What you need to know before selecting the best end-of-line testing equipment
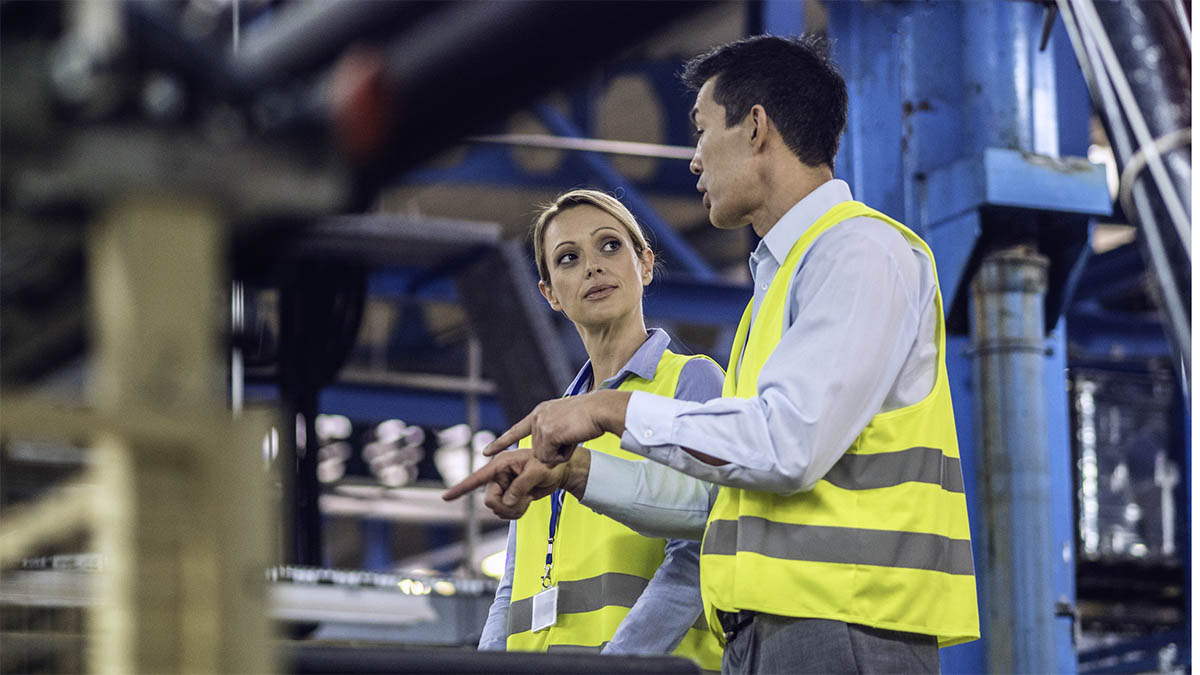
It is a pretty simple principle. Before you release your final product to the market or your client, you want to make sure there are no errors to prevent rework product failures, recalls, and scrap. To ensure that only the error-free product leaves the factory, you need to build an efficient quality check procedure with top-notch end-of-line testing equipment. The keywords you need to keep in mind when deploying such a process at your plant are time-efficiency – continuous production optimization – precision.
Why NVH-based end-of-line-testing?
Looking to the automotive industry, car manufacturers and suppliers of components such as engines, transmissions, steering components, and electric motors have adopted vibro-acoustic assessment for the end of line test systems. This technology relies on 100% vibro-acoustic measurements in the production cycle of the final products. The end-of-line testing process starts with the recording of vibration and sound signals using dedicated sensors. (Read this blog post for a detailed technical explanation.) Why this technology? There are many benefits. Let me name the most important ones. This kind of test a test happens within few seconds and brings immediate pass-or-fail results, and it is easy to imbed in the production line.
With Simcenter Anovis you can process data collected using advanced algorithms and automatically identify the product imperfection and the root-cause. Especially with the vehicle’s progressing electrification, car manufacturers and suppliers seek different end-of-line test stands reflecting new needs. As electrified engines emit lower sound levels than combustion engines, there might be errors in vibro-acoustic errors at higher frequencies. That means that the failure results in very prominent and annoying noise. (Check out this blog post for the end-of-line testing definition for electrified powertrains.)
How to maintain the production quality
When deploying the end of line testing equipment, you shouldn’t see it as an extra effort. On the contrary, it is a way to maintain the entire production quality by effective final product testing. Once you start to put the end-of-line analysis and all recorded data into a statistical perspective, you can optimize and enhance the whole production process. Once you identify the issue root-cause of the product, you can quickly investigate the production stage when it occurs and prevent it throughout the production. In other words, end-of-line testing equipment and framework creates a good bridge between the development and production teams. Consequently, having clear reports and data in hands accelerates better knowledge transfer between both teams.
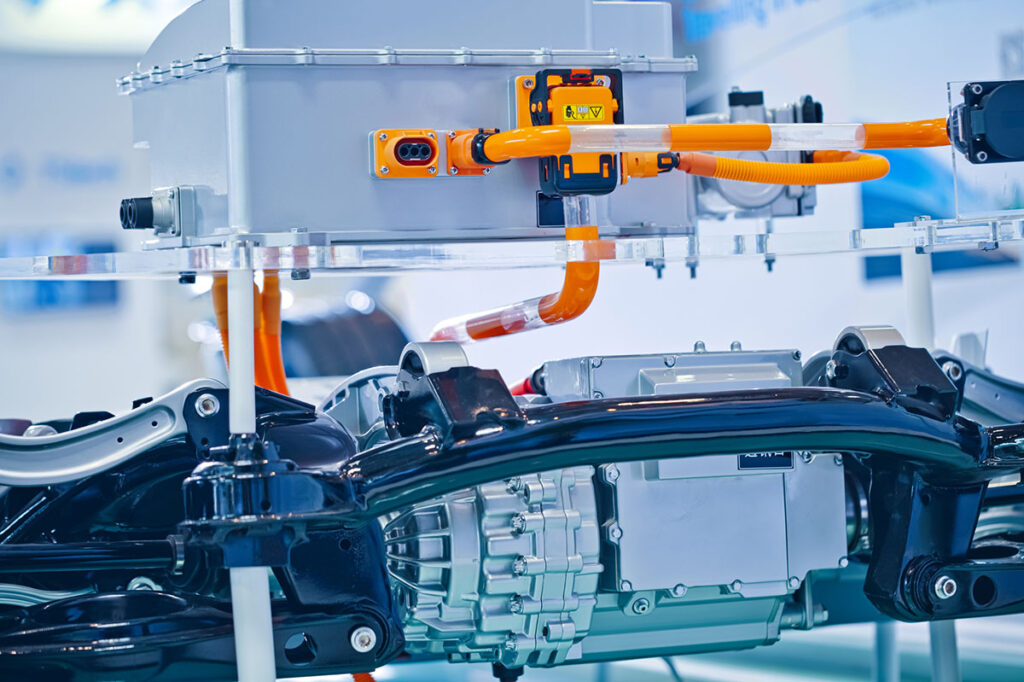
How to ensure end-of-line precision?
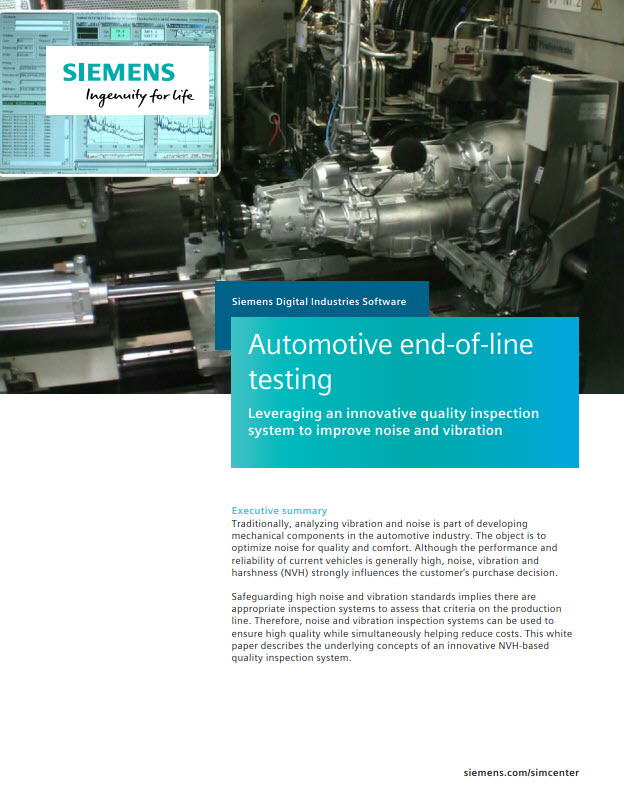
In short, the correct setup is essential. Deploying end of line test systems is a journey when you need to find answers to many questions. It is more than necessary to take a conceptual design approach to achieve the best performance, ensuring precision. Here are some of the aspects you need to evaluate.
- The optimal test setup
- The ideal end-of-line testing regime
- The elements of end-of-line analysis
- The automation of the process?
To guide you through this process, we prepared for you a white paper to download. This white paper compiles detailed information end-of-line testers and quality managers.