The fastest chemistry solver on the CFD market?!
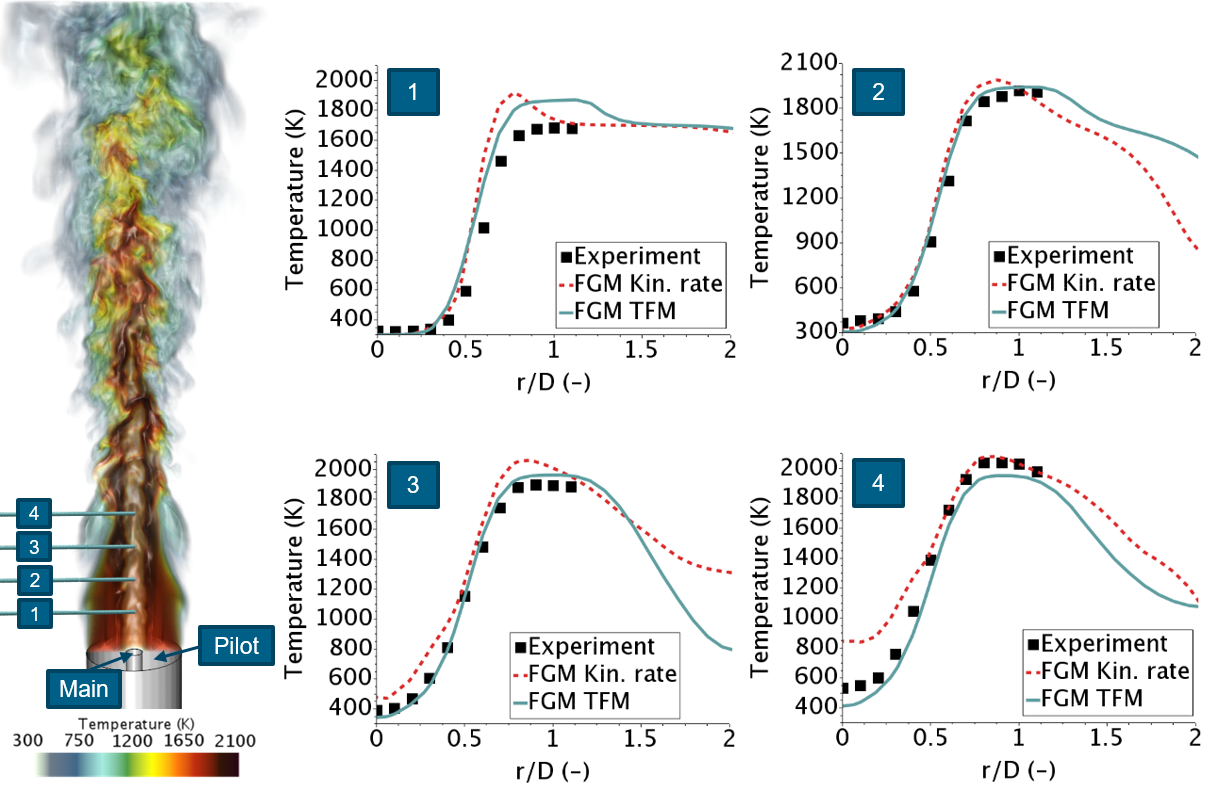
Designing next generation combustion systems is a true challenge today, with stricter and stricter emission regulations, competitive pressure to deliver shorter time-to-market to stay ahead of competition and the need to adapt to new fuels and fuel compositions. Additionally new technologies such as 3D printing creates vast opportunities to optimize the combustion chamber design for e.g. gas turbine combustors with less constraints, as recently demonstrated by Siemens Industrial Turbomachinery AB. Finding the best design among the countless possibilities while ensuring all requirements are met demands aggressive usage of the Digital Twin. The digital twin needs to be accurate and fast to minimize time to market.
New lean-burning combustion systems are typically prone to thermoacoustic instabilities, which need to be avoided. Thermoacoustic instability predictions, accurate emissions as well as re-light simulations (like in the video below) typically means LES is required. Which means the CPU cost is high. Siemens PLM software works hard to bring you as fast and as accurate solutions as possible to help minimize your time-to-market, which is demonstrated again in the upcoming release of Simcenter STAR-CCM+v13.06.
In this version two major features are added which make combustion simulations both faster and more accurate:
- Faster complex chemistry simulations – High fidelity calculations are now (much!) faster. Potentially the fastest on the CFD market..!?
- Dynamic Thickened Flame Model with complex chemistry and FGM combustion models – LES combustion simulations are now more accurate.
The complex chemistry model solves all reactions online, and is the most suitable model for e.g. CO emissions, low load conditions and ignition driven combustion. Since all reactions are calculated online it is an expensive combustion model. The chemistry solver was quick already in Simcenter STAR-CCM+v13.04, using an optimized CVODE implementation and acceleration techniques such as Dynamic Mechanism Reduction, clustering and ISAT. In this release however, the solver is made even quicker, for some cases much quicker. A secret sauce (No, we will not tell you the recipe! It’s from grandma!) is implemented which makes all simulations faster, regardless of mechanism size, and a sparse solver is introduced which significantly speeds up calculations with more than 100 transported species. See the chart below for examples of CPU time speedup in v13.06 vs v13.04.
Speedup of total simulation time STAR-CCM+v13.06 vs v13.04. All cases except the last one were run without chemistry acceleration. Case description: Sandia Flame D [1]: 5k cells, steady RANS. IFRF glass furnace [2]: 0.64M cells, steady RANS. Flameless combustor [3]: 6.3M cells, unsteady LES. Industrial GT1: Gas Turbine, 10M cells, unsteady LES. Industrial GT2: Gas Turbine, 25M cells, steady RANS. ECN spray H [4]: 92k cells, unsteady RANS. Generic GT: Gas Turbine, 2M cells, steady RANS, clustering acceleration technique. Chemical Mechanisms: GRI 3.0 [5]: 53 species, 325 reactions. Wang [6]: 109 species, 543 reactions. Lu [7]: 188 species, 842 reactions. Ahmed [8]: 246 species, 1284 reactions.
Note: This is the speedup in total runtime, not just the speedup in chemistry. The speedup is ranging from 1.16x faster to 12x(!) faster, and is very case dependent. Typically the heavier the chemistry calculation, the higher the total speedup. The cases represented by the five left-most bars were all run with the GRI3.0 mechanism, with 53 species, and are ordered by mesh size. Note that even for this relatively small chemistry a full scale 25M cell simulation of an industrial gas turbine (denoted GT2 in the graph) is more than 1.9x faster! The industrial gas turbine GT1 gives the least speedup, indicating that something else than chemistry is probably the bottleneck. The three following bars are all for the same, transient axisymmetric spray bomb case, using different chemistry sizes; Wang = 109 species, Lu = 188 species, Ahmed = 246 species. The speedup is higher the larger the mechanism. Thus usage of large chemistries is more accessible in v13.06. Finally the last bar shows a RANS simulation of a generic gas turbine with a 188 species mechanism. The massive speedup of 12x in this case indicates that the stiffness of the chemistry for this case is much better handled by the “secret sauce” in the updated solver.
With these updates, specifically thanks to the secret sauce added, we believe Simcenter STAR-CCM+ now has the fastest complex chemistry solver on the market..! Be my guest and prove me wrong! Or right…
Of course the new solver is verified to be as accurate (or even more accurate) than the previous version, as demonstrated in the plots below for ECN spray H.
Verification of results in v13.04 vs v13.06 for ECN spray H. Transient temperature trace as well as CO and n-heptane mass fraction profiles at a line 3.5 mm off axis at t=1ms are consistent.
And… now you can even use huge chemistries in your CFD calculations, as demonstrated by the axisymmetric RANS of the ECN spray bomb below. This case was run with a detailed n-heptane chemistry from LLNL[9] of 697 species and 2987 reactions(!), using DMR as acceleration technique.
And… As if that wasn’t enough… The combustion table generation time for flamelet combustion models is also significantly faster in v13.06, which makes usage of large chemistries more accessible. See the chart below for table generation times for 0D and 1D flamelet tables for FGM. The table generation time for the 163 species mechanism has shrunk from the order of hours to the order of ten minutes!
Speedup of FGM table generation in v13.06 vs v13.04
So, now you can achieve more at the same time. But that’s not it… To support the increasing need for LES combustion for accurate prediction of e.g. thermoacoustic instabilities and emissions, we have extended the Dynamic Thickened Flame model (TFM) in STAR-CCM+ to be compatible with complex chemistry as well as the efficient and accurate FGM flamelet combustion model.
The FGM kinetic rate model and complex chemistry are both most accurate when resolving the flame front on the CFD grid. However since the laminar flame thickness is typically in the order of 1 mm or less, this means impractically fine grids. The Dynamic Thickened Flame model (TFM) is a well-established technique to remedy this problem by artificially thickening the flame to be resolved on the actual grid. This typically gives a better flame position for premixed and partially premixed flames. The model is made compatible with both FGM and complex chemistry, to enable maximum impact at minimum time for the problem at hand. As a user you select the number of grid cells you want the flame to be refined on, and the model does the rest. For an example see the LES simulation of the Chen flame 3 [10] below, using FGM kinetic rate vs FGM TFM.
LES simulations of Chen Flame 3 [10], FGM kinetic rate vs FGM with dynamic thickened flame model
Chen Flame 3 is a premixed methane lab flame with a pilot flame igniting the main fuel/air mixture. The plots show temperature over radial direction for 4 measurement stations. As can be noted by measurement station 3 and 4, the flame length is better captured in TFM: The temperature at the axis is too high when using FGM Kinetic rate, meaning the flame is too short. In TFM the temperature profiles are very well captured.
We hope these enhancements will help you become more efficient and effective in your design work. We want to learn whether these enhancements help you, so please don’t hesitate to reach out to give feedback, or use the Reactions, Combustion Technical Forum group at the Steve Portal to tell us how it goes. Your input guides our future direction.
Ps. Don’t miss our recent blog on design optimization of rotary kilns and SNCR systems here.
[1] http://www.sandia.gov/TNF/DataArch/FlameD.html
[2] Nakamura, T., Vandecamp, W. L., Smart, J. P. Technical report, IFRF Doc No F 90/Y/7, 1990.
[3] Veríssimo A. S., Rocha A. M. A., and Costa M, Energy & Fuels 25 (6), pp 2469–2480 (2011)
[5] http://combustion.berkeley.edu/gri-mech/version30/text30.html
[6] Wang, H. Yao, M. Yue, Z. Jia, M. and Reitz, R. D. Combust. and Flame 162, pp. 2390 – 2404 (2015)
[7] http://www.engr.uconn.edu/~tlu/mechs/mechs.htm
[8] Ahmed, S.S., Mauß. F., Moréac, G., Zeuch, T., Phys. Chem. Chem. Phys., 9, 1107 – 1126 (2007)
[9] https://combustion.llnl.gov/mechanisms/alkanes/n-heptane-detailed-mechanism-version-3
[10] Chen, Y. C., Peters, N., Schneemann, G. A., Wruck, N., Renz, U. Mansour, M. S., Combustion and Flame, 107:223-244 (1996)