What’s new in automation?
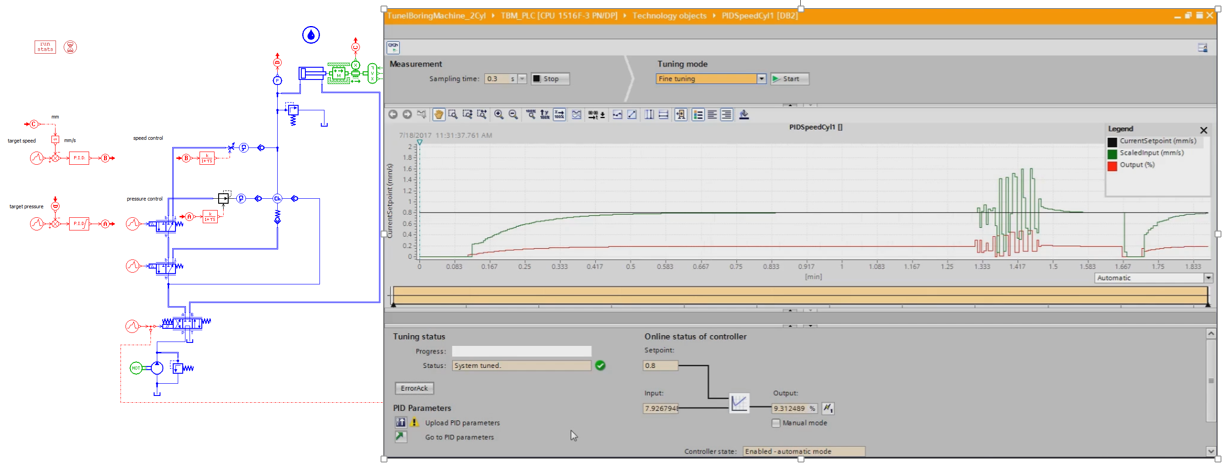
Today, mass consumption leads to new trends in terms of production. In order to meet production requirements (such as quality, safety, throughput and costs) processes must be automated. Process automation is a branch in the automation world that deals with continuous processes and therefore, with continuous process values like temperature, pressure or flow, compared to factory automation where the output is a discrete unit like a box or a car, for instance.
Nowadays, it is usual to find factory and process automation working together. Moreover, today’s industrial plants are complex engineering products that require a flawless integration of mechanical, electrical and automation systems. They have to work perfectly together in order to fulfill production and safety requirements. The classical engineering process starts with the mechanical design, followed by the electrical design and ends up with automation. With this sequential process, design errors and incompatibilities among components are first discovered when the plant has been built and the engineers are commissioning it on site. This can greatly increase engineering costs and, in the worst case, delay the completion of the project.
Saving time and money with simulation by predicting failure and process behavior
Digitalization enables you to create a digital twin of your machine at every step of its life cycle, from the design to the commissioning and operation. Simulation solutions from Siemens PLM Software enables users to model different kinds of production plants (various size, type and purpose). For instance, simulation enables mechanical and electrical engineers to test and validate components and systems during the design phase and furthermore it allows automation engineers to start programming the plant and debug the PLC code with the feedback from the virtual model. The unique combination of simulation solutions from Siemens PLM Software with the automation products from Siemens, enables specialists to perform what is called virtual commissioning of production plants.
Working together on a new solution for process and automation departments
Alvaro Canizares, part of plant engineering and simulation at Siemens, has tested an interface developed between Simcenter Amesim, automation systems and Simcenter Amesim Automation Connect, a new tool available in Simcenter Amesim.
“My goal was to model with Simcenter Amesim a real process plant that we have at our department and to use this model for virtual commissioning of the automation code. Furthermore, I used my simulation model to monitor the sensors of the real plant. To do this, the model of the plant was running on a computer at the same time as the real plant was in operation. After implementing some additional logic, the model was able to identify simple sensor failures from the real plant and replace these values with the equivalent simulated values. As a result, the plant was able to keep its function despite real sensor failures.”
From the development to a ready-to-use tool
Alvaro explains us how he proceeded to develop this tool available within Simcenter Amesim: “I used Simcenter Amesim to model mechanical and hydraulic components of the plant. The goal was to have a model running in Simcenter Amesim that could simulate the behavior of the real plant as closely as possible to let it run in parallel, and real time, to the real plant.
While simulating a real process plant, I connected simulation to the PLC. I was able to debug the automation code, improve control strategies and monitor real sensors. The work was a proof-of-concept for the use of Simcenter Amesim in the field of virtual commissioning and soft sensors.”
“Soft sensors, or virtual sensors, provide feedback of the real plant based on simulation. They do not exist physically, but they can provide information that real sensors cannot measure and they can also be used to monitor real sensors.”
Providing an off-the-shelf solution for virtual commissioning
Alvaro says that once a model is created with Simcenter Amesim, the Automation Connect tool represents an interface between Simcenter Amesim and other third-party tools. For virtual commissioning purposes users can perform software- (SiL) or hardware-in-the-loop (HiL) connecting Simcenter Amesim with an emulated (SiL) or real (HiL) PLC. The PLC sends control signals to the model and the model sends the feedback (sensor values) to the PLC. Therefore, not only can you use Simcenter Amesim to design, analyze and size your system but you can also use this model to perform virtual commissioning and deliver a software-based method to the automation department in order to program and test the PLC code.
“Virtual commissioning enables customers to use simulation models to test process sequence, as well as to debug and optimize the PLC code. For customers who are already using Siemens PLM simulation software for the design phase, it allows for deeper integration of digitalization tools at later engineering phases like commissioning. For new customers, it might represent a potential reason to opt for Siemens PLM solutions and combine them with Siemens automation products,” explains Alvaro.
Enjoyed this article?
Even watch that video: Physical systems optimization with PLCSIM Advanced and Amesim
Join us for that webinar with real application case: Simulation and virtual commissioning for mixing and filling
Find out more about Simcenter Amesim capabilities for automation in the attached document