Why throw away all your hard work? Why not make a digital twin?
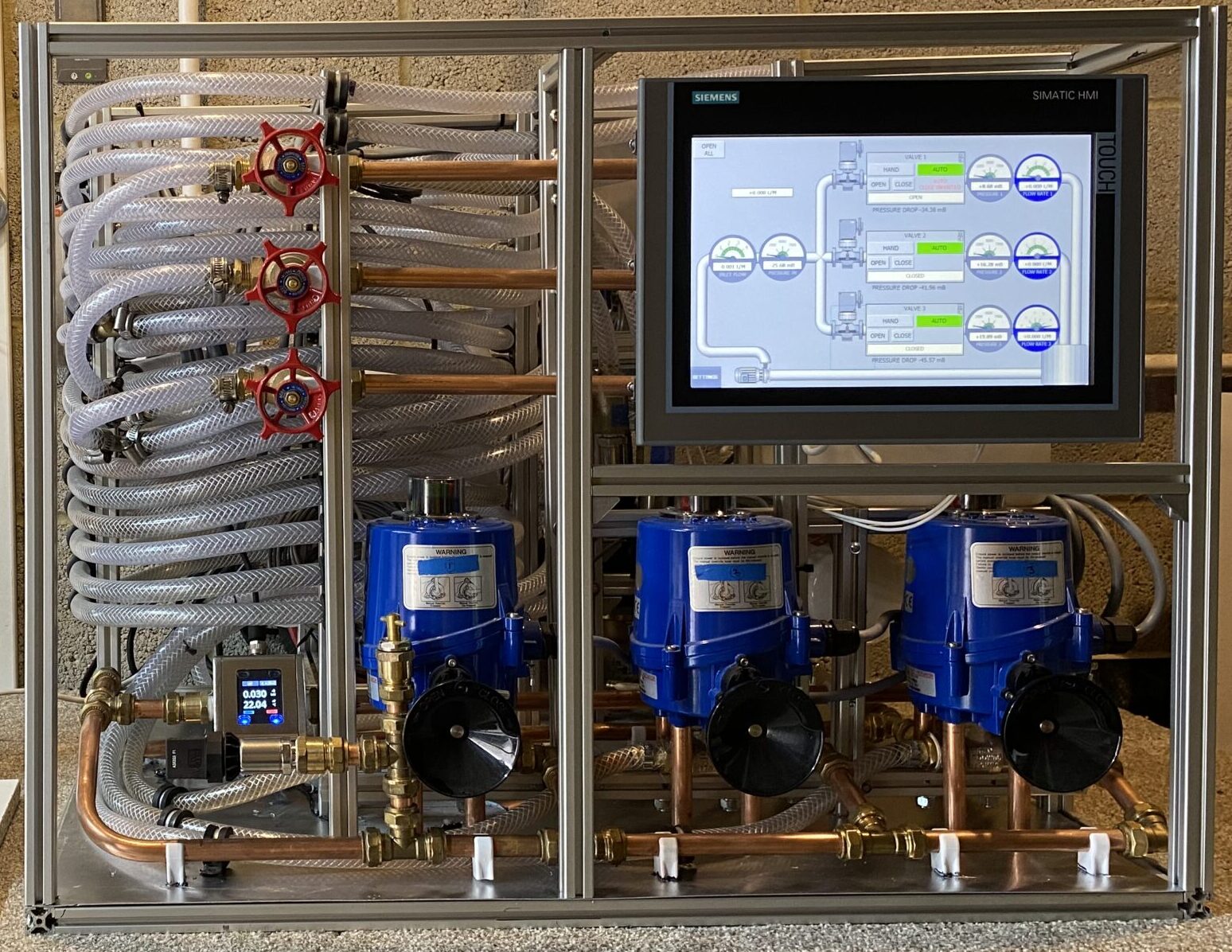
One thing that frustrates us most here at Siemens, is when you, the customer, design wonderfully detailed and nuanced systems only to throw them away when you are done validating a design. While this is a perfectly valid workflow, why stop using the model before you have extracted all the benefits of that hard work? Why not continue to use the models throughout the design and operational phases of the system?

In the past, this hasn’t been easy to do, but as we transition into industry 4.0 we need to provide you with the tools and capabilities to leverage your models long beyond the initial design phase. This has led us to develop a connector within Simcenter Flomaster that enables you to interface with hardware and create executable digital twins that can run alongside your plant that are based on your original models.
In doing so you can extend the use of simulation models into the operational phase by coupling them to a physical plant or thermo-fluid system. This means that a full-fidelity model of the thermo-fluid system can run in real-time as an executable digital twin (xDT).
The xDT is then used to compensate for gaps in instrumentation with smart virtual sensors. To detect leakages or other failures. To perform smart model-enabled predictive maintenance and to collect smart data to further enhance the design and the operation of the system.
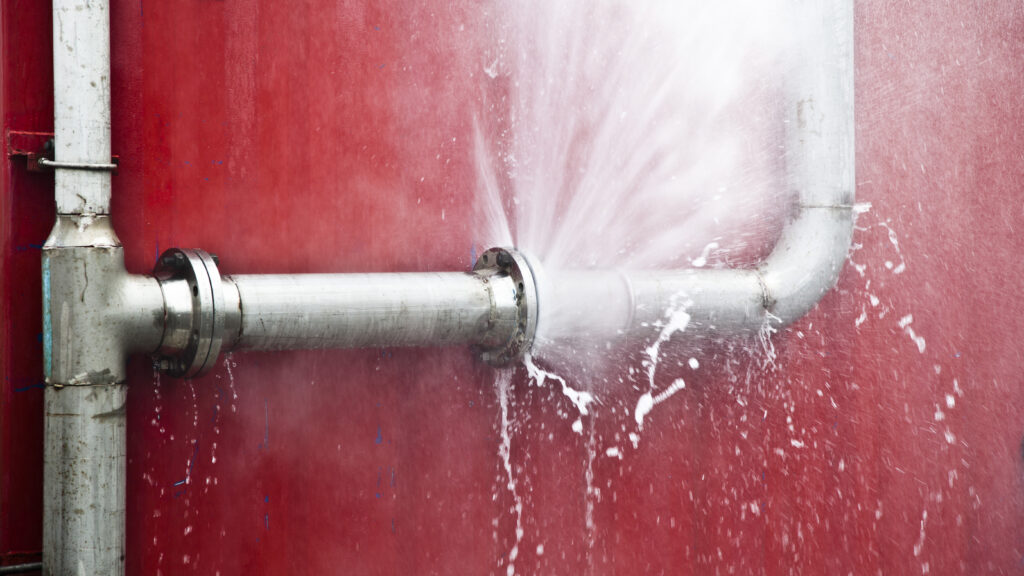
The connection between the executable digital twin and the physical system is based on the Open Platform Communications Unified Architecture (OPC UA) standard and is as simple as using dedicated OPC UA components that enable the simulation models to connect to the outside world directly from within the application. Additionally, a real-time controller ensures the model consistently runs in real-time and is in sync with the physical system.
It is all well and good to tell you about this capability and how great it is for your organization. But what if I could show you? We here at Simcenter don’t just want to create a capability, we want to extensively test it. With our simulation-based capabilities, this is achieved through validation exercises. But how do you test a connection to physical hardware?
Well, that is easy, you create a testing facility. Using this we intend to show you a handful of use cases for this capability over a series of blogs and communications. The first of which is designed to whet your appetite with an overview of this facility and what it can achieve when coupled to an xDT.
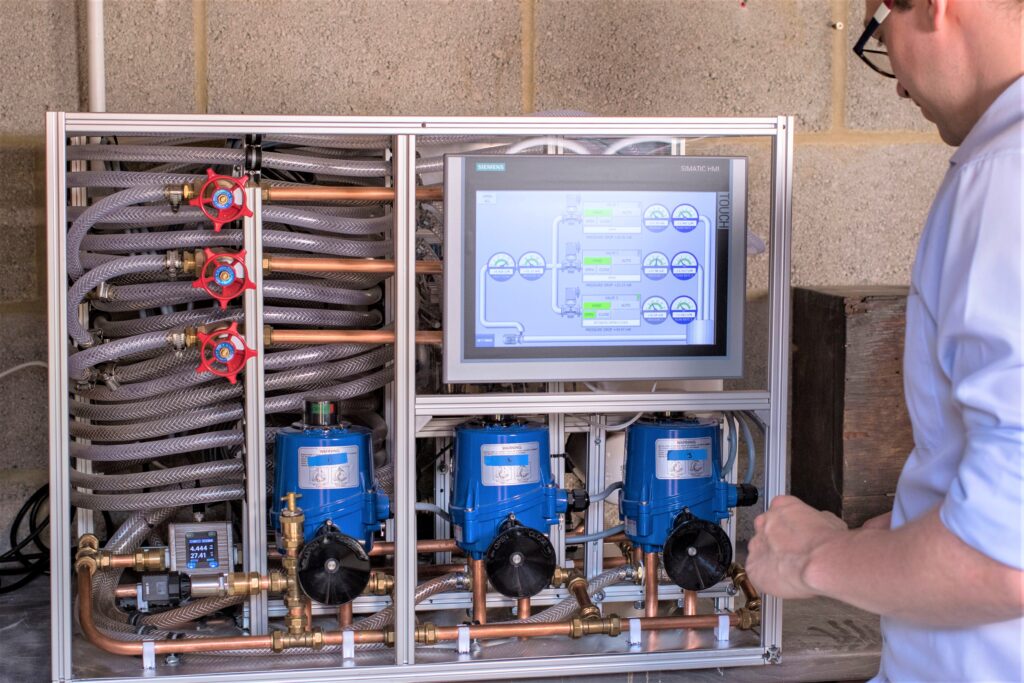
The testing facility is shown above. While it is certainly compact as it is portable, it can be used to validate several important operating scenarios. The first being virtual sensing.
This is the ability to not just rely on your physical sensors that are installed in the facility but to gain additional insight into your system through the simulation of the digital twin. This can be particularly important for several reasons. Firstly, how do you measure something without impacting the value?
Further to this what happens if your system is operating at extreme temperatures and pressures? How do you measure without melting the sensor or blowing it up?
This highlights the fact that hardware sensors are expensive and fragile along with being time-consuming to install and change.
The solution to all of this is to install some sensors but then leverage virtual sensing. We have done exactly that in our test rig as flow meters are notoriously expensive. Therefore, we have only installed one directly after our pumps, and then throughout the rest of the system, virtual flow meters are used in all of the winding and complex fluid paths.
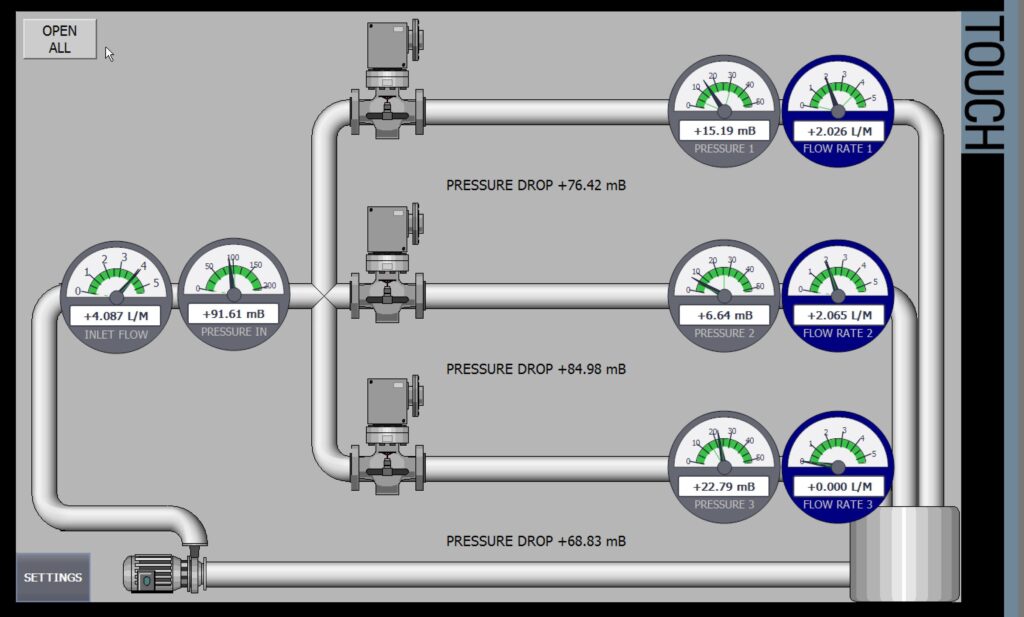
As can be seen on this Human Machine Interface (HMI) the fluid enters from the left before splitting into three distinct paths. These eventually combine and form a closed loop. Ordinarily, we wouldn’t know what the flows are in each of the lines. You could probably take a good guess that it is a third of the main flow for this example but if you had more lines with varying geometry how would you know?
Further to this what would happen if one of the valves failed to open or close? You would believe there is flow where there isn’t, which could lead to insufficient cooling and further failure would result. This type of failure is something we will look at in a future blog using this same test rig.
In order to gain additional insight into the operation of our facility we have introduced virtual sensors that run off the model inside Simcenter Flomaster. These have been coloured blue on the HMI for easy reference. We can see that there is a flow present in lines one and two, and to an operator there would be no discernable difference between a hardware or software sensor.
The system is able to respond and match the real plant through changes in the operating point. For example, starting and stopping pumps, opening and closing valves in the system, and through the leak lines that we have added to simulate a leak detection scenario. In doing so, the real time full fidelity model can handle any operating point that the hardware runs at. This is the main advantage of using a full fidelity model and not a reduced order model.
To show you this in more detail watch this short video.
I hope this has given you some insight into how you can leverage our xDT developments to extend the life of your models to design, commission and operate highly efficient and safe thermo-fluid systems, while at the same time lowering instrumentation costs and gaining additional insight into your plants.
Please check back soon as we look at how this functionality can be further used to understand failure scenarios and advanced warnings.