How to design a product that will change the world?
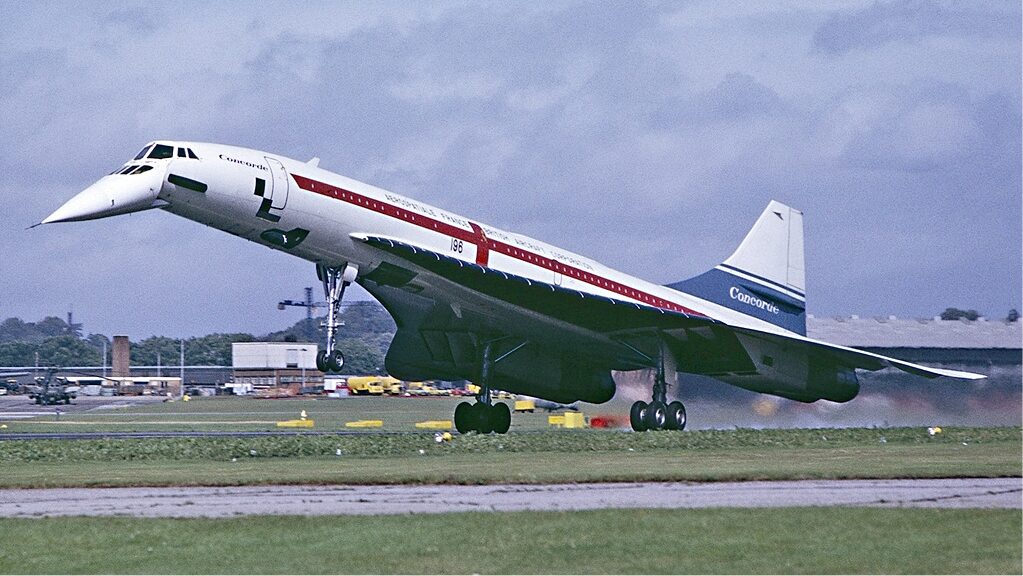
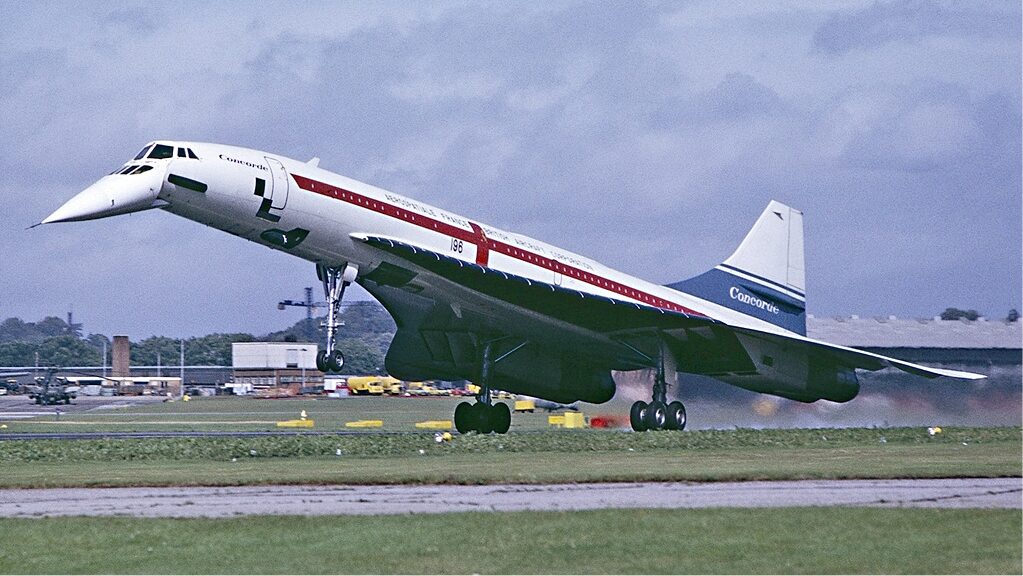
Growing up in West London during the 80s and 90s, I would often hear the deep rumble of Concorde from the school playground as it took off almost 10 miles away at Heathrow airport. Even on the tarmac, it was quite an ordinary sight, despite its rather unique looks. Probably just because it was always there, the idea of supersonic flight never struck me as all that impressive.
Now that I better appreciate some of the challenges you face when trying to overtake sound waves in an aircraft, it seems strange to have accepted these machines as the norm – and it was only after they were retired from service in 2003 that I began to appreciate how remarkable the story of the Concorde was. Designing a completely novel and pioneering aircraft as a collaboration between two countries and using the design and testing tools available at the time really is an astonishing feat of engineering and determination.
One of the most striking facts I have read about Concorde was the number of full-size prototype airframes built during its development – six. This might not sound too shocking compared to Edison’s 10,000 lightbulb prototypes or Sir James Dyson’s 5,127 iterations to perfect the first bagless vacuum cleaner. However, consider that only 14 production Concordes were ever built. This is a big part of why the development costs became impossible to recoup from aircraft sales, and the whole project was only possible thanks to a massive financial commitment from the French and British governments.
From six to hundreds with virtual prototyping
Now that we are well into the 21st century, I can’t help but wonder how the story might have been different with the CAE and collaboration tools we have available today. Using simulation in place of physical testing and prototyping, developing a pioneering and yet commercially viable new technology with confidence is much more achievable than ever before, despite the increased complexity of today’s products and the rapid pace of development needed to remain competitive. Simulation not only answers questions but also opens the door to new ideas and is a catalyst for innovation. Here are two examples of how Siemens customers use simulation to push the envelope and develop pioneering products.
Igniting the world’s first hydrogen powered gas turbine
One of the biggest challenges in switching to renewable energy sources is a lack of large-scale energy storage. During the unavoidable periods when wind and solar are unavailable, or to meet peaks in demand, the task of producing energy typically falls to gas turbines powered by natural gas.
Removing this barrier to true carbon-zero energy production requires the sort of innovative new technology recently developed by energy technology company B&B-AGEMA and Kawasaki Heavy Industries. Leveraging virtual prototyping using CFD simulation with reactive chemistry, they could predict complex flame characteristics and emissions from different combustor designs. Combined with an optimization loop driven by Simcenter HEEDS, they have overcome the difficulties of burning hydrogen fuel to create a gas turbine with extremely low CO2 and NOx emissions.
“A big benefit is we can achieve a high quality turbine in a very short time”
Rene Braun, Technical Manager Aerothermal Design, B&B-AGEMA GmbH
Developing cutting edge VTOL UAV technology
When it comes to operating an autonomous aircraft that can take off and land vertically in a tail-sitting orientation, hover, and transition to horizontal flight with a useful range and payload, there are many different demands put on the propulsion system.
The V-BAT drone uses a ducted fan which improves the efficiency and robustness of a propeller while also reducing noise – ideal for a surveillance drone with military applications. However, making the concept work requires designing a single duct to perform well across the entire flight envelope. Martin UAV tackled this challenge by uncompromised virtual prototyping: leveraging intelligent design exploration using Simcenter STAR-CCM+ and HEEDS they evaluated 100s of designs at various operating conditions to find a more efficient duct design that improved the drone’s payload and range.
“Our customers want more payload, more fuel carrying capacity and longer flight time. High-fidelity simulation is a way to stay ahead of their demands”
Zach Hazen, Aerodynamics Lead, Martin UAV
Today, it’s hard to imagine developing a ground-breaking product without using engineering simulation to prove and refine designs before embarking on the long and costly process of building physical prototypes. As well as allowing you to go faster and explore more possibilities, simulation can provide a much greater understanding of the performance of complex products over a wider range of operating conditions.
A second chance with virtual prototyping?
As for Concorde, it looks as though we will get to find out the answer – can modern CAE tools take the future of air travel beyond the sound barrier once again? Several companies are actively developing supersonic aircraft, with one operator recently announcing plans to begin operating by 2029, nearly 30 years after Concorde’s final landing. I will be watching with interest!
Your chance!
Meanwhile, we are eager to see and honor your groundbreaking innovation: