Smart manufacturing with additive and a digital twin
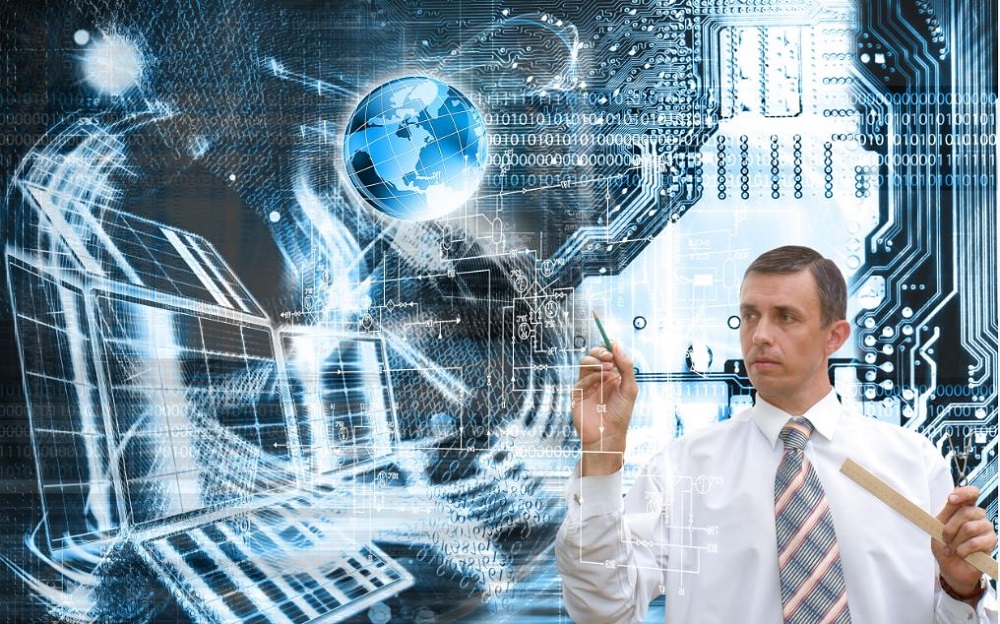
Recent technological changes have propelled manufacturing towards additive manufacturing (AM) or 3D printing. When machine builders use additive manufacturing, designers can merge components, provide economic parts, optimum reliability, robust durability, and creative design.
In addition, smart manufacturing provides an essential comprehensive digital twin for successful additive manufacturing to include more than merely the 3D process. The digital twin offers post-process machining and make-ready processes for industrial machinery assembly. Furthermore, this digital twin process incorporates electrical, software, and PLC programming. It provides a multi-disciplinary approach to creating a complete digital twin, where having the correct software is critical to managing it.
The digital twin is a holistic representation of a product, its performance, and processes for manufacturing. It parallels advancing mechanical, electrical, hydraulic and fluid devices, including pneumatics, design domains, performance and product simulation. Several software packages simulate these domains and perform well. However, the manufacturers of industrial machines and consumer products must meet customers’ changing requirements. Therefore, it is an environment requiring a strong focus on flexibility and shorter development times.
Digital twin process
A digital twin addresses challenges and optimizes production beyond the factory floor. It signifies all phases of the machine life:
- ideation (engineering and simulation),
- realization (manufacturing and requirements) and
- utilization for operation and maintenance information.
All this data helps complete the machine, including the individual serial and numbered parts.
The digital twin is essential to build and execute the printing of 3D parts while managing delivery, manufacturing, operations and quality of manufacturing operations management. These elements provide insight into delivering the correct parts at the right time. In addition, manufacturing machinery requires elaborately coordinating the supply chain, internal manufacturing and assembly. Thus, a united knowledge management component is vital for designing and manufacturing.
Virtually simulate a machine
Using a digital twin to design and manufacture machines provides another advantage using the virtual machine simulation and commissioning process that validates a manufacturing machine’s software code virtually before physically operating on the factory floor.
Machine behavior is driven by software that simulates the code on a machine’s virtual twin to generate substantial benefits by reducing time and resources when commissioning a new manufacturing machine or reconfiguring a new product type on the production line. The PLC software code validates using a modular product development strategy in a controlled environment. Therefore, machine builders can simulate this process upfront, linking the software to the modules.
Safety of a digital twin
If a machine collides in the virtual world, it’s markedly safer and less costly to fix than a physical machine. This is because virtual commissioning drives motor behaviors, integrating that data into the kinematics. This process provides a commanding capability when a machine’s mechanism moves faster than expected, resulting in a higher impact load. So, replicating the kinematics in the virtual commissioning reveals potential threats to provide immediate resolutions.
By embracing the digital twin and virtual commissioning, manufacturers collaborate with machine suppliers in a virtual environment, digitally interacting with the machine, which pays significant dividends financially. And you don’t purchase a machine without seeing it operate correctly. Or buy it based strictly on the claim of simulating and validating the PLC code. Therefore, a manufacturer must validate that a machine works correctly in its environment before it ships to the factory. So, the virtual commissioning via the simulation process provides essential solutions to overcome verification hurdles. The resulting advantages exhibit positive results in many industries, including electronics.
Digital twin and electronics
Electrical devices are entering the market rapidly. In response, separate lines for each product must be created and dismantled, then repeat the process in short production cycles. So, machine builders must deliver new machines rapidly and quickly adapt to short-term revisions. In addition, the commissioning phase of machines and lines is constantly changing from manual to automated production, providing the opportunity to meet the time constraints of electronics companies. Siemens provides ideal automation and digitalization solutions to create a machine’s digital twin. Consequently, it helps develop new machines and lines quickly with significant flexibility.
Experts are essential to electronics companies, providing a comprehensive portfolio for delivering a digital approach based on a digital twin. They offer complex hardware and software for small or large tasks with varying degrees of sophistication. Hence, high-end applications are as simple to implement as fundamental tasks, providing a straightforward production process of speed and cost-effectiveness. Consequently, there is a paradigm shift in industry trends and innovative manufacturing and machine suppliers’ advancements.
Smart manufacturing, digital twin and future of manufacturing
In conclusion, smart manufacturing using a digital twin and virtual commissioning simulation is a notable endeavor in the future of industrial mechanical design. This powerful feature, across design concept to product end-of-life, provides quality-of-life improvements to the design engineers and the business manufacturing, operations or management. In addition, providing virtual commissioning capabilities empowers machine building, the process line, and virtual simulation before shipping the physical product reduces downtime.*
By using the Xcelerator portfolio, via Siemens Digital Industries Software suite of products, it assists to simulate testing virtually, saving time and money in modeling, and optimizing operations before construction or equipment installation begins. The digital twin for smart manufacturing saves time and money for the machine manufacturer, the product manufacturer, and the end customer. They now know what needs to be built, thus providing exceptional value for all parties. Smart manufacturing with a comprehensive digital twin is where today meets tomorrow.
Related links and sources:
*Making additive manufacturers smarter via the digital twin – Electronics Weekly
Accelerating value realization in the smart factory – eBook
Smart manufacturing takes center stage in 2022 – sme.org article by Rahul Garg of Siemens
Smart machines, smart engineering (blog)