Simulate Bevel Gears Accurately and Efficiently
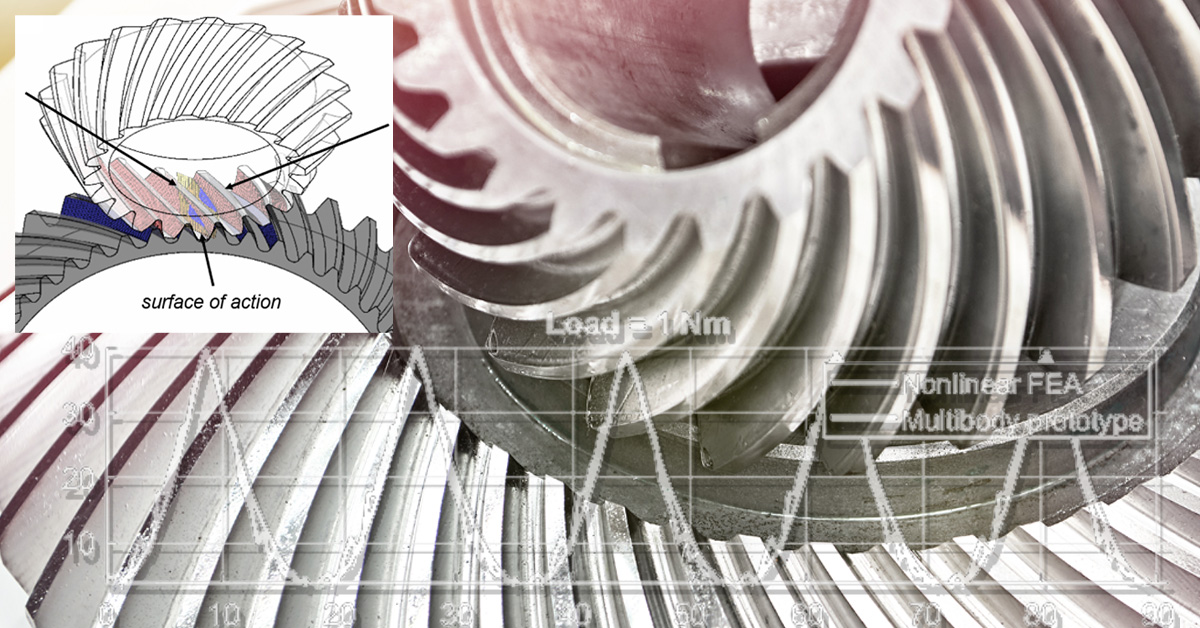
Gears are crucial components in mechanical transmissions and products, essential to transfer energy between different axes of rotation, to change rotation speed, and to distribute energy across mechanisms.
When we think of gears, we might first think of planar gears: rotating disks with teeth on the sides, connecting to other gears to transfer rotational energy via the rotational axes that they connect to. In real life, planar gears are not always suitable, as they cannot transfer rotational energy to an axis that rotates in a direction out of plane.
Challenge: the need for optimal gears that can transfer energy out of plane
Many engineering applications require the transfer of rotational energy between axes of rotations that lie out of plane. A well-known example is the differential in automotive applications. The drive shaft connects the engine to a differential, which then transfers the mechanical energy to the vehicle’s axle shafts. This puts the wheels into motion, such that the car can drive.
Many of us can visualize this by thinking back to a Lego Technic differential, which had to be built with various types of gears to transfer the rotational energy. Here, the gears that take care of the energy transfer out of plane, are called bevel gears because of their conical (beveled) shape. Bevel gears are not only crucial in the automotive sector but are also used intensively in many other sectors. For instance, bevel gears enable both driving and functional operations in off-highway vehicles, are found in marine transmissions and are key components in presses and conveyor belts in factories. In aviation, they are used in the transmission of jet engines and are crucial in the main-rotor and tail-rotor gearboxes of helicopters.
Bevel gears have a conical shape, connecting where the two shafts intersect, with the tooth-bearing faces connecting and able to transmit mechanical power between one intersecting shaft and the other. In the example of the automotive differential, the shaft angle is often 90 degrees, but alternative angles are possible. It is recognized that the share of 4-wheel drives is increasing, but today, many (electric) cars still have 1 or 2 motors to drive the 4 wheels, thus requiring bevel gears to transfer energy in a differential [1].
Unfortunately, the virtual design engineering of bevel gears has long been challenging. Figure 1 shows that bevel gears have a much higher complexity than planar gears. Bevel gears have a highly complex tooth geometry, which results in a much more challenging contact detection problem. This means that traditional modeling and simulation approaches are not suited for bevel gears. On the one hand, you cannot predict the dynamics and load transfer with a simplified contact, and on the other hand, a general surface-to-surface contact detection requiring excessive CPU costs.
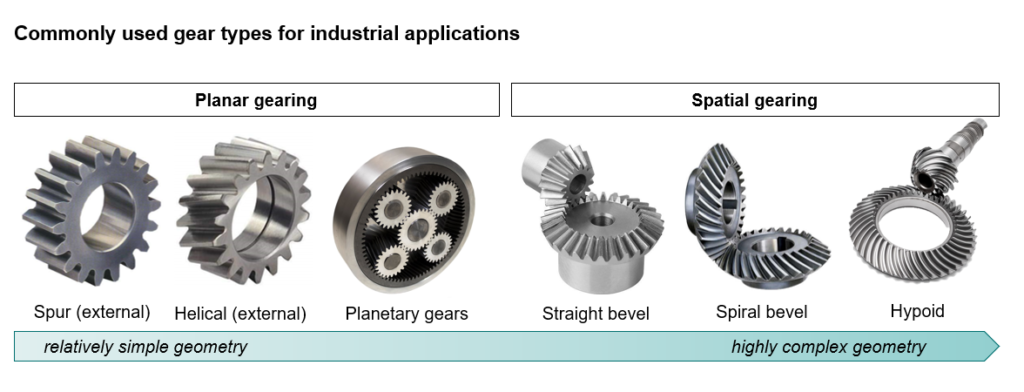
A new contact element for bevel gears simulation
This article presents a new contact method [2] for bevel gears in multi-body simulations, which provides the required accuracy in an efficient way. The new contact method has been implemented as a new contact element in Simcenter 3D, where it equips the multi-body solver [3] with the capability to analyze both straight and spiral bevel gears, and subsequently optimize them. Acoustics simulation can also be done [4] to evaluate bevel gears as a source of excitation, and as a transfer path for noise and vibration.
The recipe for achieving both efficiency and accuracy with the new contact element for bevel gears is visualized in Figure 2. The generalization of the line-of-action approach in cylindrical gears is what enables the new element to be both efficient and accurate [2]. The new element is numerically efficient and generally applicable to gear contact problems (near-conjugate). It adopts flank penetration to determine the instantaneous contact locations between the meshing gear tooth flanks. Three different types of contact force models can be included in the element: an analytical stiffness gear contact force model, a viscous damping gear contact force model, and a Coulomb-based friction force model.
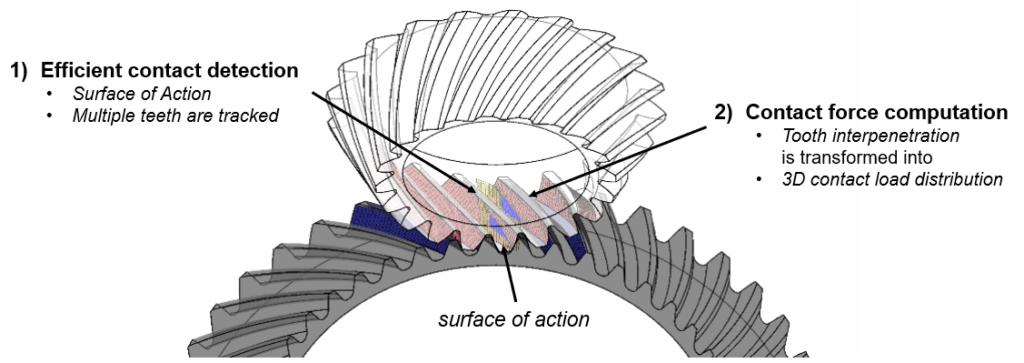
Results: Accurate and Efficient Simulation of Bevel Gears
Both straight and spiral bevel gears are essential components for power transmission between intersecting rotating shafts. They form the two main use cases for the new contact detection element for bevel gears that have been developed:
- Straight bevel gears: the gear teeth are cut straight along the pitch cone.
- Spiral bevel gears: the gear teeth have a spiral shape, cut at an angle, and curved along their length.
As shown in Figure 3, the correctness of the new contact detection element for bevel gears has been validated w.r.t. a (static) nonlinear FE model of the gear pair [5]. This confirms the accuracy of the new element. Most importantly, for typical applications, the bevel gear contact simulation is multiple orders faster in terms of computational efficiency than comparable methods that provide the same accuracy. The new bevel contact detection algorithm thus enables the accurate and efficient simulation of bevel gear dynamics.
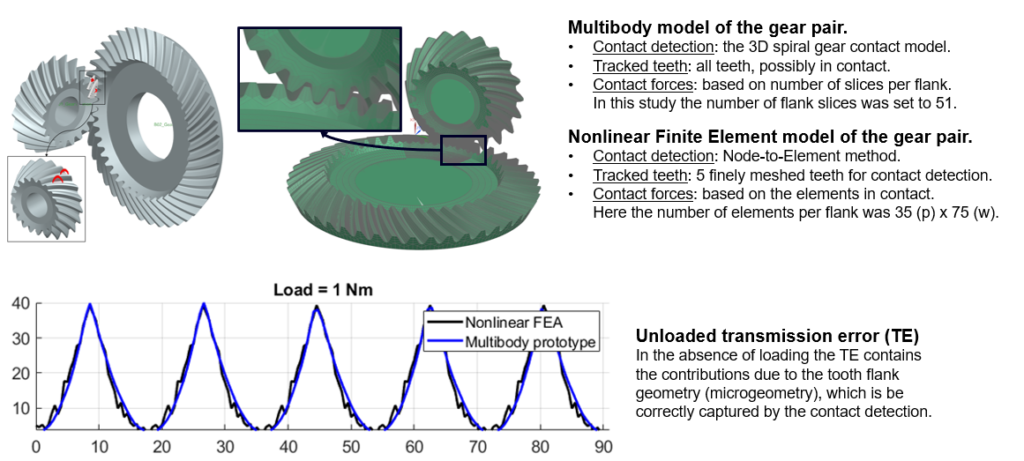
Simcenter 3D is a comprehensive, fully integrated CAE solution for complex, multidisciplinary product performance engineering. Thanks to the addition of the new gear contact element for bevel gears, Simcenter 3D Motion is now equipped to accurately and efficiently simulate the dynamic behavior of multibody transmission models that include straight and spiral bevel gears. Equipped with these novel multibody simulation capabilities, design engineers of gearboxes and transmissions can now more accurately simulate and optimize their designs by evaluating and analyzing the NVH characteristics as well as the durability performance, while directly considering the nonlinear dynamics of their products.
Figure 4 shows the use of the new gear contact element for straight bevel gears in a study on the effect of friction in a straight bevel gear pair, which can be part of an automotive differential gearbox. Only a single straight bevel gear pair was modeled in this analysis to study how transmission error can change when contact friction effects are accounted for. Besides an evaluation of this effect, the gear contact forces, which act on the meshing straight bevel gear teeth, can also be post-processed and analyzed using dedicated functionality. This enables Simcenter 3D Motion to provide transmission engineers with detailed insights to further improve their transmission and gearbox models (e.g. via a correct design of the gear tooth flank microgeometry).
Acknowledgements
An Innovation Mandate (IM) project, funded by VLAIO (Flemish government agency Flanders Innovation & Entrepreneurship), provides support to postdoctoral researchers to achieve an effective transfer of knowledge and valorization of their research, thus bridging the gap between academia and industry.
The R&D work leading to this publication has been performed in the frame of the IM Project “Advanced techniques for system-level simulation of Hypoid and bevel gEAr Dynamics” (“AHEAD”), conducted by Dr. Mathijs Vivet, with industrial partner Siemens Digital Industries Software and academic research partner KU Leuven, project nr. HBC.2019.2177, from 01/09/2019 – 31/08-2022.
References
- Jonas Verhoogen and Jonathan Melvin, “Bevel gears whine no longer due to unseen pressure”, Simcenter Blogpost, January 5, 2022.
- Mathijs Vivet, Alessandro Libralato, Jonas Verhoogen, Pavel Jiránek and Tommaso Tamarozzi, “Advanced modelling of straight bevel gear contact for multibody simulations”, Proceedings of ISMA Conference 2022, Leuven, Belgium, September 12-14, 2022.
- Siemens Digital Industries Software, “Simcenter 3D Motion Simulation”, Retrieved 2022.
- Siemens Digital Industries Software, “Simcenter 3D Acoustics Simulation”, Retrieved 2022.
- Siemens Digital Industries Software, “Simcenter 3D Structural Analysis”, Retrieved 2022.