Developing Novel Design Paradigms for Traction Motors using Simcenter Products
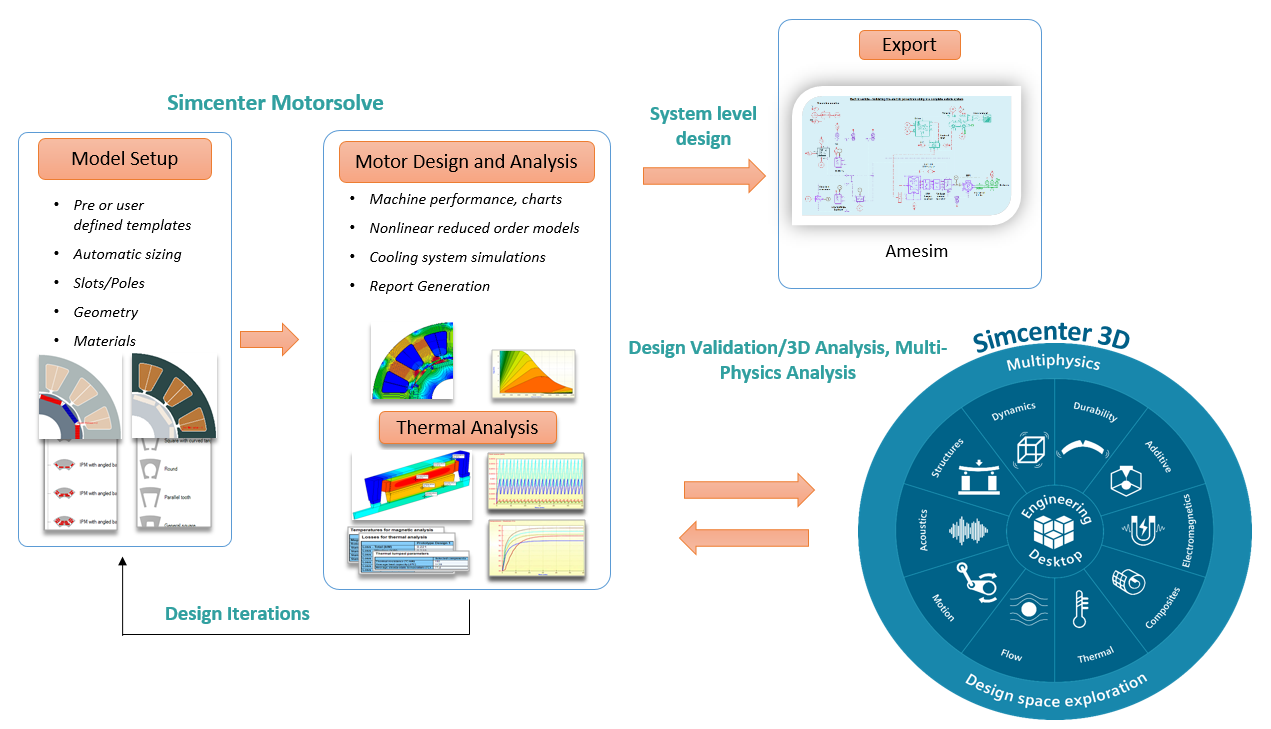
Automotive manufacturers are facing tremendous challenges for developing the next generation of motors for hybrid and electric powertrains. They are operating in markets driven by a number of factors including, regulations for greenhouse gas emissions, government objectives around electrification of the transportation sector (in many regions, the goal is ~30% by 2030), and the development of autonomous vehicles. In the age of Industry 4.0 technologies however, the potential is enormous to revolutionize the design, manufacturing and product lifecycle management paradigms of all powertrain components, including electric motors. In fact, the automotive industry is poised for all-around transformation if key stakeholders in the industry are able to leverage and effectively apply emerging technologies.
What are the main implications for traction machine design?
From an R&D standpoint the next generation of traction motors will have to,
- operate at higher efficiency levels than current standards,
- must be able to operate over wider speed ranges,
- must be designed to operate optimally under variable and challenging environmental conditions,
- must be robust against manufacturing and/or other sources of uncertainties,
- be fault tolerant,
- cost effective over their lifecycle.
These are just some of the demanding criteria engineers face today at the onset of the design process. To reach these objectives their approach must utilize deep knowledge of a number of disciplines: electromagnetics, power electronics, thermal analysis, structural mechanics, multi-objective optimization, system level design and increasingly, Industry 4.0 technology. Only by utilizing the implications of each would one be able to obtain the best possible solutions.
What’s needed from a software standpoint?
To go beyond current design paradigms, engineers must have access to tools that can model innovative topologies, provide multidimensional (1D/2D/3D) modeling and analysis options and can generate temperature dependent, nonlinear reduced order models which can be shared between multiple domain specific software.
Siemens’ SimcenterTM platform has been an industry leader in providing computer aided design solutions. Recently, the platform’s motor design portfolio was enhanced with the addition of two market leading software tools: Simcenter Motorsolve, a template-based motor design software, and Simcenter MAGNET, a general purpose electromagnetic design and analysis software. These additions were made possible by Siemens’ acquisition of Mentor Graphics, and subsequently, of Infolytica Corporation. By recognizing the potential synergy of these with its existing offerings Simcenter is taking the next step forward.
What’s on the horizon?
Simcenter 3D, a centerpiece of Simcenter’ multi-physics and multi-domain simulation software, is adding electromagnetic design and analysis capability, to be called Simcenter 3D Low Frequency Electromagnetics. This module is based on the core technology in Simcenter MAGNET. Along with Simcenter Amesim, a system level simulation software and Simcenter Motorsolve the trio will form an unbeatable design solution for traction motor design.
First, Simcenter Motorsolve’s FEA based solvers allow the performance of novel or built-in motor topologies to be analyzed in minutes. It also includes a thermal analysis module which can model a number of cooling systems. It can render temperature dependent linear and non-linear reduced order models that are critical for digital twin creation and for motor drive system design. Additionally, the Simcenter 3D electromagnetics module can be used for further validation and analysis. Some of these include “what-if” studies using parametrization, 3D magnetic and thermal system analysis, 3D hysteresis and eddy loss calculations (upcoming), demagnetization prediction, machine fault simulations, among others. Finally, Simcenter Amesim provides multi-disciplinary system level simulation capability including motor drive design.
What does this all mean?
The trio described above will be fast, accurate and capable, it combines the industry’s three leading best-in-class tools. The features described, when complemented by Simcenter 3D’s structural analysis and other capabilities, result in a system of tools ideal for meeting future design challenges and developing state-of-the-art design paradigms, as shown in the figure here. To illustrate further, in a series of future blogs, I will explore their application for solving some of the most difficult traction motor design problems and for developing a framework for digital twin creation.