Addressing new challenges with IT/OT convergence
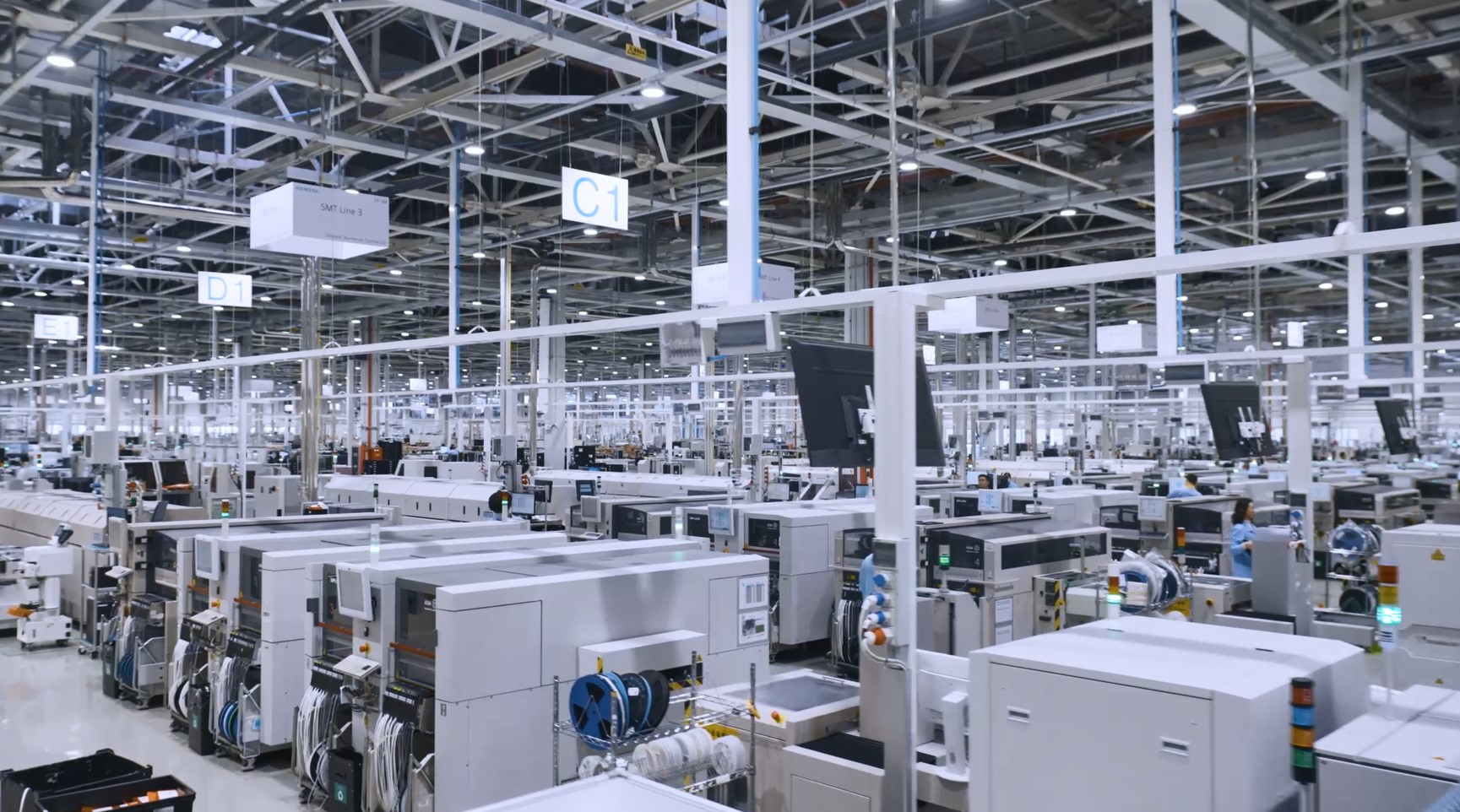
Digitalization creates new paths of opportunity for companies as they strive to tackle labor shortages, rising operational costs, and many other common challenges in the industrial manufacturing sphere. Going beyond digitalization, many businesses have begun to integrate their IT and OT functionalities to further enhance efficiency. Through IT/OT convergence, OEMs can see extraordinary gains such as productivity improvement, decreased employee workloads, and predictive maintenance.
But the advantages of IT/OT convergence don’t end there. Businesses should aim to continuously evolve to augment operations, address sustainability requirements, and remain competitive. As well, with factories becoming more connected than ever, it is imperative that companies keep up to date with cybersecurity. Properly integrating IT and OT capabilities helps companies innovate all while monitoring its environmental impact.
Ensuring secure connections
As factories press forward on their digital transformation journeys, the risk of exposure to cyber threats increases. Digitalization brings more complex ecosystems, prompting attackers to exploit their weaknesses. Additionally, many factories have legacy systems, which cannot be updated, secured, or swapped out without incurring even greater costs and risks. Safeguarding vital industrial systems requires implementing IT/OT convergence strategy successfully.
Cybersecurity issues will continue to be prevalent as long as the business’s IT and OT segments remain siloed. Desegregating IT and OT processes are part and parcel of IT/OT convergence, not just systems, but teams as well. When looking to integrate their IT and OT capabilities, companies should also make sure that their IT and OT teams collaborate effectively. Facilitating openness between the teams will help businesses maintain digitally secure environments throughout the digital transformation. Additionally, there are IT/OT convergence tools that mitigate the cyber risks posed by digital environments. Siemens Industrial Edge platform has built-in cyber safety features that support the secure operation of machines and systems.
Bolstering sustainable operations
Merging IT and OT functionalities comes with enhanced data capturing capabilities, enabling manufacturers to improve visibility and management which will help them be in compliance with regulatory standards. Tracking metrics like fluid and consumption rates as well as energy usage can give businesses thorough insight into their production’s environmental footprint, allowing them to design machining processes optimized for sustainability.
IT/OT convergence also empowers companies to identify failures and bottlenecks in their processes and address them sustainably. Pinpointing the reasons behind failures could eventually lead to eliminating them permanently, thereby ensuring sustainable operations in perpetuity.
Encouraging innovation
With clean, easy access to data, OEMs can rely on both employee knowledge and machining process data to optimize operations. Not only will IT/OT convergence enable companies to recognize approaches towards productivity enhancement, but it also helps them to address break downs in their machining processes and systems that severely impact operations. Through data analysis, digitalization, and AI businesses can quickly and easily implement new methods to increase productivity and bolster efficiency.
Data-based decision making allows manufacturers to dynamically control production processes before making physical changes to the shop floor. This in turn facilitates the innovation process, helping companies keep up with rising costs, achieve sustainability goals, and address labor shortages.
Building better factories
Digital transformation and IT/OT convergence are helping manufacturers accelerate towards prosperity. As systems and processes become interconnected, companies can address cybersecurity concerns, sustainability, and bolster innovation. Additionally, consolidating systems and connecting data helps to eliminate production bottlenecks and enhance data management, allowing organizations to operate more securely while opening the door to greater opportunities by cutting down testing times and expenses.
See how Siemens brought these rewards to fruition at our PCB assembly factory in Erlangen, German here.
Siemens Digital Industries Software helps organizations of all sizes digitally transform using software, hardware and services from the Siemens Xcelerator business platform. Siemens’ software and the comprehensive digital twin enable companies to optimize their design, engineering and manufacturing processes to turn today’s ideas into the sustainable products of the future. From chips to entire systems, from product to process, across all industries. Siemens Digital Industries Software – Accelerating transformation.