Optimizing Production in the Siemens Erlangen Factory with the Digital Twin
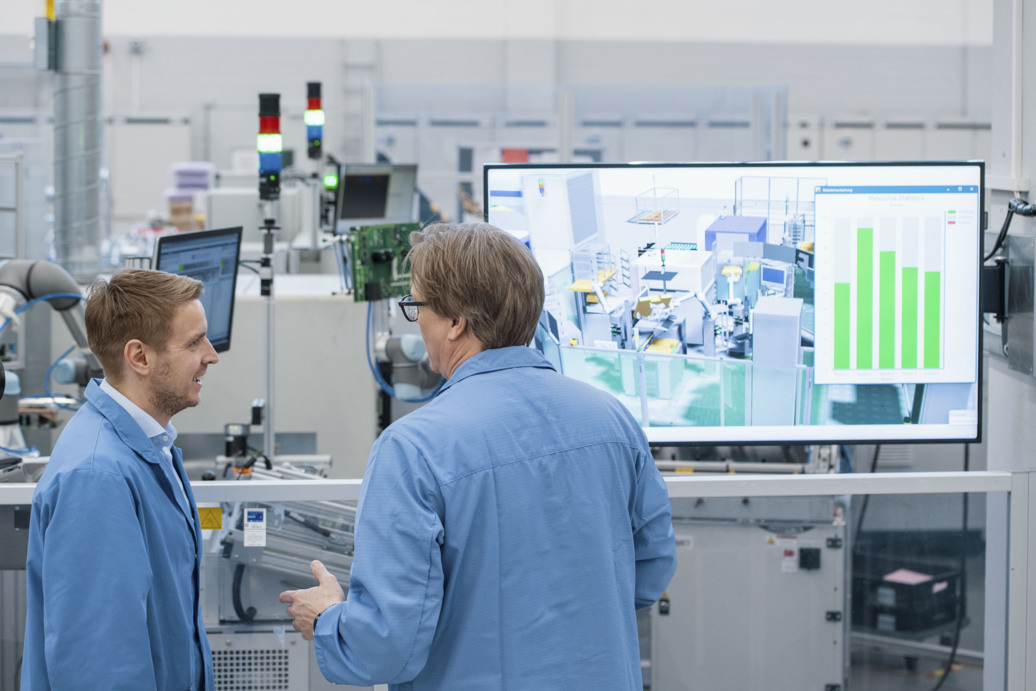
The digital twin is one of the most critical tools in 21st century engineering. Engineers can create use a digital twin as a virtual representation of almost any product or process, enabling them to test and modify anything from product designs to manufacturing operations in the virtual world before bringing them into reality. This is what makes the digital twin valuable for production lines.
As demonstrated by the Siemens Electronics Factory Erlangen, located in Erlangen, Germany, companies can create production digital twins that replicate their physical production lines. These virtual production lines can be run through simulations bolstered by real-time data from the factory, giving manufacturing engineers the ability to test and optimize their production lines faster and with less cost.
The power of simulation
The key benefit of a production digital twin is the ability to simulate its operations beforehand. Production lines can be incredibly complex, utilizing numerous moving parts such as heavy machinery and automated systems, along with multiple other factors acting from both internally and externally to the factory. As a virtual representation of a factory line, manufacturing engineers can run the production digital twin through a number of simulations to varying levels of details, allowing them to test any planned additions or changes to a line before carrying them out physically.
This enables the manufacturing engineers to spot potential errors and drawbacks earlier in the process. If a production line is built or modified physically only for errors to be discovered after its construction or modification, companies must spend additional time and money making corrections. Simulating the digital twin of a production line would uncover such errors earlier, reducing the chance of them making it into the physical production line and ensuring it runs smoothly from the beginning.
Ensuring simulation accuracy with real-time data
Of course, to ensure these simulations accurately portray the production lines they are representing, they need accurate data to rely upon. How else would simulations be able to represent real-life situations? Fortunately, the answer is quite easy. Using IT/OT applications, the Electronics Factory Erlangen collects data in real-time directly from machines on the factory floor and fed into the digital twin, providing simulations with the key to depict accurate conditions of production lines.
The factory has already seen benefits from this methodology. For example, automatic guided vehicle systems (AGVs), portable robots responsible for moving heavy materials, are a common sight in factories, and the layout of a factory floor must provide enough space to accommodate their presence and movements. By measuring data directly from the AGVs, running that data through IT/OT applications, and feeding it into the production digital twin, the Electronics Factory Erlangen was able to increase the accuracy of simulations involving AGVs by more than then percent.
Factory optimization
These capabilities serve to optimize production lines in numerous aspects. After running a digital twin through a simulation, the data collected can be analyzed by optimization software to recognize correlations between inputs and produce ideal outputs and recommendations based on relevant parameters.
Insights provided by this methodology can be especially beneficial in making a production line more sustainable. Simulations can represent factors such as material circulation and energy consumption, and the optimization software can give insight into how to get the most output while reducing material and energy spent.
The Electronics Factory Erlangen utilized the digital twin for just this purpose, reducing material circulation by 40 percent and energy usage by 70 percent. As sustainability becomes a growing area of importance for industrial operations, tools such as the digital twin and simulation can prove invaluable in maximizing sustainability efforts.
Through simulation, the digital twin enables factory engineers to identify errors and control options early, allowing them to make their manufacturing processes more efficient and less resource-consuming while saving time and money. The Electronics Factory Erlangen is a valuable use case in how the digital twin can be used for such ends and create better and more sustainable production lines for the future of industry.
Siemens Digital Industries Software helps organizations of all sizes digitally transform using software, hardware and services from the Siemens Xcelerator business platform. Siemens’ software and the comprehensive digital twin enable companies to optimize their design, engineering and manufacturing processes to turn today’s ideas into the sustainable products of the future. From chips to entire systems, from product to process, across all industries. Siemens Digital Industries Software – Accelerating transformation.