Building your digital twin
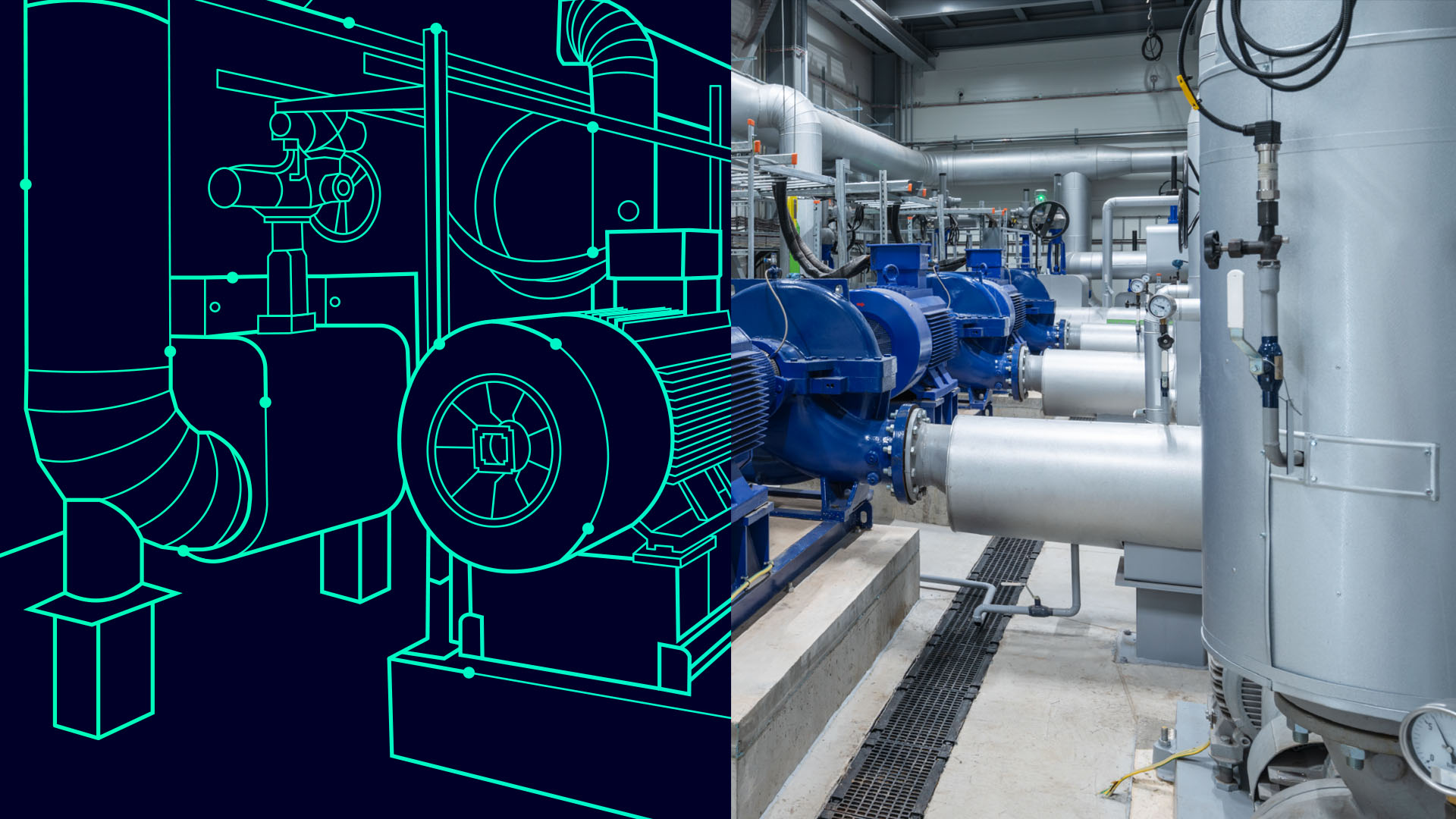
Many manufacturers have begun their digital transformation journeys to achieve goals such as quality assurance, cost reduction, and waste mitigation. Leveraging the digital twin, manufacturers can meet these targets while remaining competitive and resilient. What’s more, simulation technology like the digital twin, along with software-defined automation and production move the industry towards creating the industrial metaverse: a digital space that enhances collaboration and maximizes production efficiency.
But to materialize the digital twin’s benefits, businesses must first focus on building it properly. Similar to the concept behind technology itself, the creation of the digital twin should be separated into the virtual and physical; the virtual being representations of the future machines and systems, and the physical being the tangible machines and systems.
Physical and virtual construction
The digital twin is more than just a static representation of physical components, it is a detailed, dynamic description of how those components should be built or how they should behave. Simulations portraying the description help engineers understand how the machine or system will function, enabling them to refine and optimize them before committing to a real-life prototype or build.
Once this step is in full swing, construction can begin, with the physical lane now running in parallel with the virtual. As assembly continues, engineers should continuously update the digital twin to reflect the progress of future physical machines or systems. During this crucial period, the design, engineering, and manufacturing teams can use the digital twin to finalize the code before the physical build is completed in a process called virtual commissioning.
With the virtual commissioning approach, engineers can refine and enhance a prototype product or system, ultimately leading to significant cost savings. On top of cost savings, manufacturers may save time with physical commissioning and reduce waste by forgoing the typical steps that come with traditional prototyping.
Continuous improvement
The digital twin can bring your business benefits ever after construction ends. After the physical components of the factory are built, the digital twin can help continuously improve factory operations by enabling manufacturers to better understand their operations. Benefits the digital twin creates include:
- Improved employee training: staff can train virtually before working with physical machinery
- Optimized throughput and enhanced quality: through simulating scenarios, manufacturers can change and enhance throughput
- Sustainability support: simulation helps monitor energy consumption
- Efficient troubleshooting: since the digital twin updates in tandem with real-world machines, it can diagnose problems in the system
- Predictive maintenance: the digital twin can help manufacturers predict equipment failures
These benefits are mainly achieved through the digital twin’s augmented data capture capabilities. The digital twin uses several methods to capture data in real-time; these methods are sensors, AI, and IT/OT convergence. Machine sensors capture data directly from the equipment and have the benefit of enabling data capture from older machines.
Additionally, AI works in conjunction with the digital twin to quickly train machines to complete different tasks without the need for other physical systems. Meanwhile, IT/OT convergence enhances data capture by homogenizing siloed information technology and operation technology systems. The integration of IT and OT unlocks previously untapped data, helping the factory get a comprehensive view of its operations.
Digital twin for different needs
The digital twin landscape is capable of aiding in a multitude of operations, but every factory has unique needs. Not every business will find the all-compassing information a comprehensive digital twin provides necessary. Different use cases demand a distinct digital twin, with a strategic focus on specific information that aligns with its intended use.
Whether your organization is seeking to optimize operations, dip into predictive maintenance, or needs a more compact, yet scalable solution, the digital twin can help you move further along in your digital transformation journey. Read more about how Siemens’ digital twin can address your factory’s individual needs through a broad range of integrated software and automation solutions here.
Siemens Digital Industries Software helps organizations of all sizes digitally transform using software, hardware and services from the Siemens Xcelerator business platform. Siemens’ software and the comprehensive digital twin enable companies to optimize their design, engineering and manufacturing processes to turn today’s ideas into the sustainable products of the future. From chips to entire systems, from product to process, across all industries. Siemens Digital Industries Software – Accelerating transformation.