Vibration control testing for electric cars
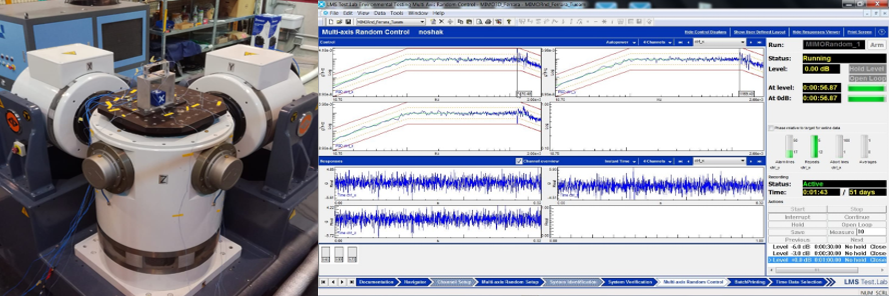
Simcenter Vibration Control Testing
Have you ever heard the song ‘Fuel’ from Metallica?
Gimme fuel
Gimme fire
Gimme that which I desire…
Oh, on I burn
Fuel is pumping engines
Burning hard, loose and clean
And then I burn, turning my direction
Quench my thirst with gasoline…
Wait a second, there should be something wrong with it.
This song is from Metallica’s Reload album which was released at 1997. Okay, I think this explains everything. So, maybe 22 years ago, fuel was still that popular and we should not judge Metallica for this. But, what if they decide to write such a song today? Can they easily adapt ‘electrified vehicles’ or ‘autonomous vehicles’ terms into that song? Anyway, let’s build something from scratch.
Automotive and transportation industry is evolving
We see more and more hybrid electric or fully electrified vehicles on the road. This is actually a crystal-clear fact. But, are we really ready for such radical change? This change will increase uncertainties for vehicle development teams. If we check the weight distribution of Tesla Model S, we see that battery mass is 28.59% of the total vehicle weight. Surprisingly, the battery is even heavier than motor.
Electrical vehicle mass distribution – Tesla, model S (https://www.teslarati.com/tesla-model-s-weight/)
All the different vehicle driving characteristics we brought with electric car development aside, this distinction on mass distribution would even change vehicle development strategies. Due to the difference in mass distribution, vehicle loads will also change dramatically. And this requires extra attention from vehicle development engineers, of course including testing engineers.
Vehicle loads would change due to electrification (symbolic)
The need for vibration control testing
Test engineers need to conduct highly productive tests that make sure the quality is also confirmed to avoid expensive product recalls. Managing vibrations would be vital and test engineers need to create safe, reliable and scalable test profiles. These have to be obtained from standards or real time operations to guarantee life time of the designs.
Turn on I see red
Adrenaline crash and crash my head
Nitro junkie, paint me dead
And I see red…
(Voice of conscience: Okay, enough! Stop singing!)
Vibration control test is quite important for automotive and transportation industry since any product will be exposed to different level of vibration (caused by transportation, different road profiles, engine induced vibrations etc.). In addition to existing importance of vibration effects, fundamentals related to electrification would also bring more complex vibration profiles. And lack of vibration control testing (environmental testing or dynamic environment testing with other words) will increase the chance of mechanical failure and customer dissatisfaction. This all may add cost and reduce brand credibility.
Single-axis and Multi-axis Vibration Control Testing
Vibration control testing can be executed either on the time domain (TWR: Time Waveform Replication) or on the frequency domain. The purpose of this is to simulate a source signal to induce structural responses, which are comparable to the operational environment of the structure.
TWR method uses the exact time history measured in operation conditions. It is ideal for higher amplitude and lower frequencies. Frequency domain closed-loop control is used with a control spectrum. And this control spectrum can be derived from specs (standards) or measured time histories with random (Power Spectral Density – PSD – based), sine or combined modes.
Environmental testing with closed-loop
Measuring the response of a structure when exciting, it is necessary for closed-loop test to check if control signal matches the predefined excitation level. To do this, drive signal needs to be constantly updated. Closed-loop vibration control is also necessary to verify that the test structure is not in danger and to shut down the test if it is.
Closed-loop testing by using Simcenter SCADAS and Testlab
Vibration control test can be done either on single-axis or on multi-axis based on the required specs, system complexity or load characteristic.
Simcenter Testing presents solutions for both single-axis and multi-axis systems.
For single axis systems we offer a complete solution for vibration and shock testing. This includes sine, random vibration, shock and tracked sine dwell control. The solution integrates common industry standards and is fully compatible with electro-dynamic shakers, hydraulic actuators and climatic chambers.
Single-axis closed loop test in practice
In addition to single-axis control tests, we also offer multi-axis control systems. The goal is to represent real word environments, where all modes excited simultaneously. MIMO (Multiple Input Multiple Output) vibration control is suitable for heavy and/or slender structures and bring time efficiency by reducing test duration. Time efficiency is very important for such lab tests. You want to replicate real-life conditions where all the customers expect long-term quality without exception.
Multi-axis vibration control test by using Simcenter SCADAS and Simcenter Testlab
Simcenter vibration control solution lets you to enjoy high-end performance in an entry-level solution. What’s more, it maximizes your productivity to qualify your products faster. It is easy-to-use and can also automate your test procedures for lengthy and complex campaigns.
Multi-physics Data Acquisition and Analysis
In addition to closed-loop vibration testing, Simcenter SCADAS hardware enables parallel data acquisition from a wide range of different sensor types during both single-axis and multi-axis control tests which can be used for further analysis. This enables users to cover multi-physics testing on single system.
Simcenter Testlab software enables in-depth online and offline data analysis to gain better understanding about the environment. By using Simcenter Testlab software, it’s all possible to execute multidisciplinary analysis including NVH, acoustics or durability.
I guess that Metallica was right on some point when they turn their direction (maybe to electric cars?) after they burn.
And then I burn, turning my direction…
For further information, visit our website, post a comment or email safak.has@siemens.com.
Stay tuned! ?