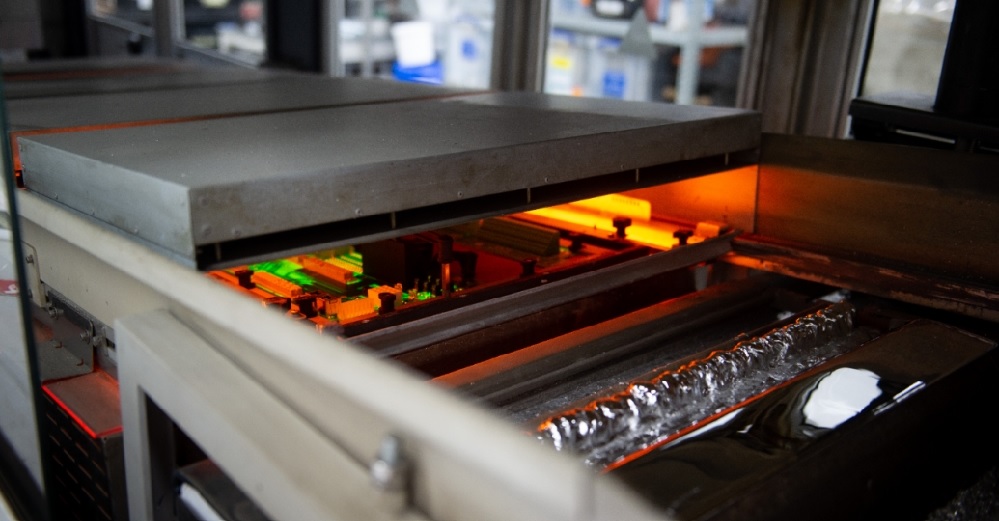
Industrial machinery in manufacturing is witnessing highly significant innovations. It is challenging to design, validate and manage modern-day manufacturing and assembly processes to achieve unrivaled quality while optimizing cost.
In this seventh blog of the Advanced Machine Engineering series, we are providing a transcribed excerpt of the third podcast, focusing on virtual machine simulation and commissioning and how machine manufacturers are implementing this approach to improve quality and reduce delivery time for highly complex machines.
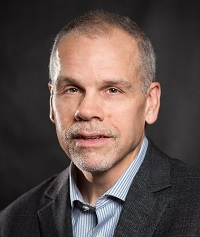
Again, I interview one of our resident engineering experts, Bill Davis, who is the Director of Industrial Machinery and Heavy Equipment Solutions at Siemens Digital Industries Software. Bill’s expertise in this industry expands over 30 years, with 20 years as an engineer.
Below, is the transcribed excerpt from the third podcast in this series:
Bill Butcher: Welcome to Siemens Digital Industry Software podcast series on Advanced Machine Engineering, brought to you by the Siemens Thought Leadership team. Innovations with industrial machinery in manufacturing are seeing groundbreaking technological advancements. Today, in our third podcast of the series, we will learn the advantages that advanced machine engineering brings to the industrial machinery manufacturers, and more specifically, we will focus the discussion today around virtual machine simulation and commissioning and how machine manufacturers are implementing this approach to improve the quality and reduce delivery time for highly complex machines. I want to welcome again our expert in the series, Bill Davis, who’s the Director of Industrial Machinery and Heavy Equipment Solutions at Siemens. Bill has over 30 years of experience in engineering and operations management, and has spent the last 20 years, focused on the industrial machinery industry. So, welcome Bill!
Bill Davis: Thank you.
Bill Butcher: So, I’ve got a few questions on the topic. In our last two podcasts, we talked about the evolution of technology within the machinery industry, and key trends that continue to shape the industry today. We also introduced the Advanced Machine Engineering solution at a high level, where you discussed three key differentiators – multi-disciplinary design, virtual machine simulation and commissioning, multi-disciplinary Bill of Material (BOM) management and configuration management.
In our last session we took a deep dive into multi-disciplinary design. In this session, though, I’d like to kind of twist the conversation and shift over to virtual machine simulation and commissioning. What is virtual machine simulation and commissioning?
Bill Davis: Thank you, Bill, and thanks to everyone for attending this series. The virtual machine simulation and commissioning is what we talk about, broadly speaking, as it relates to how does the machine that we prove out to a customer physically, on the factory floor, operate in the virtual world? No one is going to buy a machine sight unseen; and they’re not going to buy your claim that you virtually simulated this because you ran some software code. They still want to see that machine work before they let you ship it to their plant. However, because many software integrations and safety factors are necessary to run a machine, you don’t want to do it for the first time with people around. You want to be able to do it in the virtual world so that when you get to the point of building or turning that machine on, and performing the real commissioning, there’s less pressure for you and your customers. So, that’s what we’re talking about when it comes to virtual machine simulation and commissioning.
Bill Butcher: Let’s try and narrow it down for our listeners a little bit. What are some of the specific challenges that machine builders are facing in where this approach could benefit them?
Bill Davis: I will divide up our industry a little bit and talk about different types of machines and how their commissioning might vary depending on their virtual commissioning needs. So, if you build your own equipment, you would also buy third-party equipment, and build the intermediate pieces – conveyors, sensors, etc. – that integrate as well. Therefore, what we call line builders, even though that wasn’t our major focus of our business, needs to prove that every one of those pieces will work in the way that we designed it and orchestrate that behavior so that it operates seamlessly. Sometimes this interface is challenging in bringing those disparate systems and code together – this is one piece of it.
A second area of machine development where virtual commissioning is very important is in robotic cells. You may have heard in the press that robots, cobots and all robotic integration where there is a multi-axis capability of moving many directions, has code that’s embedded into the robot to prevent it from not operating efficiently. So, you have more of a transactional relationship, and you must get into that code with those robots to be able to extract that behavior. So, when there is a couple of robotic cells and traditional picking places this is not a big deal; however, when you’re integrating them for machining or continuous data that must flow back and forth between the PLC code and the robot, it is more complex. This is a crucial situation when you’re driving machines to be more and more efficient and operating near the edges of their capability and performance.
Another trend is if you’ve ever bought something from Amazon, did you ever wonder how they got it to you in less than an hour? Whole factories, including lights-out factories, have production systems, and this is an area that’s growing quickly, called “logistics automation“. So, not only do you have the capabilities around behaviors of a machine that’s supposed to pick and wrap, but now you have autonomous capabilities around where you have a robot that must seek out a certain SKU, based on a warehouse location. The level of automation and the need to do a virtual commissioning is amped up significantly because now you’ve got way to have more pieces in play at the same time. You’ve got multiple robots roving through these factories, and obviously they can’t collide. Whereas, in a robotic cell, it’s usually a single robot or an orchestration of a couple of different robots in logistics automation, and it’s a bit of a free-for-all, where each one of these robots has its own goal and it doesn’t necessarily matter if there’s another robot in their way. Therefore, is necessary to orchestrate these interfaces in a unique way. So, that’s an example of a few of the different types of machinery companies and machinery integrators where virtual commissioning is becoming an important part of their manufacturing or their design execution and manufacturing strategy.
Bill Butcher: So, even though we narrowed the scope a little bit, the challenges you just talked about are vast. Help me understand how Advanced Machine Engineering, and more specifically, virtual machine simulation, can help overcome these challenges. What exactly is the simulation approach or approaches that are being leveraged to address these challenges?
Bill Davis: We started talking about the different machinery types of companies, but there’s various disciplines within the simulation world that we have and are included in Advanced Machine Engineering. Siemens has an entire digital industry software solution suite that involves simulation. One of the first is what’s called a 1D Simulation, or more appropriately, system modeling. One of the capabilities is before you decide how something is to be powered, you model it in various manners for prime optimization. Now, it’s a symbology, if you will, of behaviors; it’s not really a design in a more traditional mechanical CAD mock-up kind of way of doing simulation. It’s an understanding of how the systems are powered and what must be done in terms of each one of the types of behaviors. They overlay on top of the diverse domains, whether it’s a pneumatics or electrical, to increase the fidelity because it’s very simple in terms of it not requiring the building of any CAD models. You’re working with symbols and connecting them together for goal-seeking quickly, failing fast and figuring out how things are supposed to work. Realistically, it’s a new concept for machinery companies, but more common in the heavy equipment space up until now, as it’s starting to take root in machinery companies, and I’m glad because it’s the best way to get to that optimal, streamline design – the mechanical 3D portion of it, which is what we’ll talk about next.
In a more traditional 3D simulation world, I think most people are familiar with how they can take the CAD model and apply loads and constraints to them and get behavior out of the model, where the high stress is. A long time ago, the series on American Chopper, with the older guy who founded the company that builds custom motorcycles, has his first exposure to 3D simulation and he said, “Okay, so let me get this right: red is bad and blue is good. Okay, I got it.” So, in a humorous, simplistic way, 3D simulation can be explained. However, I think what’s more common today is that it’s not just about static load cases and forces being applied to models – we need to think about different multi-disciplinary or multi-domain kinds of simulation in the 3D space. Also, in addition to structural, we have fluid and behavior in a vacuum, especially for packaging machinery, where we use much vacuum to pick a product and place it. So, the behavior from a fluid dynamics perspective is important, including thermal and vibration and acoustics.
We have a customer who built a machine for our simulation group, where they use heated rollers to form this package on separate films. So, it became critical for them to understand the behavior of the heated rollers and where it was effective along the entire length of that roller. And if there were other fluid portions of that thermal, the air that goes into the system shows how it was impacting the thermal conductivity between the rollers and the film. And then, because it’s a rotating equipment, incorporating things like vibration and acoustics into that, I mean, that gets to be pretty complex. But, what we’ve seen is that as the machines are getting faster, and people are expecting greater production capacities, these other disciplines or domains of 3D simulation are becoming more important to integrate into the mechanical design in the Advanced Machine Engineering design.
That upfront simulation is good, but you also must be able to test it out to virtually commission it and physical testing. Using the thermal example again – the varying temperature doesn’t exceed 30 degrees Celsius. Even though your model said, “Yes, it will do that”, you still must have the testing capability to be able to prove the machine behaves the way that you designed it.
So, we talked about virtual commissioning as a set of capabilities in terms of simulation – simulating the machine performance in the virtual world is necessary because we’re having more and more behavior of that machine that’s being driven by software. Therefore, to express that and know that it’s going to behave the way that you want it to, you must be able to test that code on a virtual twin, and it’s more than just behavior; however, there’s the physical safety aspect of it. If the machine collides in the virtual world, it’s a lot safer and less costly than in the real machine. Of course, it costs more money and it extends out your lead time, but having that virtual commissioning capability and being able to drive not just the behavior of the motors – turn on the motor, turn off the motor, light this lamp, turn this lamp off, etc. – but also integrating that into the kinematics and working it backward up into the 3D simulation. This is powerful because we don’t always have a good handle on what the forces are for the 3D simulation. In other words, we tend to express it as best we know, but when the mechanism moves twice as fast as we thought it would, the kinetic energy is a factor of the square of the velocity – an actual impact load can be greater than we anticipated. If you don’t have a way of replicating the kinematics in your virtual commissioning software, you’re missing out on potential hazards that you could see downstream. So, those are some of the areas of simulation that we focus on when we talk about the whole simulation suite of products and machine engineering, but especially on the virtual commissioning side.
Bill Butcher: Can you continue that thought further by diving a deeper into what some of the benefits are for those manufacturers that go all the way and incorporate this virtual machine simulation commissioning approach and integrate it into their manufacturing process?
Bill Davis: Yes, sure, Bill. So, we talked about a few different capabilities and I think it’s important to just touch on these from an operations side. Having experience on the manufacturing operations side of automation companies gave me a unique perspective. I was kind of what I would call a victim of engineering. So, where we started to press for more virtual commissioning and simulation in that process, it gave us benefits in operations were more cost-effective. Therefore, we could deliver in a more appropriate timeframe. Every day that I’m late in delivering a machine to a customer means X number of thousands of dollars that come off the bottom line for that machine sale. So, it’s important for the operations and manufacturing side of the business to deliver that machine as quickly as possible within the construct of the contract. So, all these factors that we’re were discussing are about risk mitigation and schedule compression.
Having an integrated simulation supports parallel engineering development. It avoids me having to have a programmer sitting on the machine floor while the machine is mechanically and electrically complete, for them to do their programming and code validation. Therefore, it shortens up the overall manufacturing delivery schedule. We have significant experience from a Siemens perspective because we build our own hardware, we manufacture our own products, we can actually test those manufacturing processes out and we can build a very tight integration between our software code development and the hardware itself, so we’ve been able to test out this and we’re leaders in this whole virtual commissioning simulation for a number of years. The products of Siemens are just amazing in terms of the fidelity and how complete the capability of testing is around both the PLC code and the HMI integration. I haven’t seen anything in the market that’s close to it.
Bill Butcher: Are there any other examples of companies that have taken this approach and implemented it? And if so, what kind of benefits they’ve received?
Bill Davis: Tronrud is an example. They have been able to reduce their commissioning time up to 70 percent, while compressing their engineering time by 25 percent. These numbers are a significant benefit to their bottom line. Just an example from my past is having the ability to build about twenty machines at one time on the manufacturing floor, thus shortening commissioning time by one week that translated into about 10 or 15 percent increase in productive capacity on the machine floor. That’s huge.
Bill Butcher: That gives a competitive advantage, I can see that, yes!
Bill Butcher: Well, thank you again, Bill, for the conversation today and taking us even further into the Advanced Machine Engineering Solution and looking at the advantages it provides machine manufacturers when they leverage a virtual machine simulation and commissioning approach. We look forward to the next and final podcasts in the series.
Listen to podcast01, podcast02, podcast03 and podcast04 from this series via our Thought Leadership blogs.
Also, you can access the entire podcast series via Apple, Stitcher, Spotify, Castbox, TuneIn or Google.
To improve the speed and efficiency of your machine design process, watch our Advanced Machine Engineering – Start your digital transformation journey today webinar.
About our expert:
Bill Davis is the
acting Industrial Machinery and Heavy Equipment Industry leader for Siemens
Digital Industries Software. His experience and insights have been acquired
from a career spanning 30 years in engineering and operations management with
machinery and heavy equipment companies. Bill holds a master’s degree in
Business Administration from Marquette University, with a concentration in Operations
Management and Strategic Marketing,
as well as a Bachelor of Science degree in Mechanical Engineering from
Milwaukee School of
Engineering.
This blog is an excerpt from the advanced machine engineering podcast transcript, displaying the second in a series of four podcasts.