The evolving role of simulation in the pharmaceutical industry
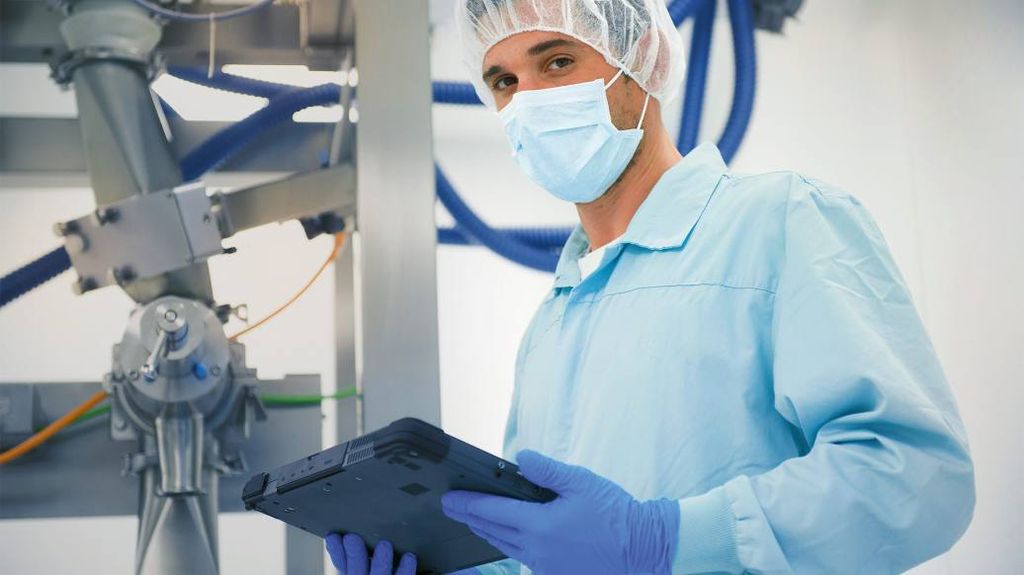
The pharmaceutical industry is no stranger to adapting to constantly changing pressures, both on a plant and industry-wide scale. Failure to see these challenges in advance and react can cause costs to soar and allow competitors to claim an advantage. Now, what role does accurate predictions (or modeling) play for companies in the pharmaceutical industry? Let us explore this idea further-
Shifting from conventional approaches to process design & technology transfer
Process design and tech transfer in the pharmaceutical industry has traditionally been very conservative – and perhaps with good reason. There are stringent regulations for product and processing standards, with the cost of new development extremely high. Companies have a lot to lose and so often revert to ‘tried and trusted’ empirical methods of experimentation and scale-up. However, these may not be the most efficient approaches and can lead to slower drug development or sub-optimal processes.
With the rise in advanced computing capabilities, simulation tools and platforms have become an increasingly viable solution to model complex pharmaceutical processes and gain real-time insights. There are a few important imperatives for such tools to be successfully deployed in any pharmaceutical company:
Digital design of products and processes: A comprehensive digital twin would be a boon to the pharmaceutical industry, facilitating confident process scale-up, optimized equipment design and operation and faster time-to-market.
Knowledge-driven recipe transformation: A holistic approach to design and scale-up of recipes from lab to clinical trials and commercial manufacturing is facilitated with an ISA-88 guided enterprise recipe management (ERM) approach.
Manufacturability verification & optimization: Process optimization can be driven by reducing use of raw materials and ensuring optimum equipment usage, increasing the robustness, cost efficiency and sustainability of commercial production.
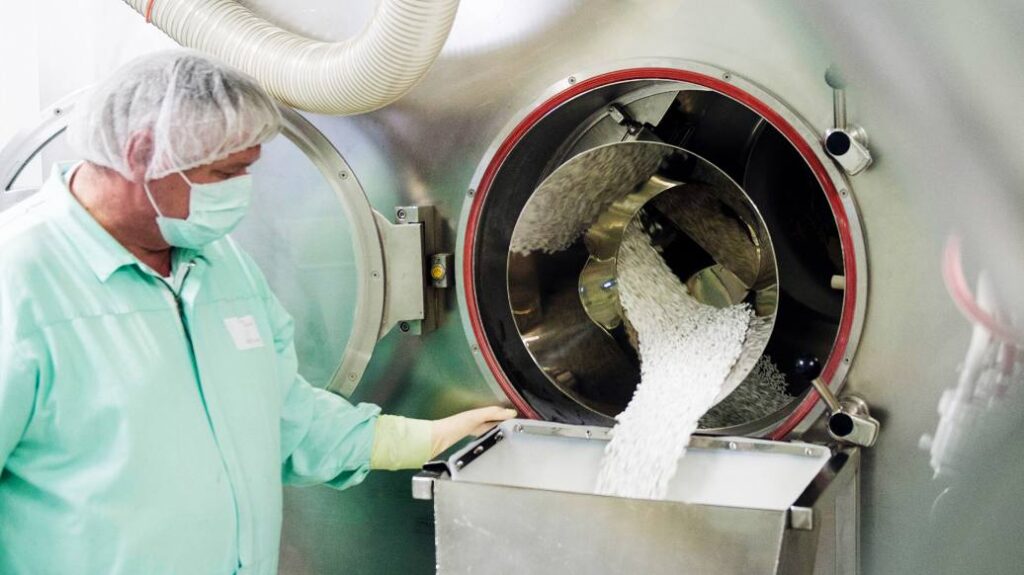
Leveraging the complexity in pharmaceutical processes as a competitive advantage
Physicist Werner Heisenberg allegedly once said, “When I meet God, I’m going to ask him two questions: Why relativity? And why turbulence? I really believe he’ll have an answer for the first.” Perhaps fictional, the quote nonetheless captures the sentiments of many engineers and students when trying to model turbulence due to the complexity of the flows and sometimes unpredictable behavior.
Unfortunately for those in pharmaceutical manufacturing, turbulence is not the only antagonist to consider; particles, non-Newtonian fluids and multiphase systems often coexist together in a potpourri of all the scary physics young engineers learn about at university. Failure to accurately understand the behavior of such systems can lead to increased physical experimentation or a sub-optimally designed system.
Complexity is inherent in many pharmaceutical processes – there is no escaping it. In order to be successful, companies must understand the complexity and leverage it as a competitive advantage. This is already underway; with industry incentives such as Quality by Design (QbD), and concepts such as Industry 4.0, companies are starting to explore new methods to gain the advantage of digital transformation in an increasingly competitive market.
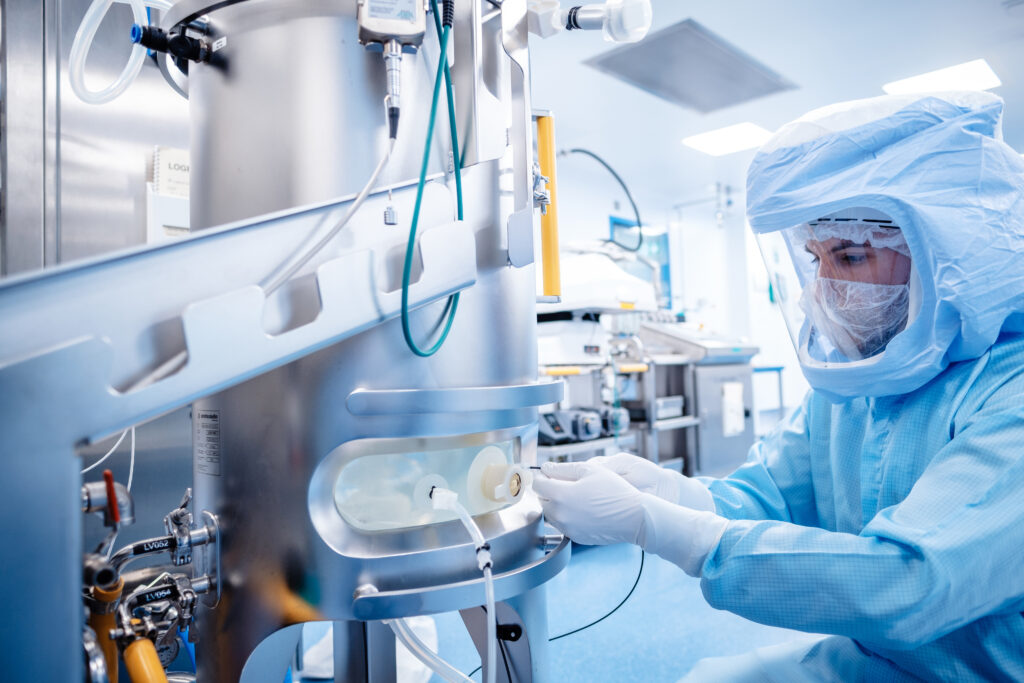
In digitalization, we trust
While the traditional empirical methods of experimentation, scale-up and tech transfer are not altogether redundant in the pharmaceutical industry, they cannot provide that same cutting-edge innovation and competitive advantage which the move towards digitalization can. For example, artificial intelligence software in design optimization can quickly generate novel and optimized designs which can outperform human designs. Companies who do not leverage modern solutions to industry challenges risk getting left behind.
The Simcenter suite offers unrivalled, best-in-class physics capabilities to meet the complex demands of pharmaceutical manufacturing. gPROMS provides a mechanistic and hybrid process modeling environment for configuration, calibration and deployment of digital twins. It is typically used by subject matter and modeling experts who calibrate the models on a per unit operation basis. These models can subsequently be used for optimal design and operation & sensitivity analysis to identify and mitigate robustness issues.
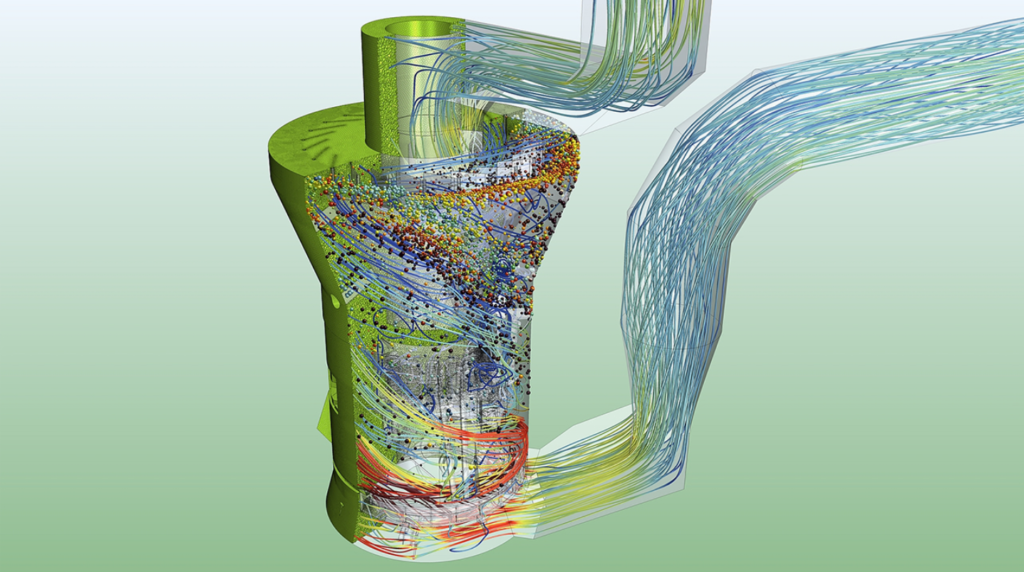
With Simcenter STAR-CCM+, CFD engineers can leverage its Multiphysics CFD software to accurately capture the relevant physics that influences the performance of increasingly sophisticated products or equipment. The modeling capabilities go beyond fluid flow and heat transfer to include single and multiphase flows, particle dynamics, reactive flows, fluids-structure interaction, aeroacoustics, rheology and electrodynamics modeling. These capabilities help in the analysis of thousands of design tradeoffs to arrive at the optimum state, while realizing significant cost savings.
Coupling the advanced process modeling environment of gPROMS with the 3D CFD simulation of Simcenter STAR-CCM+ enables a uniquely complementary approach for accurate modeling of complex chemical processes with practical simulation time. This can help realize a virtual representation of product and process: an executable digital twin that helps accelerate recipe development, foster collaboration through digital technologies and enhance drug manufacturability.
Summing up…
The shift towards digitalization is already happening. Some virtual methodologies have even been used to entirely validate a process for FDA inspection. This saves companies time, money and improves efficiency. With Simcenter and gPROMS, tools to enhance processes are now readily accessible and have been shown to provide benefits to the pharmaceutical industry. Now is the time to be proactive and embrace the complexity of processes and the benefits which digitalization can bring.
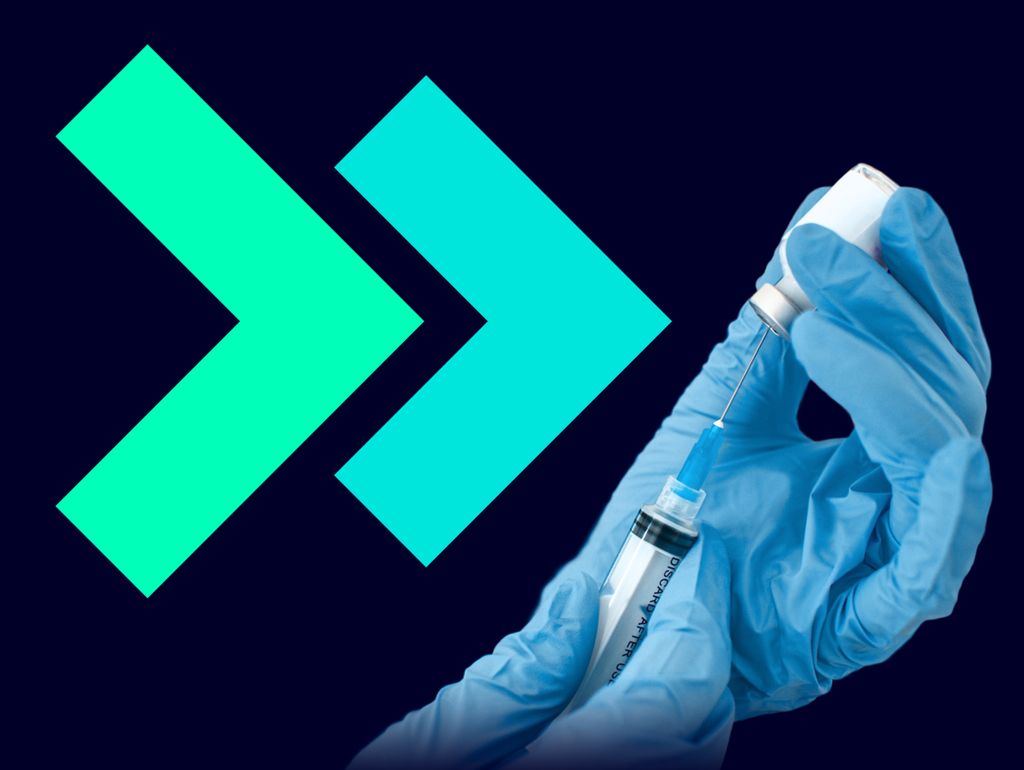
A unified solution from drug discovery to full-scale production
Simcenter and gPROMS offers the complete suite of tools to help manufacturers and companies in the pharmaceutical industry to turn the complexity of the shifting industry landscape into a competitive advantage. By combining these tools in an open data-transfer system, pharmaceutical companies are enabled to rapidly design a robust manufacturing process that can efficiently scale-up from lab to production.
To discover how simulation and digital twin technology can and already has been used in the pharmaceutical industry, check out the white paper Simulation in the pharmaceutical industry: Assessing the role of physics-based simulation in realizing a comprehensive digital twin in the link below.