Future-proof with the IoT miniseries – ep. 4 Transcript
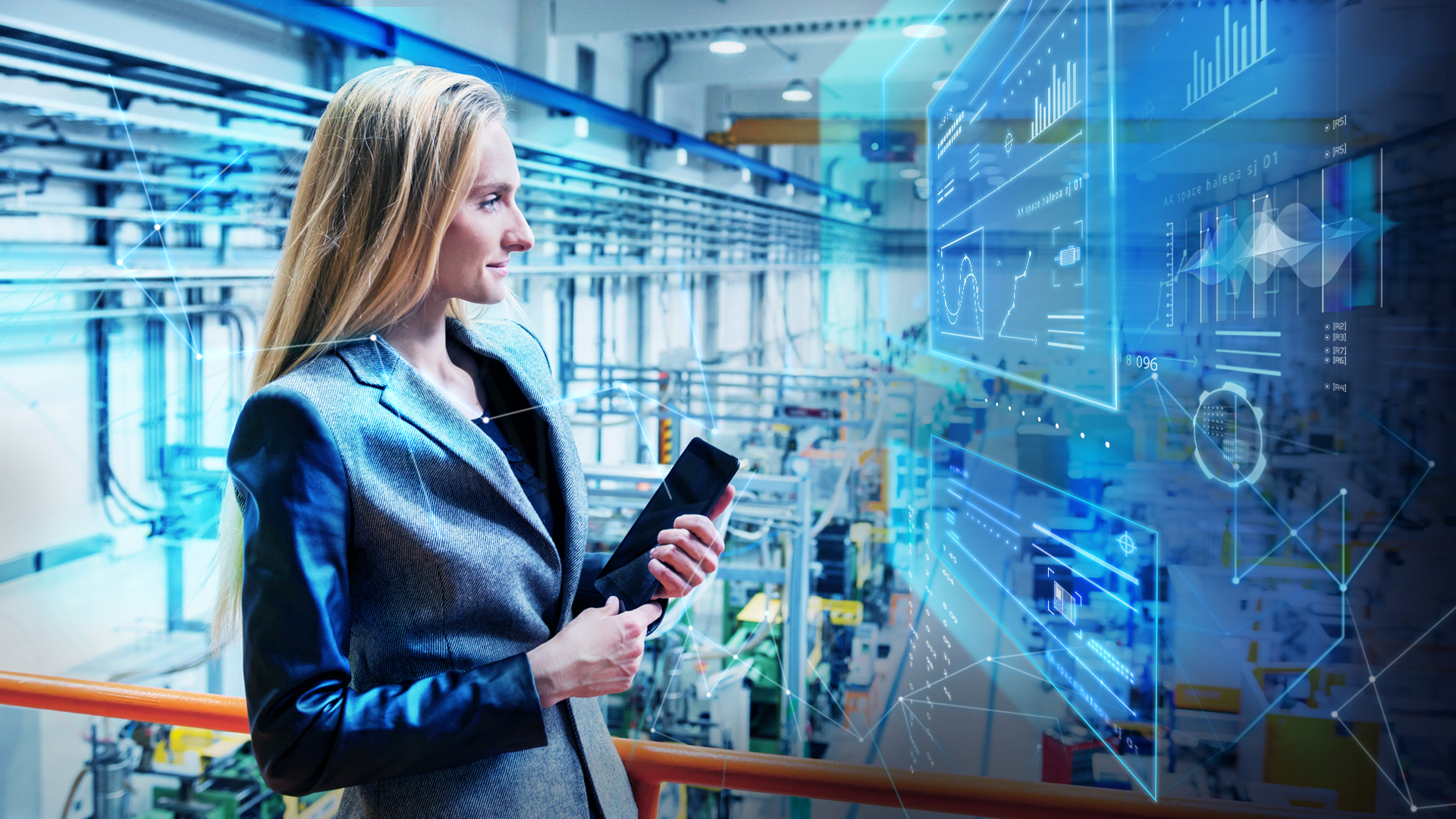
Whether you missed it or have been waiting for the transcript to read it, episode four of the miniseries Future-proof with the IoT is out! With a cooperative understanding of the challenges facing industrial machinery and the benefits an internet of things (IoT) solution can bring, our experts dive into how to architect your solution to fit your needs. Whether you are ready to build it in-house or are looking to hire IoT experts, this episode is full of insights on what an IoT implementation can be. And for those looking for more evidence of the benefits, Sebastian Oeder and Heiko Dickas of the Siemens Bad Neustadt factory offer their insights as to how IoT has improved their processes.
Sit back and read along or put in some headphones for a walk and a great discussion on how to implement an internet of things infrastructure for your industrial machinery business:
Jörg Ludwig: Hello! This is “Future-proof with the IoT”. A podcast mini-series for the IM industry, learning how to leverage digitalization to overcome manufacturing disruptions and bounce back stronger. I’m your special host, Jörg Ludwig.
If this is your first time joining, don’t forget to catch up on our first three episodes. They are available now on all your favorite platforms, and we’ll include a link in the description.
Today, we’ll continue talking about how the Internet of Things (IoT) can help with some of the challenges in manufacturing.
Joining us again today are Colm Gavin, Portfolio Development Manager at Siemens Digital Industries Software, Matthias Lutz, Head of PreSales and Solution Design at DI SW, and Heiko Dickas and Sebastian Oeder, leader of the digitalization team and head of the production unit main motors at the electric motor factory – Siemens Bad Neustadt.
Let’s get started! Colm, are there any other solutions and benefits IoT can offer to face the challenges of the manufacturing trends: new IoT business models, hyperautomation, low-cost competition, and new generation workforce?
Colm Gavin: From my standpoint, a key topic that shows the benefit of how IoT can be used is in conjunction with our simulation tools for what we refer to as closed-loop digital twin. This is, you know, taking the feedback from the machines and pushing it back into the simulation model. This means that simulation tools – in our case, such as plant simulation – can be used not only in the concept phase of the production line but also in the continuous optimization of the line, where data coming off the line can be fed to the cloud, and from the cloud directly into the plant simulation tool. And we’re doing that in a very easy way as far as configuration of “which machines are you connected to? When do you want the data? How often do you want the data? And how long should you collect the data,” and so on. So, what this means is that you can record data from a previous shift, and then use this data to run the simulation model in playback mode. And why would we do that – to look back in time – is we want to verify where are the bottlenecks because then with our simulation tools, we can run an eight-hour simulation in just a few minutes. And we can use the analysis tools already built into, again, tools like Plant Simulation where they have a whole suite of tools to look for bottlenecks. in the past, it was always like, “Well, what’s the data would we use for the simulation model to use hypothetically?” But now, if we can push data via IoT, we can get the data directly off the machine, use that as the basis for the simulation model. So, as a result, using IoT, the data used in the simulation model, results in a far more accurate simulation and forecasting. This is particularly useful in use cases where there are a lot of daily optimizations or weekly optimizations need to occur.
Matthias Lutz: The technology is there, everything is possible, and you have to start somewhere. And not starting now and waiting for everything to be there would be a massive mistake. So, imagine you are having real-life data from your machine in production somewhere in the world, and you’re directly using all the technology out there to monitor this data and to come up with new models for maintenance. What I see as well in many customer engagements is that predictive maintenance based on IoT is a perfect combination together with existing or new remote service solutions.
A couple of other use cases, I would like to share, based on our experience is, as well inventory management or spare parts management. So, if you have once identified a failure in one part of your machine, you can immediately trigger via an SAP interface, a service order, or an order for a spare part. But I think that’s the start where a lot of our customers are right now working on; they see the benefits. IoT has the potential to increase the speed and performance by reducing energy consumption; simply because of that the data was missing before. So, based on a sound data analytics, performance increase is possible today which hadn’t been possible in the past. One of the greatest things about IoT is as well the increased connection to the user and the customer. So, there’s a whole new way how humans interact with machines; they are not interacting anymore based on a human machine interface; they are interacting on data.
Heiko Dickas: Manufacturers need to turn to digitalization, and specifically automation, with the IoT and AI. As also Matthias mentioned, connect and constantly analyze the performance of machines delivers many hints of things which can be improved, and it’s also a good starting point for digitalization. A lot of customers visiting the arena of digitalization each year in Bad Neustadt and some of them are asking how they can step into digitalization? And that’s my answer: start collecting data, have a look at the performance and you will get many ideas to development, improvements maybe in a small area and keep it simple, but do it. And not only at the shop floor; we see potential also in administrative areas digitalization is supporting. Using the digital twin of a machine can increase the utilization of a machine but also it can work on it to get the full potential of a machine or bringing software robots in your daily life. Everywhere you do some simple copy-paste or transforming jobs, there are good solutions available to improve your business. And this leads then also to the topic that low-code application development can create efficiencies.
Jörg Ludwig: Taking a step back to the system architecture, there are really two options when implementing the Industrial Internet of Things: build your own IoT solution or adopt a ready-made one. For either option, it is critical to come into the project prepared. Which path would you recommend to whom? And why?
Colm Gavin: I think the discussion “Make vs. Buy” is probably one of the most critical decisions machine builders, manufacturers have when looking at IoT and how it can help. Because fundamentally, it comes down to a topic of resources and support: what resources do you have available to build the solution? Do you have the know-how in your IT department to be able to build a cloud or a cloud system and then support and maintain that? And I think a big question, especially a lot of midsize machine builders need to ask themselves: “Do you really want your IT department to be responsible for the creation and maintenance of a cloud-based solution for remote monitoring or predictive maintenance?” In some cases, maybe they do, but you’re going to have those resources there, so if they’re not there, what do you do? And “how will you remain flexible enough to innovate for the future? How do you establish the connectivity across new and existing industrial assets? What about wireless?” People don’t want to run long cables anymore. And then, critically, “how can you ensure that you reap the benefits of digitalization across design, manufacturing, and service?”
One thing I’ve noticed, we saw many manufacturers or companies that were supplying the sensing technology on equipment that would be used for condition-based monitoring. When they were offering those solutions, at the beginning, a couple of years ago, we noticed that they would try to sell those solutions by offering their own cloud-based solution to go along with the sensors that they were selling. And what we found is that many of those companies; they found it’s not sustainable, or they can’t sustain that level of investment and support to manage a cloud-based IoT solution. And that’s where Siemens can really step in and take that load off the backs of the IT department, so that the focus is on your machine and your application running on that machine. And you’re the industry knowledge expert for what to do with that data, and that’s so you can create an application that can provide value to your customers. Everything behind that; behind the scenes – the infrastructure, the support required – do you really want to have to manage that yourself? Or work with a company like Siemens that can take the load off with our MindSphere solution?
Matthias Lutz: I completely agree, Colm. I have seen a lot of IoT teams, customers, and IoT projects. And what I’ve perceived frequently is that, let’s say those teams spend 80% of their very rare resources in maintaining a platform, running this platform 24/7 on five continents. And they find themselves very often in a situation where they only can spend 20% of their time in actually developing the value add for their business stakeholders. And exactly, with a prebuilt industrial IoT solution, you can turn this equation around. It’s all about time, costs, risk, and of course, the whole ecosystem around it which enables you to build an IoT application in a much faster way.
I want to focus as well a bit on the innovation path. So, a pre-built solution really enables you to participate in the innovation power of Siemens. So, we are developing, operating, and innovating the solution for our machine builder customers and manufacturing customers in a constant way. And we want to free our customers up from this burden and give them the option to focus on their value-adding activities around app development and supplying their internal users with the applications which really lead to some measurable benefit.
I would like to highlight, as well, a bit the workforce and skill topic. I’ve recently read a study from Gartner done together with LinkedIn, and they are outlining or reporting every year the most in-demand skills worldwide in the industrial arena. You may not wonder but out of those 10 most in-demand skills eight are needed to be successful in IoT and in digitalization and manufacturing in general. So, those skills are, of course, things like cloud security experts, cloud architects, data scientists, and a couple of others. I think that’s very important. We can free our customers up from, let’s say, running this cloud infrastructure, and they can focus more on their value-adding applications.
Jörg Ludwig: Thank you. Matthias, for this great insight. So, Sebastian, what kind of improvements has IoT brought to Siemens Bad Neustadt?
Sebastian Oeder: There are quite a lot of examples. We have improvements in many different fields of our operation, depending on the use case. Let me give you some examples from the different areas. We’ll reduce the required process for us to pull our stator windings into the stator by around 20% as we analyzed the required force of every single cycle, linked it to the respective tools, and changed tooling and process parameters; detailed cycle time analysis helped us to optimize the output of bottleneck processes; the optimized sequencing of orders reduced setup times of machines and also supports further logistics improvements; condition monitoring extended by automated analysis of disturbances show us which specific problem at the machines causes the biggest losses. As I said, the analysis of test results by AI helps us to reduce testing efforts. And for maintenance, the change from maintenance by fixed cycles to maintenance by usage reduces our maintenance cost; just to give you a rough overview.
Jörg Ludwig: Thank you, Sebastian. So, the Head of Siemens Bad Neustadt factory, Peter Deml. He has been quoted recently; what he said is: “By using the digital twin, we have reduced the machine setup time from eight weeks down to two weeks. As a result, we now specify the digital twin for all new machine purchases.” And those are incredible results. So, Heiko, can you speak a bit more in detail, how the closed-loop digital twin has been implemented in the factory? And what other benefits have you personally seen?
Heiko Dickas: Using digital twins is one of our core elements in digitalization. In general, we distinguish three digital twins: the digital twin of the product, production, and performance. The example Peter Deml mentioned was when we asked an OEM for a new machine tool a few years ago, we told them to have the digital twin of the specific machine two to three months before delivery of the real machine. We got this and we implemented this in NX CAM, and with this, we could prepare a lot of things very early: clamping situation of the workpiece in the machine, the needed tools, the CNC program, and so on. The result then was that after installation of the real machine in our shop floor, we could start immediately with production, and commissioning time was reduced tremendously as mentioned before. And we used the digital twin also for optimization of existing CNC programs and had benefits up to more than 20% of reduced machining time, that’s also a lot of benefits what we have created here. But not only machines, but also for processes, we use digital twins, and therefore, a plant simulation or a process simulate is also in operation. Starting also with a small proof-of-concept, decided later to have an employee who is taking care of simulating the whole factory step by step. And for bigger investments, it’s mandatory to simulate a new process before any order is started. Also, here, we save money on new investments, having a digital twin of the process first to see how everything is working if doing things in a different way, and that’s a big benefit for us. And with a digital twin of the performance, we identified productivity gaps in specific areas like our mechanical prefabrication up to 25% more utilization, and we could take out several machines out of production, could save maintenance cost, and so on, and generate ideas for automation topics. As you can see, we use different digital twins but always with a very good result.
Jörg Ludwig: So, for the time being, MindSphere, Siemens leading industrial IoT-as-a-service solution is not being used for closing the loop of the digital twin. But where is MindSphere being used at Bad Neustadt?
Heiko Dickas: Not everywhere we are using this. MindSphere is also used to optimize processes: doing first, condition monitoring, use cases transparency, machine status, alarm dashboards, digital time management, to mention a few examples. Also, in combination with SAP or with energy data from the machines.
Jörg Ludwig: Do you think the MindSphere solution fits well with your factory activities? And if so, why? And would you personally recommend it?
Heiko Dickas: Yes, from my point of view, it’s a good solution. And it’s not still at the end what MindSphere can deliver or provide to support us. Having a clear view on the overall architecture of our factory, we can focus on the use cases. We are very flexible using all kinds of data sources, and we are independent of the devices. We have seen in the last year a very good development and our progress and savings generated with MindSphere are increasing. Start simple and small; learn fast and do your experience but start now.
Jörg Ludwig: And with that great advice, we finish this episode. Thank you all, it was great having you on the show again! And thanks to our listeners!
We still have a lot to learn about the benefits of IoT, and we hope to have you back for our last episode on how fluctuating and even volatile economic conditions such as a pandemic or other natural disasters can affect a manufacturer. We’ll discuss how IoT can ease the costs and pains associated with such events. Until then, take care!
About the Host and Guests
Jörg Ludwig – Since 2018, Jörg has been in the sales enablement team for MindSphere and since October 2020 also for Mendix, globally responsible for the creation of learning paths, enablement sessions, and value selling trainings and workshops. Prior to Siemens, Jörg ran his own business as a Value Selling trainer and coach for more than 7 years. He gained Sales experience and expertise from over 16 years in global Software Sales organizations.
Heiko Dickas – Heiko is the Team Leader of the digitalization team since the beginning of 2017 in the Bad Neustadt motor factory. His scope is being an enabler for the production unit in terms of digitalization. Heiko has been with Siemens for more than 30 years in different functions.
Colm Gavin – With over 20 years of experience in the Siemens Digital Factory, Colm works on business development for digitalization topics as they pertain to Siemens SW and Factory Automation, specifically virtual commissioning, Industrial IoT, Industrial Edge and AI topics.
Matthias Lutz – Matthias joined Siemens 14 years ago, starting in supply chain and procurement department. In 2015, he moved to the industrial customer service organization, focusing on industrial IoT and digital services.
Sebastian Oeder – Sebastian is Head of the production unit main motors in the Bad Neustadt motor factory. He has a background as a production manager at Siemens Energy and as a consultant at Siemens Corporate Technology.
Siemens Digital Industries Software drives the transformation to enable a digital enterprise where engineering, manufacturing and electronics design meet tomorrow. Xcelerator, the comprehensive and integrated portfolio of software and services from Siemens Digital Industries Software, helps companies of all sizes create and leverage a comprehensive digital twin that provides organizations with new insights, opportunities and automation levels to drive innovation.
For more information on Siemens Digital Industries Software products and services, visit siemens.com/software or follow us on LinkedIn, Twitter, Facebook and Instagram.
Siemens Digital Industries Software – where today meets tomorrow