Talking Aerospace Today – The 5 Levels of Digital Transformation Maturity – Transcript
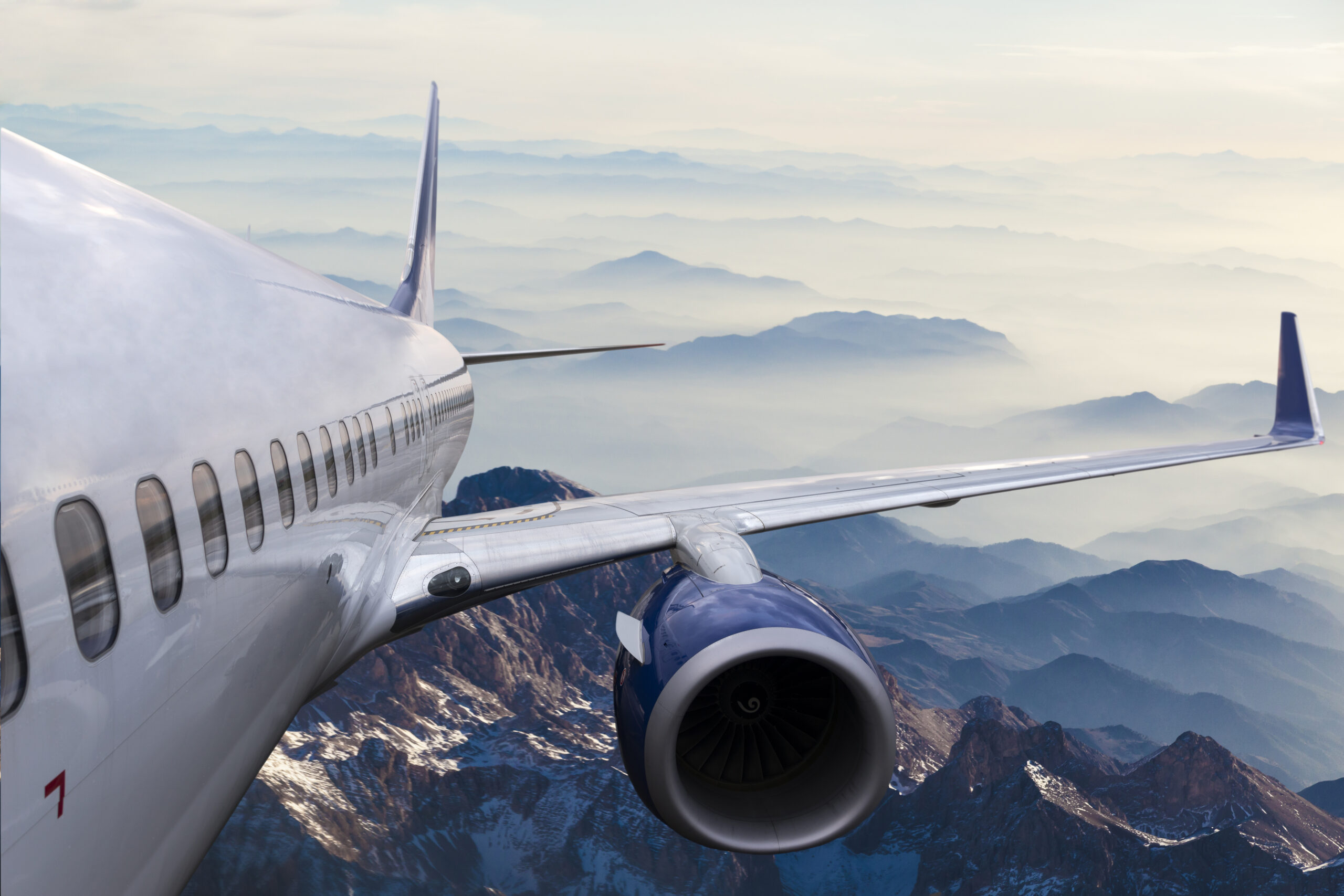
In the second episode of the Talking Aerospace Today podcast’s series on digital transformation maturity, Todd outlines the five steps companies can take their digital transformations to new heights.
Listen to the original episode or continue reading for the transcript.
Patty Russo: Hello, and welcome to Talking Aerospace Today. In our previous episode, Todd Tuthill, our industry VP for aerospace and defense here at Siemens, and I were discussing the need for the industry to consider digital transformation maturity and key drivers that our customers face. We talked about the growing shortage of engineers in aerospace and defense. We also talked about how companies are looking closely to their business processes to understand where they can leverage solutions across digital threads as demonstrated by the recent report by CIMdata we talked a little bit about last time. Many of our customers are realizing they need to take further steps, so today let’s talk a little bit more about the five levels of digital transformation and some of the benefits of the steps of digital maturity.
Patty Russo: Let’s talk a little bit now about what those next steps are and what are some of the benefits of the steps, of the five levels of digital transformation.
Todd Tuthill: Glad you’re going there. Yeah, we really see, this transformation, what I’ll call digital transformation maturity in five steps and I’ll list them off here. The first step is configuration, the next one is connection, the third one is automation, the fourth one is generative design, and the fifth one is closed looped optimization. So we’ll kind of start at the beginning and we really see that as a framework to help understand help companies understand where they at today, with their digital transformation, and what are the next steps and what do they need to do? So that’s kind of the five levels of digital transformation where we see it.
Todd Tuthill: If I think about where companies are at today, we start with configuration. That’s basically the ability to capture my data, put it in a safe place, and put metadata on top of it so that if I need to come back in two or three years and find it again and reuse it, or find it again and show it to the certification authorities so that I can certify my product for use for airworthiness, then I can find it. That’s configuration, and that’s kind of the first level and I would say right now nearly universally pretty much all companies are there. They have a configuration system in place. Many times we call that PDM product data management.
Todd Tuthill: The next step that we see on our path to kind of digital maturity or digital Nirvana, if we want to call it on our journey to digital transformation maturity, the next step is connection. And it’s not just knowing where my data is at, but it’s connecting the different pieces of data together, and we a lot of times that’s an aspect of PLM, product lifecycle management. It’s the ability to connect and trace information, so it’s not just that I have requirements and I have designed, but it’s the ability to say, “Here’s all my requirements and these are the requirements that drove this particular aspect of the design and then result in these particular tests.” And then, as happens in a complex aerospace development, things change. Requirements change, needs change, and then if things are connected in this digital thread that we pull through, if they’re connected, then I understand if requirement A changes, that means that these two aspects of the design change.
Todd Tuthill: These tests need to change and maybe these test artifacts need to change. Or if I’m already in manufacturing and production, it can also tell me that maybe I found a problem and I need to do some kind of redesign. I connect that design to my manufacturing process and it tells me which aspects of my manufacturing process and my recertification that I need to go to. That’s the connection. Those are the first two fundamental pieces that’s kind of where a lot of people in the industry are trying to get to it with their digital threads right now. So that’s kind of the first two steps and in the steps of five.
Patty Russo: So it sounds like a lot of companies are already making some progress. What are some of the other steps? Maybe talk a little bit about the what’s next?
Todd Tuthill: Right. What’s next to me is where it really gets exciting. We talked about ROI. And while I believe there is an ROI for the first two steps and those are important, I think the really, really significant portion of the feedback really or excuse me, the really important portion of the of the return on investment really happens at step three with automation. And automation is where I find ways to get the human out of the loop. Because while you know we have lots of great PDM and PLM tools, to configure data and connect data, a lot of those right now are driven by real human beings, configuration staff, engineers, and the next step is to start to automate all those things so that it’s not engineers making those connections, but we find ways to automate the connection of the data, and it’s not engineers writing test reports anymore, but we find ways to automatically generate all these tests reports and it’s something that I like to call “automate the mundane.”
Todd Tuthill: It’s one of the ways that, you know, we talked about bringing more engineers into the aerospace environment. “Automate the mundane things” is a good way to make the working environment better and more attractive to engineers. So automating the mundane is the first aspect of automation. The second aspect of automation comes from something, if you’ve been in aerospace very long, you’re probably familiar with Dr. Roper’s seminalwork on he called “There is No Spoon.” This whole idea of E-series aircraft and the vision he set a few years ago about where acquisition reform needs to go in the digital age. And he coined the term, he called authoritative automation, and he refers to that as not just doing things in computers, but creating methods and ways in the virtual world that dramatically decrease the work we have to do in the physical world. So it’s not just automating the mundane. That’s the first step, but the second step with automation is really authoritative automation, and that’s where we get into the next two steps, which are generative design and closed loop optimization.
Todd Tuthill: And those things are really key things and they’re driven by the need for artificial intelligence and machine learning. Generative design is where design tools can design things themselves based on learning from a data lake, a pool of data and the ability to create certain designs to create pieces of aircraft. It’ll start small parts. It will grow to larger structures and aircraft, and it really takes the human out of the loop and does, again, a lot of the aspects of putting PMI into mechanical drawings, of laying out circuit cards and doing all those kinds of things to really create the bulk of the design inside these tools for the engineers.
Todd Tuthill: And then the last step, the closed loop optimization is when we get to a point where we can do significant amounts of generative design. We don’t just want to design one thing. I don’t want to just design this once, but I want to be able to design this 1000 times or 5000 times and look at key performance indicators, and use simulation to evaluate the validity and the health and the practicality of those generative designs. And I put this feedback loop in place and look at things like, “Well, I don’t just want the wing of an aircraft that performs well. I want that, but I also want one that’s very manufacturable. I want one that is lightweight. I want one that is going to minimize the cost of the materials and the cost of building it.”
Todd Tuthill: And I can start to do all the things that human engineers do today, but do them in an automated fashion to the point where I can evaluate 5000 designs and present just a few to the human engineers to say, “OK, based on the request, the list of needs you gave me about the way to design this particular portion of an aircraft, here is the most optimized version of that. Look at that. Evaluate that before we go and build it.” And that’s really to me the essence of really making good use out of a digital twin, of really learning in the virtual world n thousands of cycles before we build in the physical world.
Patty Russo: That’s some really interesting and exciting insights that you are sharing here related to automation, generative design clues, loop optimization. I’d like to just digress for a quick moment related to the idea of generative design and AI. This is a topic that has been in, you know, we’ve heard it in news stories. We’ve talked about it in the industry. It’s kind of been this great theory, this great idea, but in reality there are some ways that it has some super practical uses like you’ve just talked about. And in the context of a conference that I was just at, there was a great description of what is meant by or what the description of generative AI is all about. And this presenter, he was the CEO of an analyst group related to marketing, but it applies here and it is, “Generative AI allows you to converse in your native language with a pile of data and create something new from that pile of data.”
Patty Russo: Which I thought maybe is over simplified, but it seems like a great explanation to wrap our heads around the whole idea of AI. So that being said, where does AI fit in the context of making tools easier for engineers to use? Maybe the other way to ask that question is where does the human element fit into the mix with AI?
Todd Tuthill: Wow, that’s a great question, Patty, and one that I think we might want to unpack in detail in a future podcast, but I’ll just talk about a few of the implications here. One of the things that customers talk to me about with respect to our products and we have, you know, fairly, very sophisticated products that do very sophisticated things and it pretty often can take a significant amount of learning to become very proficient with our products. And one of the things they’ve asked me is especially in light of the workforce, they’ll say, “Todd, you know, I’ll hire people and I’ll train them on these sophisticated tools that we use now for design. In a couple years, they’ll leave and I’ve just got to train them all over again.”
Todd Tuthill: He said, “Can you invest in ways to just make it just in time? So if I’m doing a task, the tool can really help me do that task and train me to do it as I run that task.” And I see AI as a very good way to do that, we can. There’s aspects of AI learning that can watch experienced engineers do things. We can train the tools with that and then present that in a natural language format to other people who aren’t necessarily as skilled in using that tool. So I see AI, one of the aspects of AI is just in the training of the people and making the complex tools easier to use, exposing them to the deep aspects and the key aspects of the tools, so that training is necessary, and so that people who are less experienced can really get the full benefit of the tools and, again, back to that working environment, it allows less experienced people to come up to speed faster, feel more effective faster, and really builds a better workforce and a better workplace. So that’s one of the many key areas I can see that AI can really help all of us in the use of these complex design tools in aerospace.
Patty Russo: So AI gets smarter and AI helps us get smarter. So is this all future-looking science-fiction, or does some of this already exist? You may have touched on a couple of these topics already, but where do you see these tools already existing and already in operation?
Todd Tuthill: Yes. So, great question and, again, I’ll go back for our audience because we’re not- it’s a podcast so we don’t have visuals, and we’ll talk about the last three steps. Automation, generative design, and close loop optimization. And the good news is, as you said, this isn’t science fiction. All of these three things exist today. At Siemens, we offer solutions that do these things right now in individual domains. I just came from a conference just this week called Realize Live in Las Vegas where I saw customers presenting back to us back to the industry, the things they’re doing, we’re doing generative design right now, inside of one of our tools, and we had customers presenting to us on generative design. We have solutions and automation that automate the writing of test reports that do all these kinds of things. We’re doing generative design on the mechanical side of our products. We have a great tool that already does optimization now.
Todd Tuthill: Now it doesn’t do it at the level, I can’t walk up to one of our tools and say, “design me an aircraft” and aircraft falls out the other side. I don’t mean to imply that. We’re not anywhere near to that point. I don’t know that we’ll get there anytime soon, but we do have aspects of these things that are available and in use by customers right now, but those things tend to be with- the solutions we have today tend to be within a single domain. Within an electrical domain, within a mechanical domain, within a software domain.
Todd Tuthill: The areas that I think we’re working for in the future is really connecting all those domains, and being able to do generative design of a major portion of an aircraft or spacecraft, not just the mechanical sections or the electrical sections, but all of those together and the structural sections, and really having all these tools communicate and work together better, which kind of goes back to where we began, to get to this connected future, this generative optimized future, it really starts with the fundamentals, of having all of our data clean and configured and connected, automating the mundane tasks so that we can go back to what Dr. Roper called authoritative automation. It’s a really exciting journey and as I said, an exciting time in aerospace and we can’t wait to partner with a lot of companies in aerospace to do that.
Patty Russo: So we’ve covered a lot of territory and before we close out for this session, I’d like to just ask you an open-ended question, which is, is there anything that I’ve not prompted you to cover related to digital transformation and digital transformation maturity that you’d want to cover before we sign off today?
Todd Tuthill: Well, I’ll say that there’s a mountain of information that we didn’t cover. We just touched on the you know, I’ll say just the individual pieces and whetted the appetite of our audience. I’ll say I think we’re planning future episodes of our podcast where we can dive deep into some of these topics, and I’ll go back to where I started. You know, it’s such an exciting time in aerospace with all these innovations. We at Siemens are looking so forward to working with our customers and people across the aerospace community to really bring digital transformation maturity everywhere. As we say all the time, digital transformation, it’s not a destination. It’s not a place you’re going to get to and finish. It’s a journey. We’re learning it, Siemens. We’re learning all the time just like the aerospace industries learning all the time, creating new innovations, new needs for things. And we at Siemens are so proud to partner with and be a part of all these great innovations. And Patty, I can’t wait to talk to you and our listeners in detail about several of these things we’ve talked about today.
Patty Russo: Likewise, I’m looking forward to the next conversation about this topic as well. Today we covered a lot of, like I said, we’ve covered a lot of territory. It’s a great time to be in aerospace and defense based on the projections for growth and innovation that’s happening across the board. We talked a little bit about our challenges and customers’ challenges related to the workforce and how digital transformation can help potentially close that gap and then some. And you covered a little bit about the steps toward digital transformation and I think there’s probably a lot more that we could dig into, but this is a great place to pause. We’ll call this our cliffhanger and pick that up, perhaps on a subsequent podcast. That’s all the time we have for today. Thank you Todd for sharing such great insights and we can’t wait to talk in our next episode.
Siemens Digital Industries Software helps organizations of all sizes digitally transform using software, hardware and services from the Siemens Xcelerator business platform. Siemens’ software and the comprehensive digital twin enable companies to optimize their design, engineering and manufacturing processes to turn today’s ideas into the sustainable products of the future. From chips to entire systems, from product to process, across all industries. Siemens Digital Industries Software – Accelerating transformation.