The digital impact on industrial machinery – modeling and simulation
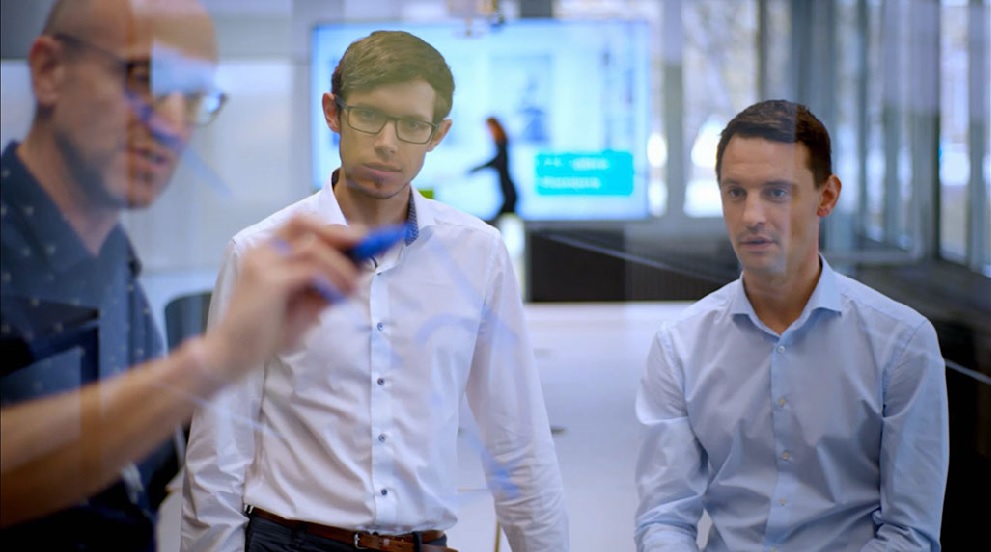
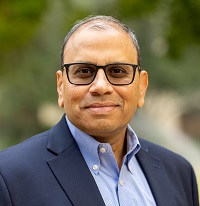
In a recent IndustryWeek Executive Summary, Rahul Garg, VP of Industrial Machinery and SMB Business Program at Siemens Digital Industries Software, and Giulio Camauli, Simcenter Industry Lead, Industrial Machinery at Siemens Digital Industries Software, participated in a webinar with other experts discussing how modeling and simulation technologies in industrial machinery manufacturing equate to positive performance, increasing quality and time to market, using reliable designs, material modeling, and consistent simulation.
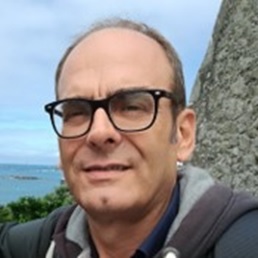
Simulation is moving to the next level for manufacturing; a beneficial process shift is occurring by adopting simulation techniques early in the design, manufacturing, and logistics processes rather than treating it as a back-end validation system. Companies that are leveraging digital modeling and simulation are leading the pack.
Digital modeling and simulation provide multiple layers
Modern manufacturing challenges are being addressed using digital modeling and simulation tools. System simulation for manufacturing companies does not sit with one functional or business group. Indeed, it has multiple layers and levels, combining electrical components and thermal physics, while the manufacturing and supply chain process allows us to understand the entire business more thoroughly.
Siemens’ integrated simulation solution combines design, validation, and supply chain functions to offer a cost-effective path to digital transformation. With over 50 years of experience in the industrial manufacturing software space, Siemens brings the expertise and knowledge to help manufacturers move toward the future of modeling and simulation.
More than five thousand libraries are available in simulation and modeling, helping speed production and energy consumption. This approach connects the modeling simulation environment of physical automation. These models can be embedded into the industrial edge to monitor the performance of the machine operation and feed that data back to the designer. As a side note, it can also train the operator.
Continued investment in modeling and simulation is mission-critical to a company or manufacturer. It works in tandem to create models of businesses, machines, and operations. It’s like opening the door to a system beyond the machine, from sales to the manufacturing line at a system level. Subsequently, it can move to the next level of the entire factory.
It helps address the significant issues and challenges in the industrial machinery industry. Indeed, we have all experienced global supply chain issues over the past couple of years. From a mindset perspective, people think of the supply chain as a purchasing function. This type of thinking must shift as suppliers are a vital part of delivering the desired specifications, using essential tools on their digitalization journey, scheduling alternative resources for supply chain functions and managing logistics in receiving parts. The entire modeling and simulation can be leveraged to obtain parts, design, and receive the goods to their factory.
So, modeling and simulation are not merely a catalog for a motor or system, but through an integrated environment, to share models. The supplier’s design can become a part of the machine, connecting the supplier with you, then sharing that knowledge and technology as part of your program to gain a competitive journey and make the supply chain fully functional and efficient.
Addressing the supply chain with digitalization
In the past few years, the pandemic showcased the fragility of the supply chain. Digital transformation technology was accelerated by this event, along with enabling technologies like modeling and simulation and others. We are witnessing companies collectively taking advantage of big data, AI, modeling, and simulation (a key enabler for the digital journey) and delivering on it through a SaaS or a cloud-based solution. These capabilities reduce the total cost of ownership, making it more accessible from an adoption perspective, with fewer skills required, providing ease of use for extensive success.
Furthermore, the value of the scalability applied to the infrastructure makes tools that once seemed difficult now more adoptable. The first step is using various disciplines for a structured simulation through a token license. With SaaS capability, all tools are available through a cloud server, so you can send your server simulation and run it in the modeling environment. Truly, it enables the technology to make the digital journey an ecosystem.
Cloud computing and SaaS increase marketability
Cloud and SaaS technologies enable more companies to access simulation tools and computing power. Another advantage of these innovations is access to critical technologies for the masses, making them more marketable, irrespective of the size or capabilities of a company. It’s not just for large, sophisticated companies. Now, with cloud computing, it can be used for small or start-up companies.
Internally, there is now access to a workforce and technology infrastructure that is scalable and acceptable of technology and the infrastructure. These innovations are applied and used for testing, research, and prototyping – from a production perspective – and they can simulate, for instance, how a robotic arm would be functional through process simulation, from the component to the cell, and how the goods are received, to their speed, and the functions of each capacity.
More companies are taking advantage of what modeling and simulation can offer. So, it’s coming to center stage to leverage modeling and simulation. It addresses the trends around reshoring and bringing production capacities closer to where they are being consumed, thus taking full advantage of these innovations. Auto-simulation provides benefits from a design and manufacturing perspective, bringing it to the front end, evaluating it, and taking it to the masses at total capacity.
Eventually, we can measure how operations are running and optimize the process with measurable capabilities of what is occurring on the shop floor, closing front-end models, designing the manufacturing intent, managing expectations, and adjusting operations.
Siemens Digital Industries Software helps organizations of all sizes digitally transform using software, hardware and services from the Siemens Xcelerator business platform. Siemens’ software and the comprehensive digital twin enable companies to optimize their design, engineering and manufacturing processes to turn today’s ideas into the sustainable products of the future. From chips to entire systems, from product to process, across all industries. Siemens Digital Industries Software – Accelerating transformation.