Collaborating for Successful Thermo-Hydraulic Modelling
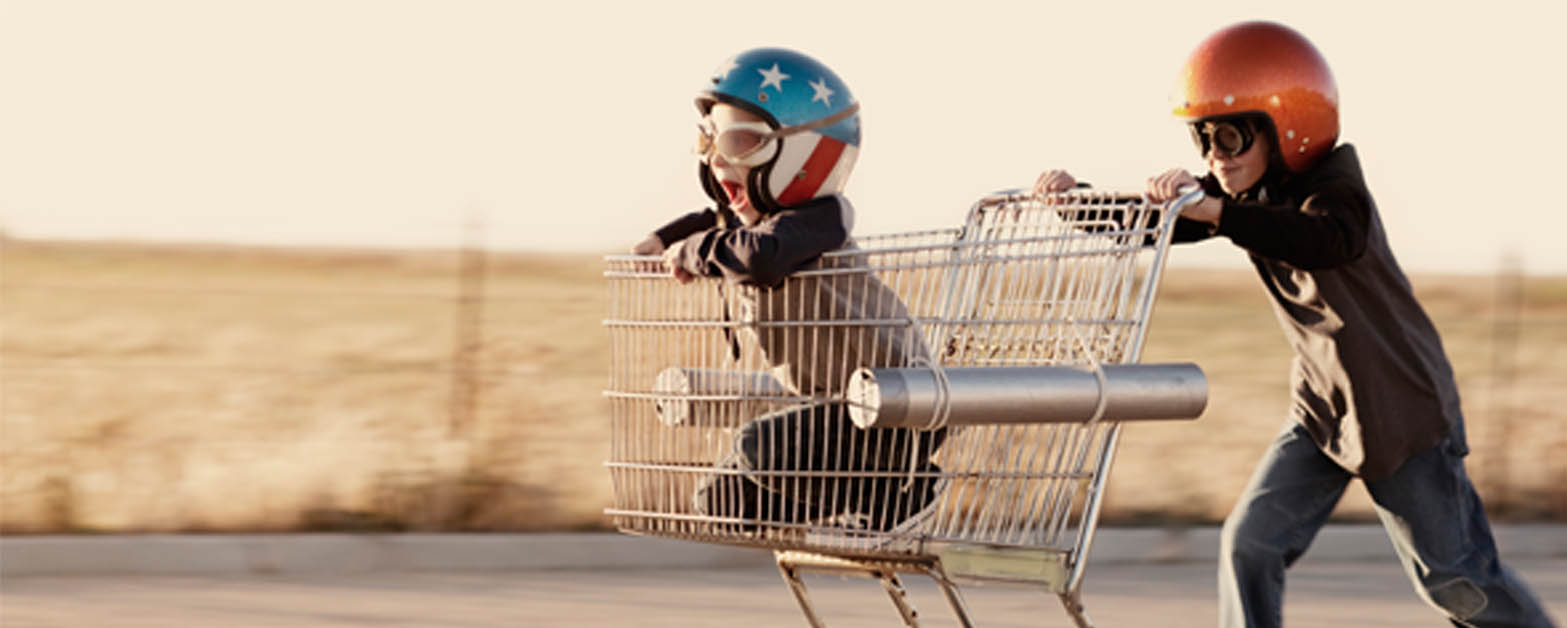
The importance of thermo-hydraulic modelling
As Simcenter Flomaster Product Manager, it is my responsibility to define the product roadmap together with my team and different stakeholders. The main question I always ask myself is: “How do we choose from all the different possibilities for new functionality?”
For me, the key is to always put our customers at the centre. We need to listen to them to fully understand their needs and the challenges they must solve. And not only does this deliver the best product, but it also gives myself and the whole team great satisfaction.
This is perfectly illustrated by a recent comment from one of our team leads, Anusha Gurrapu:
The best bit about the job for me as an engineer is sitting down with the team and brainstorming a solution to a customer’s problem. And when we’ve finally solved it, hearing our customer’s gratitude, and knowing that we’ve made the world a better place, even if in a very small way.
Challenge feeds development
Dow Chemical Company is one of the largest chemical producers in the world and a long-time user of our software. They selected Simcenter Flomaster and deployed its use throughout the organisation as the standard tool for thermo-hydraulic modelling, i.e. static and dynamic simulation of liquid and gas flow in piping systems.
Thermo-hydraulic modelling is just one of the many tasks that need to be performed to design a successful plant. As in most other chemical and engineering companies, responsibilities are shared among different teams. Cross-team collaboration and accurate simulation results are imperative to design and build safe and efficient plants.
And when it comes to thermo-hydraulic modelling, one of the key aspects is to define fluid properties that are accurate and consistent throughout the engineering cycle. This means that those properties computed with different tools by process engineers need to be transferred to the thermo-hydraulic simulation tool – in this case, Simcenter Flomaster. Doing this manually is a time-consuming exercise which can lead to user frustration and create opportunities for error.
So, in one of our meetings they described the process and asked me: “Is there a way to automate the transfer of data to Simcenter Flomaster?”
At the time there wasn’t, but, as I said, the development team love a challenge and were eager to help Dow and other customers who were facing the same issue.
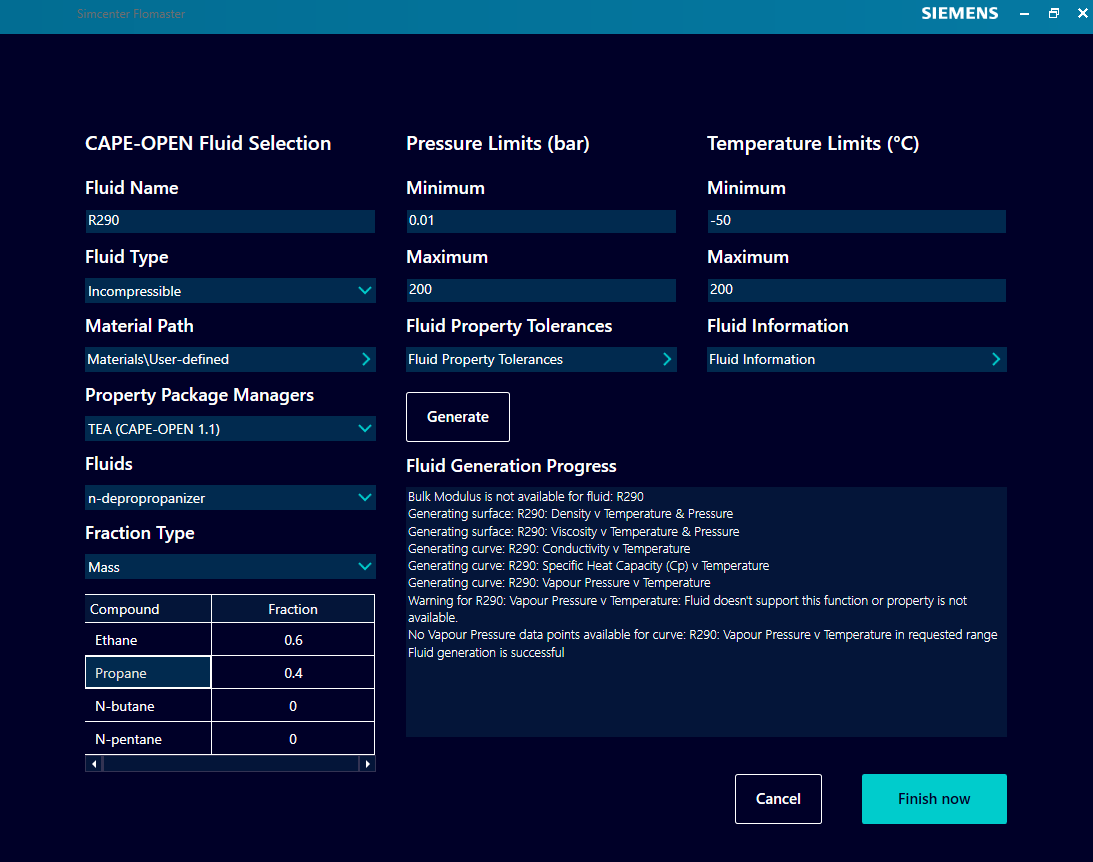
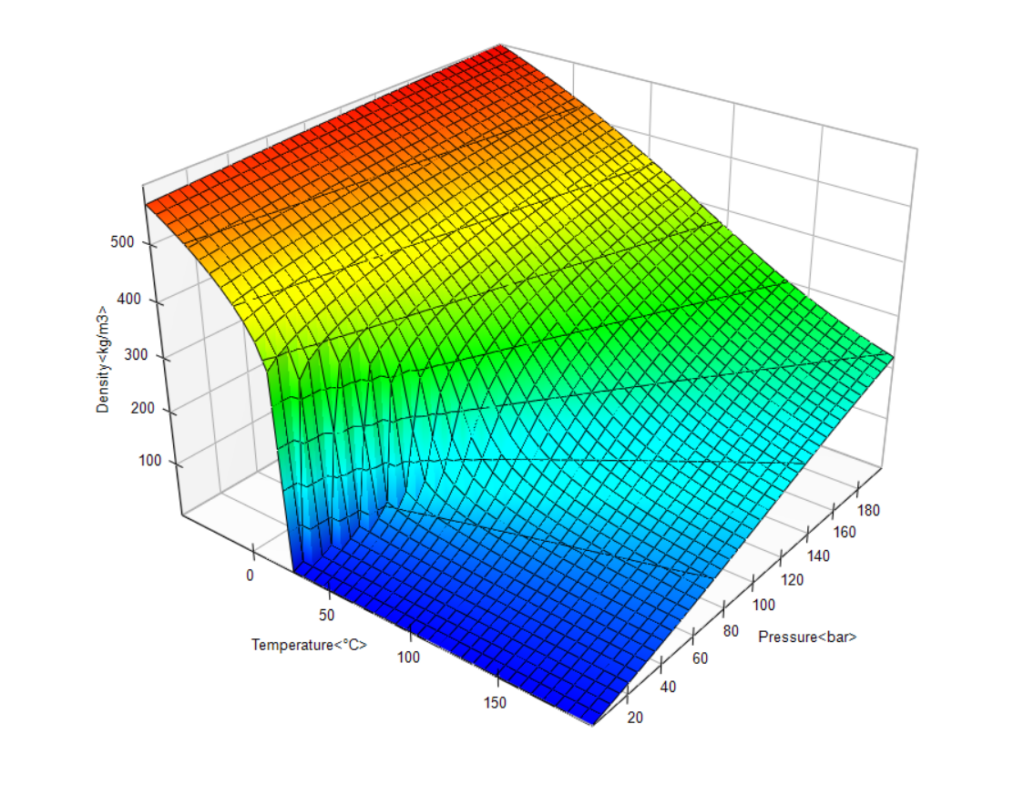
CAPE-OPEN interface in Simcenter Flomaster (left) together with one of the generated surfaces describing fluid properties used in thermo-hydraulic simulation (right)
The power of collaboration
Once we assessed Dow’s requirements it was clear that the best way to proceed was a collaborative project between our organisations to support the CAPE-OPEN standard which would automate the data transfer.
Anusha worked with Björn Altendorf, the technology expert in fluid mechanics and mixing at Dow Chemical. As Anusha and her team developed the interface, they were able to check and confirm its accuracy at key stages with Björn, thus saving considerable time and development efforts.
The end result? The interface was developed and put into operation in less than six months. To demonstrate the success of this collaboration, Anusha and Björn presented their results last year at the annual CAPE-OPEN meeting.
Most importantly, Dow Chemical no longer have to spend time on manual data transfer. Their engineers can focus their efforts on more valuable activities, using their ingenuity to design safer and more efficient plants without needing to doubt the accuracy and consistency of the data.
Not only that, thanks to this collaborative work, all Simcenter Flomaster customers can benefit from this development as it is now a feature of the latest version.