Virtual acoustics and sound quality evaluation using CAE auralization
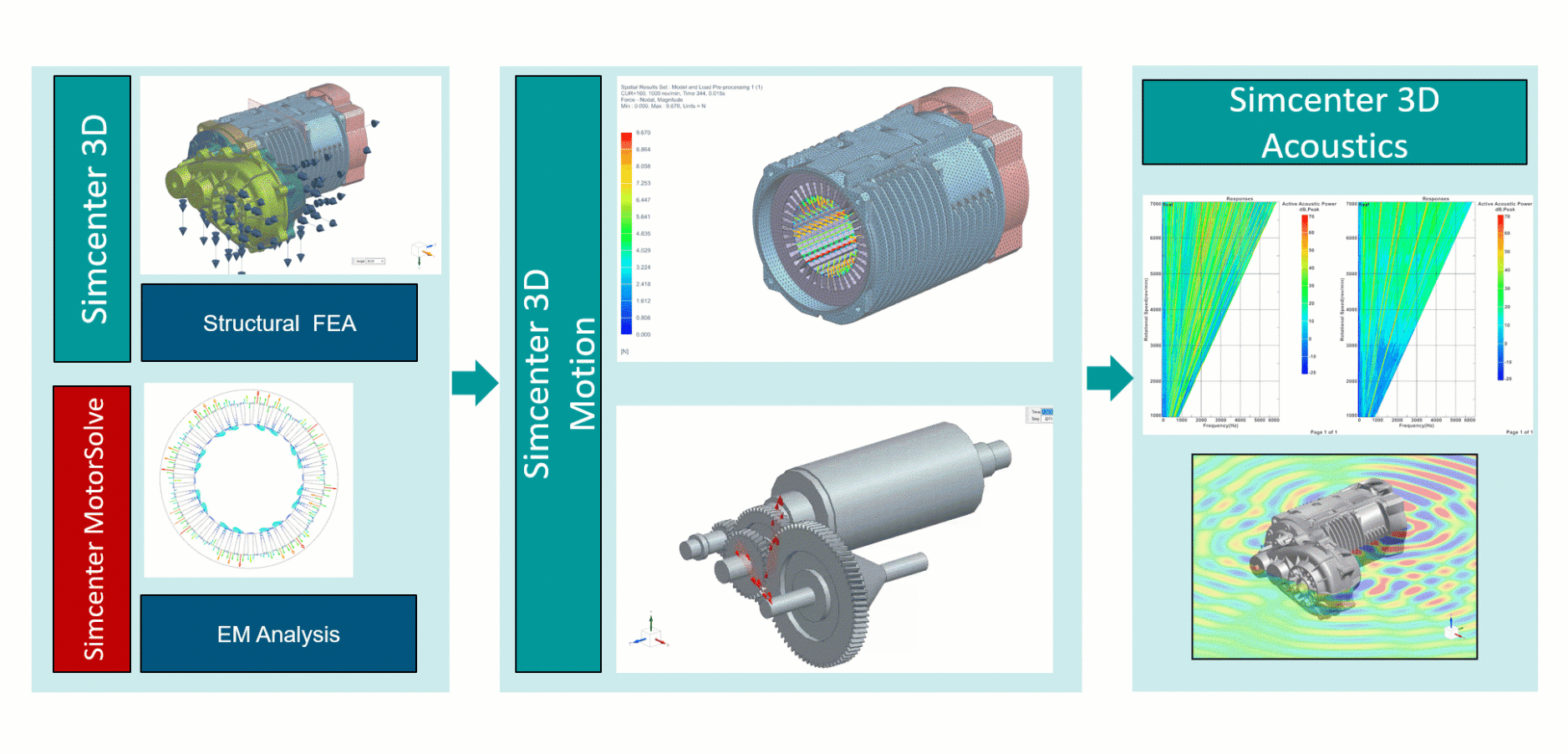
As virtual acoustics engineers and product designers, especially those that identify as the Computer Aided Engineering (CAE) kind, we like numbers. Quantifiable and objective data gives us a foundation to build great products that meet our customers’ expectations. Unfortunately, this is only part of the story for Noise, Vibration, and Harshness (NVH) engineers. Brand recognition and customer acceptance depend not only on Transfer Path Analysis (TPA) forces, panel and path contributions, order cut data, and waterfalls but how these quantities translate into the personal perception of the sound your product makes.
Think about the sound of the coffee maker with that first cup of coffee in the morning, and how the sensation of quality gives you confidence that it will make it exactly how you like it. Or when your car door shuts with a solid “thud,” giving the sense of security and safety, as opposed to a metallic “bang” you would expect from a car made in the 70s. Or even the bell in the bus or tram, how a lifetime of hearing the same sound gives you confidence that the driver will hear it and the bus will stop.
How do you make a simulation model “sound better”?
One day at the coffee corner…
For many NVH CAE engineers, the following situation may sound familiar. The simulations are running, and for Dave, it’s time for a well-earned coffee. Ahh bliss. Unfortunately, this moment of tranquillity is short-lived as powertrain integration program manager Sarah comes in and starts discussing the prototype tests they have been doing and the difficulties they are having finetuning the gearbox. She approaches Dave and asks:
– Dave the engineer
Troubleshooting this purely using tests will be nigh impossible especially given the very tight release timeline. So, it’s up to Dave to come up with some suggestions, to make it all “sound right” – whatever that may mean.
If it looks good, it sounds good, right?
Like in other application areas, efficient integrated NVH simulation workflows for electric powertrain analysis are readily available. Starting from electro-magnetic forces calculated in Simcenter Motorsolve and a structural Finite Element model, a Simcenter 3D Motion model that includes detailed gear and bearing models can very accurately predict the structural vibrations of the outer housing of the electric powertrain. With that information, Simcenter 3D Acoustics can easily predict the noise signature. The advanced post-processing capabilities give a thorough understanding of how this signature came to be, as seen in the different result plots below.
See how Simcenter Motorsolve and Simcenter 3D Motion can predict the structural vibrations of the electric powertrain outer housing in this blog
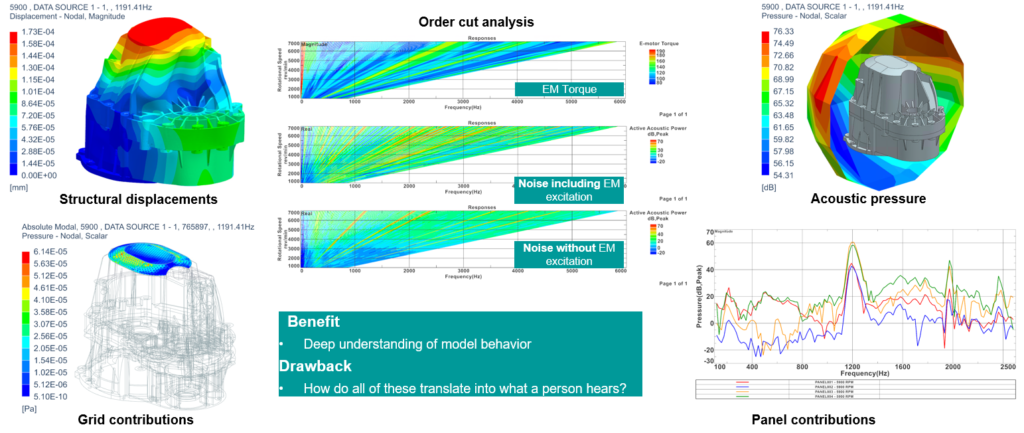
The question still remains: if we change the design to reduce the most important order line, will this make the powertrain “sound better”?
Why can’t we just listen to a simulation model?
As a matter of fact, we can! The latest releases of Simcenter 3D Acoustics integrated a new Auralization product that allows CAE engineers to take their simulation results and listen to them. Understanding how someone will perceive sound coming from an acoustic source helps to more intuitively design and optimize the acoustic performance of products. Additionally, with such a virtual acoustics model, you enable a much broader set of stakeholders, like engineers, marketeers, or sales personnel, to listen to the acoustic signature of different product designs and select the best one with their ears.
Let’s get back to Dave and his effort to make the electric powertrain “sound better.” Using this new toolset, he can simply take the order cut simulation results from his previous analysis, define one of the typical speed profiles considered during validation testing, and listen to the produced sound with a few clicks. Moreover, he can plot the time data of the powertrain noise and analyze its sound quality using a dedicated tool to evaluate sound quality metrics like loudness and sharpness.
The sound is playing in his headphones in less than a minute, and he finally understands what Sarah means with “it does not yet sound right.”
With these results in hand, the discussion with Sarah becomes a lot easier, and by going through several scenarios together, they soon realize the gearbox causes the high sharpness levels that result in the main annoyance, but the electro-magnetic forces drive the loudness, as you hear and see in the results below.
Can we extend the virtual acoustics model to the whole car? Or is that too much to ask?
Components or assemblies like a powertrain are not a final product, they are part of a bigger system. To cope with this additional level of complexity, the Simcenter 3D Acoustics Auralization product integrates the capability to create multi-track scenarios. Each of the tracks consists of
- A source, which can be a rotating machine as described above or a simulated or measured soundtrack in wav or mp3 format
- A simulated transfer function defined by time-domain impulse responses either directly calculated using Simcenter 3D Ray Acoustics or obtained by post-processing frequency-domain simulation results from Simcenter 3D Finite Element or Boundary Element models
Once the scenario is set up, you can easily switch tracks on and off interactively or change their relative importance. This lets you virtually place the product in its intended operational environment and listen to the resulting soundscape. See the illustration of a typical vehicle interior scenario below.
By exploiting these new functionalities, Dave not only feels more confident about his recommendations, he can also let Sarah immediately listen to his suggestions and give feedback.
The virtual acoustics conclusion
The Simcenter 3D Acoustics Auralization product enables CAE engineers to listen to different simulation models and introduce them into their intended user environment (such as a car with acoustic trimming, road noise in the background, and music playing over the radio). Moreover, evaluating the sound quality of these virtual acoustics scenarios in line with typical standards used in industry helps to understand the impact of design modifications and make recommendations that will effectively “make the products sound better.” Inviting key stakeholders to listen to suggested improvements will provide them with the expected final user experience, enabling them to give feedback early in the development cycle.
To learn more about the Simcenter 3D Acoustics suite of simulation tools, visit the dedicated Acoustic Simulation section of the Siemens Simcenter CAE Simulation website.
Content related to virtual acoustics
Leveraging Simulation in the Digital Twin: Simcenter 3D – Acoustics – On-demand Webinar
Acoustic Simulation – Web page – Siemens simulation tools
The science of music – Blog – Acoustic testing equipment
Vehicle NVH integration: how to combine test and simulation – Blog