How are SMBs simulating for decarbonization in the process industry?
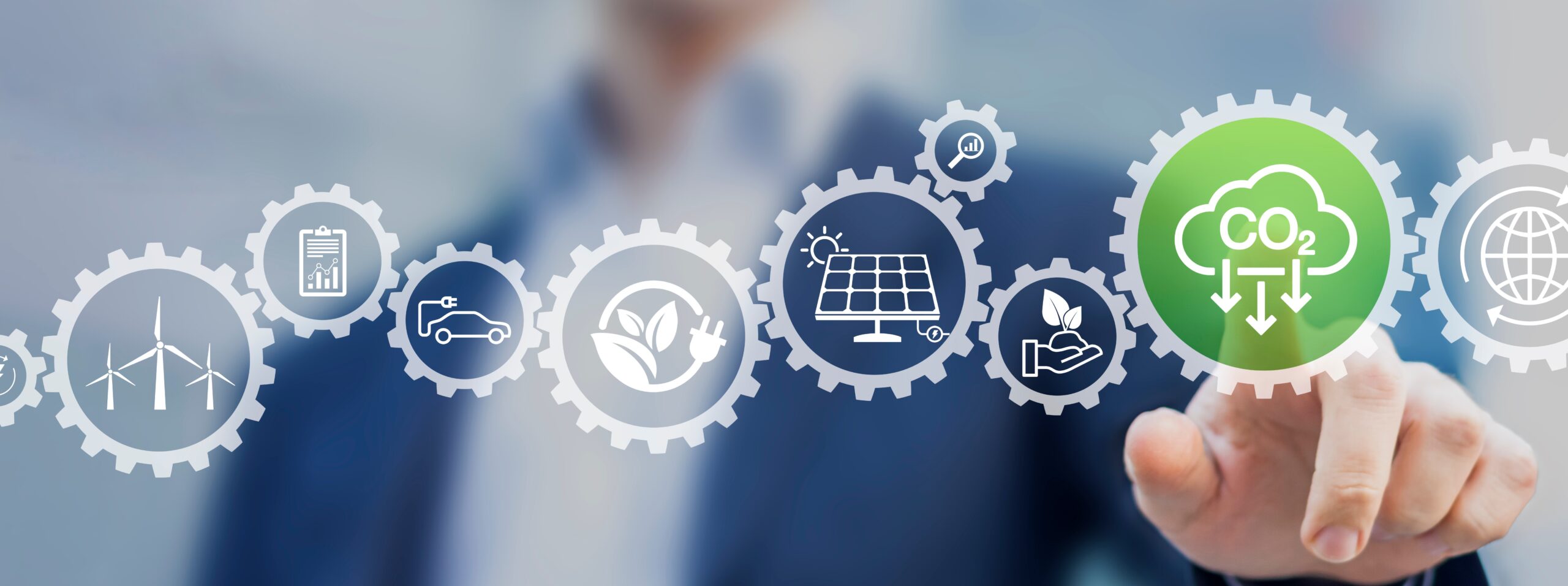
Industry in general and process industry in particular are facing manifold challenges nowadays: Decarbonization and the global push for net zero undoubtedly belong to the most important megatrends currently, obviously fueled by the progressing climate change. Extra emphasis is given by climate incidents which can be observed more and more frequently.
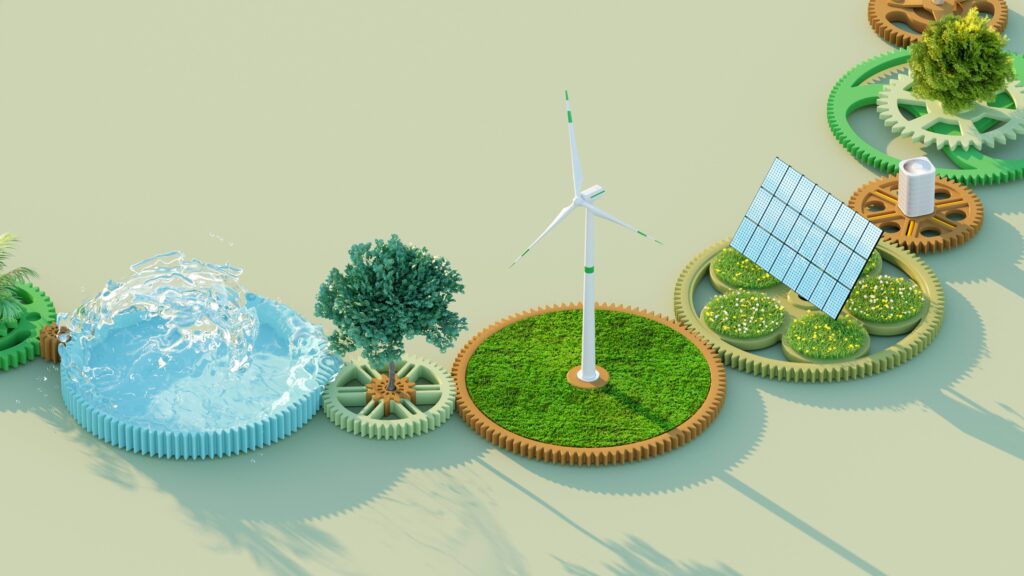
While literally almost any industry is affected, the challenges for the process industry are tremendous, as it is both energy intensive and hard-to-abate in terms of energy transition. In this context, energy transition can mean a lot of things, from green energy to increase of efficiency, from new materials to alternative production methods. The global push towards greenhouse gas reduction results in requirements for the complete industry and can be observed especially in the process industry, causing an increasing demand e.g. of renewable energy.
On the other hand, the demand for green energy and decarbonization also leads to a lot of opportunities. In principle, there are different ways for companies to succeed: To take the chance and adapt disruptive technologies as a business, or to be able to react fast enough to disruptive developments. In any case, digitalization is the key to success. Simcenter simulation technologies can help to make products smarter, cheaper, more efficient, and more reliable, and at the same time decrease time to market.
Developing New Processes and Transferring them into Industrial Applications
New processes are typically developed in a laboratory or research environment. To transfer the relevant basic process to an industrial scale, it is necessary to understand how the scaled-up system behaves. In micro scale, a process might depend on parameters like e.g. the properties and concentrations of species, shear, temperature, or the presence of catalysts.
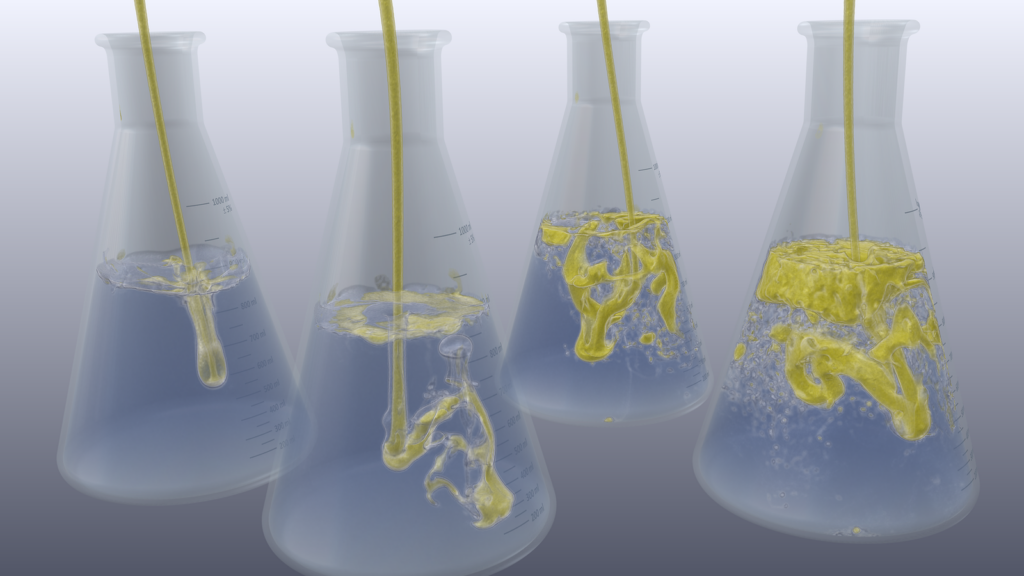
In macro scale, on the other hand, flow conditions and heat transfer in a reactor will significantly affect the micro scale behavior. Trial- and error procedures are frequently used to understand the relationships between all the variables characterizing the micro and macro behavior and are governing the respective system. These variables are representing and inherently tied to the physical and chemical properties, and it is crucial to understand how they would behave under different conditions.

3D Simulation methods can help to increase the respective scaling-up processes significantly.
Let’s have a look at some few examples to illustrate what this can mean:
Example: Battery Electrode Coating
Battery electrodes significantly affect the overall performance of the electrochemical energy storage system. There are numerous methods to produce battery electrodes, like die coating, screen printing, spraying. Developing new methods usually starts with experiments in test facilities first, and – like in all emerging industries – new players on the market are often operating in startup-mode. In a film casting process, for example, active material, additives and binders need to be applied onto carrier materials, followed by a drying process. The process also includes steps like mixing or dispersing materials.
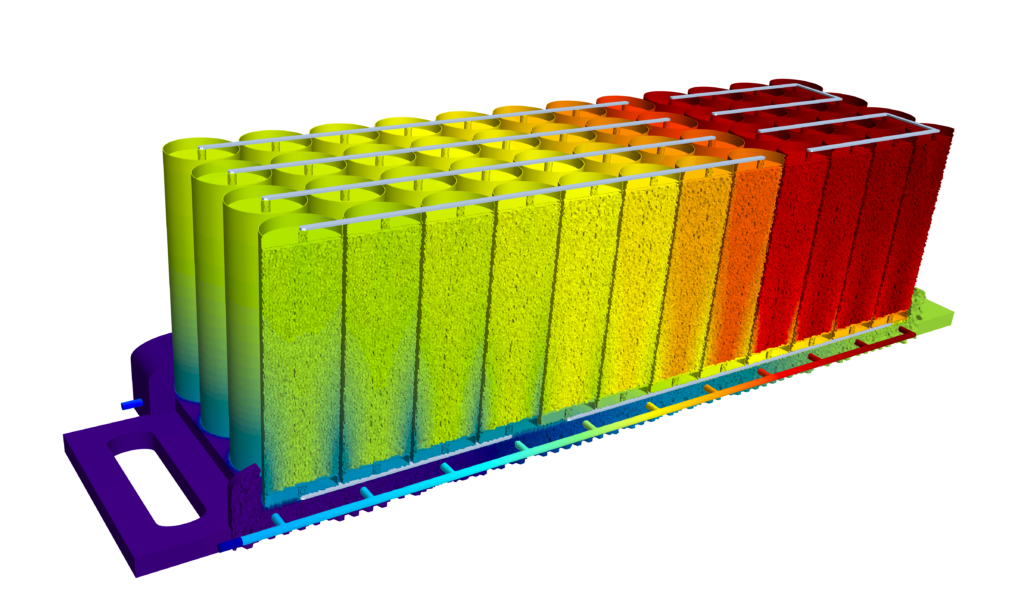
With electromobility and industry electrification expanding, research and development efforts are spent, and new materials are developed, requiring the adjustment and optimization of the respective coating processes. Properties like layer thicknesses or conductivity can be optimized by adapting different process parameters. In the process of developing new methods, and to transfer and scale the newly developed processes from lab order of magnitude to an industrial scale, simulation tools like Simcenter STAR-CCM+ play a crucial role.
Example: Carbon Capture, Usage and Sequestration
Limiting the combustion of fossil fuels is a significant contribution to reduce the amount of climate gases, and huge efforts are ongoing in this area, e.g. by electrifying the transport sector. Nevertheless, there are also other sectors emitting greenhouse gases. Industrial processes account for roughly 30 % of the worldwide carbon dioxide production. In principle it is feasible – albeit challenging – to cover the heat generation needed for melting, cracking or drying processes, e.g. in the steel, glass, or chemical industry, by renewables. But there are also industrial applications where this is not possible: In cement production, carbon dioxide is inherently emitted as part of the process and can’t be avoided, and in the chemical and petrochemical industry, greenhouse gases are for example generated as a byproduct during ammonia production.
Thus, the only realistic way to reach the 1.5 or even the 2.0-degree Celsius goal is to apply CCUS – “Carbon capture, usage and storage”. The term in general describes technological approaches used to remove CO2 from the exhausts or flue gasses. It can then be stored – e.g. in empty oil or gas reservoirs – instead of releasing it into the atmosphere. Alternatively, it can also be useful as raw material.
The technology is not new: In the Oil & Gas and chemical industry, there is a lot of experience in handling carbon dioxide. CO2 injections in oil or gas fields with the goal of increasing the yield have been used for many years. Natural gas can also contain significant amounts of CO2, which must be removed.
Separation processes have always been necessary, and several separation procedures are established and ready to use:
- CO2 ad- and absorption: Scrubbers as well as packed bed reactors are tested-and-proved devices for adsorption and absorption processes and can be used to remove pollutants and CO2 from a gas stream.
- Membranes: Diffusion process allows the separation of species
- Cryogenic Separation: By cooling down exhaust flue beyond ca. minus 56 degree Celsius at pressures smaller than roughly 5 bar, use of desublimation – phase change from gas to solid – is made. Gaseous CO2 will change its phase to solid and can thus be separated from the gas stream. Subsequent heating will melt and drain the separated substance
- Numerous other methods are currently subject to research!
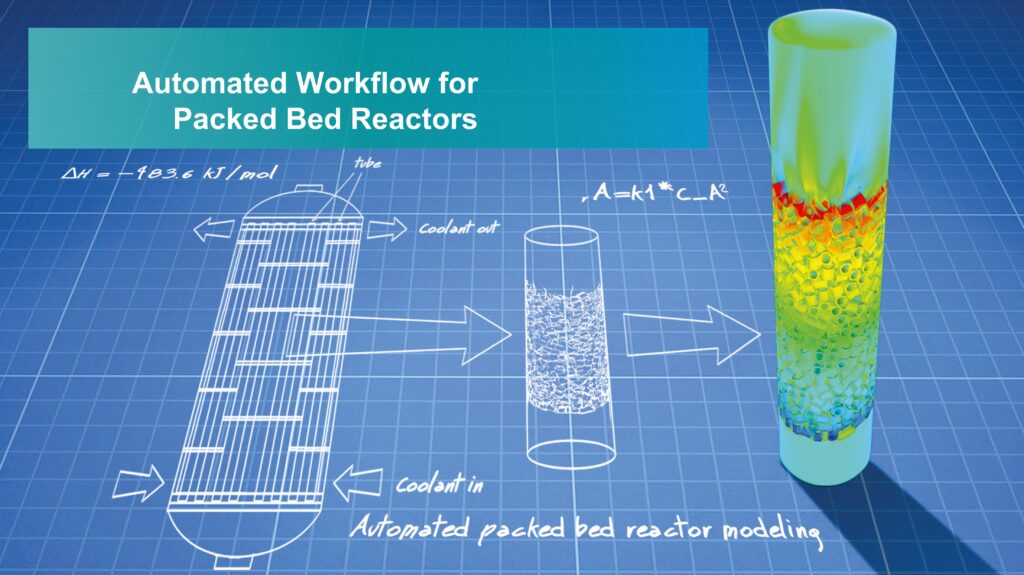
New Challenges: New Business Models for SME
Proven methodologies might exist, but what is new when it comes to large-scale decarbonization is the sheer amount of e.g. climate gas that needs to be captured and treated, or the number of batteries to be manufactured.
Companies taking the chances arising from the race towards net zero are facing several challenges: New methods need to be developed, prototypes must be built and tested. Eventually, scalability to industrial usage needs to be guaranteed, which can be a huge challenge for small and medium enterprises who are often operating in start-up mode. Developing and testing a new method can be expensive and requires a lot of effort, time and money, always with the risk of failure, when it is done in a traditional way. With Simcenter Star-CCM+, both lab conditions as well as scaling processes can be virtually tested and developed, allowing to shorten development time as well as costs and thus can help to make energy transition a reality.