A digital thread drives smart manufacturing
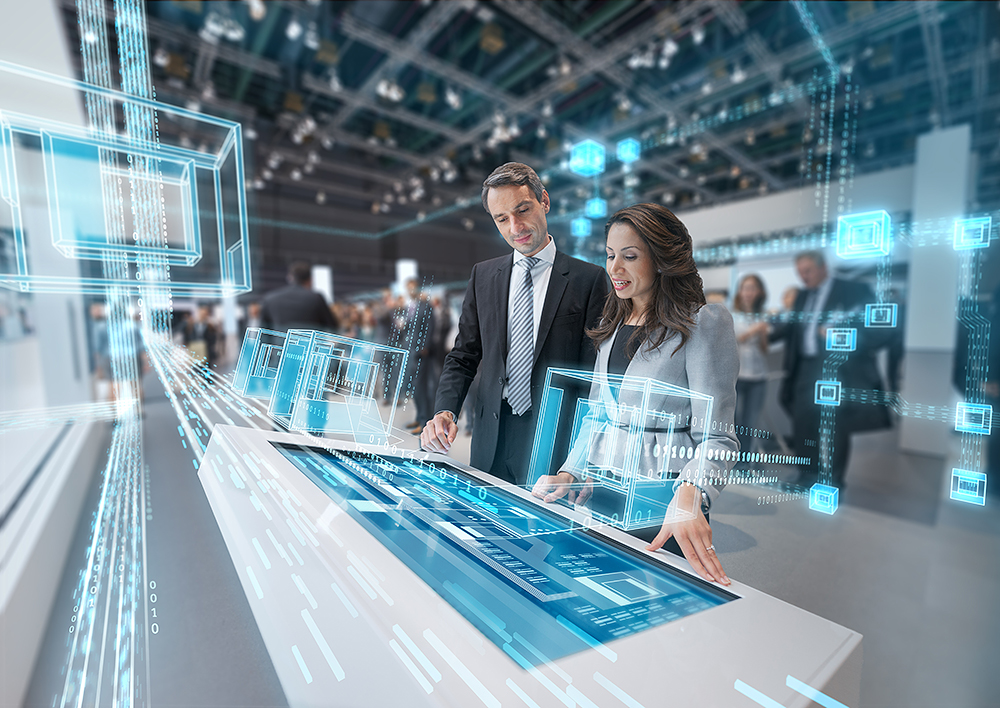
The industrial machinery manufacturing sector is undergoing groundbreaking technological advances using smart manufacturing. However, it can be intimidating to validate and manage modern manufacturing and assembly operations to achieve premium quality while optimizing cost. Manufacturers need additional content, like sensors and feedback, to execute the production and manufacturing processes in the machining industry. Then leverage this information into the manufacturing digital twin. For instance, creating a machine tool requires an inspection data process for design traceability, manufacturing, and closing the loop with a high-fidelity digital twin.
For more information: Download the white paper.
Then it is essential that the product’s digital twin links with the machine’s digital twin. When using mart manufacturing, industrial machinery manufacturers can extract information and drive it into manufacturing operations. This process includes computer numerical control (CNC) programming or inspection and assembly processes. A digital twin formulates from this information at the product level.
A comprehensive solution is necessary to be aware of every step in the manufacturing process, including idea creation, developing the product with machining, executing in manufacturing, and extending across the entire service life based on the digital twin.
This process enables machine manufacturers and designers to create value, drive costs down, and compress delivery schedules. It also closes the loop faster between manufacturing operations and engineering. The manufacturing industry is continually changing due to connectability, adaptability, predictability, and extendability. Also, there is a shift in the smart manufacturing approach by offering production-as-a-service, in which customers buy machine capacity instead of purchasing the machine.
This change is primarily occurring with equipment manufacturers that lease machines. So, they only pay for performance when using the machine. Subsequently, the OEM ensures that the machine is always running at its best. Suppose machine upgrades are necessary to meet production requirements and general service. In that case, the OEM corrects performance improvements or downtime issues and ensures it is running quickly to capitalize on cash flow.
3D printing, digital twin and smart manufacturing
The manufacturing industry has been moving towards 3D printing/additive manufacturing in recent years. From a machining perspective, it permits the machine designer to consolidate components using the additive manufacturing process, leading to less expensive parts, superior reliability and increased durability.
This process includes the digital twin. The digital twin needs more than additive manufacturing in smart manufacturing; it also contains post-process machining and several make-ready processes for industrial machinery assembly. The digital twin incorporates designing parts or mechanical components, adding flexibility and adaptability to reflect the electrical part, the software and the programmable logic control (PLC). A multidisciplinary approach incorporates a digital twin, which is essential to have the correct software to manage it.
Siemens Digital Industries Software provides a comprehensive executable digital twin with software that realizes all the steps in the manufacturing process – idea creation, machinery production, execution, manufacturing and extending the service life. Siemens is a leading provider of industrial automation, the largest industrial automation supplier globally, so they know how technology needs to integrate into the machinery.
Manufacturing – disciplines and space
The manufacturing disciplines must generate the coordinate measuring machine (CMM) or inspection files to automate the system manufacturing process for mechanical, electrical or software. It is essential to simulate the engineering software to execute the product and provide a physical domain. Electrically, there can be various manufacturing requirements, especially when equipment is from multiple vendors. Machinery customers often have requirements that specify the machine needs to contain only specific manufacturer’s components.
This is common in electrical and fluid areas, where the customer has machinery standards in their plants. The machine builder chooses various hardware based on exports to different regions. Though the machine functionality might be similar, their electrical and mechanical configuration could differ. This variability must be reflected in the machinery builders’ digital twin.
So, it involves not merely building the part and executing it but managing delivery, manufacturing, operations and quality. There is a need to manage manufacturing operations to provide insight that coordinates all activities to deliver the correct parts at the right time. An all-inclusive approach that is low volume and highly complex is one of the differentiators of smart manufacturing and additive solutions, solidifying the dynamic process of additive manufacturing.
It’s a multidisciplinary approach incorporated into a comprehensive digital twin, and it is vital to have the exact software to manage it. Engineers provide the optimal design to balance cost and durability based on machine dynamics and up-front simulation. Also, there is a closed-loop environment where manufacturing can use the same model for machining and fabrication based on the machining simulation, thus providing accurate cost estimates.
So, it uses an integrated change management process, where manufacturing informs engineering about the real cost drivers for the part. Subsequently, engineers can iterate quickly on a solution that provides the same durability at a lower fabricated cost. So, Siemens follows this multidisciplinary approach, so manufacturers can continually seek ways to take advantage of the most recent innovative thinking. In addition, this methodology enables the user to profit from every aspect of the manufacturing process with various volume scales.
Siemens is continuously working to help industries worldwide take advantage of this fast-growing technology. As a result, they can provide a comprehensive solution to realizing every step in the manufacturing process, including idea creation, developing machining products, and executing the entire service life based on the digital twin, helping customers succeed in highly competitive markets across the world.
Learn more in the Smart Manufacturing white paper.
Siemens’ software solutions
Siemens’ Xcelerator portfolio helps companies of all sizes create and leverage digital twins that provide organizations with new insights, opportunities, and automation levels to drive innovation.
For more information on Siemens Digital Industries Software products and services, visit siemens.com/software or follow us on LinkedIn, Twitter, Facebook and Instagram.
Siemens Digital Industries Software – where today meets tomorrow
Related links:
Industrial-machinery and smart manufacturing
Implementing smart manufacturing for a smart factory
Smart manufacturing and industrial machinery – Podcast series
About our expert
Rahul Garg is Vice President of Industrial Machinery and the SMB Program for Siemens Digital Industries Software. He and his team are responsible for identifying and delivering strategic initiatives and developing solutions for the industry, working closely with industry-leading customers and providing thought leadership on new, emerging issues facing the machinery industry. Rahul’s experience and insights are derived from a 25-year career of delivering software-based solutions for product engineering and manufacturing innovation for the global manufacturing industry. He has held leadership positions in multiple areas, including research and development, program management, sales and P&L management, having focused exclusively on the industrial machinery and heavy equipment industry since 2007. Rahul holds a master’s degree in Computer Science from Wayne State University, with a concentration in Operations Management and Strategic Marketing, as well as a Bachelor of Computer Engineering degree in Computer Engineering from Bombay University.