Digitalization is imperative to the future success of manufacturing
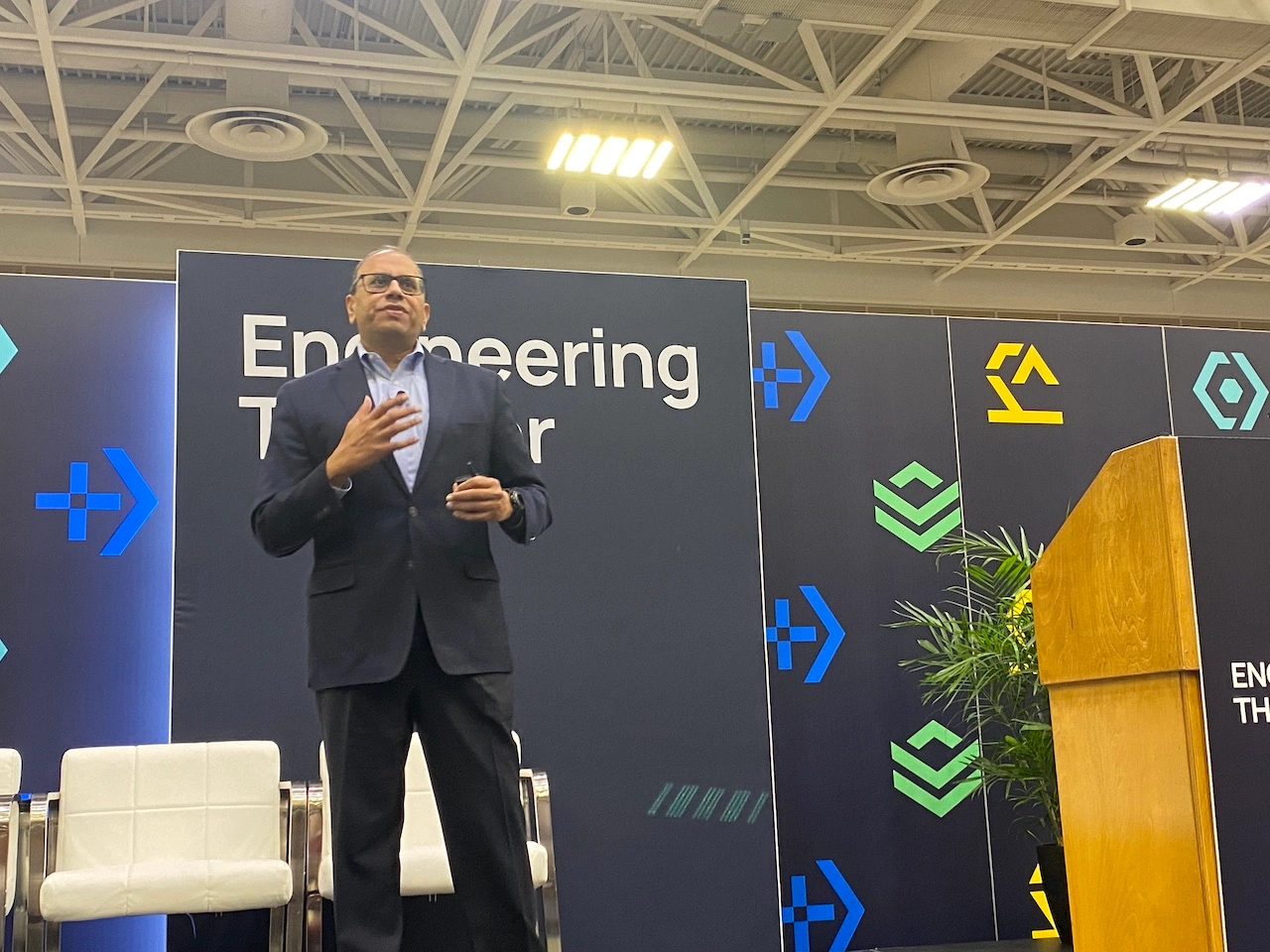
Rahul Garg, VP of Industrial Machinery at Siemens Digital Industries Software recently presented the keynote at Advanced Manufacturing Minneapolis. In his presentation, he outlined the challenges machine builders and manufacturers face as we enter the modern era of progress and how the key to staying ahead is by leveraging digitalization. In this blog, we’ll explore the insights from his presentation and uncover why digitalization is not just a trend but the key to driving manufacturing progress and a vital investment for the future.
First comes challenges, then comes change
Manufacturers are experiencing a serious workforce gap, with an estimated 2 to 3 million unfilled positions projected in the near future. Unless solved quickly, this talent shortage will significantly impact both production processes and capabilities (To learn more about solutions to this challenge listen to our podcast on reskilling and upskilling here).
While the gap between open positions and number of workers widens, the industry is also being transformed by the rise of smarter, more connected machines. with IoT related capabilities. These advancements will completely change the way machines are designed and built.
Business models are also shifting. As Garg points out, customers now expect companies to offer their equipment as a service, where they previously wanted to buy the machine. Manufacturers must navigate these evolving expectations while also accounting for increased regulatory scrutiny and global competition.
The change: Becoming a digital enterprise
So, what is the solution to these complex challenges? To Garg, the answer is embracing the concept of a digital enterprise. The digital enterprise model combines the real and digital worlds and brings them together to reveal new ways of optimizing an organizations’ operations—and the secret ingredient to making this work is data.
By integrating the real and digital realms, companies have the power and ability to harness hard-to-reach data in useful ways to effectively drive business operations. In essence, the digital enterprise equips manufacturing organizations to reveal troves of data and ultimately make smarter decisions.
The components
According to Garg, there are 3 main elements of a digital enterprise
- A comprehensive digital twin
- A digital thread that combines all digital pins in a more process-centric way
- The ability to leverage new artificial intelligence (AI) tools and technologies
As mentioned, one of the central elements of a digital enterprise in the comprehensive digital twin—a digital replica of both the products being produced and the processes used to manufacture them. This allows companies to simulate, test, troubleshoot and design production operations digitally before making changes in the real world.
Garg emphasized that this approach not only enhances problem-solving abilities, but also enables manufacturers to monitor how a given product is being used by customers. This mean not only monitoring machine performance, but also examining the machine data, putting it back into the design and engineering modifications to address any inefficiencies or issues.
Another key component is the digital thread, which connects all aspects of the enterprise in a cohesive way. By linking all digital twins, companies can leverage and bolster the effectiveness of all their digital twins. This collective intelligence makes business decisions better, faster and more effective. Moreover, Garg states that digital threads have to be customized to industries and customers alike. Like a subway map that gets you from stop A to stop D, companies can expand the digital twin and the digital trade across their entire enterprise. As companies mature in their journeys, they can continue to expand their digital thread roadmap.
The last, but certainly not least, piece to the digital enterprise equation is industrial AI. For Garg, Industrial AI is what will drive the concept of digitalization into hyper mode. If the digital enterprise is the method for unleashing data, then AI is the key to turning that data into solutions.
For example, by taking advantage of large language models (LLMs), training them to speak the language of engineering and manufacturing, then teaching it a company’s vernacular, AI can be leveraged to automate mundane processes. This helps to close the talent gap by solving simple, yet time-consuming issues, freeing up worker’s schedules to focus on more impactful tasks.
In addition, AI can be used by an automation engineer with a copilot. The industrial copilot is capable of generating code for PLCs. Rather than starting from ground zero, the PLC engineer can soft through pre-written code, verify its correctness and make sure it fits the task. In fact, the productivity of a PLC programmer can increase by 30-40% since the initial task of writing code is performed by the copilot. And since PLC programmers are in short supply, using AI copilots makes it simple to democratize the value of AI across an organization.
Digitalization is the way forward
For manufacturers looking to remain competitive, digitalization isn’t something that can wait—it’s a necessity today. For Garg digitalization sets opportunity in motion. It opens the doors to greater efficiency, innovation, and growth by allowing companies to harness data, optimize operations and ultimately meet the demands of a changing market.