Closing the Loop between As-Designed and As-Manufactured Composites
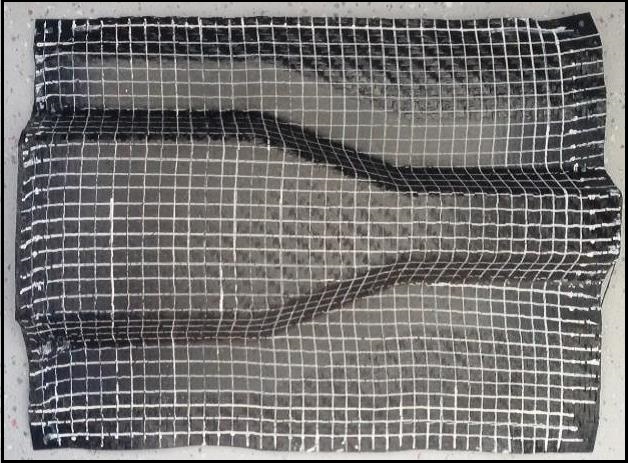
Over the last 30 years the usage of fiber-reinforced plastics (FRP) composites have grown due to their lightweight properties and structural performance. Still, there remain significant manufacturing challenges to overcome and predicting structural performance often remains more of an art than a science. Consequently manufacturing of composites is often costly and time consuming involving significant trial and error.
Assessing Product Performance
The development of composite products has always been unique in that its form always follows its function. It is no surprise then that virtual simulation of the design and physical performance of composites has been essential to the growth of its usage. With our laminate composites and Fibersim solutions we have been meeting this challenge for some time now to predict a composite product’s performance.
Separately we are also able to physically test the manufactured composite part and correlate the test results back to the virtual predictions.
Manufacturing Challenges
However challenges have remained in the manufacturing process. The influence of the manufacturing process is visualized on top-down view of an Omega(Ω)-profile in the two figures below of thermoplastic composite sheets that have been stamped. In figure 1 we see the weft & warp fiber orientations are nicely perpendicular to one another. In figure 2 however asymmetric forces with asymmetric boundary conditions cause a deformation of the product, such that the fibers are no longer perpendicular. The resultant composite part has significantly greater shear deformation which affects the part’s structural performance.
Moreover, in most composites manufacturing the matrix undergoes a phase transformation from a liquid to a solid state. This transformation causes the material to generate residual stresses, which in their turn cause the composite structure to emerge in a deformed state (i.e. not as-designed) after manufacturing. During assembly, the manufacturer forces the composite component into the desired as-designed shape by mechanically fixing the component to a base structure, which puts a pre-load on the structure and hence affects the structural performance.
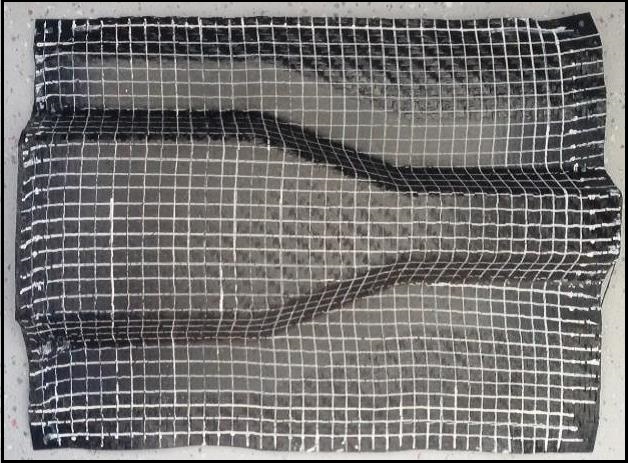
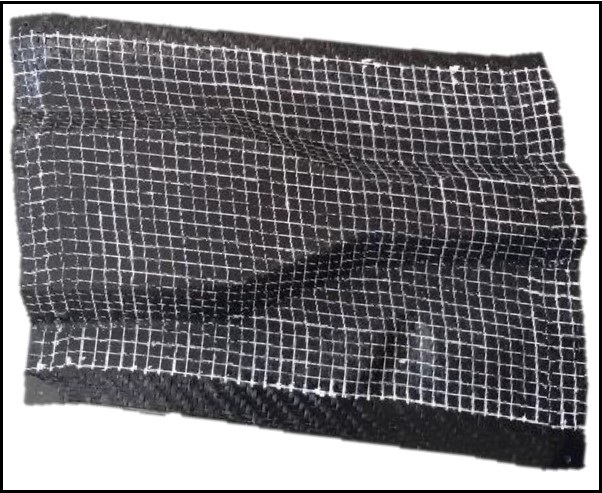
Simulating Manufacturing Process
Thus a second step in virtual simulation of composites parts has been to simulate their manufacture to predict and therefore compensate any deformation due to this process.
- Thus Fibersim can simulate the laminate composite layup by accounting for draping and drop off (scroll down to Producibility Simulation) to predict and avoid manufacturing-induced defects such as wrinkling.
- Within Simcenter 3D curing predictions (thermal and mechanical) can be performed to compute the distortion and taking into account the temperature variation across the part and the corresponding cure cycle. Given the integrated nature of simulation & design in Simcenter 3D the results from this simulation tallows for updating the initial mould geometry and hence to manufacture an as-designed composite component.
Closing the Loop
However a gap remains between the as-designed product and the as-manufactured product. Even if we can predict how a product’s design should be and how it should be manufactured, the next step is to predict the product performance and its impact on the manufacturing parameters and vice versa. Only then, can you virtually and simultaneously optimize the manufacturing process and product performance, thus closing the loop.
We were able to close this loop in partnership with with FlandersMake, KU Leuven, Borit, Bosal, and Noesis Solutions on a research project entitled Virtual Design Platform for Sheet Material Products (VIDESPRO).
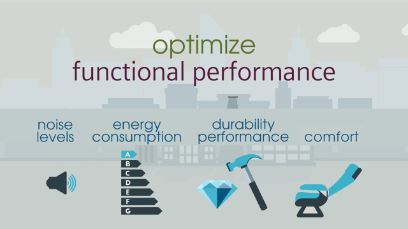
The key methodology to acheive this closed loop was through a process called functional performance engineering which is used to relate the product’s attributes to fundamental behaviours during the product development phase. Applying this process to manufacturing simulation enabled sensitivity analysis, optimization, and the assessment of the impact of manufacturing parameter uncertainties on the product performance.
With the closed loop process, it becomes possible to fully acheive the lightweight potential of FRP composites for the automotive, aerospace, and other industries. By virtually refining both the product and its manufacturing process, the risk of failures are minimized (see prediction #4 to learn more). Moreover, the development time and costs can be reduced by avoiding “trial and error” approaches to optimize the manufacturing process parameters.