Assessing composite variability’s impact on performance with virtual testing
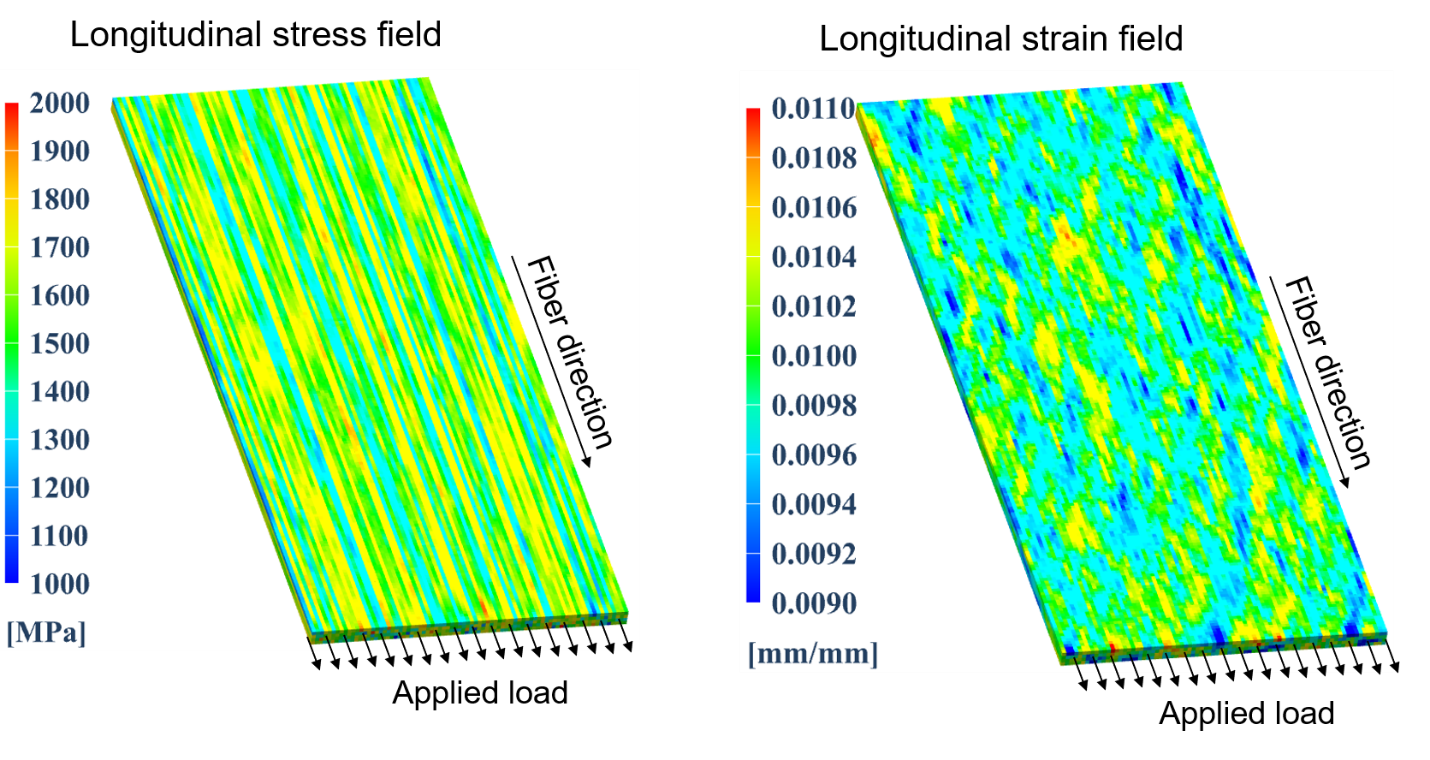
Statistics impact our world
One of Albert Einstein’s most famous quotes is: “God does not play dice with the universe”. This was situated in the days when Quantum Mechanics emerged, when Einstein was apparently eager to find another theory to describe small-particle physics that is not governed by statistics. Another angle at this is that Einstein mainly expressed with this quote how bizarre quantum mechanics is as a theory [1]. Whereas most of the universe is deterministic and measurable, the quantum world of tiny particles is governed indeed by probability, and quantum theory is very successful to describe the behavior of small particles in the quantum world, thanks to statistics.
How does variability affect manufactured products?
Most of the world on a macro scale is rather deterministic in nature, with the motion of a car, aircraft, … largely described with classical mechanics. I say largely, as a level of randomness exists in the properties of products, which has an impact on their behavior. For example, a range of identically manufactured vehicles show a variation in performance, e.g. body stiffness, noise and vibration levels, and durability. This is because there exists variability in the dimensions, material properties, connections, etc. of the car parts, that has an impact on the product performance.
Typically, in industrial product design engineering, a single deterministic nominal product is designed and evaluated, and safety factors or performance margins are adopted to ensure that the product behavior will also meet the targets in the presence of the real-life presence of variability. Computer Aided Engineering (CAE) design engineering tools are used for the deterministic product design, and Process Integration and Design Optimization (PIDO) tools, that can be put in a loop around the CAE tools to evaluate the effect of variability on the product performance. An example of a PIDO tool is HEEDS, part of the Simcenter portfolio. Deterministic design works rather well for metal products as cars, for which the variability is limited and its sources can be better controlled.
Higher variability in composite materials
The situation is different for composites, that are being used more and more by car and aircraft manufacturers, because of their weight (and hence fuel and emission) reduction possibilities, and ability to deliver favorable mechanical properties. Composites are subject to higher variability as compared to metals. This is due to their complex micro-structure, to the variability of the constituents (i.e. fibers and matrix), and to the manufacturing process. This means that one should design a component made of composite material, considering statistical variations between the components produced, which would not have identical performance. To do so, the designer can ensure that an entire population of components (rather than a single component) meets the design criteria.
Also, composites require that lower length scales in the simulation are introduced to be able to predict the properties and optimize the final product performance. This means that one should select appropriate methods which limit deterministic calculation time. The analysis of the effect of variability on the product performance requires a substantial number of simulations. This blogpost will explain how variability analysis of composites has become a reality through the combination of multi-scale approach for the composite simulation and subsequent Monte Carlo simulation for the variability assessment.
Variability analysis of fiber-reinforced composites
Fiber-reinforced composites (FRC) are often used in high-end applications where the mechanical performance and the weight are crucial design requirements. Despite these favorable strength and lightweight characteristics, it should also be said that FRC have a heterogeneous nature and a complex mechanical behavior. The variability of the material performance is such that the material properties should be described with statistical distributions rather than deterministic values.
For the design of fiber-reinforced composites, traditionally the product manufacturers rely on testing to validate the performance of the design and iterate where needed.
Even for a nominal design, the proper mechanical characterization would require a high number of experimental tests to obtain statistical distributions of the properties. This, however, is not always possible due to cost and time required. As a result, to guarantee the robust product performance, the designer typically introduces large safety margins to compensate for a lack of knowledge of the material, limiting the lightweight potential of the composite component, and increasing the manufacturing cost.
It is now clear that the proper characterization of composite material is a bottleneck in the design phase of composite components. But what if this tedious process could be made cheaper by replacing experimental tests with numerical simulations? This calls for a new approach, that is presented in the remainder of this blogpost.
Virtual testing toolchain to evaluate composite performance
This blogpost proposes a non-deterministic virtual testing methodology to predict the mechanical response of unidirectional composites and their variability. The method is based on Finite Element Analysis of virtual composite coupons. Its multi-scale formulation incorporates modelling of the material variability, which is always present in reality. Monte Carlo simulations are automatically run for many virtual composite coupons. As such, distributions of mechanical properties can be obtained virtually on a very large number of samples, which would be impossible in real testing. An overview of causes of variability in FRC composites and an example virtual testing result, are both shown in Figure 1.
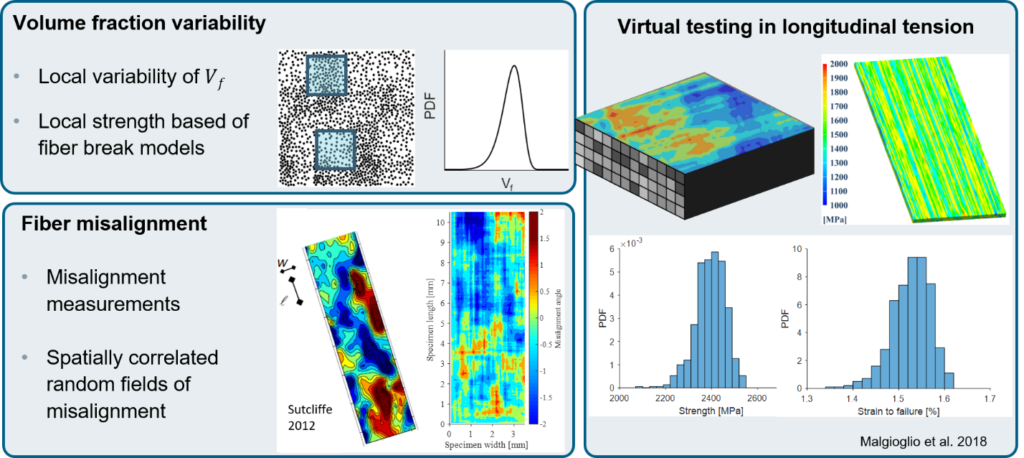
From left to right, the toolchain includes the material properties and material variability from the micro-scale up to the ply scale. On the micro-scale (left), there’s variability present in the local fiber volume fraction and the properties of the constituents (fibers and matrix). The tensile failure of composites involves very complex micro-scale phenomena. To take them into account, fiber-break models are used to predict the local strength of composite at sub-ply level. The local strength can be calculated either with a full Finite Element (FE) calculation [2] or with an analytical calculation [3].
Variability is captured, then used for analysis
The model of the ply consists of a finite element model in which each finite element has a unique set of mechanical properties and local material orientation. This enables the variability of the material to be captured. A value of fiber volume fraction is assigned to each finite element. The local material properties and local strength are calculated based on the volume fractions and on the calculations from the fiber-break model chosen. Local fiber misalignment is also introduced and assigned to each element as local material orientation. Random fields of misalignment are generated, taking into account the spatial variability typical of these materials. On the ply, Figure 2 shows the macro-level analysis: the calculation of the longitudinal strain field, due to an applied load in the longitudinal direction (in line with the fiber direction). A Monte Carlo simulation [4] is performed – repeating the deterministic analysis for a range of samples. In this way, statistical distributions of strength are obtained.
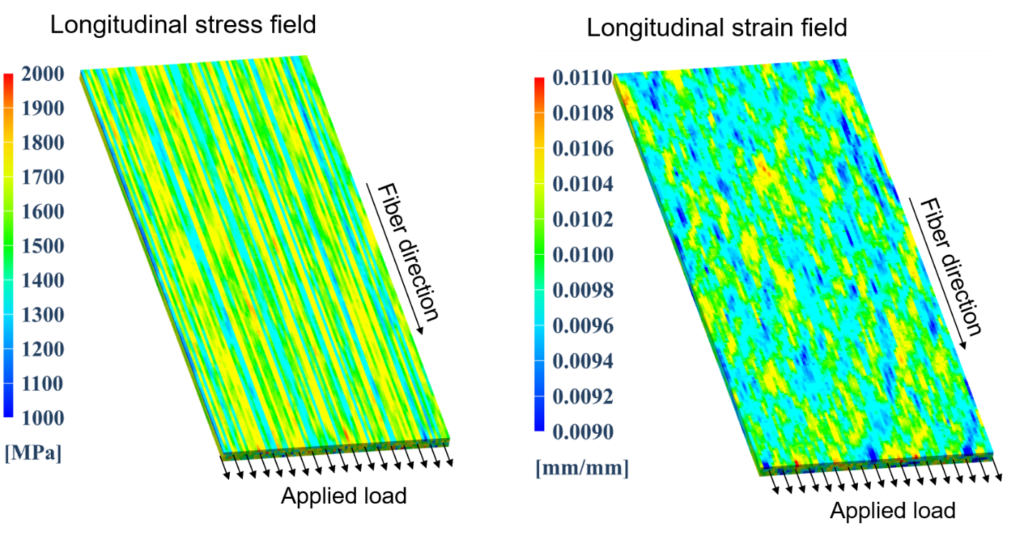
Accelerating the material design process with Virtual Material Characterization
The multi-scale approach explained in this blogpost conceptually aligns with the Virtual Material Characterization (VMC) approach [5], which was covered in an earlier blogpost. Siemens Digital Industries Software has designed the VMC ToolKit in Simcenter 3D for materials engineering of lightweight components. With the VMC ToolKit [6], the material design process can be completed with fewer tests, and then up-scaled to the component level via homogenization techniques. The multi-scale modelling workflow starts with the generation of a representative unit cell of a fiber-reinforced composite (in the size of millimeters). Subsequently, a detailed finite element (FE) model is automatically set up in Simcenter 3D and solved to obtain properties that can be homogenized for the entire volume which is representative for the studied composite material. The VMC ToolKit has been created in collaboration with several academic partners in the scope of the SIM M3 Program(1), using NX Open © to interface with key third party solutions such as the “WiseTex” suite for fiber-reinforced composites geometry generation (courtesy of KU Leuven, Belgium) and key methods such as virtual parameter identification schemes required to model composite damage (courtesy of Ghent University, Belgium).
Acknowledgements
We acknowledge the European Commission for funding the “FiBreMoD” project, which is part of the Horizon 2020 research and innovation programme under the Marie Sklodowska-Curie grant agreement No. 722626 (see http://www.fibremodproject.eu). In this project, Fabio Malgioglio is involved in an industrial PhD trajectory at Siemens, under academic supervision of Prof. Stepan Lomov (KU Leuven MTM), Prof. Yentl Swolfs (KU Leuven MTM) and Prof. Wim Desmet (KU Leuven LMSD) and under industrial supervision of Dr. Laszlo Farkas (Siemens).
The R&D activities of the FiBreMoD project in designing and modelling novel composite materials are shown online: https://www.youtube.com/watch?v=MyUF_CICc8s
Furthermore, we acknowledge the twin projects SBO & IBO “M3Strength”, which fit in the MacroModelMat (M3) research program, coordinated by Siemens (Siemens PLM software, Belgium) and funded by SIM (Strategic Initiative Materials in Flanders) and VLAIO (Flemish government agency Flanders Innovation & Entrepreneurship) (see https://www.sim-flanders.be/research-program/m3).
References
[1] K. Dickerson, “One of Einstein’s most famous quotes is often completely misinterpreted”, Business Insider, Nov. 19, 2015.
[2] Y. Swolfs, “Hybridisation of self-reinforced composites: modelling and verifying a novel hybrid concept”, PhD thesis, KU Leuven, Department of Materials Engineering, January 2015.
[3] S. Pimenta, S.T. Pinho, “Hierarchical scaling law for the strength of composite fibre bundles”, Journal of the Mechanics and Physics of Solids, 61, pp. 1337-1356, 2013.
[4] F. Malgioglio, F. Mesquita, C. Breite, A. Matveeva, L. Farkas, W. Desmet, S.V. Lomov, Y. Swolfs, “Prediction of tensile stiffness and failure of carbon fibre composite laminae: a multi-scale non-deterministic approach”, Proceedings of ECCM18, Athens, Greece, June 24-28, 2018.
[5] L. Farkas, K. Vanclooster, H. Erdelyi, R.D.B. Sevenois, S.V. Lomov, T. Naito, Y. Urushiyama, W. Van Paepegem, “Virtual Material Characterization process for composite materials: an industrial solution”, Proceedings of the 17th European. Conf. on Composite Materials, Munich, Germany, June 26-30, 2016.
[6] P. G. Catera, F. Gagliardi, D. Mundo, L. De Napoli, A. Matveeva, L. Farkas, “Multi-scale modelling of triaxial composites for FE-based modal analysis of hybrid metal-composite gears”, Composite Structures, Volume 182, 15 December 2017, Pages 116-123.
(1) Belgian R&D Program funded by SIM (Strategic Initiative Materials in Flanders) and VLAIO (Flemish government agency Flanders Innovation & Entrepreneurship), coordinated by Siemens Digital Industries Software, see http://www.sim-flanders.be/research-program/m3.