STAR-ICE: Engine simulation in Simcenter STAR-CCM+
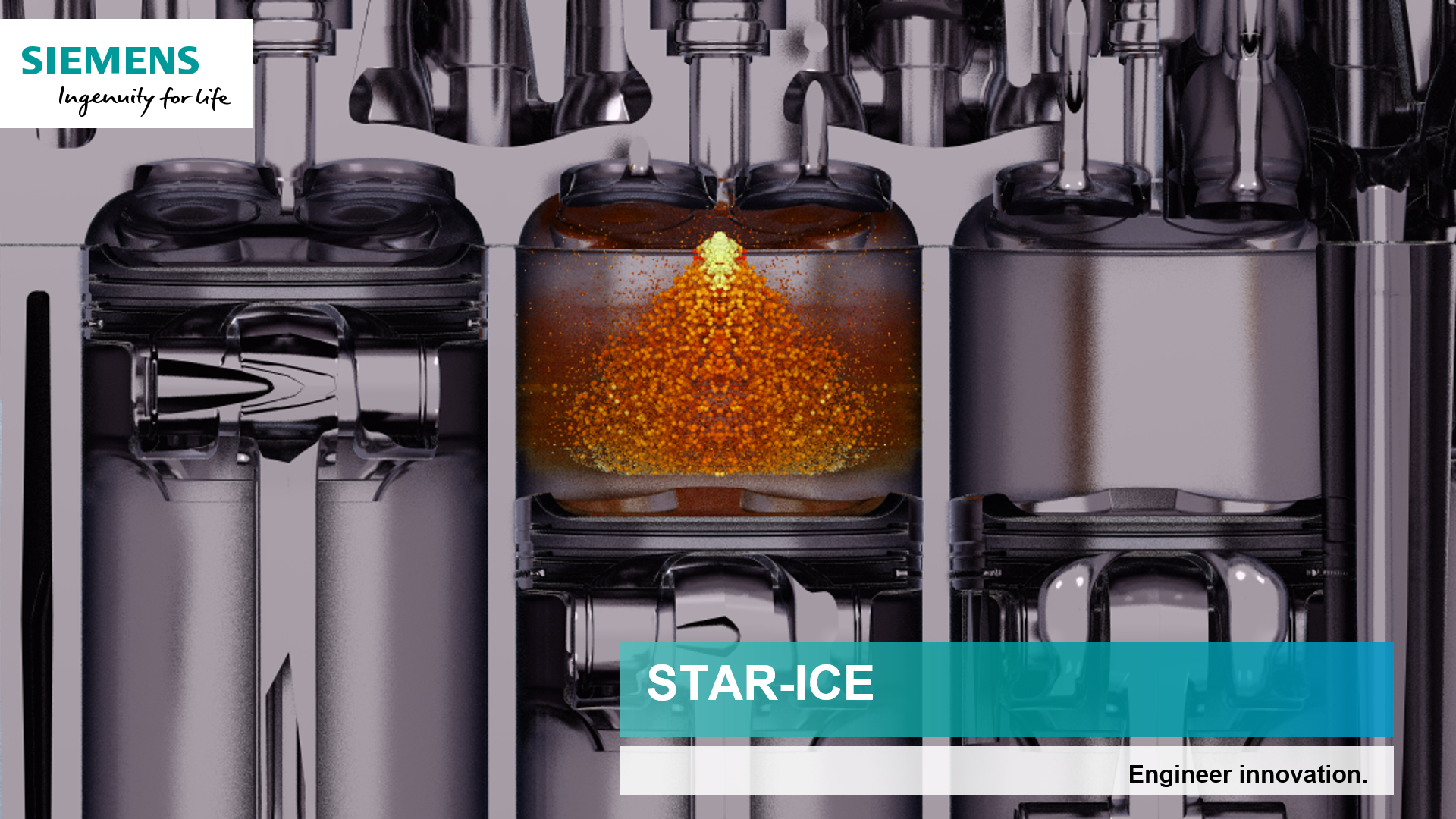
While we all continuously hear about the electrification of automotive powertrains, the reality is that the internal combustion engine will not disappear anytime soon and, in fact, will be a staple of powertrains for decades to come. The push to downsize the internal combustion engine and the integration into hybrid powertrain platforms present many new challenges for engine development which can only be overcome using extensive CFD simulation.
STAR-ICE is a new add-on to Simcenter STAR-CCM+ that allows you to easily perform accurate in-cylinder CFD simulations of engines. Default settings and automatically-created post-processing output are aimed at giving the engineer a “running start” and mean that you don’t need to be a CFD expert to set up and run one of the most challenging CFD simulations around!
STAR-ICE benefits and features at a glance:
- problem set up: setup an engine simulation in minutes
- automatic meshing: morph and map takes care of moving components
- cold flow: maximize trapped air mass
- charge motion: improve mixing of inducted air and injected fuel
- design exploration: automatically optimize engine performance
- validation: excellent correlation with experimental data
- the future: combustion is coming
Simple Problem Set Up
STAR-ICE opens up a minimal interface which shows only those inputs required for setting up an in-cylinder simulation, presenting a “top-down” workflow (you start at the top and work your way down through various levels). Most menus are one or two levels deep.
You do not have to be an expert Simcenter STAR-CCM+ user to set up and run in-cylinder simulations using STAR-ICE as it uses an application-specific workflow and simplified interface. However, expert users can use STAR-ICE simulations as the starting point for performing more complicated multiphysics engine simulations that exploit the full range of Simcenter STAR-CCM+ simulation capabilities.
STAR-ICE has been specifically developed to make setup quick and easy and leave time for the analyst to spend on “engineering” the solution rather than setting up the problem with lots of mouse miles and button clicks. From fast setup of typical multi-hole injectors which can easily be customized for spray targeting, to quick selection of fuels, to automatic setup of common post-processing outputs like liquid and vapour penetration plots and fuel mass tracking, STAR-ICE has been designed to make the simulation setup easy and allow engineers to derive the most value of out the simulation process.
Return to top. ^
Automatic Meshing
STAR-ICE employs a simulation driver to run a transient mesh motion process. You only need to create a single initial mesh (comprising of trimmed cells and prism layers to capture boundary layer flow features). All of the mesh movement is automatically taken care of by STAR-ICE, which automatically morphs and maps the mesh to account for the movement of the piston and valves. STAR-ICE performs quality checks on the mesh as it morphs, automatically creating a new undistorted mesh when necessary and mapping the simulation results to it.
The mesh is automatically refined in critical areas in line with best-practice: around the valve, the valve seat, the valve throat, up into the ports and around the gasket gap. This is done automatically for every simulation and does not require manual intervention by the user. The user has complete control over the mesh setup and can add additional regions of refinement (such as around a spark plug) as required.
This morph-map approach has been extensively tested and is highly conservative of mass for all practical applications.
Return to top. ^
Cold Flow
Any in-cylinder simulation is among the most complex CFD simulations you can perform. The combination of high-speed flows, mesh motion requiring an EXTREMELY high level of mass conservation, and very small time scales (fractions of a crank-angle degree typically require time steps on the order of 1e-006 [s]) means a lot of work goes into the setup and the numerics must be carefully selected to accomplish stable runs with reasonable turn-around times. This is all before we start layering on complex physics models when we start to include fuel injection (Lagrangian spray, droplet-wall interactions, wall films) and combustion (ignition, flame propagation, emissions formation, knock).
For this reason, a lot of simulation performed early in the development process is concentrated on so-called “cold-flow”. This involves modeling the transient process of the airflow in the cylinder, typically with the objective of maximizing the trapped air mass and examining the bulk motion (swirl and tumble) that this flow induces. Often we also look at the evolution of turbulence to better understand the potential for fuel and air mixing and, specifically in spark-ignited engines, what the turbulence levels around the spark plug are at the intended time of ignition (start of combustion).
This type of simulation carries a lot of weight in the engine development process today. Using cold flow simulation, engineers can optimize trapped mass by exploring port and combustion chamber design and by looking at interactions with valve timing strategies. Some companies even keep correlations of bulk flow and turbulence metrics vs. quality of combustion to help design a well-behaving combustion system prior to even performing a combustion simulation!
STAR-ICE allows you to set up cold flow simulations for multi-valve engines with the automated setup of mesh motion, allowing you to go from raw CAD geometry to running simulation in just minutes.
Return to top. ^
Charge Motion
With the latest release of Simcenter STAR-CCM+, we take a big step forward in STAR-ICE with the capability to set up and run “charge motion” simulations. This builds upon our previous “cold flow” capability by including the setup of liquid fuel injection and modeling the ensuing mixing process. Charge motion simulations allow engine manufacturers to improve combustion quality, by controlling the mixing of inducted air with injected fuel by identifying and rectifying rich or lean mixture regions, especially in critical parts of the cycle, such as when the piston approaches TDC and during spark ignition. This is especially important in today’s direct injection designs, where the injection of fuel directly into the cylinder greatly impacts the bulk flow and turbulence level – the insight provided by simulation is more important than ever.
Another critical role which charge motion simulation plays is the assessment for potential formation of harmful emissions. Again, ideally, we want to achieve high-quality mixing of fuel and air, which is especially challenging in direct injection systems where, at high load operating points, there is fuel injection during large portions of the engine cycle. Simulation tells us not only where we have lean and rich pockets of charge, but how fast the liquid fuel is evaporating, how much is impacting on surfaces in the cylinder, and if it’s forming films or pools on those surfaces. All of these give indications of the magnitude of harmful emissions formation which, if not mitigated, will need to be “cleaned up” downstream of the engine using expensive aftertreatment devices in the exhaust line.
While the ultimate in-cylinder simulation to address these concerns is one with full combustion and emissions models, these can still be comparatively expensive to run. It may take significantly longer to get a solution from a combustion and emissions simulation than a simpler charge motion simulation. Additionally, over the years OEMs have developed large databases for design guidelines based purely upon charge motion, using just the bulk motion inside the cylinder, metrics of fuel and air mixing quality, and levels of turbulence around the spark plug which tell them whether combustion is going to be good or not, saving them valuable engineering time, especially in the early design stages of a combustion system.
Return to top. ^
Automated Design Exploration
With the power of the Simcenter STAR-CCM+ platform and the recently-released Design Manager, users can leverage the automation capabilities, scalability, and flexibility of the platform to easily and quickly execute design studies in order to optimize their engines for the next generation. Additionally, since STAR-ICE automatically creates a parametric model, you’re only a few mouse clicks away from easily sweeping multiple operating conditions to understand the bulk motion and turbulence at different speeds/loads.
Return to top. ^
Experimental Validation
STAR-ICE and Simcenter STAR-CCM+ have been extensively validated for engine simulations, using both proprietary and public domain engine designs.
One example is our validation of the University of Michigan Transparent Combustion Chamber-III (TCC-III) Optical Internal Combustion Engine, which is a 2-valve head, 4-stroke, spark-ignition engine with a pancake-shape combustion chamber. The report shows that STAR-ICE produces a runnable physics setup, with appropriate boundary conditions, automatically and produces key post-processing plots in terms of the crank angle. STAR-ICE then automatically drives a Simcenter STAR-CCM+ simulation of the engine using the morph/map process.
The results demonstrate excellent correlation with global thermodynamics variables (including cylinder trapped mass, pressure, and temperature) and, compared with visualization from the experimental rig, the major features of the flow field are also well captured.
Return to top. ^
Future Developments: Combustion
Siemens PLM is completely dedicated to the Engine Simulation market, recognizing that internal combustion engines are here to stay and that only advanced simulation can deliver the cleaner more efficient engines that society deserves.
The meaningful simulation of cold flow and charge motion is just the beginning of the in-cylinder simulation process. Modern simulation teams build upon this by adding combustion to get a more complete prediction of the engine performance. STAR-ICE, as part of Simcenter STAR-CCM+, will receive updates three times per year and will continue to add features that address these simulations in the coming year, including class-leading combustion capability combining physical and kinetics models.
Return to top. ^
For information on or to download STAR-ICE, please visit the Steve Portal.