Advanced machine engineering – multi-disciplinary design (podcast transcript – part 2)
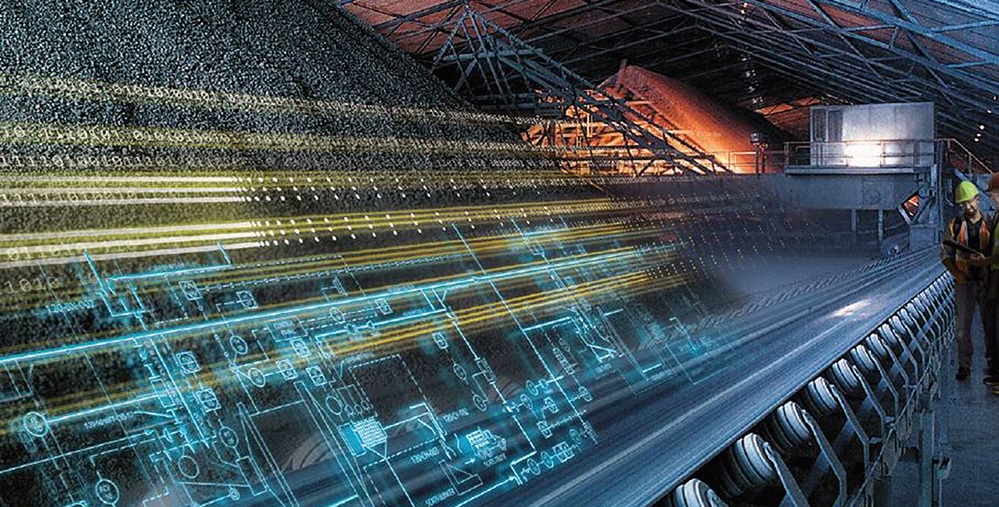
Industrial machinery in manufacturing is observing widespread technological advancements. It is an intimidating mission to design, validate and manage modern-day manufacturing and assembly operations to achieve first-class quality while optimizing cost. In our current blog series on advanced machine engineering, we are learning how machine manufacturers are leveraging multi-disciplinary design to make their manufacturing more efficient.
In this blog, we are providing a transcribed excerpt of the second podcast of this series, covering multi-disciplinary collaboration for machine builders and examine more thoroughly the machine design process and the benefits of implementing this approach.
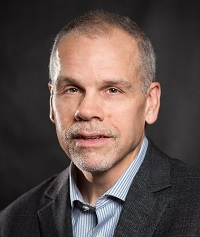
I am interviewing one of our resident experts, Bill Davis, who is the Director of Industrial Machinery and Heavy Equipment Solutions at Siemens Digital Industries Software. Bill’s expertise in this industry expands over 30 years, with 20 years as an engineer.
Below, is the transcribed excerpt from the second part of this podcast series. You can also listen to this second podcast.
Bill Butcher: Welcome to Siemens Digital Industries Software podcast series on advanced machine engineering, brought to you by the Siemens Digital Thought Leadership team.
In our last podcast, we talked about the evolution of technology within the machinery industry and the key trends that continue to shape the industry today. We also introduced the advanced machine engineering solutions at a high level, where you brought up three key differentiators. Let me see if I can capture that correctly: multi-disciplinary design, virtual machine simulation and commissioning, multi-disciplinary BOM and configuration management. Did I have that right?
Bill Davis: Yes.
Bill Butcher: So, in this session, I’d like to focus the conversation on one of these differentiators – multi-disciplinary design. Can I ask, for our listeners, what exactly is multi-disciplinary design?
Bill Davis: Yeah, thanks, Bill! And thank you for welcoming me back to the podcast. I appreciate the opportunity to speak again. When we talk about multi-disciplinary design, I think it’s essential to do a little bit of retrospective on what’s involved in building a machine, what’s involved in doing the engineering design and manufacturing of the machine, and how that multi-disciplinary design fits into it. In most companies, historically, it’s been focused around mechanical CAD, so the parts that need to be manufactured within tolerance and how things had to function together was primarily a mechanical arrangement and mechanical assembly. To a considerable degree, a machine is a mechanical machine, right? It’s a mechanical piece of equipment, like an auto or an airplane.
The difference is that over the last 20 to 25 years, we’ve always had electrical power to run motors and rotatory equipment to move camshaft gears and all of that. But what’s changed is that, now, all those motors are driven by software and PLC codes. So, whereas in previous days, you could keep the mechanical design in one space, electrical design, the schematics and all of that in another space. Then, the software guys were kind of left out in the cold to do their design work, once everybody else was done with what they were supposed to do.
When we talk about multi-disciplinary design, we’re speaking about a blending of those capabilities and skill sets in a more collaborative environment and how that pays dividends for the output quality of the machine that we design –everything seems to have its place. It’s more of an art form than bolted on electrical, sensors and cable runs and everything else. It’s an integrated solution. So, there’s harmony in the multi-disciplinary design that didn’t exist when they were silos.
Bill Butcher: Okay, so that seems straightforward to me in theory, but some may say, “I’m a small supplier” or “I have a process that right now is working just fine for me.” How would you respond to someone who might minimize the value that you just described for multi-disciplinary collaboration?
Bill Davis: Yeah, that’s a good point. Most of the machinery manufacturers are what I would call more midsize companies and, in many cases, have the same people doing the electrical work and the software. So, they already understand this multi-discipline approach. One item of importance is the capabilities of PLC and automation code, which have accelerated in the last several years, driven by what I call “performance-based programs.” The software is adaptable to conditions on the floor and on the machine – the sensor reading and reacting – the game is changing. Even something as simple as a cylinder extending and retracting, we’re seeing people use pressure differential and flow regulation and other technologies that were not available to small and medium-sized businesses a few years ago due to cost. So, we’re witnessing more mechanical and capability features being replaced by software. It’s a game-changer for every machine designer.
I guess there are some other things that on a small scale or a smaller business they have to be considerate of – for them to take the approach that “we used to build it, we used to design it, build it and then see if it actually worked by testing it.” Today’s machinery companies don’t have the time to do that because their time to market is much more compressed. Again, machine complexity is more significant. So, they need to change their approach to engineering and adopting things like generative capabilities and its requirements: what forces, what gets a hold – so they can perform the simulation up front. Not that they must do everything up front, but realistically, from a design exploration, it’s much easier to do the entire digital machine if you can show how it performs in the virtual world. Therefore, items like Mechatronics Concept Designer, which is a digital industry software with specific capabilities around kinematics that can be used to define PLC code, using those capabilities to show what a virtual twin looks like and lets companies fail fast. It allows them to do all that kind of work in the beginning. Realistically, it’s not more work, it’s the same work that’s already being done by the team, but now they’re doing it together in a synchronized manner.
Bill Butcher: Right.
Bill Davis: You need to be conscious of having the right level of electrical engineering integration, for knowing where software belongs in the process. There’s much concern in going from silos and throwing the design over the wall to allowing the electrical personnel to work on it after the mechanical people. Also, there’s a danger in having too much integration too soon. An example of this is when smaller companies get a bit hung up on trying to adopt multi-disciplinary engineering. If you think about a piece of machinery in assembly that articulates back and forth 90 degrees, and it has pneumatics – with cables, sensors, hoses and tubing that’s necessary – building those detailed pieces out for that kind of functionality early in the design. You end up finding there’s more rework because the design in these early stages is very iterative.
So, trying to take advantage of collaboration means that you get to a certain level of maturity with parts of the mechanical system opening up that expose it to the electrical and software teams and you’re performing the kinematics up front with 90-degree motion, for example, already knowing the limits of what you want that mechanism to do. Therefore, if you can build that into the mechanical behavior, you can start to realize the simulation. The software guys know what behavior you’re expecting out of the mechanical and what that they need to put into that software. It’s about performing work upfront, on the mechanical side and exposing it to the teams in the right way, without trying to do everything together at once – which never works out. If you’ve ever tried to build a deck at home and tried to dig the fence post while you’re building the deck, that doesn’t work, so you need to do things in a certain process. Companies need to migrate toward a more collaborative approach. You can’t just throw out your old processes and start new without having some level of migration. We have learned several times over, in my own experience with companies in machinery and automation for packaging machines and converting equipment. When adopting new technologies, you couldn’t consume it all once – culturally, the business can’t handle it.
Bill Butcher: Alright. That’s a good example, and one of the things you highlighted there, which I think is important is why disciplines need to interact with each other during this process. So, that was a little bit about people who think that they might be okay as they are, and you addressed why they shouldn’t be. But let’s twist it a bit. What about the benefits for those that are incorporating a multi-disciplinary collaboration into the manufacturing process? What should they expect those benefits to be?
Bill Davis: Companies that have already experienced the challenging process to a more collaborative approach and are seeing the benefits of time that they can compress out of the development schedule to the simulation piece – which is a crucial part of what’s called, “virtual commissioning” – software code validation. So, its system language-speak for being able to test out everything that should happen on the machine in the software code and having it displayed in the digital world, so the CAD from an emulation perspective. However, being able to show that the code that you’re writing is doing what you thought it was supposed to do when you envisioned the mechanical part, when coming down to the human-machine interface part, and pushing the button to start the machine – does it actually start the machine or does it do something else? When I say, “stop”, does it stop it or, again, does it keep going and ignore the command?
So, you can get to this level of simulation with software code that is necessary because this is where the complexity comes in. We used to have hundreds of sensors in machines, and now we have thousands or tens of thousands of sensors in machines, and it’s very easy when writing code to either not identify those sensors upfront and push that behavior expectation downstream if we’re trying to write that code from scratch, or to take the code from somebody else’s machine, or the last machine that we built. Therefore, being able to compress the delivery time in terms of the code writing simulation is where the dividends get paid, when the machine is sitting on the floor, waiting for the customer to accept it and the software guy is cooking away at his keyboard – that’s not a very pleasant feeling for an operations manager. Those were my most sleepless nights when I walked out onto the assembly floor and I saw the director of software building his code, when I was expecting that code to be already written.
So, having this in a managed environment with an entire modular product development strategy, companies realize they can beat their competitors to market by having the simulation upfront and linking the software to the modules. This scenario is a significant groundbreaking achievement for companies to be competitive in this space.
Bill Butcher: I liked the way you just said, “strategy”. I mean, strategy implies specific actions to get to a desired result. Do you have any examples for any companies that have embraced advanced machine engineering as a strategy, and if so, what kind of results they might have seen?
Bill Davis: We have a customer that I’d like to highlight, that has a lot of experience with us, and they’re not in the traditional kind of machinery world, as they don’t build machines for machines. They build machines for the medical business. So, they manufacture and fill ampoules or small vials. When it is cold and flu season, if you had your flu shot, you probably had it dispensed from one of these little glass containers. It’s a company by the name of Bausch & Strobel, who manufactures machines that perform filling, sealing, and so, and there’s a more substantial requirement on the regulatory environment. They embraced advanced machine engineering, from the standpoint of doing the mechanical design and by embracing a virtual twin and doing both the commissioning and visualization with their customers. They bring customers into a virtual reality wall and see them interact with the machine in its digital form. From a financial perspective, it pays huge dividends for them. Also, it brings together the engineering upfront in the design, and the collaboration of various disciplines in testing the machine code, they compressed their delivery schedule by over 25 percent.
Bill Butcher: That’s an excellent example, It is an intimidating mission to design, validate and manage contemporary manufacturing and assembly operations to achieve first-class quality while optimizing cost. In our current blog series on advanced machine engineering, we are learning how machine manufacturers are leveraging multi-disciplinary design to make their manufacturing more efficient.
Listen to podcast01, podcast02, podcast03 and podcast04 from this series via our Thought Leadership blogs.
Also, you can access the entire podcast series via Apple, Stitcher, Spotify, Castbox, TuneIn or Google.
To improve the speed and efficiency of your machine design process, watch our Advanced Machine Engineering – Start your digital transformation journey today webinar.
About our expert:
Bill Davis is the
acting Industrial Machinery and Heavy Equipment Industry leader for Siemens
Digital Industries Software. His experience and insights have been acquired
from a career spanning 30 years in engineering and operations management with
machinery and heavy equipment companies. Bill holds a master’s degree in
Business Administration from Marquette University, with a concentration in
Operations Management and Strategic Marketing,
as well as a Bachelor of Science degree in Mechanical Engineering from
Milwaukee School of
Engineering.
This blog is an excerpt from the advanced machine engineering podcast transcript, displaying the second in a series of four podcasts.