Transforming RAMS Engineering in the Aviation Industry: A Mission-Driven Approach
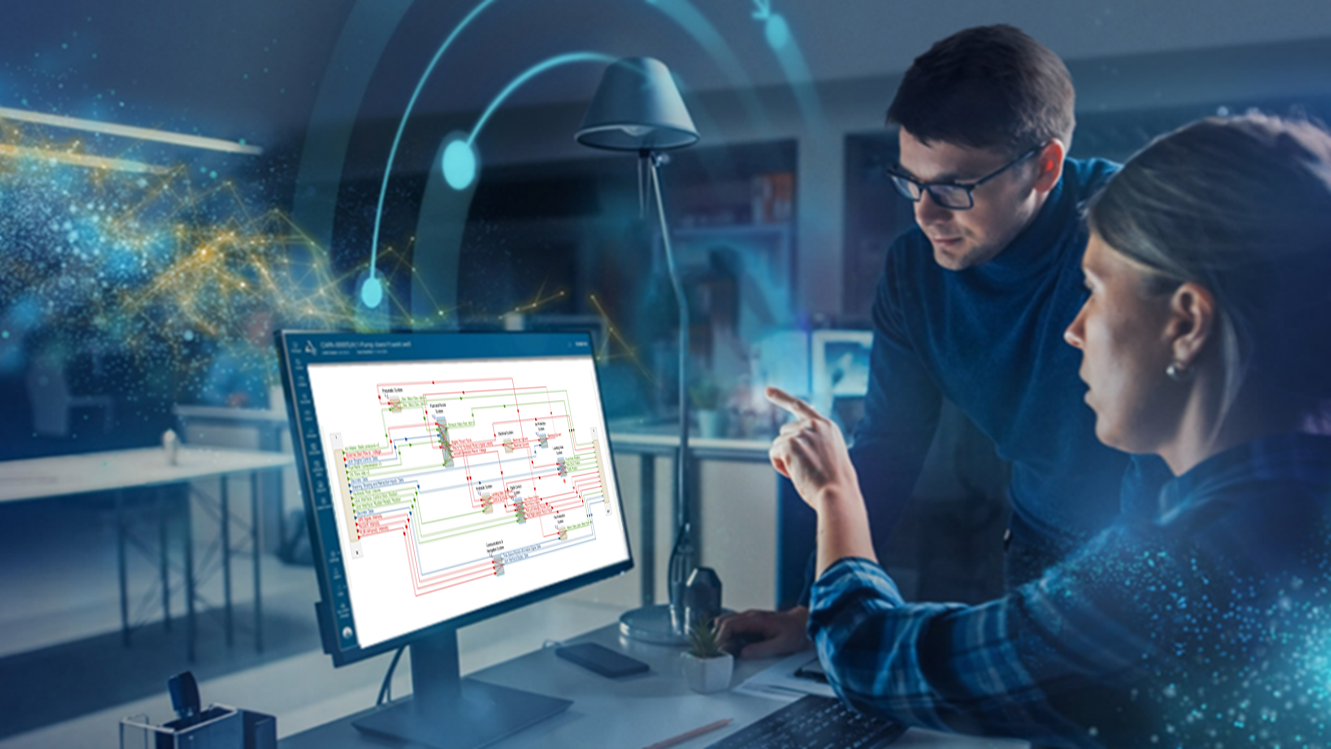
RAMS engineering is critical for the safe and efficient operation of modern aircraft. As an engineer or manager working on a new aircraft program, it is essential to prioritize RAMS engineering throughout the design, development process and operational phases. By prioritizing RAMS engineering, aircraft can achieve high reliability, availability, maintainability, and safety levels, ensuring a successful and sustainable operation lifecycle throughout the aviation industry.
Reliability
Ensures systems to work according to their intended function without failure. It involves identifying potential failures, assessing likelihood, and implementing design and maintenance measures to prevent them.
Availability
Ensures readiness for operation when needed. Involves maintenance procedures and spare parts availability to minimize downtime and maximize operational readiness.
Maintainability
Determines ease of servicing or repairing systems. It involves designing for easy maintenance, optimizing procedures, and ensuring proper training for maintenance personnel.
Safety
Physical injury or damage to people’s health due to hazards is still the top priority in the aviation industry. It involves identifying hazards, assessing risks, and implementing redundancy and safety procedures to ensure safe operation.
Current challenges
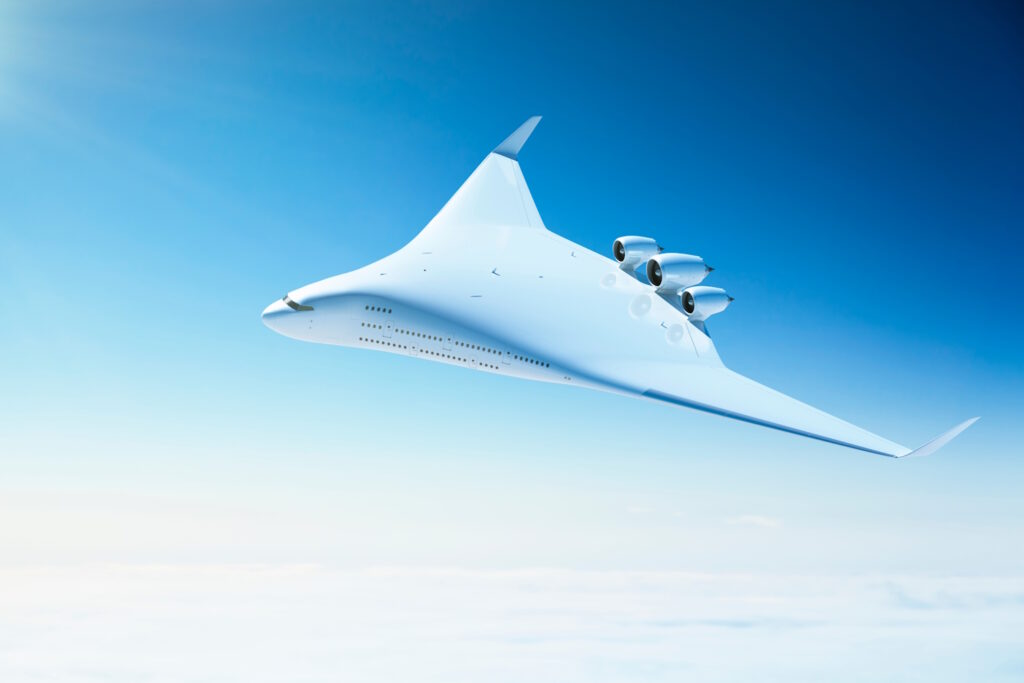
The modern aviation industry has witnessed a remarkable evolution in aircraft technology. Aircrafts today are far more complex than they were in the 1980s, with each new model raising the technical bar for everyone else in the industry. A case in point is the amount of software used in the latest jets from Boeing, Airbus, and others. Advanced systems and components are increasingly integrated to meet the ever-growing competitive expectations and demands of aerospace and aircraft manufacturers, Wall Street, airlines, and their flying customers.
Aircraft systems now consist of intricate networks of interconnected components with a critical software layer, making it more challenging to analyze and optimize RAMS effectively. All this complexity is a highly complex challenge to manage. Below are four key challenges:
Distributed development
The development and production of aircraft systems are often distributed across multiple suppliers and manufacturers. This decentralized approach introduces additional complexity as the coordination and integration of RAMS activities become more intricate. Traditional document-based RAMS methodologies struggle to adequately account for this distributed reality, leading to inefficiencies and potential gaps in data collection, management, and planning.
Scalability
Scalability is another significant challenge faced by document-based RAMS methodologies. As aircraft fleets expand and operators expect continual improvement, the volume of required documents, data and analysis can become overwhelming. Document-based approaches tend to be time-consuming and resource-intensive and introduce errors, hindering their ability to scale effectively with the growing demands of the aviation industry.
Information capture and management
The completeness of RAMS analysis can be compromised when relying solely on documents. It is challenging to capture and document every possible scenario, failure mode or interaction within complex aircraft systems—consequently, the risk of a critical aspect being overlooked or inadequately addressed rises. The static nature of documents makes it difficult to stay current on system changes and updates, further exacerbating incompletion issues. This can lead to gaps in understanding potential risks and inadequate mitigation measures, creating potential threats and harm to the safety and reliability of aircraft systems.
Analytical subjectivity
Document-based RAMS methodologies can also be negatively affected by the subjectivity of analysis. Interpretation and assessment of RAMS data can easily vary depending on the analysts. Analysts may have different perspectives, biases, or expertise levels, which can introduce inconsistencies and otherwise avoidable subjectivity into the analysis process. Additionally, reliance on manual interpretation of data and information from various sources can lead to discrepancies and errors that can affect the accuracy and reliability of the RAMS analysis outcomes.
A new path to improve RAMS
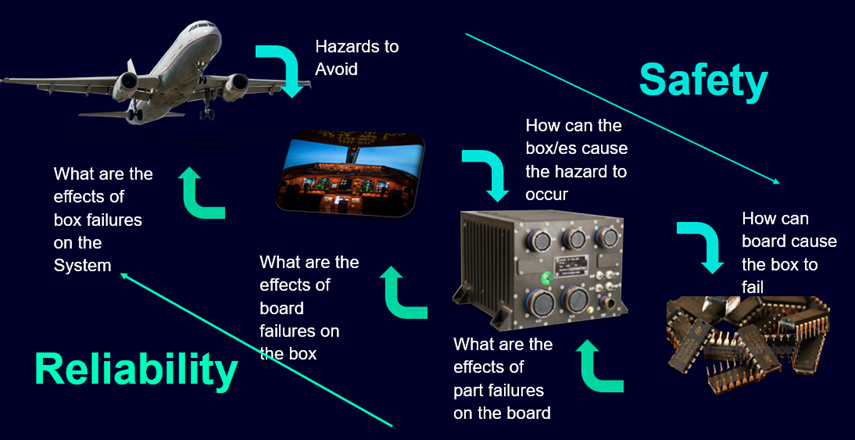
To overcome these challenges, a new approach is needed to embrace the benefits of mission-driven RAMS engineering. By leveraging advanced modeling techniques, this approach offers a comprehensive and integrated solution for tackling system complexity, facilitating distributed system development and production, and enabling scalability.
Mission-driven RAMS engineering provides a holistic view of the entire aircraft system, capturing the interdependencies and interactions between components, subsystems, and functions. Using models, it becomes possible to describe system failures according to taxonomy and libraries more accurately and efficiently and simulate the propagation of failures of the complete system.
Furthermore, these models can be continuously updated and refined during the aircraft’s lifecycle, supporting proactive decision-making, maintenance optimization, model updates and safety enhancements.
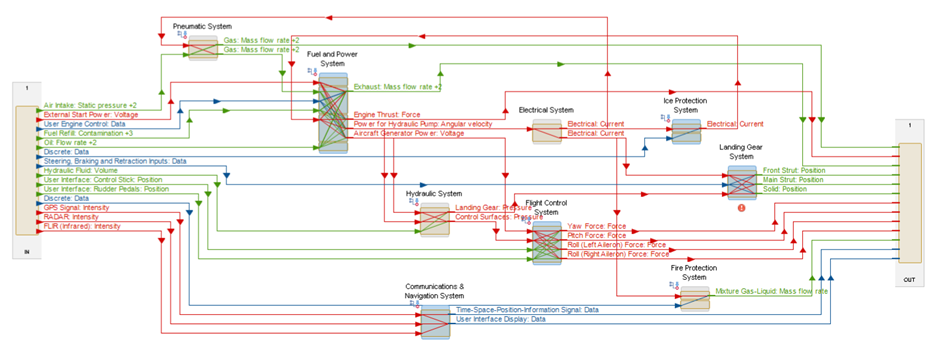
Benefits of mission-driven RAMS
An instantiation of MBSE RAMS is the DRT – Digital Risk Twin; it offers several key benefits that revolutionize RAMS for Aerospace engineering process:
Holistic system understanding
The DRT captures the interdependencies and interactions between components, subsystems and functions, providing a holistic view of the system’s RAMS attributes. This comprehensive understanding enables proactive decision-making and risk mitigation.
Objective analysis and optimization
The DRT allows for objectively analyzing RAMS parameters, identifying potential risks and enabling optimization strategies throughout the system’s lifecycle.
Integration of RAMS information
By integrating RAMS data within the DRT, MADE ensures that RAMS considerations are embedded into the design process from the early stages. It allows the automatic execution of RAMS analysis, such as Fault Tree Analysis (FTA) and Failure Mode and Effects Analysis (FMEA), leading to more robust and reliable system architectures.
Enhanced collaboration and communication
The DRT serves as a common platform for collaboration among multidisciplinary teams, with the ability to automatically generate standard-based reports, enabling seamless communication and knowledge sharing across the RAMS engineering process.
If you want to learn more about RAMS, check out these links:
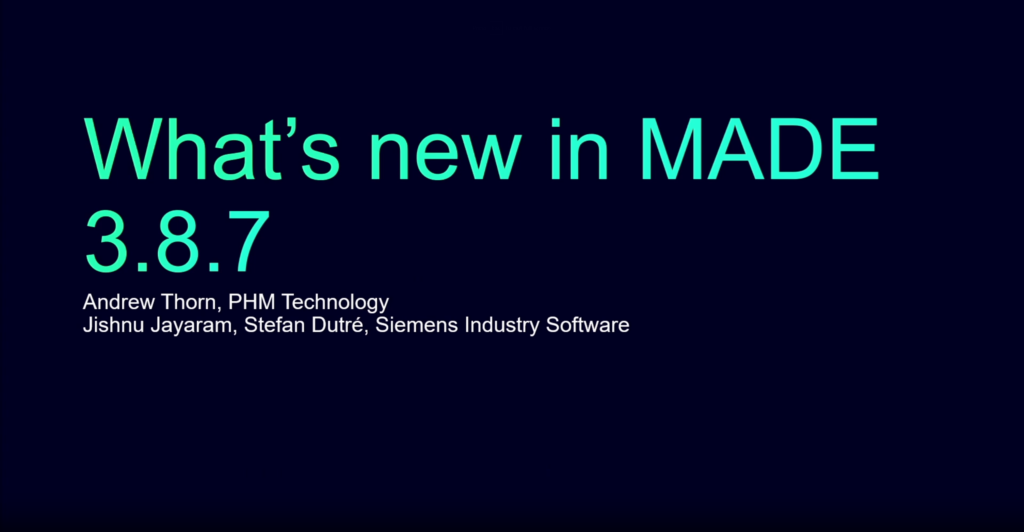
Blog
Model-based RAMS with MADE 3.8.7 – What’s new?
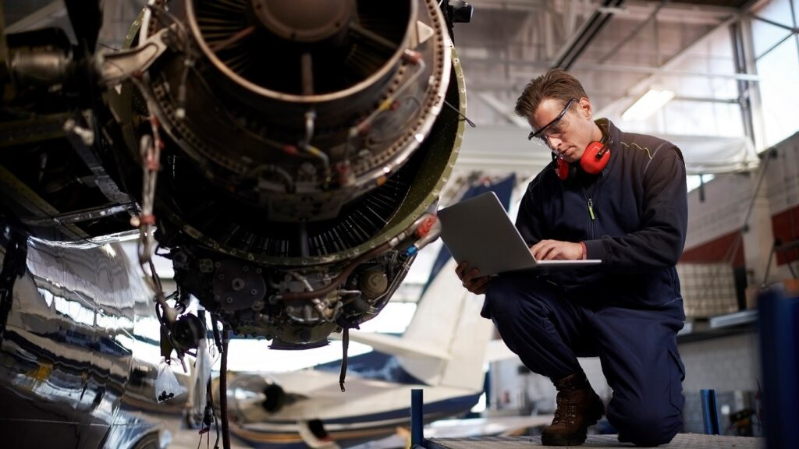
Blog
5 reasons aerospace companies need model-based RAMS
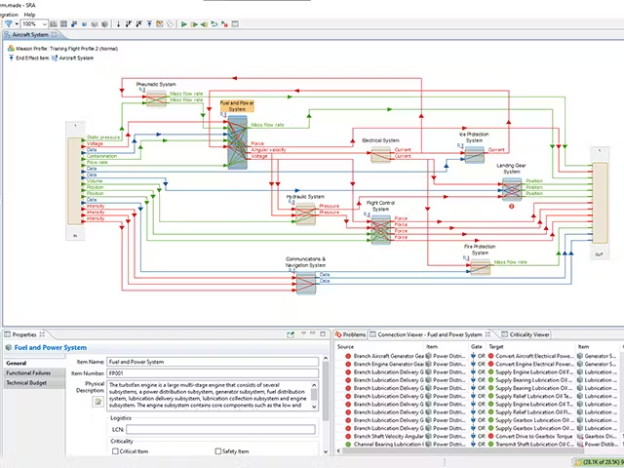
Website
Maintenance Aware Design Ecosystem (MADE)