Smart manufacturing: Battery production for the future
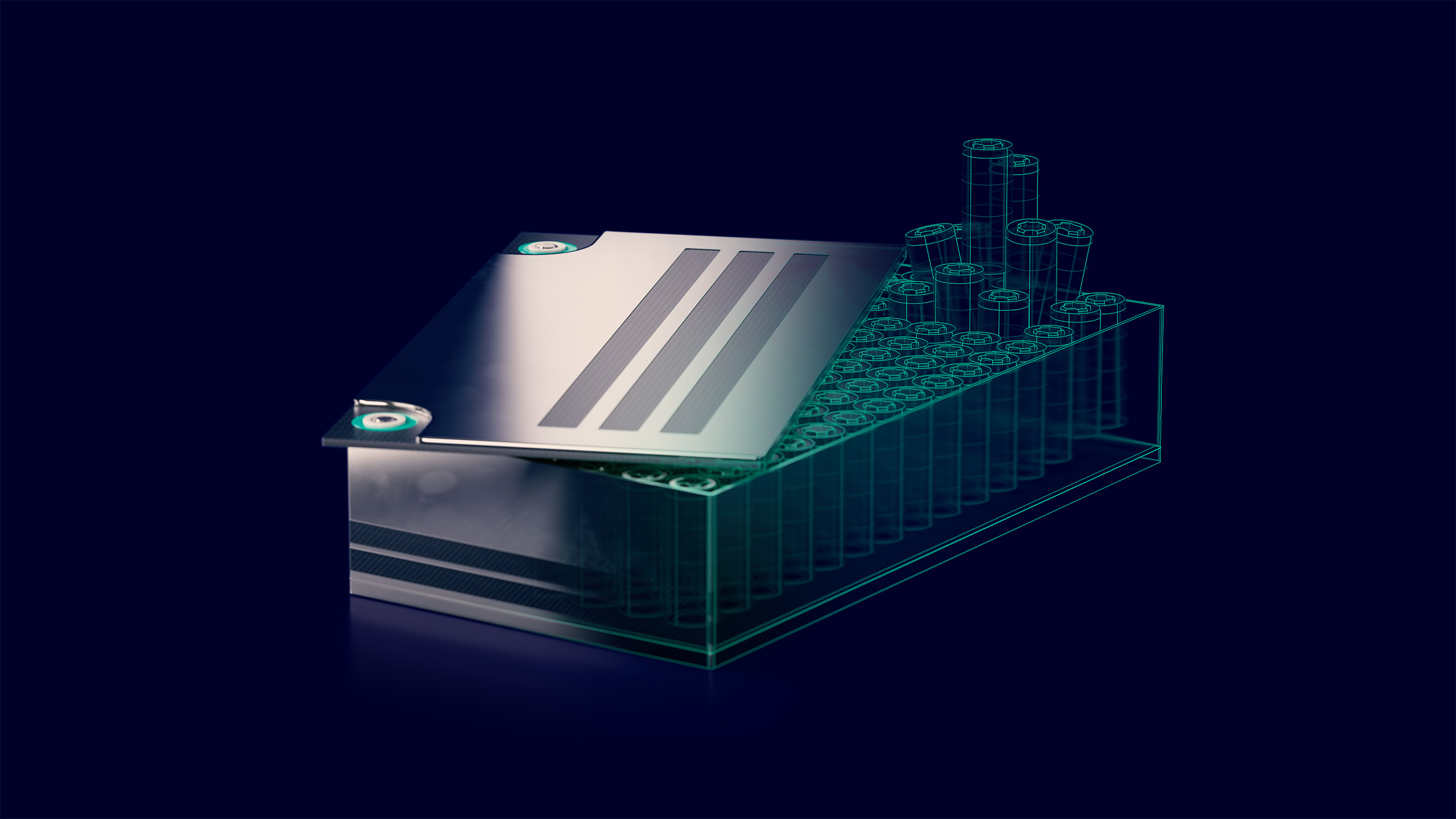
Modern manufacturing challenges require modern technological solutions. That’s why organizations across all industries are beginning to embrace and adopt smart manufacturing. One industry in particular is recognizing the immense potential of this transition—the battery industry.
In a recent podcast, Puneet Sinha, Sr. Director, and Global Head of the Battery Industry at Siemens DISW joined Rahul Garg, VP of Industrial Machinery and SMB Program at Siemens DISW met to discuss the impact of digital transformation on the battery industry and how it can help solve issues like standardization, sustainability and scalability. In this blog, we’ll share their insights and reveal why smart manufacturing is the answer to machine building for the battery industry.
The imperative of standardization
Unlike discrete or traditional manufacturers, battery manufacturing has historically been highly individualized, relying on artisans for the entirety of the production process. However, with the recent meteoric rise in battery demand, battery manufacturers are attempting to transition away from bespoke processes and into more standardized procedures. In addition to increased demand, battery manufacturers also face pressing challenges such as:
- High scrap rates: Initial production phases often see scrap rates of 40% or higher, with stable operations still experiencing rates between 10-15%. These high scrap rates can significantly impact profitability
- Maintaining material quality: The variability in raw materials such as lithium, graphite, cobalt and manganese introduces additional challenges. Microscopic defects and slight environmental changes can lead to a number of production issues
The manufacturing process for batteries involves numerous steps, each demanding exact control. Even small variations in these steps or in dry room operating conditions can have major repercussions. The process is incredibly delicate and occurs at a microscopic level. For example, when electrode sheets are coated and dried, they must meet stringent thickness requirements, typically ranging from 450 to 100 microns. Ensuring the entire electrode roll is uniformly dried is a complicated task, and even a miniscule undried area can lead to significant quality issues.
These defects often go unnoticed until the final stages of manufacturing, by which time it’s too late to correct them without scrapping large portions of material. This delay in defect detection leads to high scrap rates, which is both costly and inefficient.
To begin tackling these challenges, standardizing processes is necessary. Consistent procedures and quality control measures across the industry can reduce variability and improve overall product quality. This includes standardizing raw material quality, manufacturing steps and operating conditions. By doing this, battery manufacturers can improve efficiency, reduce costs and produce high-quality batteries.
Addressing environmental impact
Sustainability presents another formidable hurdle for battery manufacturers. In recent years, there has been a tremendous push towards creating more environmentally friendly factories. However, battery cell manufacturing is an incredibly energy intensive process. It takes approximately 30-40 units of energy consumption to create 1 unit of battery energy. This creates a significant carbon footprint in a factory, especially when producing at a large scale.
For battery companies, it is crucial to have a comprehensive understanding and precise control over their operations. Monitoring operational efficiency and machine utilization to minimize energy consumption is essential. This responsibility extends beyond battery suppliers to encompass machine builders as well.
Machine builders must focus on designing and producing equipment that consumes less energy while maintaining high process efficiency. Addressing the sustainability challenges in battery manufacturing requires a holistic approach, bringing together insights from operations and smart manufacturing to create more sustainable production processes.
Achieving transparency with the Digital Twin
While standardization is imperative when it comes to overcoming the challenges of battery manufacturing, digitalization, IT/OT convergence and the Digital Twin all play an equally important role. The implementation of these digital tools and virtual commissioning in factories is nothing short of paradigm-shifting. These technologies enable manufacturers to create a comprehensive digital replica of their equipment, processes and even their entire plant, while gaining access to a wealth of fresh data insights.
By simulating and testing in a virtual environment, manufacturers and machine builders alike can fine-tune their operations, optimizing possible variables prior to production. This proactive approach ensure that potential issues are addressed and processes are refined, leading to a more efficient and predictable manufacturing outcome. This transparency enables decision makers to identify where sustainability can be improved and where quality can be increased.
Success with Siemens
Siemens is a key technology partner in the fast-evolving battery ecosystem, with 8 of the top 10 suppliers using elements of our robust solutions portfolio. A standout success story comes from HCM, a Taiwanese company specializing in LFP cathode materials and manufacturing equipment. By adopting Siemens’ plant simulation portfolio, they optimized their production line, reducing equipment idle time by 15% and energy consumption by 5%. This hasn’t just improved efficiency but also paves the way for a fully automated factory in the future.
This case study highlights the role of digitalization in tackling industry obstacles. As the battery industry scales up, Siemens’ experience and innovative solution will be central to driving sustainable and efficient manufacturing practices. To learn more about smart manufacturing in the battery industry, listen to the podcast here.
Siemens Digital Industries Software helps organizations of all sizes digitally transform using software, hardware and services from the Siemens Xcelerator business platform. Siemens’ software and the comprehensive digital twin enable companies to optimize their design, engineering and manufacturing processes to turn today’s ideas into the sustainable products of the future. From chips to entire systems, from product to process, across all industries. Siemens Digital Industries Software – Accelerating transformation.