Deformation modes of flexible components in mechanisms, their effect on NVH, and how Simcenter 3D motion can simulate them.
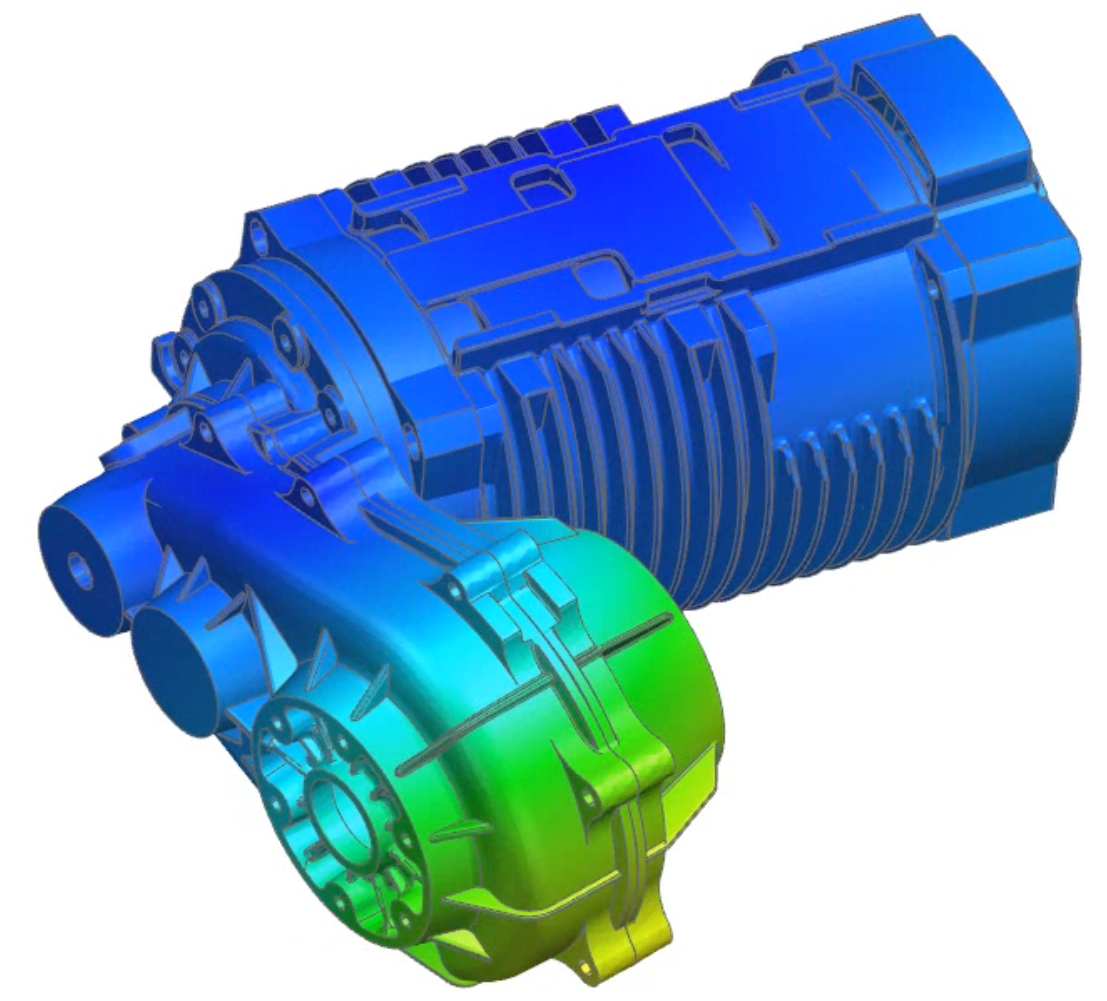
How we used to model deformation and NVH
Until now engineers have faced the challenge of studying the effects of deformation on the NVH performance of a system. They must go through a long modeling process to modify the structural model and change its vibrational behavior. This required a high degree of modeling expertise, and even experienced users must go through a time-consuming iterative process of model re-meshing, solving, and post-processing. To make matters worse, structural modifications usually impact all deformation modes of a flexible component, making it harder to decouple them in a vibration sensitivity analysis.
Modal editing
Now, Simcenter 3D Motion has come to the rescue. They have introduced a new feature called Modal Editing, which exposes to the user all frequencies of a modal equivalent ERFEM-based flexible body. Each mode is represented by a simple mass-spring 1 Degree-Of-Freedom system, and the oscillations of any modal mass are linked to the corresponding mode shape of the structure through a set of coefficients representing the deformations measured at any node in all directions. Running a modal analysis on this equivalent modal model gives, by definition, precisely the same results as the original model, allowing it to be used as a parametric, editable input for a Motion flexible body.
The advantage of equivalent modal modelling
The advantage of using an equivalent modal model is that in principle the user could modify both frequencies and mode shapes of the flexible body just by editing the input deck file of the modal solver. In practice, changing deformation shapes is complex due to the many parameters involved, but editing modal frequencies is much easier. Each system in the modal model is fully decoupled from any other, enabling users to edit single modes without affecting the remaining mode set.
Finding the motion dynamic solution
This new technology proved useful in evaluating the impact on the vibration levels of the flexible housing of an eDrive powertrain from a 10% increase of the 1st bending mode frequency. By modifying the desired modal frequencies using the Mode Editing tool, a new solution was started to compare the vibration results obtained with the new model. The overall level of vibrations at the selected node was decreased, especially in the speed range up to 4000rpm. The results of the Motion dynamic solution were then reused for further acoustic analysis of the housing.
Summary
In conclusion, Simcenter 3D Motion users now have access to a new functionality that enables them to edit the modal frequency content of a flexible body. Through a fully automated process, they can perform sensitivity analyses and what-if scenarios to quickly evaluate how changes influence the performance of the mechanism in the flexibility of any component.
Simcenter Mechanical 2306
This blog was release as part of the Simcenter Mechanical 2306 release series, other blogs in this series include:
Simcenter Additive Manufacturing – A Robust Compensation Workflow
Strength and fatigue analysis wizard guides you to the results – Simcenter 3D 2306
Advances in resonance and cyclic symmetry of bladed rotor assemblies – Simcenter 3D 2306