Simple and fast access to strength and durability insights
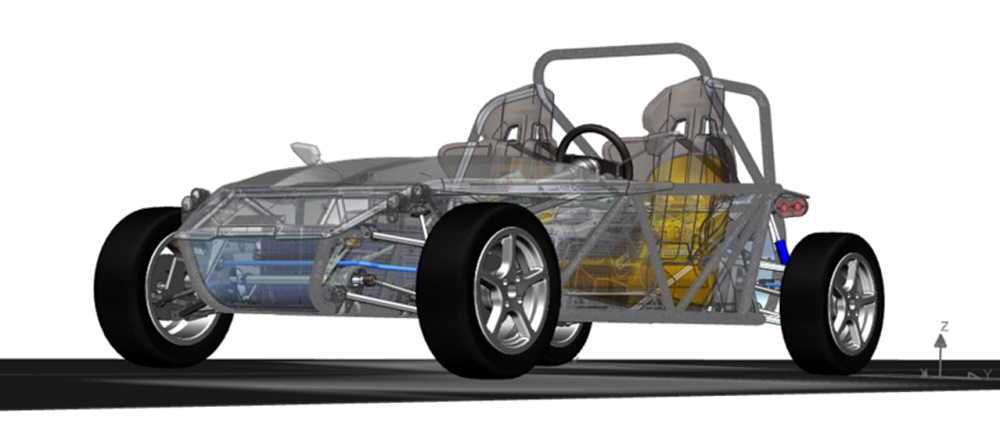
Durability performance will always remain one of the most critical design criteria, related to very fundamental product and brand values. In this blog post, we explain why combining test and simulation is the best way to optimize and validate products for this aspect. And we describe how Simcenter 3D Specialist Durability can help engineering teams gain maximum durability insights from their simulations using a dedicated step-by-step postprocessing approach.
Costly durability testing
A durability testing campaign requires the availability of expensive hardware resources and is very labor-intensive. Besides, it must usually take place when there is little time left, or when any time which is spent will cost a lot of money. For example, when companies approach the moment of product sign-off, a test that is poorly thought through can have dramatic consequences for the release. Also, if during production, samples need to be tested on their durability performance, it is very important to have an efficient scenario.
Durability insights for complex structures
This is definitely the case for complex structures, such as a car for example, of which we can expect that they will experience an enormous amount and variety of load situations (duty cycles) during their operational life. Simply blindly starting to test all those scenarios to the full would be complex, very expensive, and would take forever. And most of the work would be useless anyway. Analyzing forces on the entire system does not say anything about the impact those have on individual components.
That is why upfront durability insights are key. With simulation, you can setup scenarios to do local analysis and discover which load events are important for which location. Then you can understand which loads specifically cause problems, and why. By using simulation in this way, you can give guidance to testing teams, so that they can achieve enormous efficiency gains by applying more targeted testing scenarios. Or of course, you can simply immediately use these durability simulation results to improve your design with structural adjustments.
Unique combination of durability test and simulation expertise
At Siemens, we understand better than anyone how to achieve synergies by combining test and simulation, as with Simcenter, we offer the only platform on the market that combines both worlds. So, we know all the challenges test teams have to deal with, and we can respond to them.
Our CAE solution Simcenter 3D Specialist Durability gives engineers access to state-of-the art fatigue analysis methods that enable them to perform fatigue life prediction analyses quickly and accurately, accounting for realistic loading conditions. Besides, the software includes a set of postprocessing capabilities that specifically aim at providing immediate answers to the most important questions via a clear workflow. Those include, when does damage occur? During which event? Where does the damage then take place? And why?
Gaining durability insights through step-by-step post-processing
The very first thing to do after a simulation is, obviously, to check whether the results are meaningful at all. After setting up and running the durability simulation analysis case, engineers have access to a comprehensive overview of all possible results in the results table. Any obvious mistakes in the setup, such as, for example, using a wrong unit system, will be visible here.
Once it is clear the analysis was fine, further post-processing can begin. Typically, by following the steps in figure 1, you can most effectively obtain durability insights. Simcenter 3D Durability Specialist has specific tools for each step.
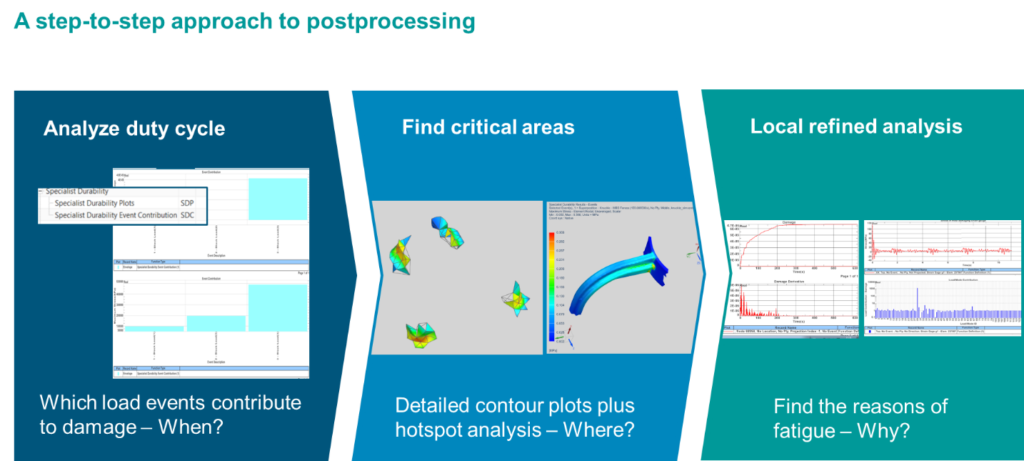
First, analyze the events
Very often, a durability analysis consists of a huge amount of possible load events – a duty cycle. So, finding exactly those events that are actually causing fatigue problems, can be challenging. Especially trying to do so by manually clicking through them, is almost impossible. Therefore Simcenter 3D Durability Specialist has dedicated tools to analyze the contribution of each event. This can be either at critical locations, at a user-defined position, or for a component or a group of components. This contribution can be processed for all possible durability results, including damage, lifetime, stress amplitudes, safety factors, and more.
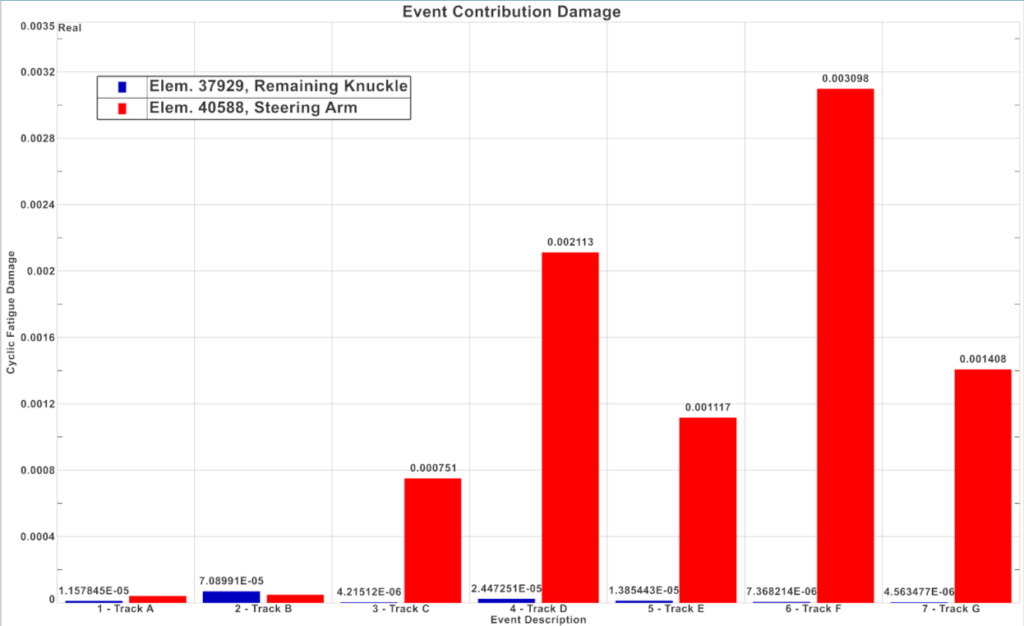
In this way, Simcenter 3D Specialist Durability provides engineers with very quick insight into which events apply damage where, which is a necessary starting point for efficient further analysis.
Second, analyze the component
The next step is to use this information to postprocess any results type on event level. This spans a huge number of postprocessing activities, ranging from getting an overview of stresses, strains, temperatures, and strength analyses like static failure, to detailed life and damage analyses. All these capabilities can be found in the Simcenter 3D Durability Specialist postprocessor. They will help engineers detect critical areas faster.
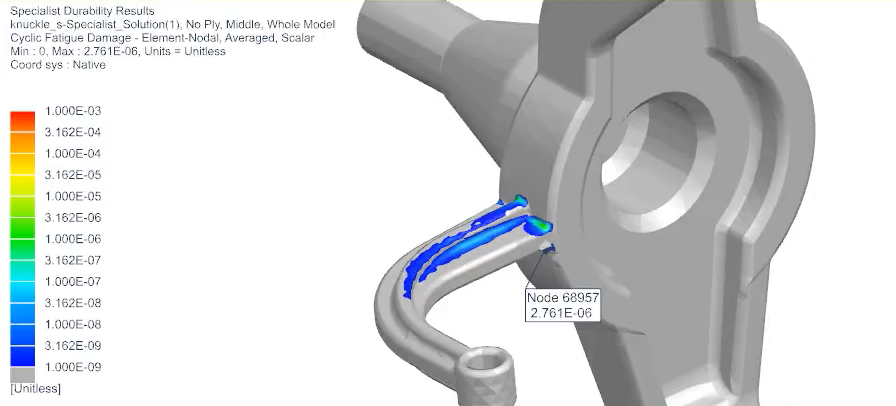
Third, gain local durability insights
And finally, it is important to understand the mechanism behind failure. Why does damage occur? For a better understanding, the engineer can analyze the critical areas in more detail. A good example is turbomachinery, where engineers need to understand early whether high stresses and high temperatures occur simultaneously. To that end, they look at so-called peanut plots, which show the relation between the different parameters and help them deeply understand the local behavior. With Simcenter 3D Specialist Durability, engineers can create such a plot for any location (node, element, direction). It can include data types like elastic/plastic stress/strain, temperature, and damage.
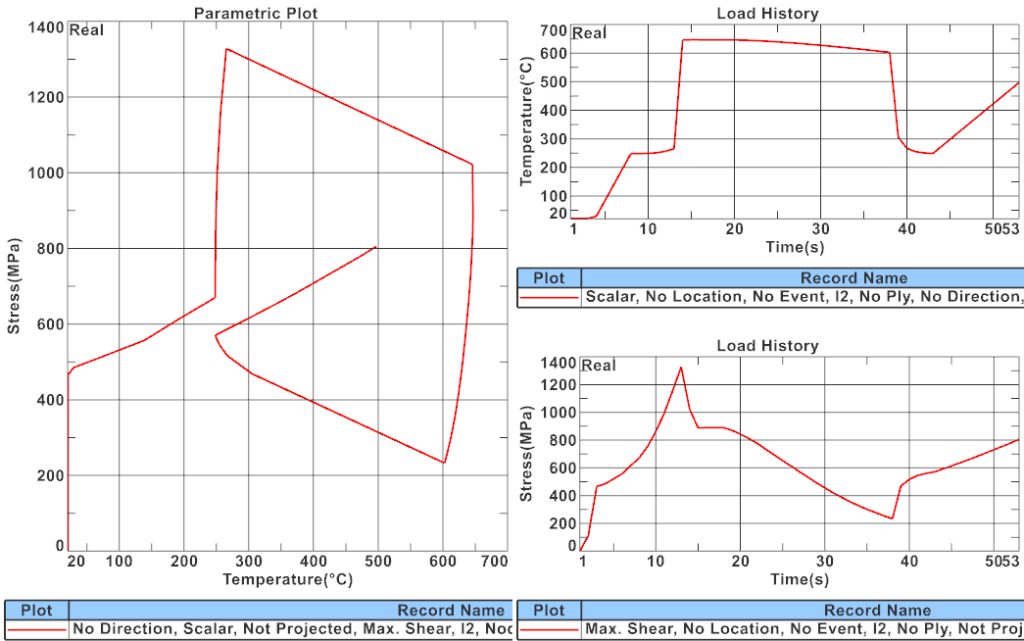
Below are some other examples of interesting plots in Simcenter 3D Specialist Durability that are very suitable to gain quick durability insights.
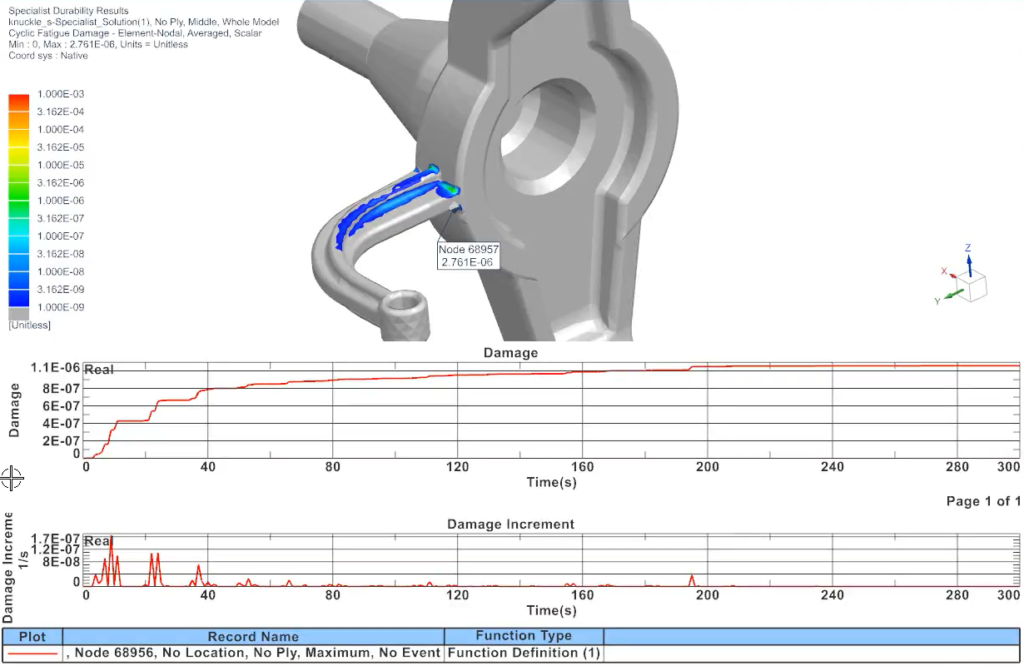
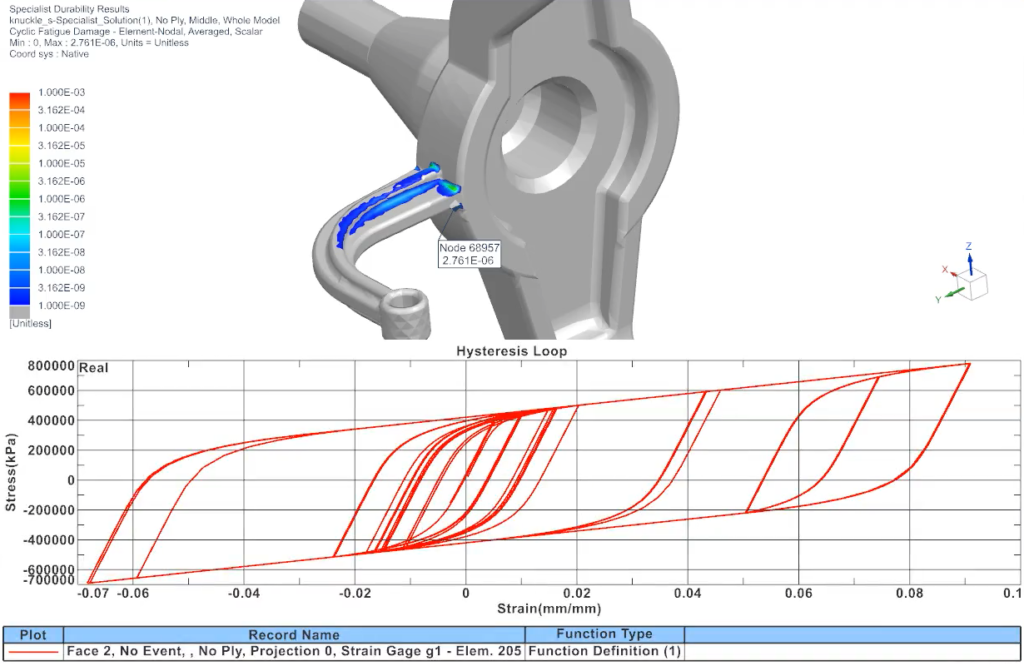
Conclusion
The Simcenter3D Specialist Durability simulation solution includes all the necessary postprocessing tools to help engineers gain deep durability insights. By following a step-by-step approach, they can find quick answers to important questions, like:
- During which event would eventual strength or durability problems take place?
- Where would it happen?
- What is the mechanism behind the failure?
This will help engineering teams save a lot of time and money, by:
- Avoiding testing time is spent on components that are not “test-worthy”
- Better defining efficient testing scenarios
- Providing the necessary insight to improve the structure for better durability performance
All these postprocessing capabilities are available in Simcenter 3D 2022.1 to help engineers design durable products.