Reach 50% efficiency of your heavy equipment large engines with system simulation
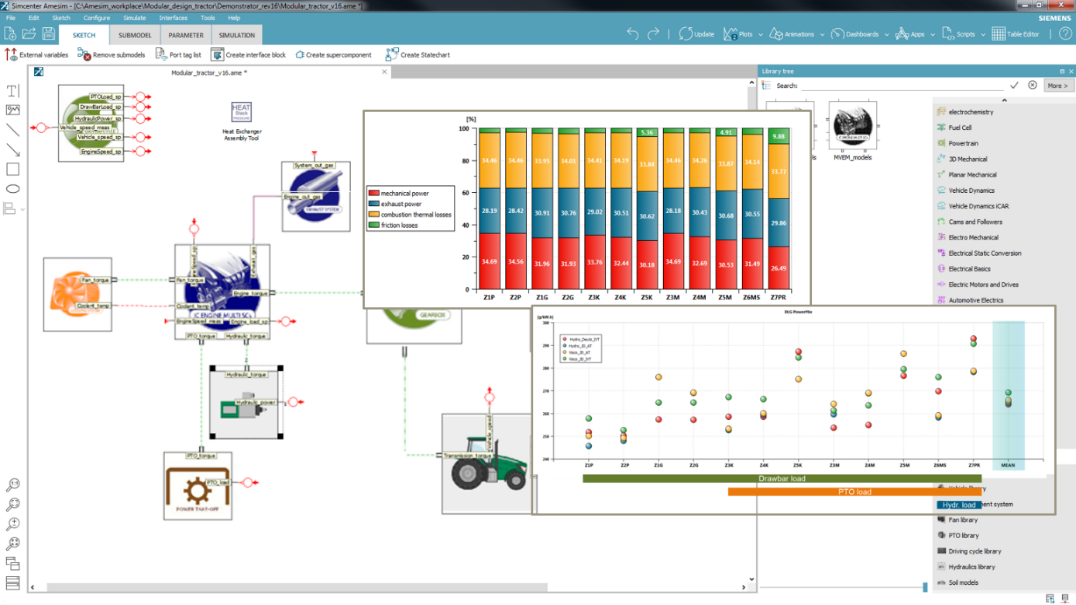
Fit with total cost of ownership objectives complying with emissions regulations
Even if we are currently hearing a lot about electrification, off-road machines remain mainly powered by the internal combustion engine (almost nearly 100% for construction equipment). However, pollutant emissions from combustion engines significantly contribute to air pollution by emitting carbon oxide (CO), hydrocarbons (HC), nitrogen oxides (NOx), and particulate matter.
In 2019, a new European regulation enters into force: Non-Road Mobile Machinery (NRMM) makers have no choice but to introduce machine with engines complying to strict criteria that Stage V implied (Fig1). Industrial actors had several years to get prepared to progressively reduce the pollutant emissions.
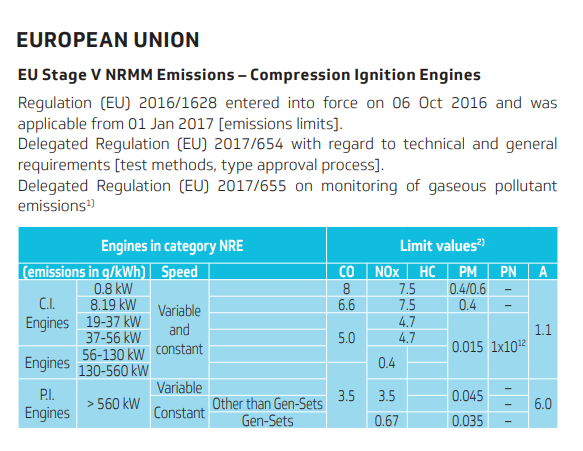
In parallel, OEMs still need to comply with the total cost of ownership reduction objectives, meaning improving fuel efficiency. By 2020, they may reach the 50% engine efficiency target – positioned between 30-40% today. This requires investigating several means for OEMs and engine suppliers.
Technical requirements are complex to find out the right balance between emission regulation compliance and fuel efficiency target. Combined with a competitive environment, off-road machines makers have to rethink their engineering process to be able to analyze their engine design early in the development cycle.
Opting for system simulation and focus on specific areas
So, in the context of fuel efficiency optimization, while complying with emissions regulations, there are several areas where the use of system simulation can accelerate product innovation such as:
- In-cylinder
- Thermal Management
- After-treatment
- Electrification
- Intake, Exhaust & engine actuation
- Powertrain integration
In the on-demand webinar Reach 50% efficiency of your off-road engines while complying with emission regulations Romain Nicolas from Siemens and Bakir Puran from Liebherr Machines Bulle cover two of the identified areas above.
- 1st, Bakir Puran covers the waste heat recovery system design and analysis. Then, he explains how to use system simulation for simulate the organic Rankine cycle system. Indeed, an internal combustion engine produces a lot of heat which is not converted into mechanical or electrical power. In that case, the waste heat recovery system can turn one part of those heat losses into useful energy. This technology is an efficient way to reduce fuel consumption and so to reduce CO2 emissions. Liebherr Machines Bulle investigates that system optimization using Simcenter Amesim. Discover how and the results they achieved !
- 2nd , it is crucial to focus on after-treatment system design while optimizing fuel economy and cost savings. The use of simulation is a key asset to develop efficient engines and associated after-treatment design system in shorter delays. Romain does a live demo of how to optimize an after-treatment system and its thermal management using Simcenter Amesim.
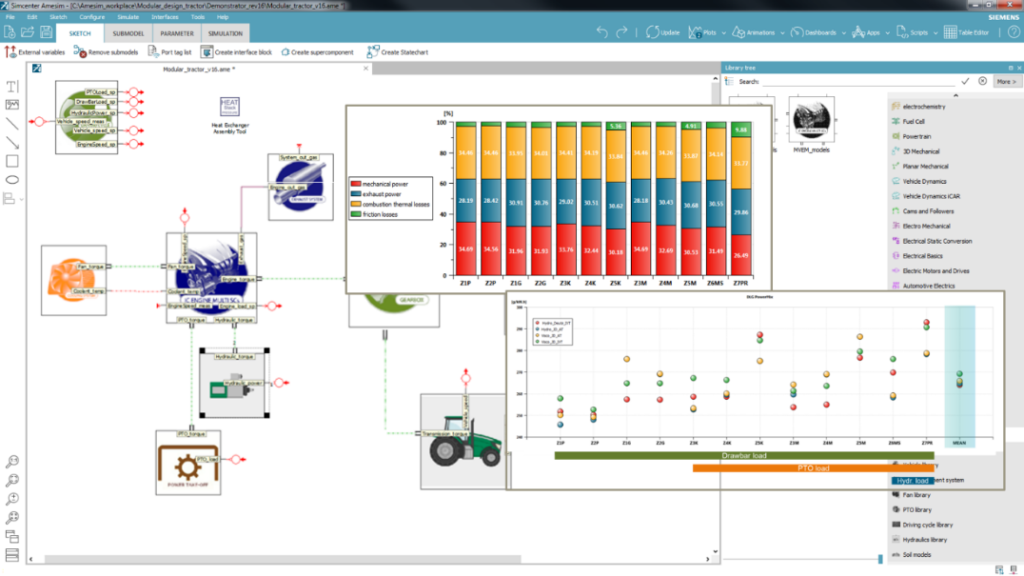
Want to explore other area where you can optimize your fuel efficiency. Then, register to our other on-demand webinar: System simulation: a key differentiator for designing electrified heavy equipment