How is the product development process evolving at small and medium businesses?
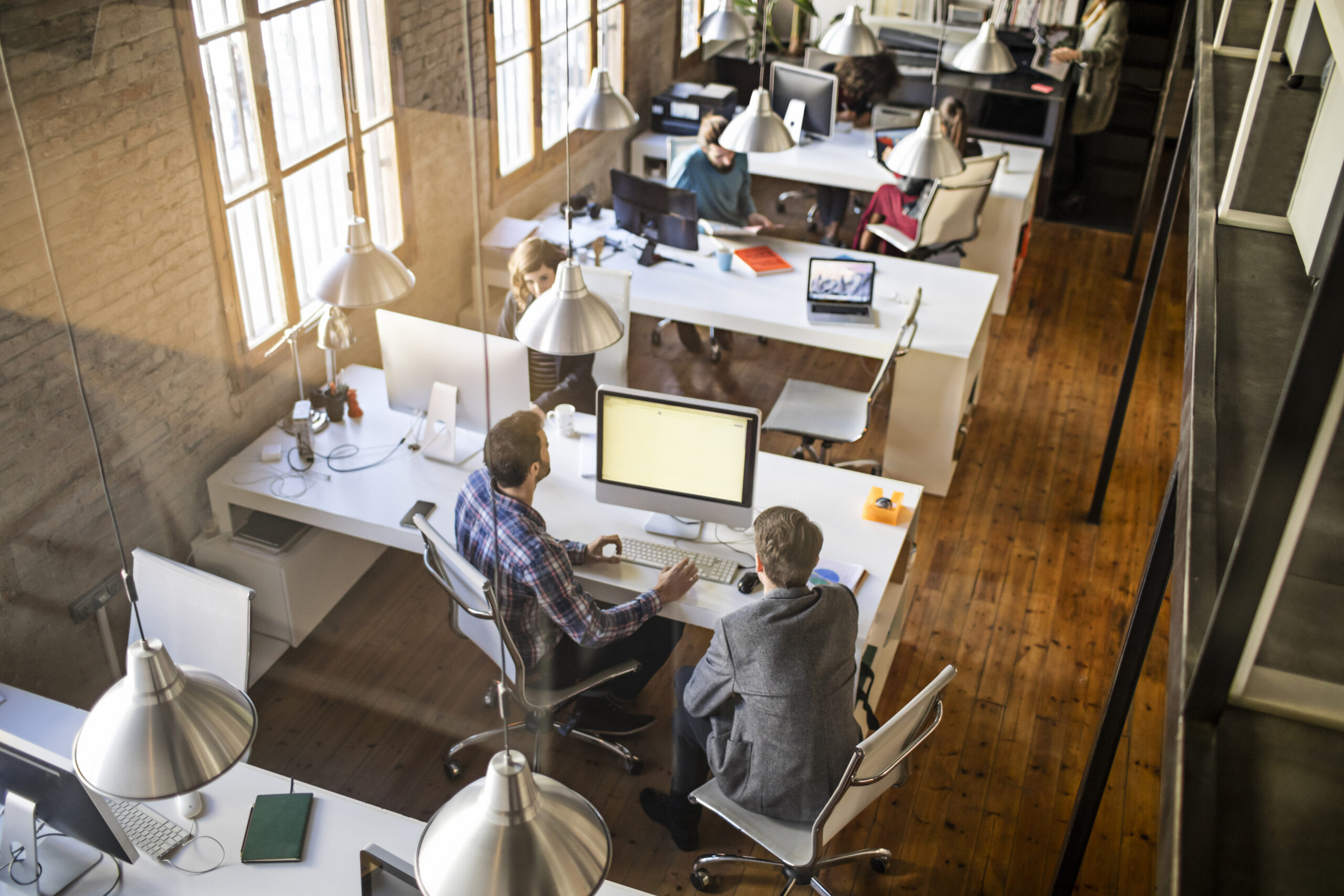
In today’s rapidly evolving business landscape, the integration of cutting-edge engineering technologies has become pivotal for companies striving to maintain their competitive edge. Small and medium-sized businesses (SMBs), once constrained by limited access to advanced tools and resources, are now leveraging innovative solutions to drive product development and engineering efficiency. According to recent market research (source: Engineering.com), the global engineering software market was at $32.6 billion in 2022 and is projected to reach $50.2 billion by 2026, with SMBs playing an increasingly significant role in driving this growth.
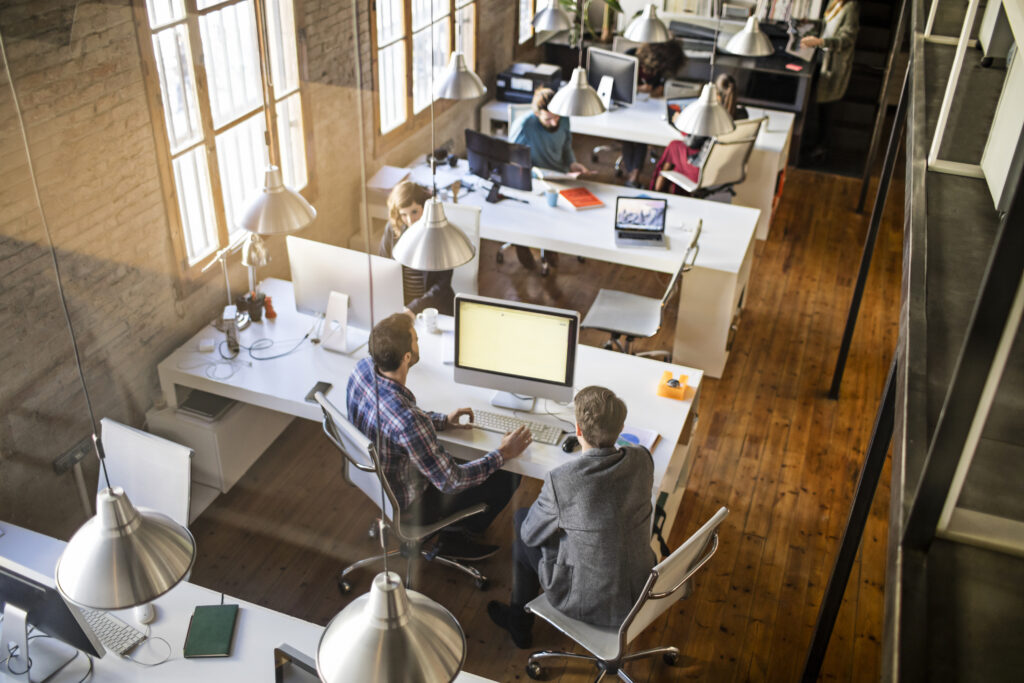
Despite the pervasive influence of engineering and technologies, SMBs historically faced challenges in adopting these tools due to cost constraints and technological barriers. Large enterprises, with their vast resources, monopolized the field of product development and engineering, leaving SMBs at a disadvantage. However, advancements in cloud computing, subscription and licensing structures, integration with CAD and PLM solutions, and increased collaboration between teams have democratized access to sophisticated advanced simulation and modeling capabilities, leveling the playing field for SMBs.
In this blog, we delve into the transformative impact of engineering technologies on SMBs’ product development processes. We explore how tools like Simcenter STAR-CCM+ are empowering SMBs to overcome traditional limitations, optimize performance, and drive innovation across various industries. By harnessing the power of simulation, virtual testing, and advanced analytics, SMBs can now compete with larger counterparts on a global scale, delivering high-quality products at accelerated timelines and reduced costs.
Trial and erroneous product development
The increasing ubiquity of engineering and technologies has rendered them more accessible to businesses and manufacturers previously unable to invest in them. Seizing these opportunities, large enterprises have maintained their hegemony in product development and engineering. Consequently, product development teams at small and medium-sized manufacturers have often relied on a blend of technology and manual methods, leaning heavily on the experience and expertise of their team members. However, attrition and talent loss pose significant risks for such teams, potentially derailing the product development process and delaying time-to-revenue. Moreover, a reliance on trial and error has been prevalent in this approach. Teams typically design, build, and test products, iterating designs through trial and error until meeting target specifications. Unfortunately, simulation tools and technologies are rarely utilized in such scenarios, resulting in sluggish, error-prone processes unsuitable for businesses aiming to develop and launch products regularly.
Nevertheless, technological advancements have dramatically evolved over time, with technology providers increasingly addressing the needs of small and medium-sized businesses. Developments in cloud computing, subscription and licensing structures, and integration with CAD and PLM solutions, together with other advancements in simulation and modeling technologies have transformed the landscape. Tools and technologies once out of reach for SMB product development teams can now guide design development, optimization, and performance validation. This paradigm shift in product development has not diminished the role of testing; rather, it has streamlined the process into a more linear workflow, minimizing the need for trial and error and enabling the creation of more accurate prototypes. Such workflows present new opportunities for businesses, including reducing time-to-revenue, increasing product output, and meeting customer expectations. Furthermore, these tools and technologies expedite the evaluation of design concepts, streamlining the request-for-quotation (RFQ) process, and enabling product development teams to support the business goal of winning more contracts.
One of the primary obstacles faced by SMBs in the past was the lack of simulation and testing tools, hindering their ability to explore new concepts and innovate. Consequently, product development teams were confined to slow, error-prone trial-and-error processes, limiting their output to basic components with minimal complexity and innovation. However, with tools and technologies becoming more accessible and suitable for smaller teams, the situation has improved drastically. For instance, advanced tools like Simcenter STAR-CCM+ empower teams to explore new concepts at the design stage, investigate innovative designs, and gain insights into complex fluid dynamics phenomena. Such capabilities provide SMBs with a competitive edge, fostering innovation and driving business growth. Moreover, these capabilities are advantageous for small and mid-sized consulting organizations, offering high-value computational fluid dynamics (CFD) analysis and simulation services to explore new concepts and innovative designs.
Eliminating the endless loop of Design-Build-Test
The real value of Simcenter STAR-CCM+ for small and medium-sized manufacturers lies in developing in-house capabilities. In addition to research and development efforts, teams can leverage such tools to simulate and optimize product performance. Key use cases include fluid dynamics analysis for industrial equipment manufacturers, enabling them to understand flow patterns, pressure distribution, and turbulence profiles. Additionally, STAR-CCM+ facilitates multiphysics simulations, predicting and analyzing the interaction between fluid flow, heat transfer, structures, and other physical phenomena. Furthermore, the software finds applications in various industries, including heat transfer, energy efficiency, aerodynamics, and turbulence analysis, empowering manufacturers to enhance product performance across diverse sectors.
Another significant benefit offered by simulation tools is virtual testing and validation. While physical testing remains indispensable, virtual prototypes based on simulation results enable the development of accurate prototypes conforming to target specifications, thereby eliminating the endless loop of design-build-test.
What’s catapulting small and medium businesses to the forefront?
As the technological ecosystem matures within small and medium-sized businesses, top management should consider the broader implications of these tools on the entire product development process. Streamlining communication between tools enhances product development workflows, with integrations with product lifecycle management (PLM) and computer-aided design (CAD) tools being crucial. Manufacturers equipped with these integrations can consult simulation results, make design modifications, and perform simulations to predict behavior and analyze results seamlessly. To optimize simulation workflows and address challenges associated with manual processes, a bridge between CAD and simulation tools is essential. PLM tools, such as Teamcenter, address this need, efficiently managing product data, facilitating collaboration, and serving as a central repository for CAD models, simulation results, documentation, version control, and user access management.
Process industry incumbents stand to benefit significantly from software tools like Simcenter STAR-CCM+, enabling manufacturers to optimize manufacturing processes by simulating process fluids, heat transfer, and chemical reactions. Simulation results impact both top-line and bottom-line metrics, maximizing product yields, minimizing by-product generation, and improving process efficiency.
Numerous case studies specific to the process industry offer valuable insights. I invite you to explore our next blog, “How are SMBs simulating for decarbonization in the process industry?” authored by my colleague Barbara Neuhierl, as she delves deeper into how simulation solutions like Simcenter STAR-CCM+ empower small and medium businesses operating in the process industry to drive decarbonization. She explains how CFD solutions can be leveraged to develop new processes and transfer them into industrial applications, while citing insightful examples of battery electrode coating, and carbon capture, usuage and sequestration. Happy reading.