The Mechanical Side of Generative Design Part One – Summary – Talking Aerospace Today
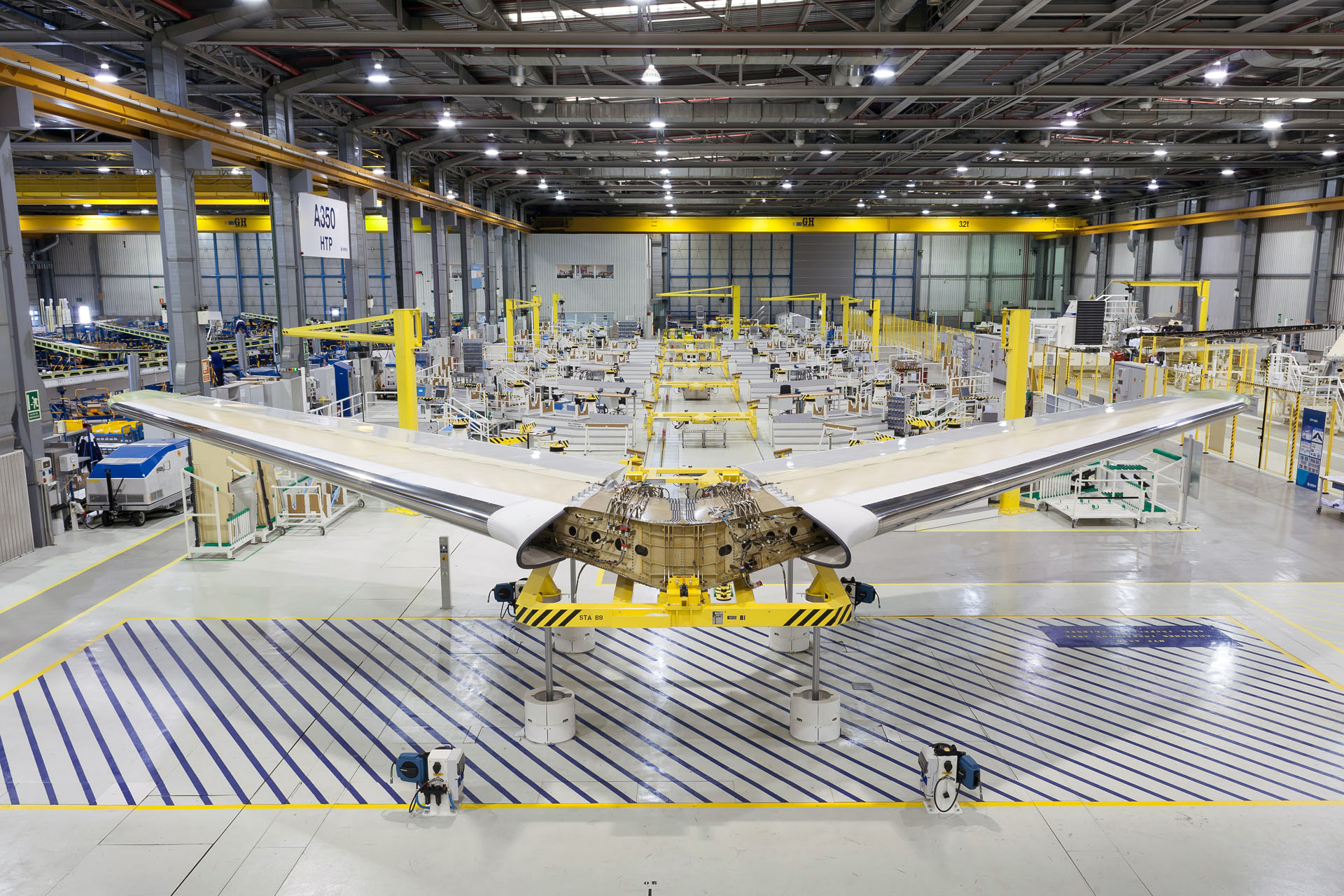
As discussed in previous episodes of Talking Aerospace Today, generative design, the process of automatically generating design artifacts based on a set of defined parameters, will play a crucial role in digital transformation maturity. These episodes discussed the great potential generative design has in store for the electrical domain. Yet aerospace and defense (A&D) products are incredibly complex, integrating many engineering domains, and generative design will apply differently for each one. For example, what does generative design look like for the mechanical domain?
In this latest episode, Todd Tuthill, Vice President of A&D for Siemens Digital Industries Software, is joined by John O’Connor, Director of Aerospace Product and Market Strategy for Siemens Digital Industries Software, to answer this question. They begin by briefly reiterating what generative design is before delving into how generative design for the mechanical domain is different from that of electrical systems, as well as the mechanical domain’s long history with generative design.
Defining generative design
As mentioned above, generative design is the automatic generation design artifacts, such as the wing of an airplane in aerospace, based on a set of parameters defined by engineers. Essentially, it is the automation of design. The overall goal of AI is not to replace engineers, but to take on the more tedious tasks involved in design and enable engineers to focus more on higher-level engineering and critical thinking.
The important thing to note, however, is that while generative design in the context of digital transformation maturity implies artificial intelligence (AI) will be a critical component of generative design, AI is not a requirement. As explained later in the episode, generative design as a concept has existed in previous iterations prior to the rapid rise of AI in recent years.
Furthermore, generative design is much more geared toward engineers and industrial design than other forms of AI commonly discussed in the public conversation. Those scrape data from the Internet to generate simpler forms of content like text and code. Meanwhile, as Todd explained in previous episodes, generative design in the context of digital transformation maturity would be taking data only from a company’s proprietary data lake to generate more complex design artifacts.
Generating for mechanical vs electrical
Generative design for the mechanical domain has quite a few differences from generative design for electrical systems, the most significant being what is actually generated. Todd explains that artifacts for electrical systems are often more two-dimensional in nature, such as schematics for wiring connections, and there is usually a significant amount of documentation involved. Mechanical artifacts, meanwhile, are more prominently three-dimensional, which come with their own additional set of considerations that can include different materials and manufacturability.
Another important difference that is not related to the generated items themselves is history. The mechanical domain has been pursuing generative design longer than the electrical domain has through digital transformation efforts and the adoption of model-based design practices. Therefore, as of writing this, generative design for mechanical engineering is more mature than for electrical engineering.
A long and fruitful history
John dives into this history by explaining the origins of mechanical generative design, and how they are derived from attempts at topology optimization. Back then, there were not so many concerns such as manufacturability or surface quality, but rather a desire to simply optimize pure geometry. Thus a lot of designs with this earlier iteration were very exciting, but largely relegated to only conceptuality and requiring engineers to manually rework them into something manufacturable.
Over time, however, generative modeling capabilities developed further and incorporated new parameters. Geometry would now conform to desires for manufacturability, followed by more complex considerations such as multiphysics. Later, algorithms would be integrated to drive the design based on the most critical design requirement. Now there are efforts today to incorporate machine learning as a component of AI to drive new types of design criteria and create an advanced, higher level of generative design in the overall process.
A perfect time to adopt
Generative design advanced alongside mechanical engineering for some time now, and the potential for its adoption has never been greater. It has already done wonders for topology and geometry optimization and manufacturability, and with the latest advancements in AI, it offers many more ways to revolutionize mechanical design and accelerate A&D companies’ digital transformations.
Stay tuned for the second part of this conversation in the next episode of Talking Aerospace Today to learn more about generative design for mechanical engineering.
Siemens Digital Industries Software helps organizations of all sizes digitally transform using software, hardware and services from the Siemens Xcelerator business platform. Siemens’ software and the comprehensive digital twin enable companies to optimize their design, engineering and manufacturing processes to turn today’s ideas into the sustainable products of the future. From chips to entire systems, from product to process, across all industries. Siemens Digital Industries Software – Accelerating transformation.