SimRod experience: Mode shapes in modal analysis need test-calibration
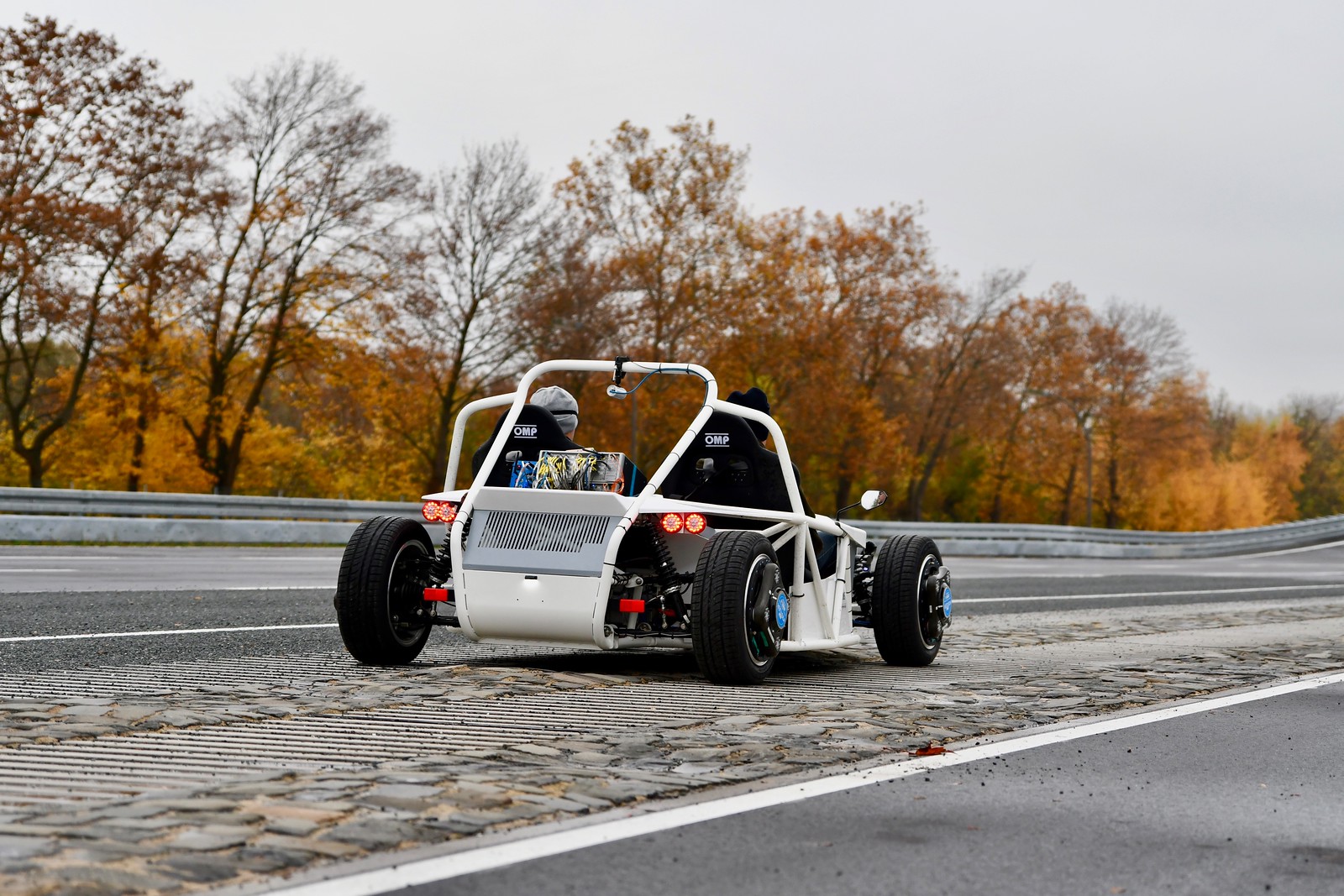
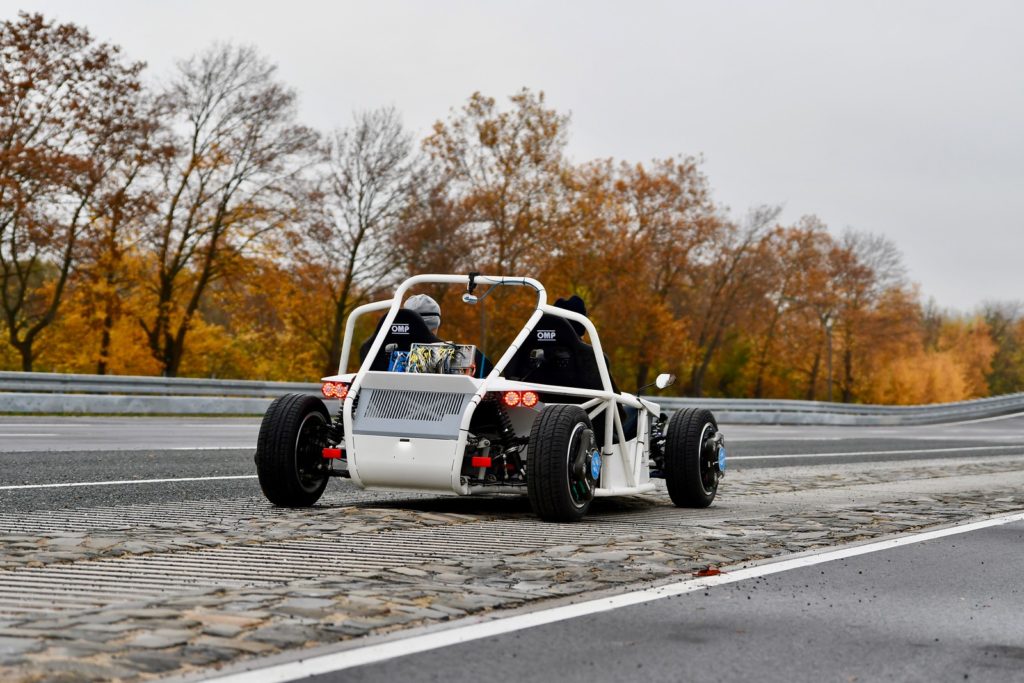
Ever heard of “Range anxiety”? The Wikipedia definition of this new term is “fear that a vehicle has insufficient range to reach its destination and would thus strand the vehicle’s occupants.” The battle is on: car manufacturers all over the world are looking for ways to increase the range of their vehicles. Obviously, a lot of effort is spent on optimizing the drivetrain. But this is just one of the many battlefronts. Learn more how mode shapes in modal analysis can be your collaborative partners.
Put your car body on a diet!
Another important factor is total vehicle weight, aka curb weight. Consequently, lightweight body design is high on the priority list. But weight also plays a crucial role in other performance characteristics of the vehicle. A lighter design may cause unacceptable NVH or driving dynamics performance. It’s all a matter of finding the right balance. The Simcenter solutions help you to find that balance, combining performance prediction and testing tools in one and the same platform.
Don’t accept extra range in exchange for driving fun. Go for both!
The key capability in the Simcenter performance prediction is to create a reliable structural dynamics model of a vehicle body. To make sure that this model represent reality, Simcenter provides you with an end-to-end process. This includes running structural dynamic tests, aka modal test, to derive test-based mode shapes in modal analysis, and an extensive set of methods that can be used to correlate and update the Finite Element structural dynamics model.
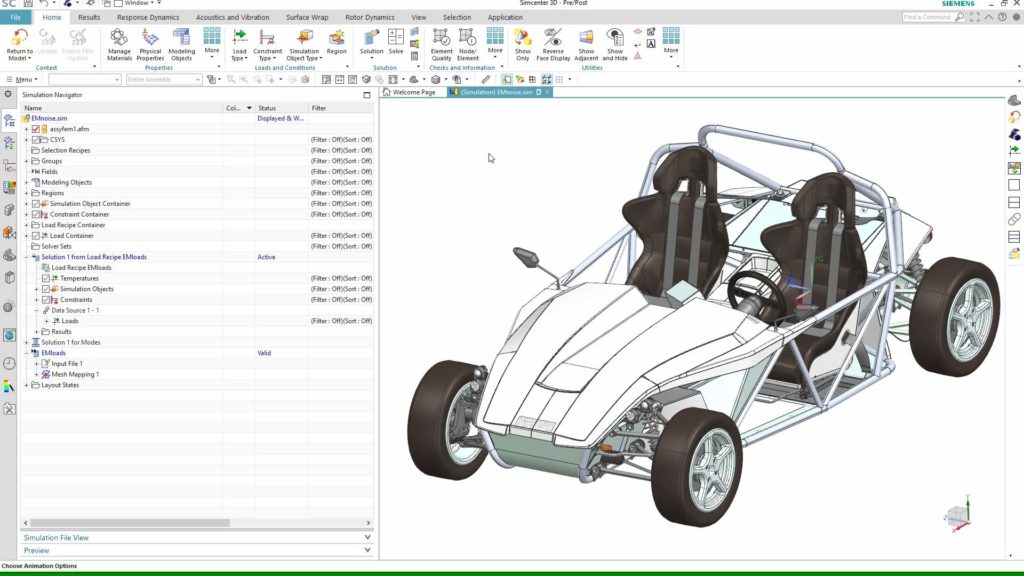
What does this look like in reality?
Let’s look at a practical example: the SimRod, a full electric sports car. It is made by KYBURZ, an electric vehicle manufacturer in Switzerland. KYBURZ’s core business is making small electric vehicles with minimal ecological footprint. To showcase our Simcenter solutions, we bought a couple of these electric sports cars.
The SimRod “Body”
Our SimRod vehicle is a bit special: the body is a frame structure. It consists of a set of welded beams. The beams are made of S235JR steel, a European standard hot rolled non-alloy structural steel grade. It features good plasticity, toughness and weldability. The material density is 7.85 g/cm3, bringing the total frame weight to 96 kg, which is about 16 % of the total weight of the vehicle. Definitely a large fraction to consider saving a couple of kilos. And by doing so, adding a couple more kilometers of driving fun!
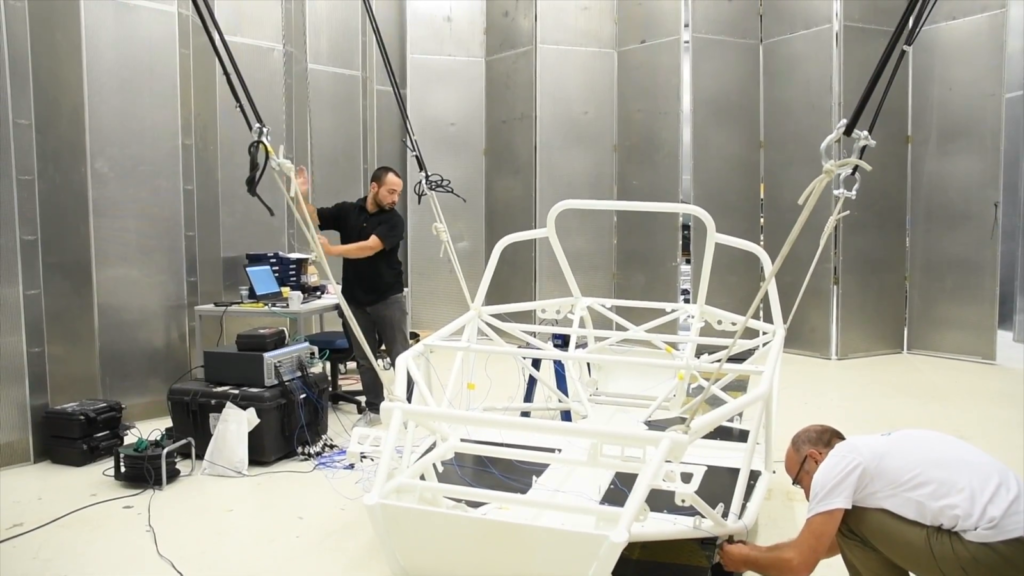
Test vs. Simulation
An anonymous researcher once stated: “Nobody believes the result of a simulation, except the person who performed it, and everybody believes the result of a test, except the one who ran the test.” This old proverb used to be very true, back in the days, when simulation and test were two totally different worlds. The Simcenter platform is designed to remove the boundary between these two worlds and aims to create a test-calibrated simulation model that EVERYBODY believes, simply because it is correct.
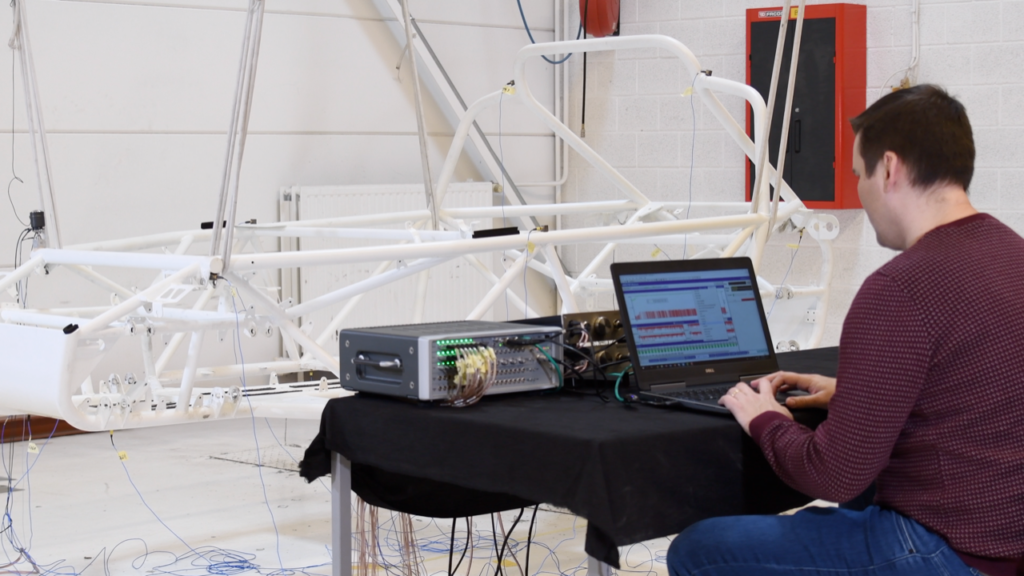
On your mark, get set, go!
Prior to the testing, CAE engineers usually do some NX Nastran runs to estimate the mode shapes. Although these models have limited fidelity, they are useful in early development phases, as they can help making design decisions. This process is much faster and more cost-effective than iterations that involve building prototypes. To close the loop and make everyone believe the prediction, test-calibration is required. Simcenter 3D Structural dynamics uses the preliminary Finite Element model to define the optimal set-up. The analysis helps to define the test wireframe geometry, shaker locations and interface conditions. It also provides a preview of the expected mode shapes in modal analysis. A good preparation is key to successful and efficient test campaign!
Simcenter Experimental Modal Analysis – industrial productivity
Testing is expensive. That’s why Simcenter testing solutions is also designed to minimize test time. For example: to ensure validity of the setup, a tablet-based Instrumentation app helps to detect and correct potential instrumentation errors. The actual experimental modal test itself consist of suspending the structure in bungees and excite it with a number of simultaneously running shakers. During this excitation, the input forces and resulting accelerations are measured to calculate Frequency Response Functions. If you have ever done such a test, you will agree: it is not easy to ensure that the shakers are properly positioned and the stingers are well-aligned. The Siemens answer to this: self-aligning Simcenter Qsources shakers, which can be mounted directly on the relevant excitation locations.
Traditional shaker setup with stinger Time-saving, self-aligning Qsources shaker
Unrivalled Modal parameter estimator: Simcenter Testlab Polymax
Once all data is acquired, modal analysis can start. Within Simcenter Testlab, a model is fit over the measured FRFs, using the well-established Polymax algorithm. The different modes are selected from the Stabilization diagram, either manually or automatically. For highly damped and complex structures, such as trimmed bodies, more advanced algorithms, such as MLMM are crucial. MLMM stands for “maximum likelihood modal model” and iteratively improves the modal model, while at the same time preparing for better correlation with the CAE model.
Final step: make everybody believe that the simulated mode shapes in modal analysis are accurate
The results are now ready to be accessed in Simcenter 3D, where they can be used for comparison of numerical modes, as well as to update the CAE mode. This model will serve to make further optimizations. With this true digital twin, it now becomes possible to find the right balance between different performance attributes.
Are you interested to learn more about modal analysis process?
Here is a webinar explaining this technology step-by-step.