Transforming battery manufacturing with digitalization
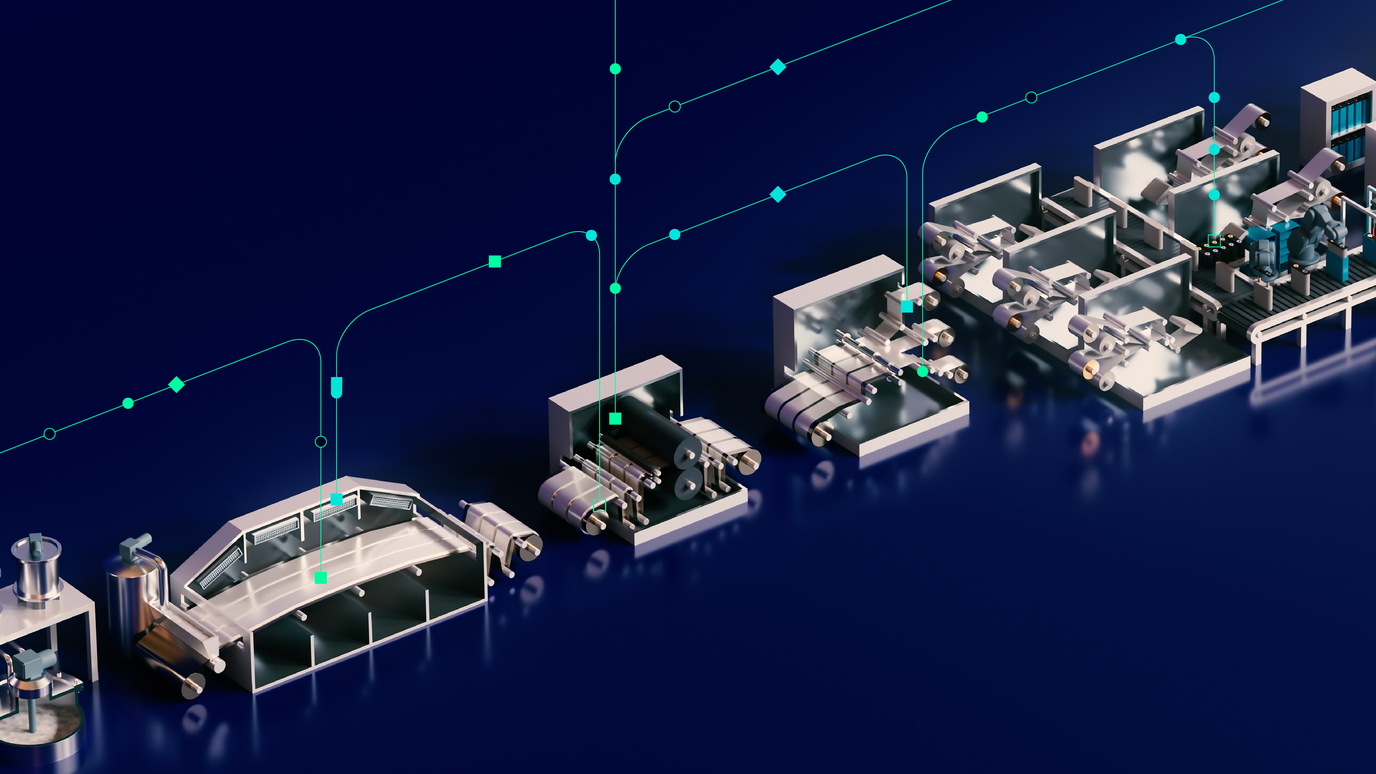
The battery industry is seeing massive growth in the markets, it is projected to reach 14-fold by 2030 from 2018’s market demand. Making that acceleration possible with digitalization is why Puneet Sinha and I sat down with Magnus Edholm, who drives the Digital Enterprise at Siemens, for episodes five and six of the Battery Podcast. Together we dive into why it is important to be rethinking batteries, how connected digital tools are helping optimize production, and where companies can find the ability to accelerate growth to meet market demands over the next decade. You can listen to the first half of our discussion below and keep reading for a summary of the most important points.
It is understandable coming from a digital enterprise expert at Siemens, but going digital with more facets of manufacturing will be a massive accelerator for battery manufacturers on their journey to scale production and release new technologies. The digital environment helps streamline so many processes that would traditionally be slowed by physical iteration. Instead, new chemistries can be simulated, the battery can be developed alongside the battery management system, and factory planning can happen cooperatively to minimize wasted time, space, and costs. Digitalization allows iteration without the high cost of physical iteration – letting the entire business learn faster than ever.
And aside from making traditional processes faster, going digital can also help companies optimize more-complex challenges. One of the largest sectors for batteries is in automotive and transportation, and the complexity of a battery drivetrain is deceptively complex compared to internal combustion engine (ICE) vehicles. While there are far fewer parts in an EV, there are more domain interactions – chemistry, mechanics, thermal, software, electrical, and electronics. Digital solutions for battery help designer, engineers, and manufacturers rapidly gain competence that will rival the experience pool for ICE vehicles. It is vital for the industry’s success.
Massive factory scale
The volume of batteries needed does not rely solely on increasing production speed, there are limitations in how fast a battery can be produced. This is why factories need to expand their physical footprint, which is why gigafactory is such an apt name for such sites. A gigawatt hour of battery storage capacity production takes up 10,000 sq. meters (100,000 sq. ft.). In these massive facilities, the machines continuously generate and exchange data while monitoring cell production. Collecting, sorting, and analyzing that data is incredibly valuable and intensive, which is why a robust IT/OT solution is so important to manufacturing. This pool of data helps find the root of scrap rates, equipment deficiencies compared to expectation, areas for process improvement, and much more. And while the conversation is about batteries, this type of solution is valuable for most processes industries and many more discrete manufacturers.
Executing a fifty-step and multi-week recipe
Manufacturing batteries is a complex mix of around fifty discreet steps and process phases. Each has it’s own challenges – time, energy, material loss. Combining this complex web of manufacturing in the digital twin helps companies understand the overall throughput and cost with greater granularity. Cell formation and aging are two large bottlenecks for production, requiring a two week waiting period for the products. And in that time, businesses often lack visibility into the progress and success of these developing cells. Improving data collection on manufacturing processes and quality of the cells on completion can create a data pool for earlier evaluation of success. With data in hand, battery manufacturers can make decisions in real time and take corrective actions immediately when manufacturing KPIs are projected to drop in the factory.
Digital factories and the battery industry
Starting today, and for the next few years, digitalization of factories, design, and production will be critical for the battery industry to meet not just market capacity demands that continue to grow, but the pressures to make the industry more sustainable. Going digital helps businesses iterate on ideas faster than the real world and with fewer resources – both critical to battery manufacturing that already understands the deadline for decarbonization and the limited resources for their current products.
But for more information on how to make digitalization a reality, there is still more in the episode above. You can also check out our other discussions from the Battery Podcast or read more about what we are doing in the industry on our website siemens.com/battery.
Siemens Digital Industries (DI) is a leading innovator in automation and digitalization. In close cooperation with its partners and customers, DI is the driving force for the digital transformation in the process and manufacturing industries. With its Digital Enterprise portfolio, Siemens provides companies of all sizes with all the necessary products, along with consistent solutions and services for the integration and digitalization of the entire value chain. Optimized for the specific requirements of individual industries, this unique portfolio enables customers to enhance their productivity and flexibility. DI continuously extends its portfolio to include innovations and the integration of future-oriented technologies. Siemens Digital Industries, with its headquarters in Nuremberg, has a workforce of around 72,000 people worldwide.
For more information on Siemens Digital Industries products and services, follow us on LinkedIn, Facebook, Twitter, and YouTube.