Simcenter Additive Manufacturing – A Robust Compensation Workflow
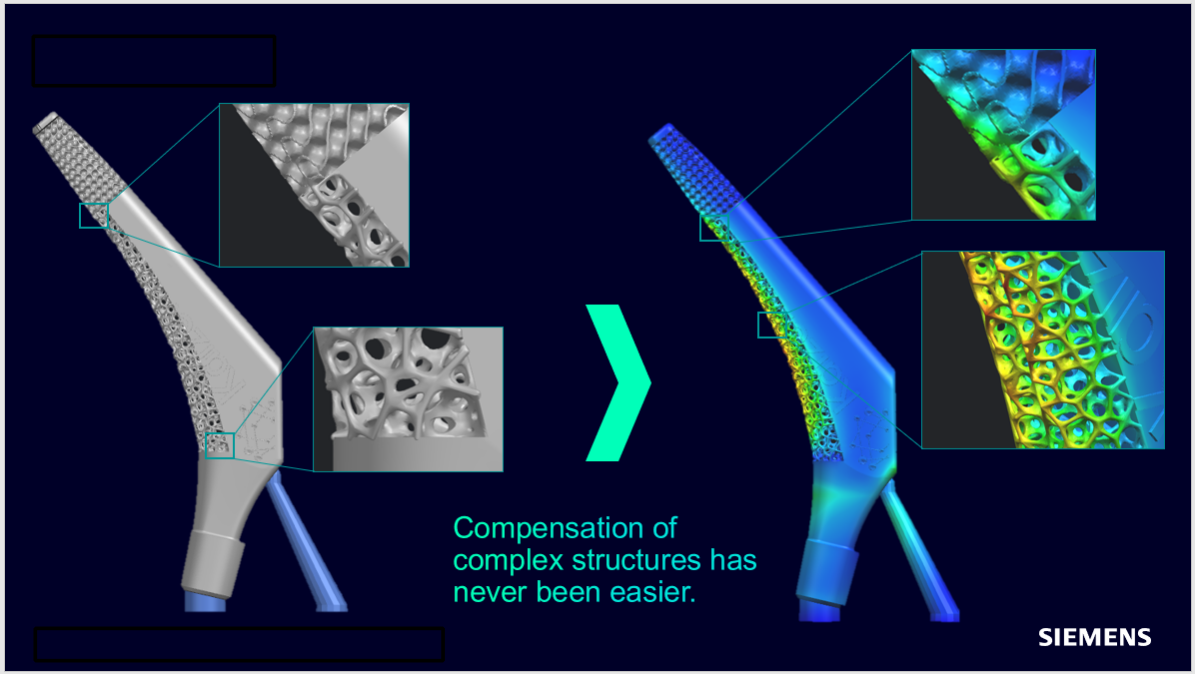
Additive manufacturing growth
As the world of 3D printing / additive manufacturing continues to expand and diversify, an increasing number of businesses are turning to metal printing technologies. However, while the printing process itself can be efficient and precise, metal parts are susceptible to distortion and deformation caused by residual stresses. This can result in parts that do not meet specifications, leading to inefficiencies, wasted resources, and poor-quality products.
New in Simcenter 3D
Simcenter 3D Additive Manufacturing’s geometry compensation is a solution to this problem. The software allows for the prediction and compensation of any deformations caused by the printing process, resulting in a more accurate final product.
When a metal part is printed using a powder bed fusion printer, the material undergoes melting and solidification. These processes create thermo-mechanical stresses, which will result in residual stresses that cause the deformation of the part. These deformations occur during printing and after the part has been removed from the printer, leading to a mismatch between the specifications and the final product.
compensated geometry
The compensation functionality in Simcenter 3D Additive Manufacturing addresses this problem by using the predicted distortion field to apply a compensation effect to the original geometry. The user selects the appropriate load case, and the compensated geometry is generated. The compensation functionality also allows the export of the compensated support structures, thus allowing the user to skip support structure regeneration. The compensated files, in STL format, are then put back in the build setup and can be sent to the printer.
The key advantages of using the STL-based compensation algorithm include a highly robust approach for compensating for distortion and visualization of the distortion field directly on a facetted (STL) geometry. This feature provides a major plus because the distortion results are calculated using a voxel mesh, which has been chosen for its meshing robustness. These two choices are thus combining the best of both worlds, regarding robustness.
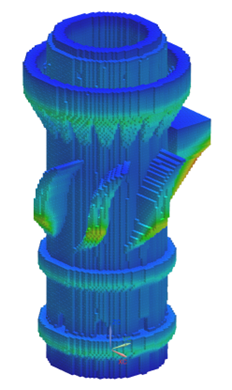

Distortion during printing
To accurately predict distortion during the printing process, Simcenter 3D Additive Manufacturing relies on a calibration-based inherent strain method that uses direction-dependent strain values. The process involves printing two calibration beams and then partially cutting them to create the bending deformation necessary for obtaining the correct inherent strain values. With this approach, users can accurately predict distortions and compensations, resulting in high-quality printed parts that meet their design specifications
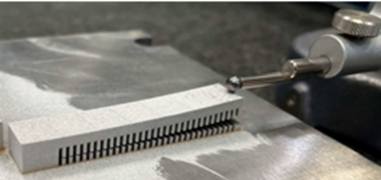
Summary
Overall, Simcenter 3D Additive Manufacturing’s STL-based compensation algorithm and calibration-based inherent strain method provide a powerful set of tools for additive manufacturing professionals. These features enable users to achieve the highest level of precision and accuracy in their 3D printing projects. It is a valuable tool for companies that rely on 3D printing metal parts, such as aerospace or medical device manufacturers.
Simcenter Mechanical release
This blog was released as one of a series celebrating the release of the Simcenter Mechanical solutions products. Other blogs that were released in this Simcenter Mechanical series include:
Strength and fatigue analysis wizard guides you to the results – Simcenter 3D 2306
Advances in resonance and cyclic symmetry of bladed rotor assemblies – Simcenter 3D 2306