To mesh or not to mesh: Smoothed-Particle Hydrodynamics (SPH) coming to Simcenter STAR-CCM+
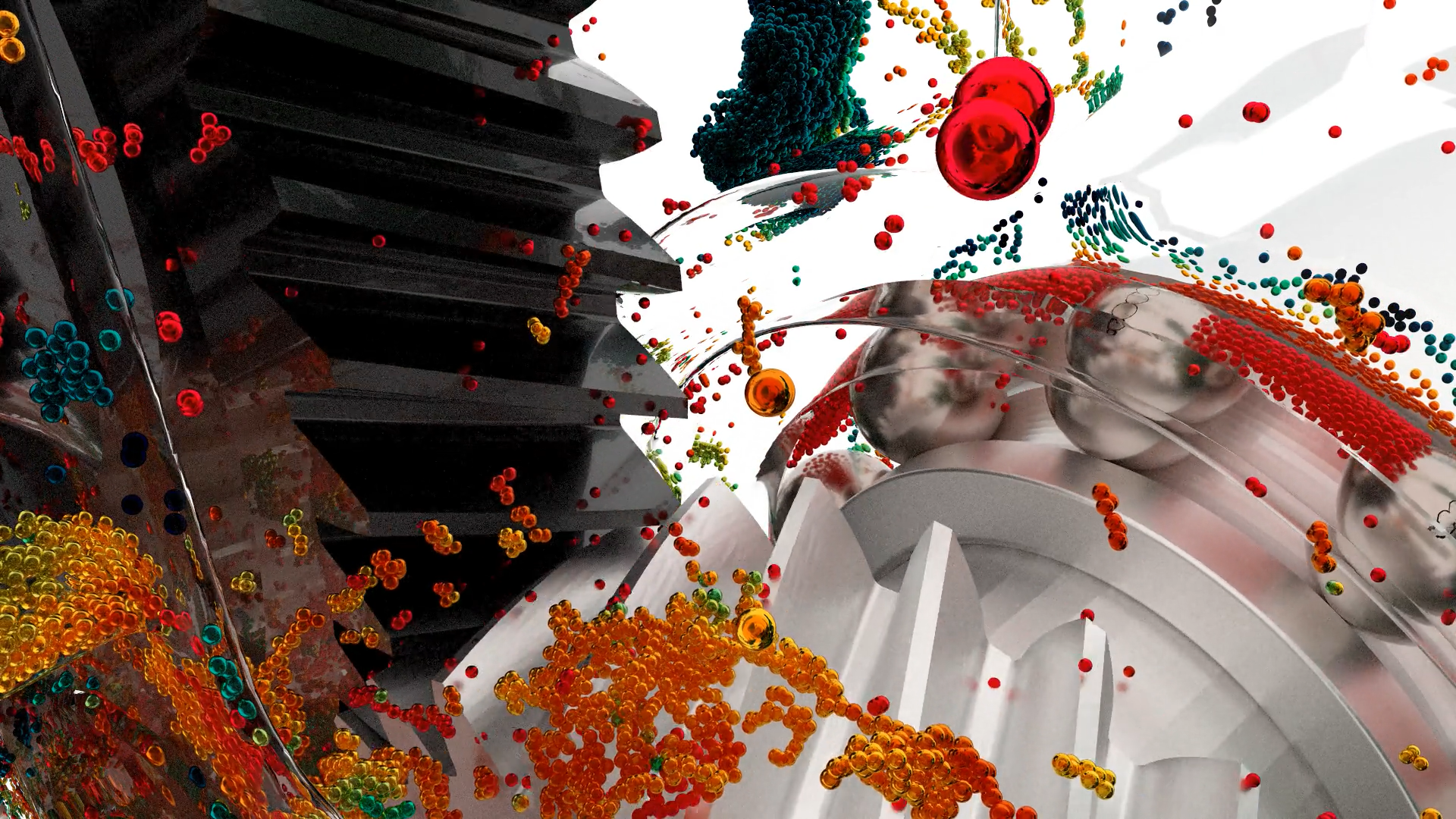
To mesh or not to mesh, that is the question…
If Shakespeare’s Hamlet was a 21st-century computational fluid dynamics (CFD) engineer, that would probably be the revised version of his existential question. Triggered by the murder of a close relative, the original Hamlet wonders and counts arguments and counterarguments about what is more desirable: “To be or not to be” is the question about being alive or not being alive. And if you look at the development of CFD technology these days, the rise of meshless technology makes you wonder:
Will Smoothed Particle Hydrodynamics (SPH) one day kill the mesh-based finite volume CFD approach? And is one better than the other?
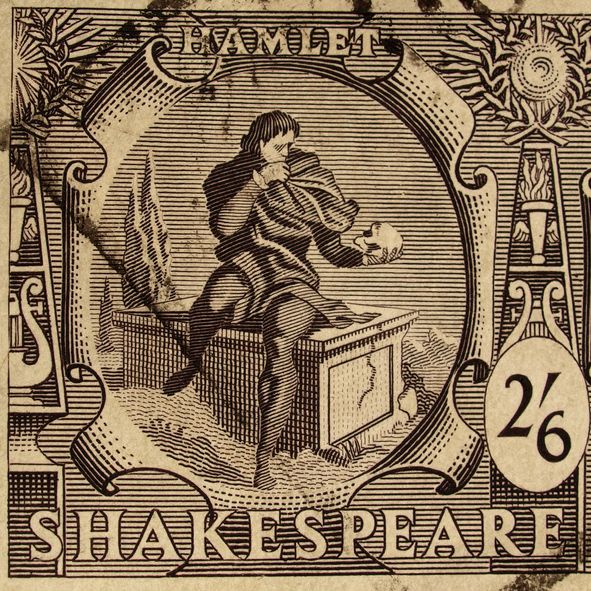
The original Hamlet concludes that the “to be or not to be” question remains unanswerable. There is no guarantee that each side, dead or alive, is better than the other and therefore, he cannot choose to be or not be.
But all philosophy aside… and back to fluid dynamics:
“To mesh, or not to mesh”… does the revamped CFD question also remain unanswerable? Is there no guarantee that the mesh-based method or meshless technology is better than the other? That is the question we will try to answer in this article.
A little bit of history
Numerical simulation has increasingly become prominent in solving various applications inherent to fluid dynamics. Two approaches evolved parallelly in recent years.
Eulerian methods emerged in the late 1960s. Those techniques are based on geometric, fixed, or adaptive grids. Flow properties like velocity or pressure are estimated at each mesh cell via numerical formulations such as finite differences, finite elements, or finite volumes. The finite volume methods are very successful for most of the fluid applications today. However, the use of mesh-based methods results in difficulties for specific applications, particularly for highly dynamic free surface flows, complex moving objects, or large deformations. And while those can be overcome with modern finite volume technologies, this typically comes at an increased computational cost.
To address and lift these restrictions, Gingold, Monaghan (1977), and Lucy (1977) introduced a Lagrangian approach: the so-called Smoothed-Particle Hydrodynamics (SPH) method. This technology is part of a new generation of numerical methods, developed to overcome meshing-related constraints.
Still based on the Navier-Stokes equations, the SPH meshless method represents the fluid flow by moving elementary bodies referred to as particles. Moving particles thus discretize the continuous space domain. This defines a particle-based method.
Those particles are individually tracked: they have their own position, velocity, and size. They carry – like mesh cells in standard finite-volume methods – the state variables of the fluid parcel (velocity, density, pressure, temperature…). This evaluation considers the neighbor particles’ contribution by using a kernel function, giving the smoothing characteristic of the formulation.
If you look at the video below of an experimental setup of a simplified gearbox lubrication application, the SPH method discretizes the liquid oil by fluid particles.
Thanks to its Lagrangian nature, the SPH meshless method can easily adapt to complex moving objects, despite two solid bodies coming in contact. Even if the SPH technology does not discretize the gas phase, it represents the free surface between liquid and gas with no diffusivity even though there are lots of jets and splashes in the fluid flow.
Lately, many studies have been carried out on the numerical aspects of precision and stability (Groenenboom et al., 2019; Shadloo et al., 2016; Violeau and Rogers, 2016). Research and development allowed the current industrial use of the SPH solver for industrial applications in multiple fluid mechanic fields, such as the automotive, marine, and aerospace industries.
A huge bit of history
The good news is that with the release of Simcenter STAR-CCM+ 2402, we will merge these two historical streams of CFD methods inside one CFD software tool. With the SPH add-on license, you will now be able to choose – for a first set of applications – between mesh-based finite volume and mesh-free SPH CFD depending on your accuracy vs speed requirements.
By removing the volume meshing step, the SPH workflow in Simcenter STAR-CCM+ benefits from a seamless user experience compared to other multiphase models. Like the mesh-based approaches, it takes advantage of the advanced pre-processing of 3D CAD in Simcenter STAR-CCM+. But to further boost productivity, as opposed to classical finite volume methods, SPH can perfectly deal with geometries that are not closed or non-conformal. Moreover, the SPH model robustly simulates complex motions even if there are contacts between solid bodies, like the teeth of moving gears.
In the video below, you can see in practice how you can set up an SPH simulation of an industrial gearbox in just a few minutes!
For such a powertrain gearbox, the typical objective is to minimize the volume of oil inside the casing of the gearbox while ensuring the oil gets into critical locations. Ideally, we would like to minimize the churning losses of the machine and therefore, optimize its efficiency. As you can see in the animation, you can seamlessly leverage the unrivaled power of Simcenter STAR-CCM+ visual post-processing and look at where the fluid goes by visualizing the particles and monitoring wall wetting.
But you can also leverage all quantitative data analytics capabilities of Simcenter STAR-CCM+ and -in the example at hand – control the churning losses by looking at the evolution of forces and torque along your simulation.
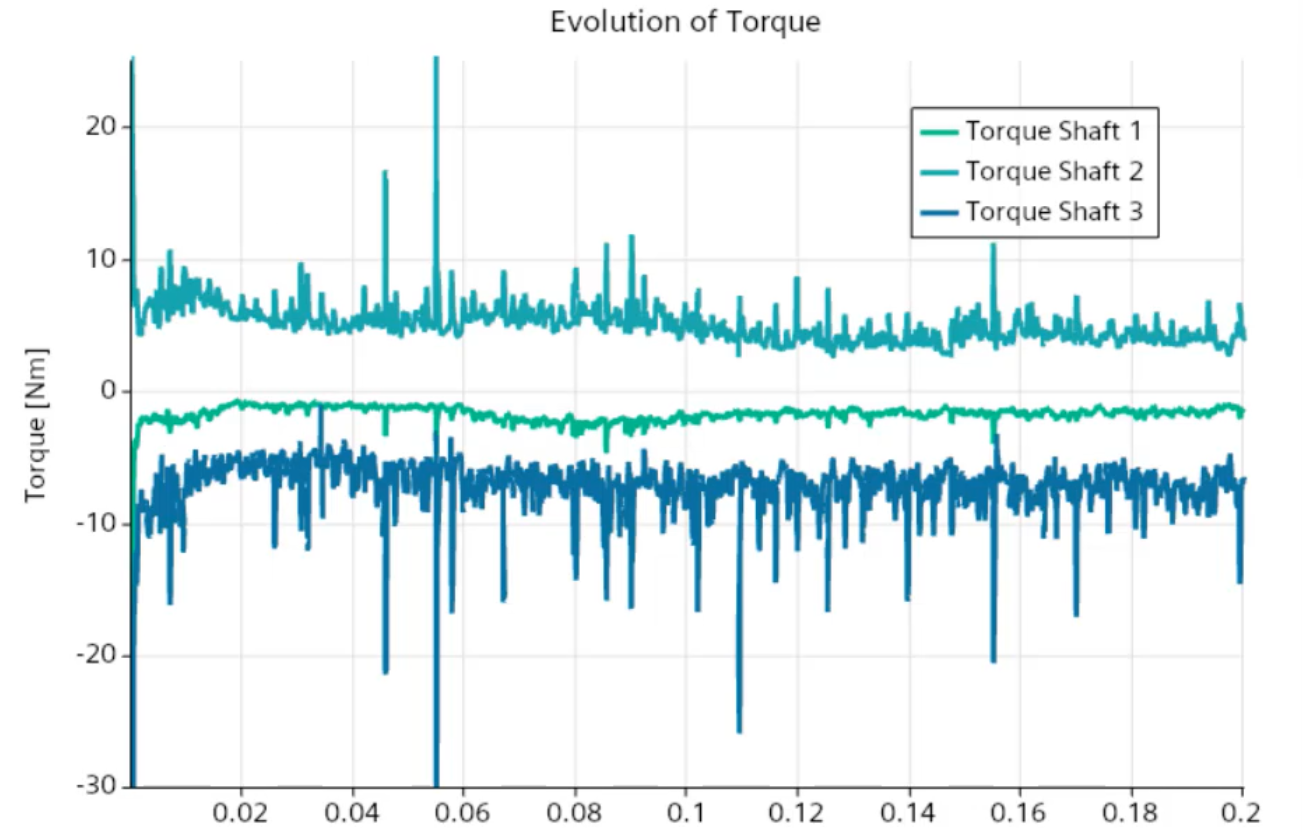
Furthermore, thanks to the integration, the SPH meshless solver works out of the box with the Design Manager. With a single click, you can create a design exploration project for your multiphase applications. For powertrain lubrication applications, it can help you select the optimum conditions for the rotation speed or the oil quantity in the casing. It also enables you to test multiple design shapes and select the optimum one in terms of the number of gears, number of teeth for each gear, design of the casing…
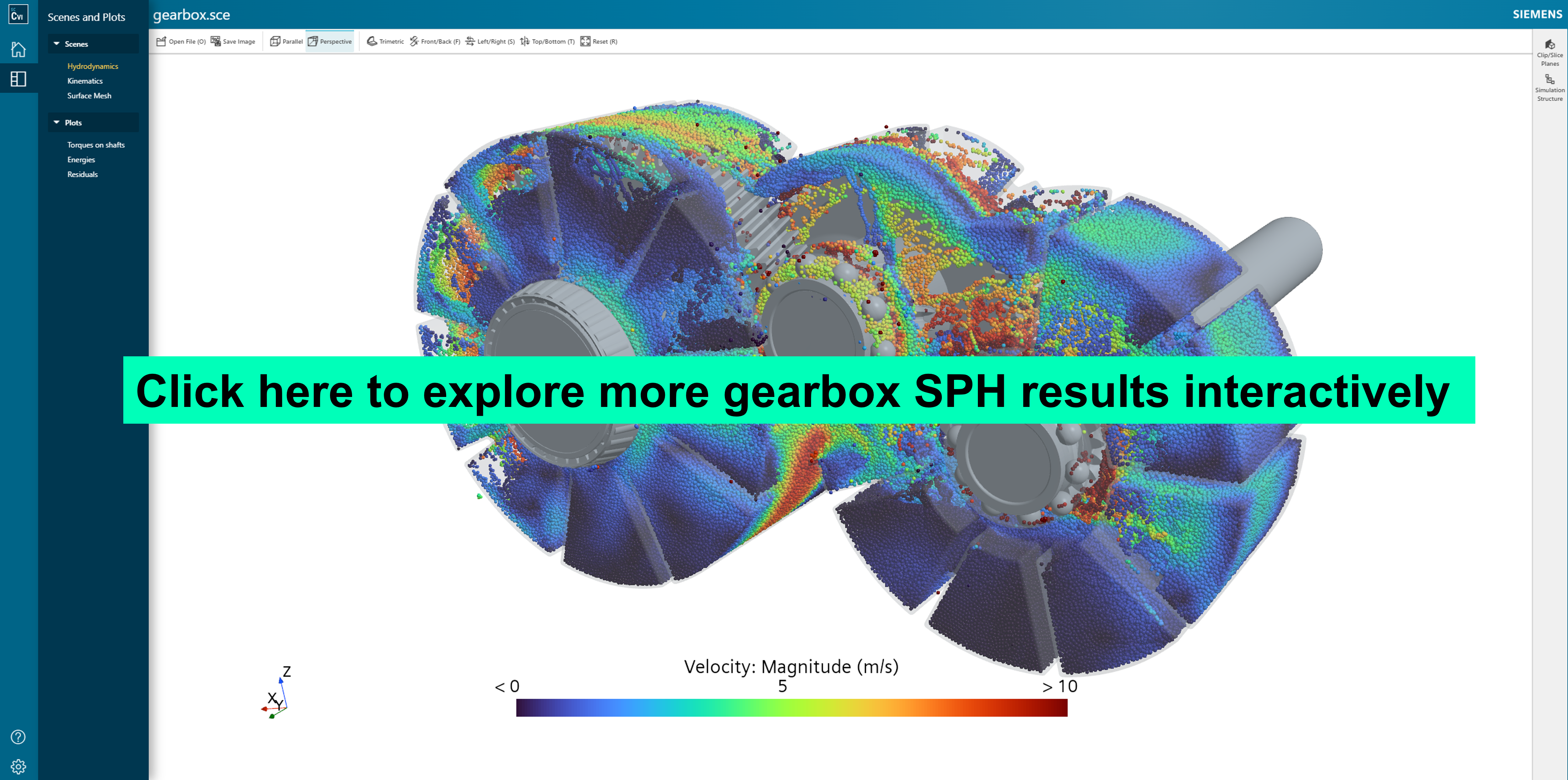
Faster than ever
Regarding performance, SPH in Simcenter STAR-CCM+ version 2402 enables you to run a gearbox simulation with 0.5 Mio particles in approximately an hour on 8 CPUs. Running the same job on 64 CPUs you can even study a gearbox in an impressive runtime of only 12 minutes, demonstrating the excellent scalability of the solver. Adding the fact that the preparation time almost vanishes with SPH this enables rapid CFD-driven insights.
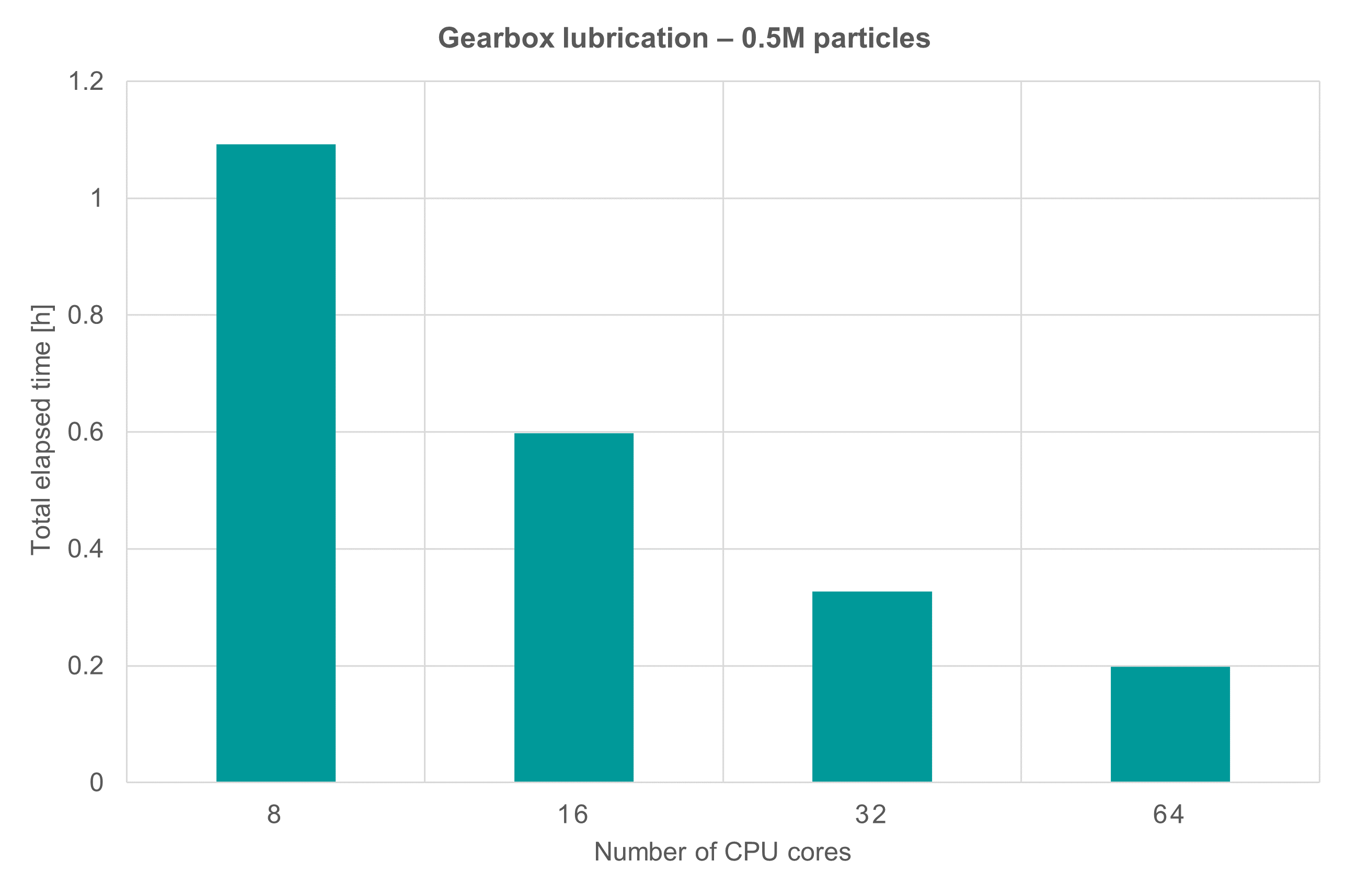
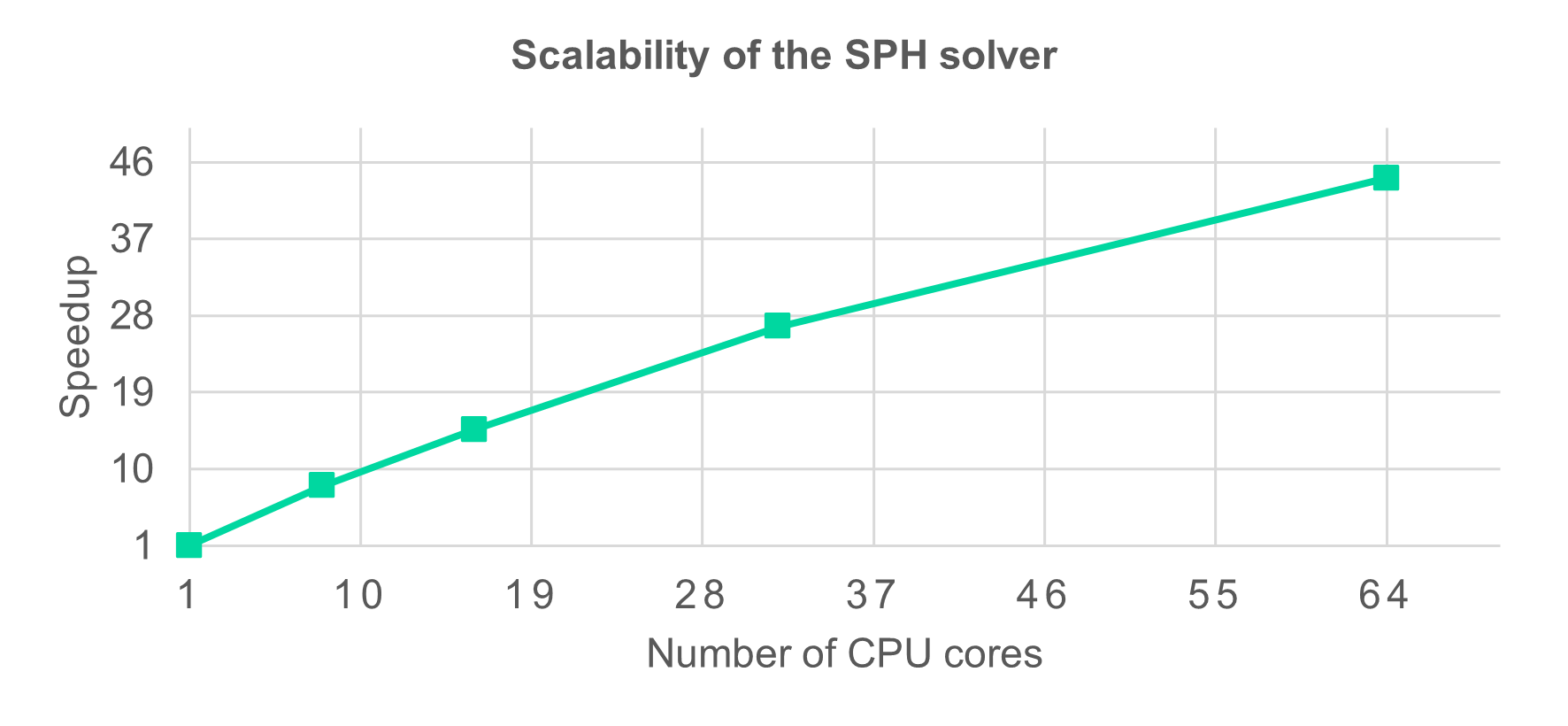
Optimize your gearbox design with SPH meshless method
Coming back to powertrain design’s main challenges, using the cutting-edge SPH technology in Simcenter STAR-CCM+ version 2402 allows you to easily check if the oil gets into critical locations and minimize churning losses. The SPH add-on license enables you to faster simulate and analyze sophisticated CFD simulations earlier in the development cycle.
Thanks to the streamlined workflow, you’ll be able to select the optimum design and conditions with the Design Manager. Moreover, you have the possibility to run additional in-depth simulations with the FEA solver or VOF liquid/ air computations, staying integrated in one single-user environment.
How does it compare…
For gearbox lubrication applications, we compared both finite-volume and SPH methods in terms of setup engineering time.
If we look at the engineering time needed to make the simulation setup, it is undeniable that the SPH workflow is faster than for finite-volume. Simply, because with the SPH meshless technology, you can skip the volume meshing step and you do not have to go through overset or other complex techniques to set up the rotation speed of each of the gears. In some cases, setting up the volume mesh and the motion can take up to a couple of weeks for a complex industrial gearbox. For an SPH computation, you just simply get rid of that complex step.
With SPH, you quickly get a low-fidelity, yet plausible solution to your most complex applications. With finite-volume methods, for a first solution, you would usually need to go back to your setup and do a bit of tuning to the mesh and/ or the numerical settings to get a first low-fidelity solution.
The SPH meshless technology comes as complementary to other existing finite-volume multiphase models to overcome meshing-related constraints.
SPH is the ideal solver for design exploration to eliminate quickly and effortlessly low-performance design. Now, if you need to model the influence of the air or if you need to model phase change or other complex phenomena such as electromagnetics, you must use finite-volume methods. It all depends on the scope of your applications and the required level of fidelity to make that choice.
So, to mesh or not to mesh, is there really a choice to make?
So, to mesh or not to mesh, this is still the question… and the truth is that it indeed remains difficult to answer as was the original quote from Hamlet. Today, both mesh-based and meshless methods are essential in the CFD world. Both methods are complementary and remain fundamental for your most complex multiphase simulations. Mesh-based and meshless technologies still have a bright future ahead of them.
The choice of one over the other depends heavily on the scope of your project and its objectives. Required accuracy versus desired turnaround time will always remain a project-specific question that engineers must answer in the most efficient way. But unlike before, you now have one integrated CFD tool to cater to them all, one single-user environment, and one single workflow for all your different multiphase applications. You can run in the same user interface Volume Of Fluid (VOF) or Discrete Element Method (DEM) or… SPH simulations! The question “to mesh or not to mesh” becomes more of a best practice choice rather than an a priori costly (multi) CFD tool investment decision.
And so, with Simcenter STAR-CCM+ version 2402, the 21st-century CFD engineer Hamlet can rest assured:
To mesh or not to mesh, that is not a real question anymore.