Accelerating production ramp-up – now’s the time for lift-off
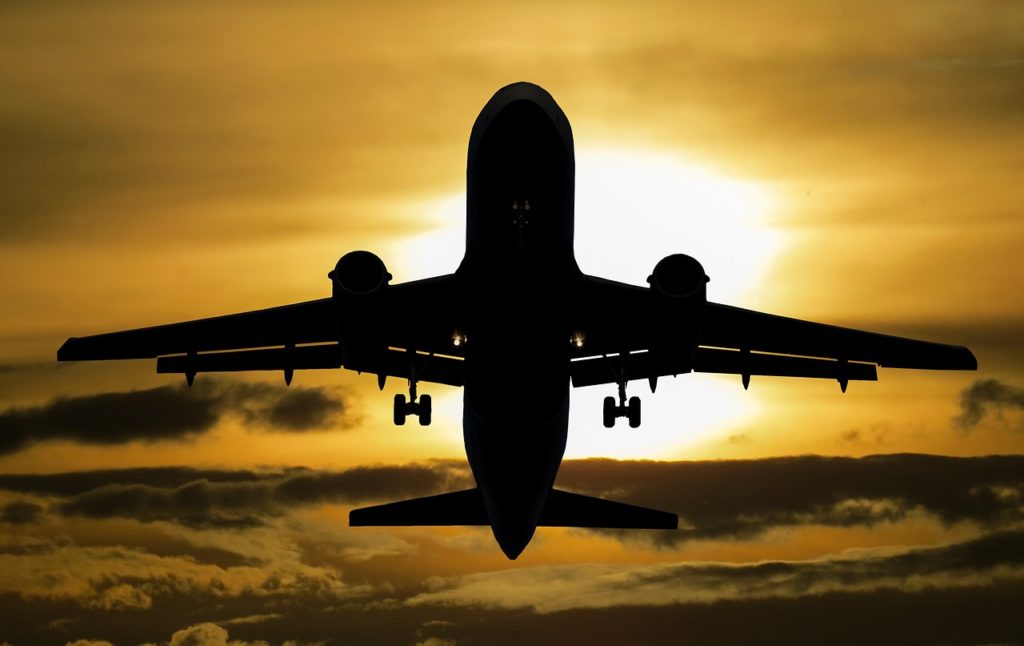
Our industry has always been known for innovation and delivering technological breakthroughs. Even during the pandemic, teams are finding new ways to work together – across departments and across borders.
It’s really an amazing thing to see.
Despite increased remote work among our teams, we continue to see great strides in urban air mobility, electric propulsion, supersonic flight, next-generation fighters and commercial space exploration just to name a few of the more promising areas.
The pandemic has changed the way we approach our jobs. Companies that have made early strides in the digital transformation find themselves ahead of the curve today – in both engineering and manufacturing. And if there’s one area that’s come to the forefront, it’s being smarter about manufacturing, or intelligent manufacturing.
In my final podcast of the Talking Aerospace Today “Productivity” series, I discuss what is meant by intelligent manufacturing. Yes, it’s about the digital factory of the future, but it’s also about accelerating production ramp-up and adding flexible automation up and down the product lifecycle. I touch on all of these points in the podcast link below.
Challenges facing the aerospace industry today
The manufacturing process has always been at the receiving end of a very long process, everything flows down to final production. In many respects, manufacturing has been an area that’s slow to change because companies can ill-afford the smallest of disruptions. Many OEMs still take traditional approaches to manufacturing. But trends today are forcing OEMs to make notable changes or modifications to the manufacturing process.
What are these trends? The ones I see impacting the industry include:
- Customers in both commercial and government sectors demand getting to market faster at less cost. They also want higher performing, more reliable and safer products.
- To meet customer demands for increased performance aerospace and defense products are becoming increasingly complex and more highly integrated.
- The desire for greener solutions and increased reliability and maintainability are driving the need for increased electrification.
- Increasing globalization is driving changes to how companies collaborate both internally and externally.
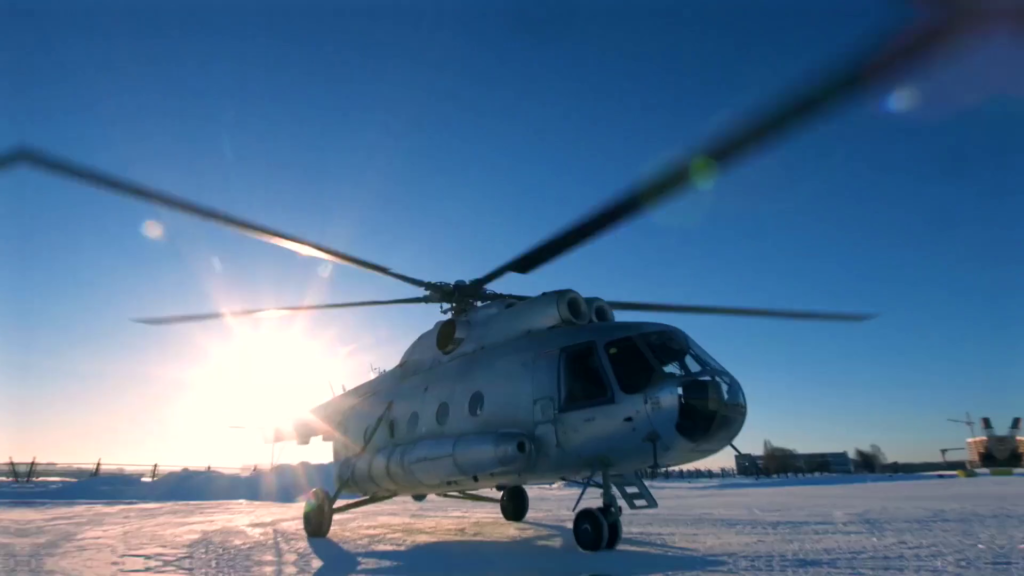
Many of these challenges should not surprise you. One of the more common questions I hear, especially when faced with the major challenges confronting the industry is how do I as a company incorporate automation or a more digitalized process into my manufacturing production line while managing my investment? That’s a very real concern. And then, with so much complexity out there, how does a company verify that with numerous customizations made to a product throughout its developmental lifecycle that the “as-built” matches the “as-designed” specs as it rolls off the production line?
Hand labor or automation?
I don’t think anyone would be surprised to hear that hand labor is still used to build airplanes today. Many A&D companies use traditional manufacturing concepts. Unfortunately, the state of the art hasn’t changed much for many of these companies. They still rely on assembly labor to build products. For these companies, much of the tooling becomes associated with the manufacturing process itself. A huge percentage of the workforce is associated with tooling and assembly, and then there’s the cost of training and making sure everyone is safe on the assembly line.
And let’s not fool ourselves. Yes, the cost of automation among many companies, has been deemed cost-prohibitive. There’s always a trade-off between automation and labor hours. A great way to illustrate this is to look at the automotive industry. An automotive OEM might produce 300 to 400,000 cars a year and so, they can implement automation – and justify the costs. But an airplane manufacturer might say “Well, I’m going to produce 60 aircraft a year, why would I want to invest all that money in automation?” I won’t deny it, getting aerospace companies to adopt automation in manufacturing has been a challenge. I will say, however, that forward-thinking companies and start-ups see the many advantages of automation.
Introducing “flexible automation”
No question you need to introduce automation in a smart and cost-conscience manner. It’s what I call flexible automation. Oftentimes a customer is replacing tooling with automation or robots, but because of the production rates, they’re not going to have a robot sit and do the same thing over and over. Flexible automation means you have that robot do four or five different tasks. Also, there’s additive manufacturing (AM) which is changing how everyone is looking at building parts. AM also provides product benefits as it reduces weight and material usage through generative engineering that uses advanced design technologies such as topology optimization and lattice structures. In fact, I believe in ten years, you’ll see AM come online in all kinds of imaginative ways. And then, finally, how do you present the information to technicians so that you have advanced work instructions appear on any device? You move away from paper, maybe you move into augmented reality.
Yes, augmented reality (AR) and virtual reality (VR) are another way to introduce flexible automation into the product ramp-up process. VR and AR technologies strengthen the link between the virtual design world and the factory floor. Of course, AR/VR is very much part of the digital factory of the future.
Here are just two examples:
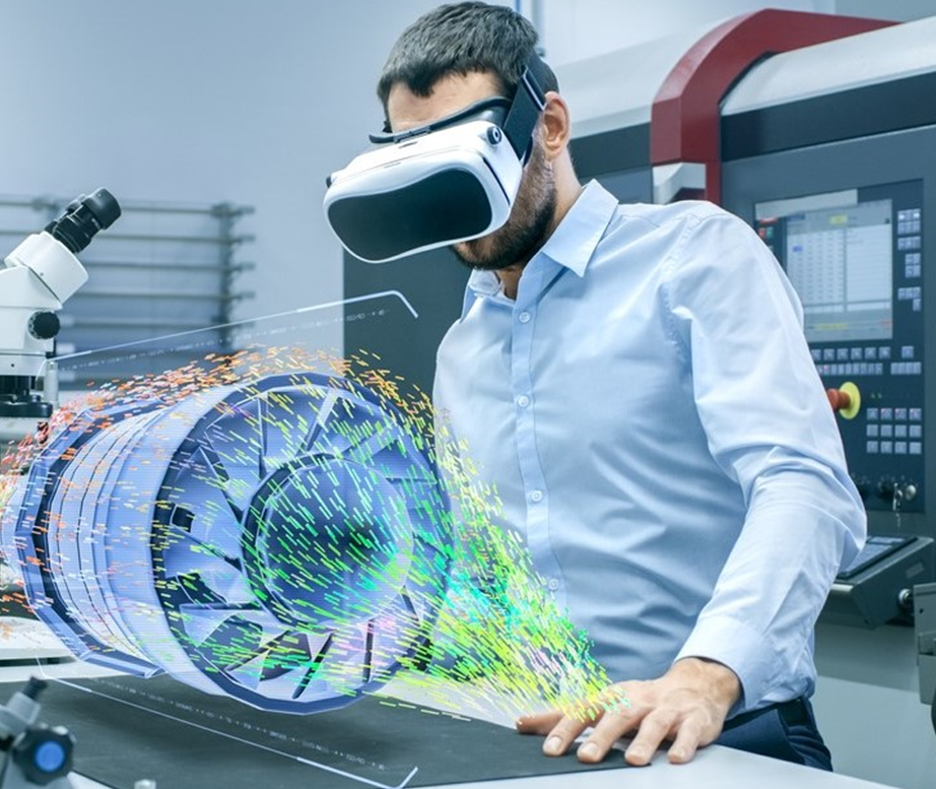
- AR on the factory floor: With cameras to help locate parts, design teams are able to replace 2D work instructions with 3D augmented reality. Teams locate parts using the rich features already available in the 3D models. As the technician prepares to install the parts, a technician must verify that the correct part has been selected. It is then automatically recorded by the system when the bar code is scanned.
- AR tailored to work instructions: Not only can AR be used on the factory floor, but it can also be implemented in smart wearables to further free up technicians from having to manage paper documents and devices. In the future, electronic work instructions (EWI) can be tailored to any number of criteria such as complexity level of the installation, how often the task is performed, or whether the part has changed since the last time it was installed. EWI sends out automatic verification notices when the part was installed and whether the work was successfully completed.
A couple of good examples of intelligent manufacturing. To summarize, it’s looking at the manufacturing environment, the tools, the parts and processes in place. It’s looking at the people on the factory floor, how to empower them to interact with each other and within the digital environment.
“It’s looking at the people on the factory floor, how to empower them to interact with each other and within the digital environment.”
Connecting the engineering world
to the manufacturing world
The Siemens Xcelerator portfolio seamlessly connects engineering and manufacturing domains. The key here is the Siemens comprehensive digital twin, which enables our customers to achieve true concurrent engineering. Customers are able to shift processes to the left, allowing users to evaluate their manufacturing processes at the same time they’re designing products. This brings that voice of manufacturing further to the left in the design processes. How is this possible? Teams can simulate not only the manufacturing processes, but also tooling and planning through virtual commissioning which reduces the risk of issues as the production facility is stood up – which ultimately reduces the risk of increased cost and schedule delays.
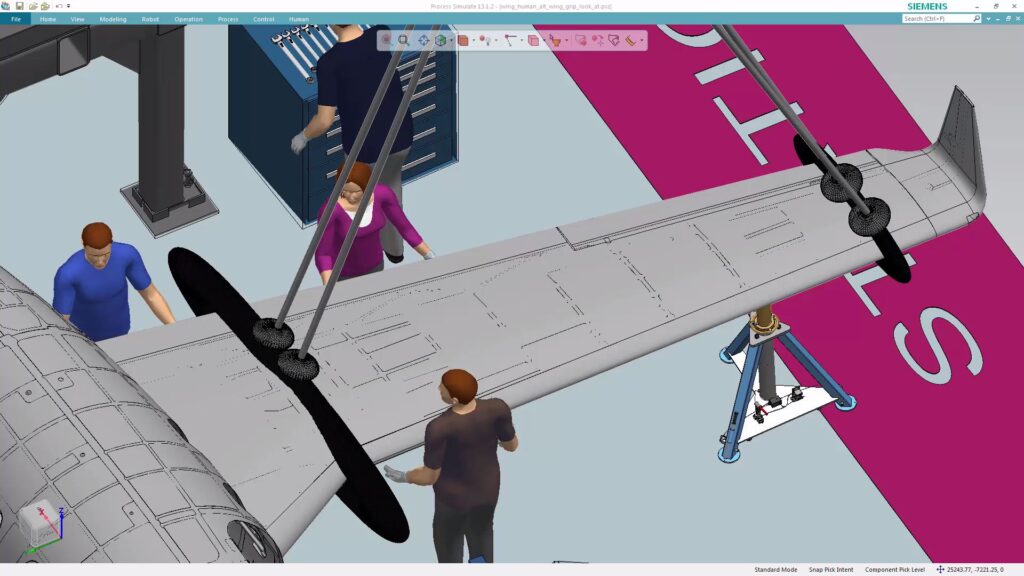
I cannot emphasize enough the importance of virtual commissioning within intelligent manufacturing. It can have huge implications when planning a new production line or facility. Virtual commissioning is leveraged to simulate manufacturing processes in a virtual factory setting to estimate the impact and cost of a design change or general setback – and reduce the propensity of risk during production.
When you think about how much investment companies make in tools, automation and facilities, teams must utilize virtual commissioning and identify issues early in the process to easily design out any problems. And then when a company finally starts up the production line there are no last-minute surprises. Risk due to change orders is all but eliminated. Xcelerator provides companies with a flexible work environment, along with the complete offering of our full lifecycle management toolsets. It allows users to incorporate new materials and technologies faster because it’s easy to connect to this open environment.
And then with IoT, and the tools now available within Xcelerator and the comprehensive digital twin, customers are able to leverage more data to close the loop on the production processes and provide insights into both how a product is designed and manufactured. Teams are able to utilize a multi-disciplinary process that involves both electronics and mechanical components to allow them to fully integrate complex and integrated products into the product line, saving time, reducing cost and limiting schedule delays.
We bring a lot of tools together to help companies make the digital transition onto the factory floor.
The digital twin and digital thread for intelligent manufacturing
I should point out, having the digital twin is really about the ability to rapidly evaluate different concepts, how to build a part and how to understand the many trade-offs. This is a key element of intelligent manufacturing. The ability to quickly look at different concepts through simulation means you’re not building physical mockups, you’re doing it in the digital twin. This can transform how you look at your manufacturing processes, and it can help you go faster in starting up your production line. Siemens offers a closed-loop manufacturing process, so you’re connecting your PLM system to your Manufacturing Execution System (MES). You’re managing this very complex aerospace and defense product with this full digital thread that connects from your engineering all the way into all of your production processes. The production digital twin and digital thread cover the full lifecycle of engineering to manufacturing, improving rate ramp-up and overall quality within a closed-loop manufacturing system. Such as system also greatly improves first-pass yield and scrap rate.
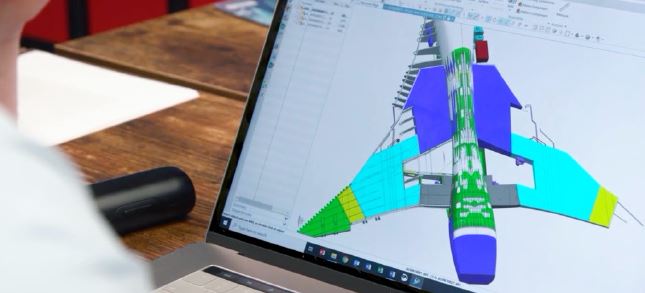
Now that’s what I’m talking about when I say Intelligent Manufacturing!
In summary
As companies seek to optimize their production processes to improve quality and reduce cost, production environments require the ability to share data insights from current processes and turn this into actionable information with a digital twin. Companies are looking for a better way to manage capital-intensive manufacturing resources and processes, accelerate their production ramp-up, and seek to incorporate new manufacturing technologies or concepts faster.
The intelligent manufacturing digital thread discussed in this blog orchestrates production processes and brings relevant production data to every aspect of program development. It proves concept viability of products by including manufacturing feasibility analyses through simulation early in the design process using the production digital twin. It validates production readiness with detailed manufacturing planning and virtual commissioning and incorporates design changes quickly to the factory floor to reduce re-work.
We talk about the factory of the future, but a lot of it is here today. It’s the foundation for where we’re going. Siemens wants to be your partner in helping your programs be on time, to execute within budget, and most importantly, accelerate production ramp-up while improving product quality. The entire Siemens portfolio helps users capture and reuse their manufacturing best practices and knowledge and be more effective as the company moves forward.
If you’d like to learn how to turn intelligent manufacturing into your competitive advantage, I urge you to attend this on-demand webinar. There’s a second webinar you can check out that focuses on how to implement a digital transformation strategy in the A&D industry.
Don’t forget to read our Intelligent Manufacturing industry white paper.
And finally, for information on all our industry solutions, please visit our Aerospace & Defense website.
Dale Tutt is the Vice President of Aerospace and Defense Industry for Siemens Digital Industries Software. He is responsible for defining the overall Aerospace and Defense industry strategy for Siemens Digital Industries Software, driving specific industry requirements into solutions for Aerospace and Defense customers. Dale has over 30 years of experience in engineering design, development and program leadership within the Aerospace industry.