A template to contemplate: automate your marine design processes
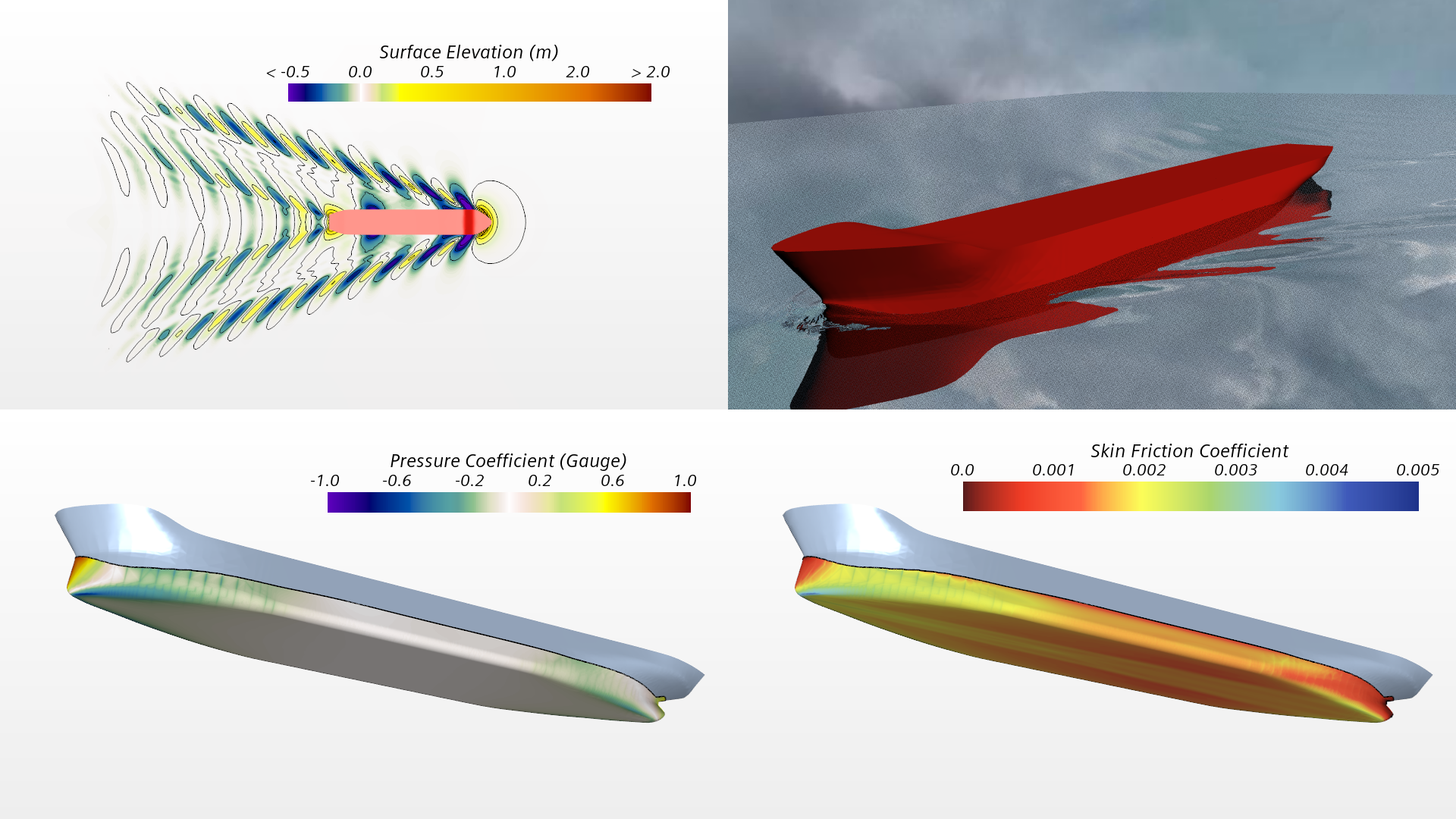
The industry has an actual deadline to meet: 2050. Since the adoption of the International Maritime Organization (IMO) Strategy on Reduction of Greenhouse Gas (GHG) Emissions from Ships in 2023, the maritime industry has been looking at ways to reach its goals on time. Whether modifying existing fleets or building new ships, the engineering challenges arising to comply with environmental guidelines are huge.
Naval architects and design engineers need to make radical decisions faster. To do so, they turn to simulation. In this maritime context, simulation is no longer a nice-to-have tool, it’s essential for exploring every aspect of vessel performance and numerous design options.
To meet your targets, you need CFD simulation tools that make it easy to set up complex cases, embed best practices, and enable automation. You also need tools that are fast to run and contain the advanced multiphysics features needed for marine simulation. The good news is that you can do all of that and more with Simcenter!
Should we introduce it?
Simcenter STAR-CCM+ has a full suite of tools to completely automate processes and workflows and create simulation templates. These templates allow for repeatable workflows that can be created by experienced analysts and passed on to design engineers to make engineering decisions.
Simulation templates can eliminate most of the manual processes involved in building a CFD simulation via a parameterized template model by boiling down the simulation to its minimal set of inputs. From there, all meshing calculations, boundary conditions, solver settings and post-processing can be applied such that simulations are repeatable and embedded with your organization’s best practices. The templates utilize tools all built into the software, so they can be updated when desired; they are not black box tools you get from your software provider!
One such template is the virtual tow tank (VTT) template. Let’s explore it a bit more, shall we?
Setup time: it went so fast, I didn’t see it happening…
Setting up a marine CFD simulation requires a lot of steps: importing CAD, defining mass and hydrostatic properties, creating a suitable mesh, defining solver physics… Not here.
The parameterized template model automates all these settings and calculations. There is no need for scripting and the file can be reused for multiple simulations and shared with others. So, using a template ensures consistency and best practices across all simulations and the repeatability of results.
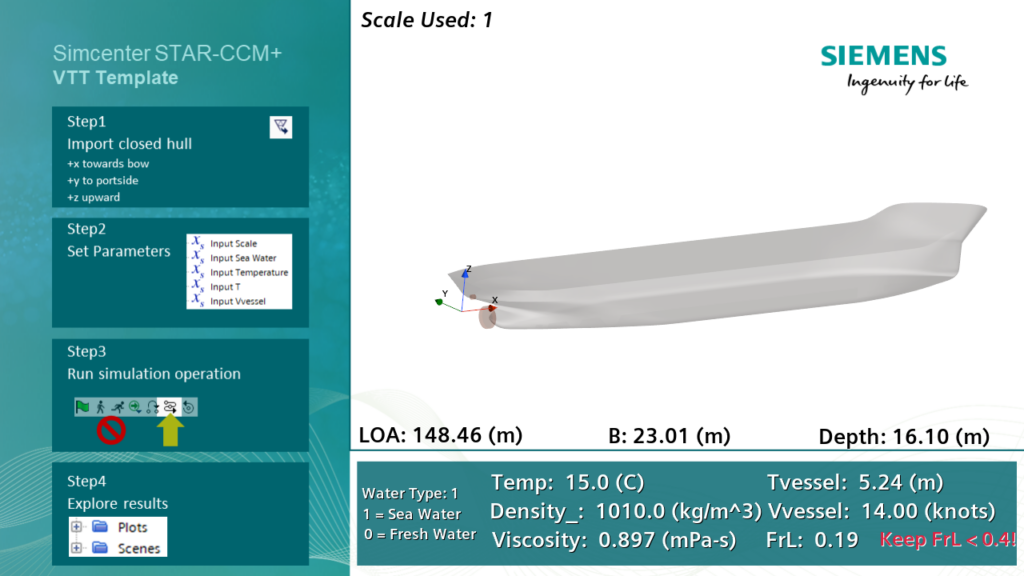
Okay… What’s next? Meshing?
Traditional CFD approaches require several hours of manual setup. What size should the mesh be? How do I suitably build my boundary layer mesh? And where should I place the appropriate refinements?
If you think about it, all these decisions are based on the vessel speed and size and shape of the vessel being analyzed. A set of step-by-step simulation operations is embedded into the simulation file to make these decisions automatically. The operations will determine all the meshing sizes, places for refinement, where to apply the boundary conditions and all the relevant solver settings and stopping criteria. This process is so powerful, you won’t even notice it taking place and you press a button to mesh AND run the simulation; and these two steps are seamlessly linked together.
What is perhaps even more powerful, is this automated process then allows for multi-mesh sequencing (MMS). This method automatically refines the mesh, maps the previous solution to the mesh and continues the run. This process is repeated systematically until the final mesh discretization is reached. On average, this process improves the run time by a factor of 4 compared to running the model only on the final grid!
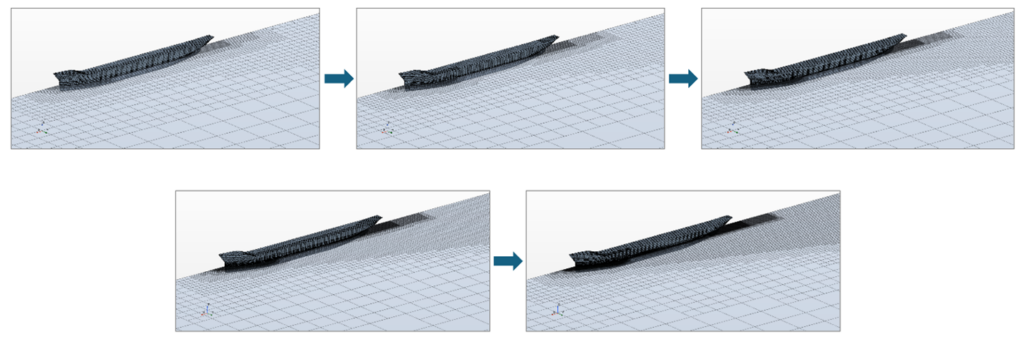
What about post-processing?
Reporting for key metrics such as resistance, trim, heave or shaft power can be set up in advance. Field data such as friction coefficients, pressure coefficients and generated wave elevation can be displayed in pre-defined scenes and exported to PowerPoint using a macro. Key information, such as local wake fraction can be exported to CSV data automatically to be read into other software packages for further analysis, if required.
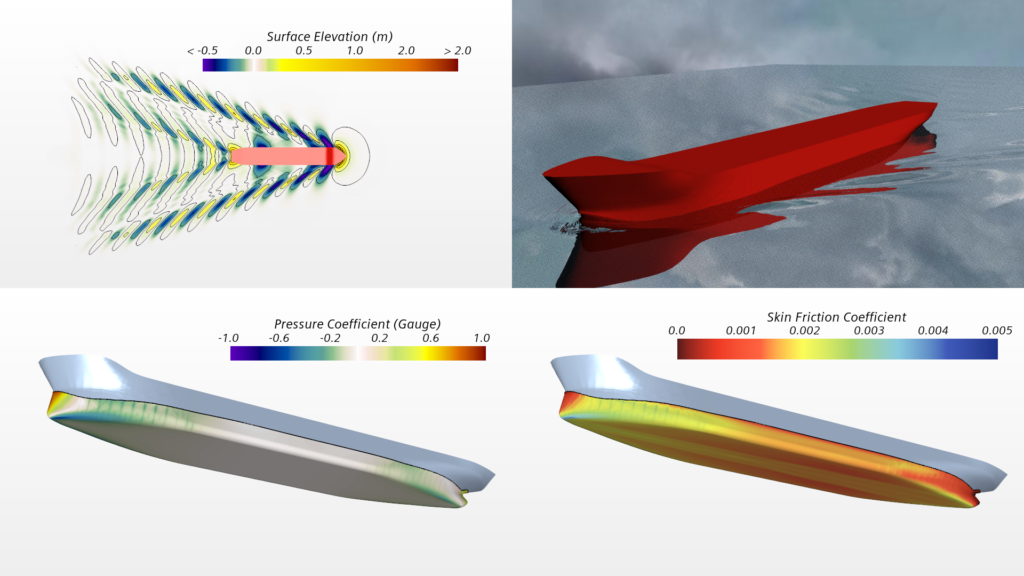
Got it – faster simulation runs. What about a complete design sweep?
The template is fully parametrized, meaning that any type of design exploration study can be implemented using the design manager tool in Simcenter STAR-CCM+. You can automatically explore the design space; generate resistance and powering vs speed curves, explore effects on mass, or analyze a range of possible hull forms and more!
Curious to learn more?
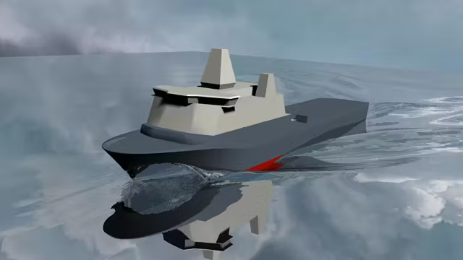
WEBINAR
Improve your ship design process with faster hydrodynamic simulations
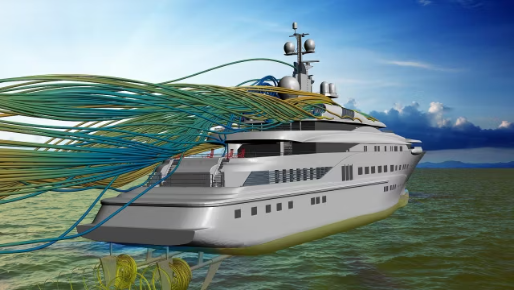
EBOOK
Marine computational fluid dynamics (CFD): simulation for ship design optimization
Comments
Leave a Reply
You must be logged in to post a comment.
That’s really informative post. I appreciate your skills. Thanks for sharing.