Process Simulate Robot Safety in Production Systems [VIDEO]
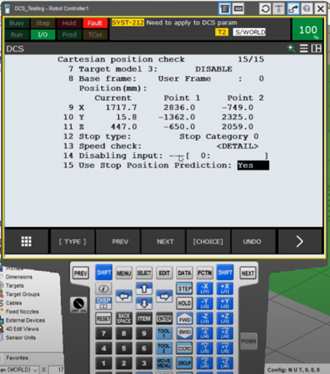
Delve into the capabilities of Tecnomatix Process Simulate software, specifically Safety Robot Manager (SRM), and how it ensures comprehensive safety and efficient robotic design while validating concepts, visualizing secure spaces, and optimizing processes.
As manufacturing and logistics industries continue to embrace industrial robot systems, annual robot shipments are predicted to double by 2030, from about 500,000 in 2022 to nearly 1 million in 2030. While this trend helps to enhance productivity and quality and addresses labor shortages, it poses significant challenges in terms of ensuring operational safety.
With more robots in densely populated automated lines, planning and validating their functional safety becomes increasingly complex, and the risk of human injury and equipment damage increases. Therefore, whenever a new robot station or line is planned or changes are needed to introduce new products or alter the layout, ensuring robot safety is a crucial factor to consider. Explore the nuances in robot safety in production systems, discussing challenges and strategies for mitigating risks with Process Simulate Safety Robot Manager.
Meet the authors
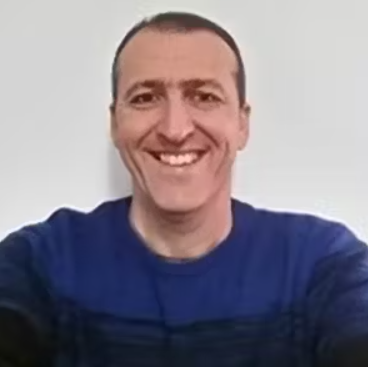
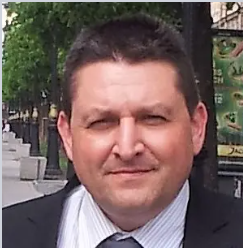
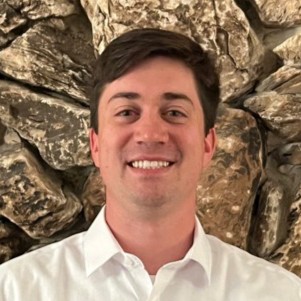
Controller safety – the concept
Classic safety guards such as fences or cages provide hardware protection to the people and equipment behind it, but it does not prevent the robot from accidental crashes. In addition, limiting the joints travel is not able to “protect” zones in the robot cell space. To resolve this, the leading robot vendors developed controller capabilities allowing an individual robot to restrict its entrance and exit from predefined virtual safety zones.
To explain how it works, let’s look at the image below which shows the blue shape encapsulating the gripper. This shape is moving with the robot arm and the yellow box encapsulates the table and fixture mounted on it. This box is stationary and a rule is then set forbidding the blue shape from entering the yellow zone or enforcing it to stay inside. Also, the reaction to breaching condition is set, such as activating an emergency stop.
With these rules set, before performing the next move, the controller checks for breach of the rules. If a breach is found, depending on the safety requirements, the robot would stop with an alarm or slow down the motion speed, preventing a collision from happening.
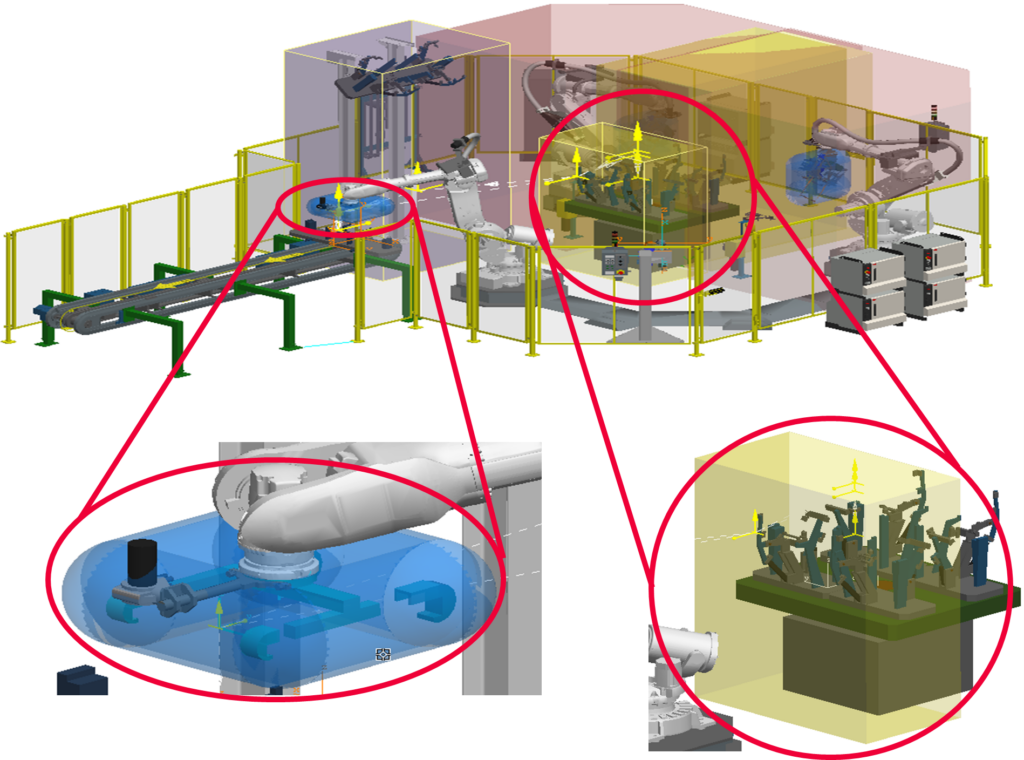
There is another layer of safety based features on sensors placed in the robotic cell communicating safety breach to the PLC, which then have a logic set to send signal, such as emergency stop.
Controller safety interaction
Basic safety adjustments (touch-ups) can be done on the shopfloor using the robot teach pendant. However relying solely on this approach can be very costly, laborious, error-prone, and time-intensive.
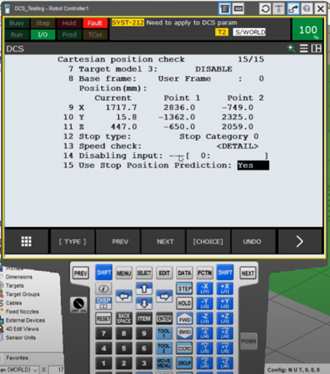
In modern robotic systems, the safety aspects are defined in the beginning of the planning process and after the layout is planned. This planning must be aligned with the robotic production operations during its entire development process to achieve optimal robotic movement, otherwise there can be significant challenges with system complexity. Modern robotic systems require a comprehensive solution that incorporates a 3D graphical tool. Several robot vendors use their software for their specific robots, but the optimal solution is to use one that integrates 3D representations of the entire robotic cell combined with simulation, offline programming, and virtual commissioning capabilities.
This entails not only the robot and its associated equipment but also various brands of robots coexisting in the same cell, auxiliary equipment i.e. conveyors, turning tables, clamps, as well as manipulated parts.
Process Simulate with Safety Robot Manager tool provides a comprehensive solution that supports all capabilities, ensuring an end-to-end safety and robotic operations design. Leveraging these capabilities during planning and process development helps validate the safety concepts, visualize safe spaces as well as safety-wrapped robots and analyze them against safety standards and rules, resulting in an optimized process and high-quality safety environment.

The validation of safety settings in the physical realm often involves manually jogging the robot to diverse poses within the robotic cell to observe when safety breach signals activate. However, this method is labor-intensive, time-consuming, and limited in scope. Process Simulate SRM (Safety Robot Manager) offers safety feature validation in the context of the complete simulation environment, which allows users to assess if the safety features correctly reflect the equipment or zone. This feature within Safety Robot Manager helps to protect and manipulate visibility to eliminate obstructions, make measurements between safety features and other objects in the station, such as distance from the fence.
One of the most important capabilities in Safety Manager is reading and writing safety data in the specific robot language, as well as in a standard safety technology description format. A cohesive language enables users to seamlessly exchange safety design data between Process Simulate and the robot controller to support the process of safety approval, including:
- Overlay classes in the real robot station
- Robot controller
- Process flow analysis
- Emergency stop behavior
- Hardware axis fixes
As a best practice, users should define safety features and rules in the early stage before starting the path planning. In case of a newly designed robotic cell (“green field”) the user can start the safety design from scratch. In case of pre-established safety settings (“brown field”), Process Simulate can import data from the controller, and adjust it as needed for the new process.
Dynamic safety validation along the robot path
A critical challenge in robotic safety design lies in addressing breaches that occur along the robot’s programmed path. Without prior safety validation in a 3D simulation environment, emergency stops can occur without gaining clear insights into the source of the problem. Process Simulate resolves this scenario by providing the capability with its SRM (Safety Robot Manager) tool to adjust the visibility of safety features during path planning and simulation. For example, breaching objects are visually highlighted, offering immediate insight into the problem. If the breach triggers an emergency stop or controlled halt, the robot’s operation halts as well. This empowers users to diagnose the breach, identify appropriate solutions, and implement modifications in the context of the breach itself early in the planning process and prevent the issue from occurring at the shop floor during physical commissioning.
Brand specific safety settings
Each robot controller brand has distinct capabilities, limitations, and terminologies related to safety settings. Process Simulate SRM bridges this gap by providing a unified, user-friendly graphical interface for accessing safety settings across various controllers.
Take a robot replacement as an example, whether it’s the same robot or a different vendor, the safety environment is kept agnostic and translated into the appropriate robot language. This seamless interface simplifies the transition between brands and enables comparative evaluations within the same simulation environment, ensuring consistent, standardized user practices regardless of the controller brand.
Change management
Changes are inevitable in production environments and managing alterations to safety settings is a complex task. Process Simulate offers a virtual platform for making modifications and evaluating the impact across the entire production lifecycles. It also provides tools that actively support the user in achieving optimal performance of the robotic process. This proves invaluable when changes arise from various sources, such as adjustments to equipment placement or manual path modifications. The ability to assess changes within a risk-free environment ensures that safety remains paramount throughout the evolution of the production system.
Automatic safety quality control and report
Once all parameters are set and the safety concept is properly designed, automatic routines are used to validate proper interaction between the process itself and the safety environment.
The resulting report notifies the user in case of violation of safety standards and provides guidance to solve the problem immediately. In addition, automatic routines provide optimization options for the process and safety environment for an enhanced process flow, while considering the operations of various equipment along the process time.
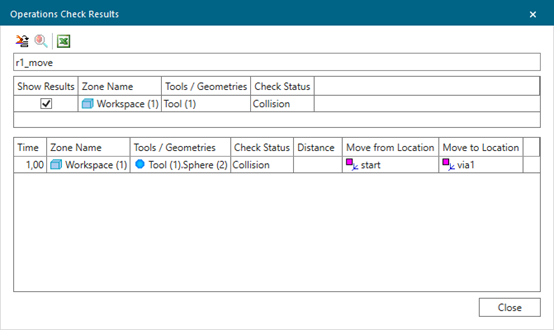
Unified platform for designing, validating and adapting safety settings
As robots continue to revolutionize the manufacturing landscape, ensuring their safety remains a paramount concern. The challenges posed by dynamic robotic motion, the need for efficient change management, and the diversity of controller brands requires innovative solutions.
Process Simulate SRM (Safety Robot Manager) is a comprehensive tool that addresses these dynamic challenges, offering a unified platform for designing, validating, and adapting safety settings. By incorporating these strategies into production systems, manufacturers can harness the full potential of robots while upholding the highest standards of safety.
Process Simulate seamlessly integrates all process requirements and safety standards, actively supports the user in the process development. It also, assists with an interactive background analysis including AI techniques, and is open to export, import, transfer and approve all aspects of robot safety management.