Digital Part Production – synchronized part production – ep 3. Podcast
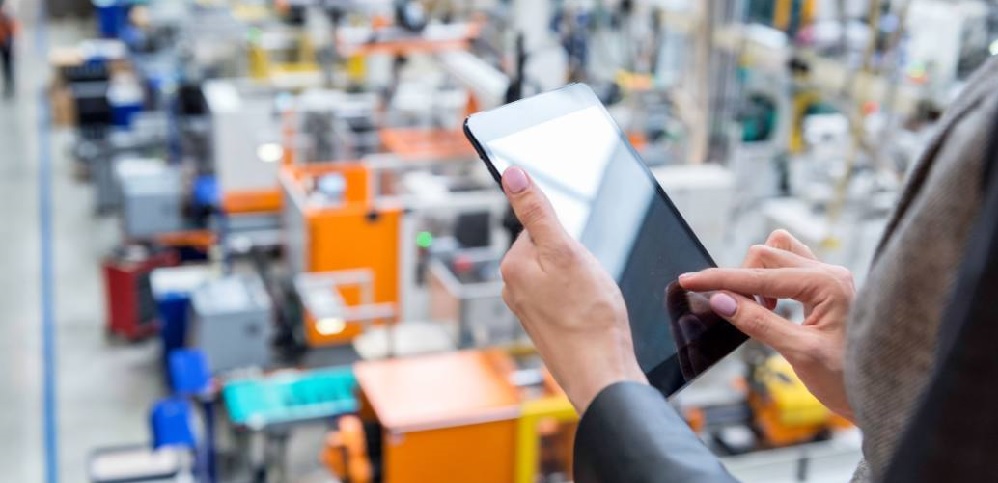
Key trends continue to shape the industrial machinery landscape, including differentiators that include highly automated CAM, synchronized part production and additive manufacturing. We presented the DPP Overview and highly automated CAM as part of the Digital Part Production (DPP) series in previous podcasts.
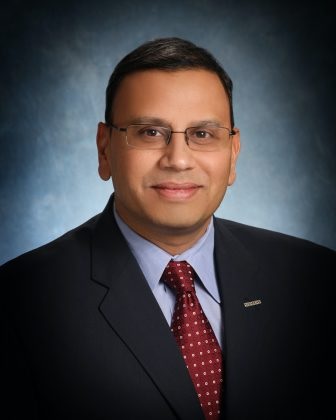
This third DPP podcast focuses on synchronized part production.
>Listen to DPP Podcast03
We address how equipment manufacturers can improve their planning by adopting and executing a closed-loop manufacturing process to enhance their manufacturing plan by introducing intelligence into it.
We are pleased to welcome our engineering experts Rahul Garg, Vice-president of the mid-market program at Siemens Digital Industries Software, and Brad Rosenhamer, Portfolio Development Executive for Siemens Part Manufacturing Software portfolio.
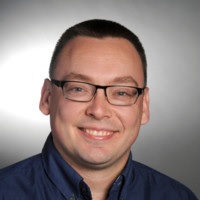
Machine builders are facing the challenge of improving efficiencies and quality to their part manufacturing processes. Most manufacturers struggle with getting the correct data to the right person at the right time. Also, manufacturing information flow is becoming more complex as authoring and collecting data occurs across a greater diversity of personnel and processes in organizations – both automated and manual – with the challenge to combine it all. So, manufacturers want to leverage this data in their decision-making.
However, without organization and data structure, the results can vary. It is essential to leverage this information for sound decision-making. Otherwise, it can lead to mistakes and waste across the entire product lifecycle. Therefore, customization is a significant opportunity for manufacturers.
With the increasing complexity of the industrial machinery industry, companies add more customizations into their modularized machines. These customizations do not change the delivery schedules or prices expected by their customers, who still want it delivered in a lean manner. Therefore, synchronization is essential to previously standardized customer-configured components.
These components include complex geometries with tighter tolerances and lower lot sizes. Introducing these variations into a product creates a new supply chain problem that requires synchronizing component part production while minimizing inventory and costs. There is a need for lean concepts that apply to standardized parts of the past. If it’s not synchronized, part inventories must increase, and warehouse space must accommodate that increase, while lead times for deliverables are lengthened. Ultimately, this impacts the organization’s competitiveness in an industry where speed and capability are critical aspects of the business.
>Learn more by listening to DPP podcast03.
Siemens Digital Industries Software drives the transformation to enable a digital enterprise where engineering, manufacturing and electronics design meet tomorrow. Xcelerator, the comprehensive and integrated portfolio of software and services from Siemens Digital Industries Software, helps companies of all sizes create and leverage a comprehensive digital twin that provides organizations with new insights, opportunities and automation levels to drive innovation.
For more information on Siemens Digital Industries Software products and services, visit siemens.com/software or follow us on LinkedIn, Twitter, Facebook and Instagram.
Siemens Digital Industries Software – where today meets tomorrow.
Related links:
Listen to DPP Podcast01 – an introduction to Digital Part Production
Listen to DPP Podcast02 – highly automated CAM
Listen to DPP Podcast03 – synchronized part production
Listen to DPP Podcast04 – benefits of additive manufacturing
Rahul Garg is the Vice President for Industrial Machinery & SMB Program, responsible for defining and delivering key strategic initiatives and solutions and global business development. He and his team are responsible for identifying key initiatives and developing solutions for the industry while working closely with industry leading customers and providing thought leadership on new and emerging issues faced by the machinery industry. Rahul’s experience and insight are derived from 25 year career delivering software-based solutions for product engineering and manufacturing innovation for the global manufacturing industry, spanning a career in R&D to program management, sales and P&L management and having focused exclusively on the industrial machinery and heavy equipment industry since 2007.
Brad Rosenhamer is a Portfolio Development Executive and experienced Senior Director of information Technology, focusing on infrastructure and application, with a demonstrated history of working in the mechanical, electronic and industrial engineering industry. Brad is skilled in value-driven business process strategy, development and implementation.