Simcenter Battery Design Studio
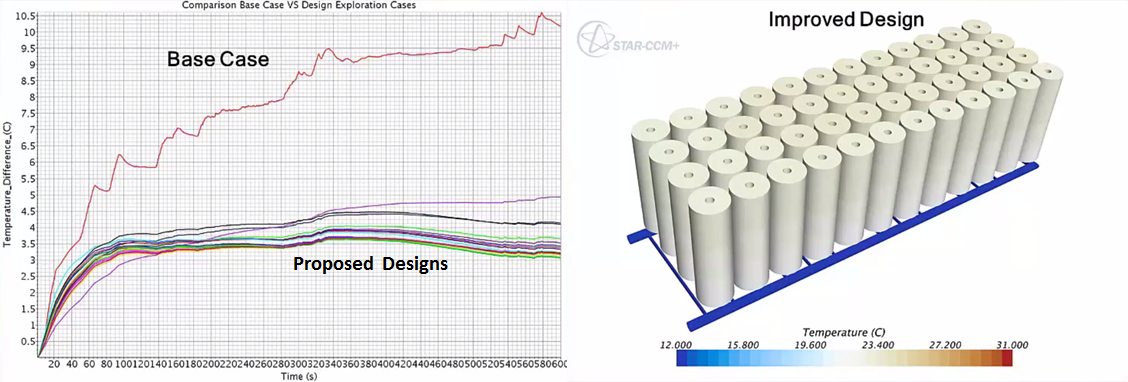
Nov. 2017 “The primary production constraint really, by far, is in battery module assembly“, Elon Musk said on a conference call with analysts after earnings were announced. “We had a subcontractor, a systems integration subcontractor, that unfortunately really dropped the ball, and we did not realize the degree to which the ball was dropped until quite recently” he added.
Thank you, Elon, for this introduction. Really appreciated as in the past five years now, we have understood several relevant points from automotive market electrification:
- Battery cell design and performance are key in mobile device development. Power, energy density, safety, aging, cost, each cell design choice might impact your position on a dynamic market.
- Solving an engineering difficulty is not a problem (as engineers we love problem-solving let’s be honest). Not realizing the coming difficulty is the issue. Though, use a performant modeling toll is mandatory to drive your decisions.
- Even if you master cell design, system integration & production must be addressed with the same importance.
Which means that battery cell designers teams must frontload impact of their engineering choices using extensive CAE simulation.
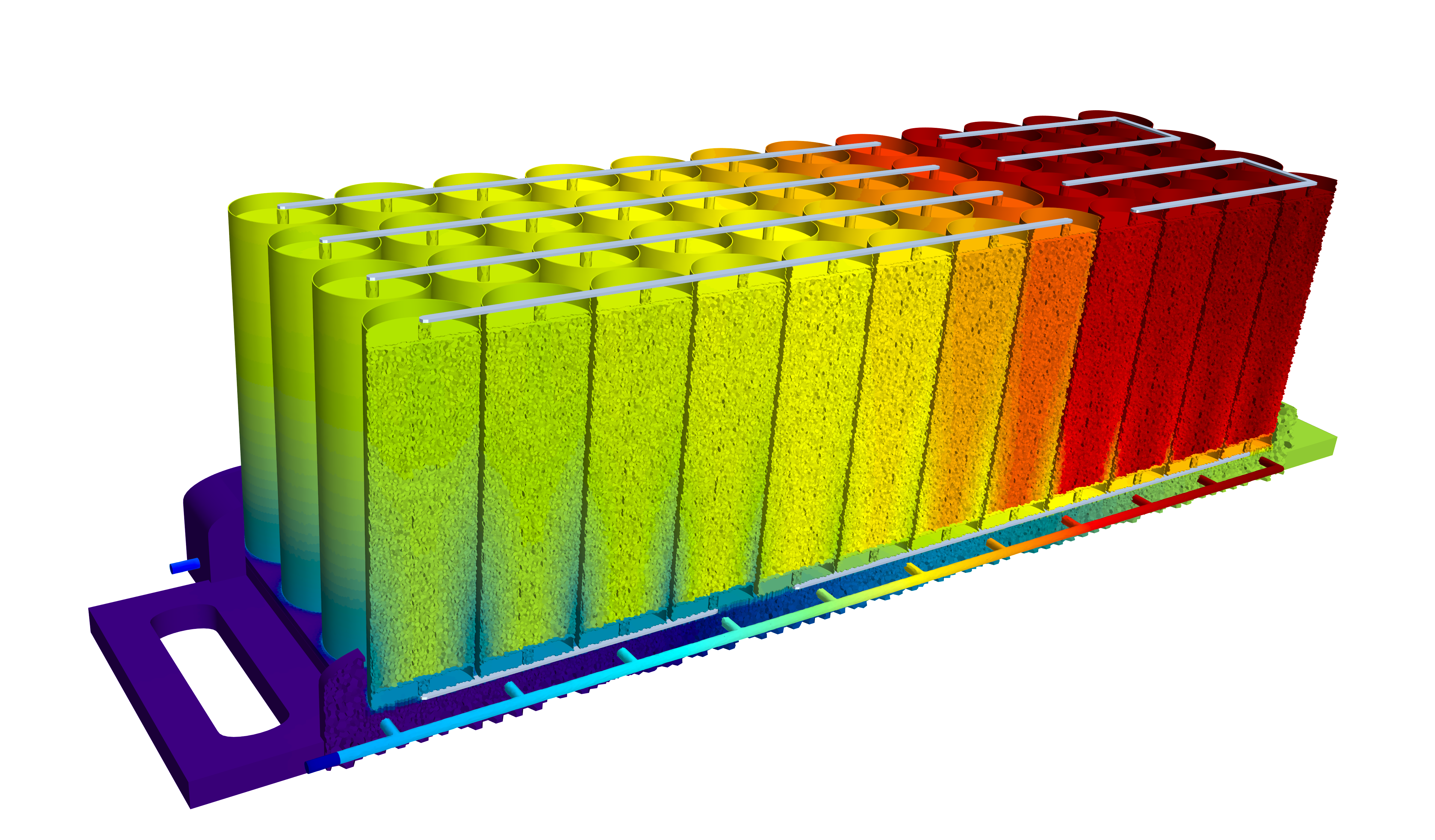
Simcenter Battery Design Studio supports engineers in digitally validate Li-ion cell design thanks to details geometrical cell specifications and cell performance simulation. Extensive components of a battery cell are available, as well as a material database to support the user in its model development.
Benefits and features at a glance:
- Physical cell description: seamless GUI with parametrizable templates available
- Integrally coupled cell design and model: simulate the impact of design changes on the cell performance
- Multi-physics software link: model export to Simcenter STAR-CCM+ via TBM file
- Design exploration: automatically optimize battery cell design and performance
- System level simulation: cell model characteristics export to Simcenter Amesim
Physical cell description
The first step in Simcenter Battery Design Studio is to specify cell components geometry and characteristics. Depending on your team responsibilities, those are either accessible, either provided by cell supplier or even obtained via component reverse engineering.
Simcenter Battery Design Studio provides standardized specifications for Li-ion battery components. The user can select cell shapes from a pouch, cylindrical or prismatic, then chose individual components, like electrodes, tabs, current collectors designs, etc. Each component can be more finely defined with characteristics such as center tab design for the electrode or control the material and thickness of the current collectors and the list goes on to fully build the cell.
When mixture formulations are usually known, exact values are often a guess at the beginning. But starting from the active material equilibrium voltage curves available from the literature or experimental characterization, the user can adjust the mixture to get a good fit to the low current discharge curve and so obtain a capacity correlation very accurate. Computed ‘Build Report’ can also be very helpful to validate your entries by for example checking final energy density or weight of the cell.
The user can also automatically generate a graphical output of the jelly roll section to review that the electrode winding is as expected.
Cell performance simulation
Simcenter Battery Design Studio offers several levels of performance models: a physics-based, macro-homogeneous model to get insights into the cell’s electrochemical mechanisms, such as the voltage loss mechanism during a cell’s duty cycle or understand concentration or heat generation distribution across the electrode; and an equivalent RCR circuit model, which is an empirical approach on modeling the cell’s behaviour in a very computational effective way.
Simulation can also tell us what is happening inside the cell in terms of distribution of potential, current density concentrated near tabs across the electrode.
Cell current density distribution for a 10A discharge
Then if you know me or my background as Siemens Engineering Services team, or if you read my previous post on Simcenter SPEED software, you know my next question. What is the real expected outcome of such a Model Based System Engineering approach? Answer: understand and so frontload impact of design choices on your system performances through your development cycle. Your tools should support you making the optimized feasible choice.
As an example, feel free to watch this On-Demand webinar about Silicon-Graphite cells in which Saft company shows how they use Simcenter Battery Design Studio to design a cell with high energy anode.
But not only your system. The interaction between parallel/series cell modules and surrounding elements part of the battery pack need to be considered too.
Seamless link with Multi-physics software
To do so, we usually advise our customers to use Simcenter Battery Design Studio to create an RCR empirical model to represent the cell voltage behavior dedicated then to 3D electro-thermal simulation of the pack. A physics-based model can be used, but an RCR empirical model will improve computational cost keeping a certain accuracy in your results and will be more suitable for non-expert users working at the battery module level. So, HPPC tests (discharge and regen pulses to characterize the resistance which depends on the cell SOC, temperature and current), either synthetic or from measurements are used as the inputs data and Simcenter Battery Design Studio automatically generate the RCR 3D empirical model parameters to be used for the 3D behavior model of the battery pack within Simcenter STAR-CCM+ in a very computationally efficient manner.
The link between both Simcenter Portfolio software mentioned above is done via a Simcenter Battery Design Studio output file, the Text Battery Model (TBM) file. The TBM file is used by the Battery Simulation Module add-on to Simcenter STAR-CCM+ to build desired battery module 3D model. By coupling the geometry, cell performance model and thermal solver of Simcenter STAR-CCM+, battery module engineers can run an electro-thermal simulation of the entire battery pack over transient scenarios.
The user can add other components part of the battery pack as the bus bars, electrical insulation pad, cooling channels and the battery casing (using STAR-CCM+ 3D-CAD or any third-party CAD software) and perform automatic meshing as well as specify material/coolant properties.
The final step will be to perform transient simulation over a duty cycle, or any kind of electrical current transient excitation profile function of the application domain. Here below an example of battery module temperature distribution results over a US06 cycle, at 25degC environment temperature and constant cooling pump speed.
Example of a 4P12S module with 18650 cells positioned on top an aluminium liquid cooling plate (not displayed here). The results show a large temperature gradient across the module which is the due to the inability of the cooling system to maintain a harmonised temperature distribution
The objective is to validate the integrated design and detect early in development cycle possible defects, undesired control behaviors or safety issue using this so to speak Multi-physics ‘Digital Twin’ of the battery module, without losing time during the hardware when issues could be discovered too late in the process.
Automated Design Space Exploration and Optimization
From these simulation results, engineers can start Design Space Exploration studies at the cell level, to maximize its capacity, for example, considering a fixed pack design but working on cell chemistry, or at the battery module level, working on its geometry and characteristics. These Design Space Exploration studies can be performed using Design Manager as part of Simcenter STAR-CCM+ as well as HEEDS software part of Simcenter Portfolio. This is what I call the Digital Twin Magic. Simulation engineer can semi-automatically, efficiently and safely explore hundreds of designs trying to balance multi-attribute performances as well as respect system constraints.
One can quickly identify that above battery pack thermal performances can be improved as the temperature is not well distributed over the battery module, certainly due to an inefficient coolant flow distribution, which will impact for sure electric performance of overheating cells and can even compromise cell lifetime or safety.
Here below a study example where we set-up our design exploration inputs, variables such as channel diameter, channel number, and coolant flow rate strategy. For the design exploration objectives, a cell temperature difference in jellyrolls lower than 2degC and pressure drop reduction were set. One can see below study results showing improved temperature homogeneity over the module.
Comparative temperature homogeneity results between base case and improved design over US06 driving cycle
Customer story: Samsung R&D Institute
A concrete example is a work performed by Samsung R&D Institute on the usage of Simcenter Battery Design Studio combined with Simcenter STAR-CCM+ to examine design decision impact on battery pack performance trade-offs.
Like other Li-ion battery manufacturers, Samsung R&D Institute is always looking for tools to support them in producing batteries with higher energy density and durability. And to do so they focused their effort on Thermal Management Systems optimization thanks to a coupled 3D electro-thermal model of the battery pack.
Empiric model parameter export to Simcenter Amesim
Simcenter Battery Design Studio RCR empirical model opens the capability to extract necessary parameters in order to set-up a system level battery model to be used within Simcenter Amesim software and so consider battery pack as an integrated component of a ‘bigger’ system: an electric wheeled vehicle, an aircraft, a powerplant or even a house smart grid.
Within Simcenter Amesim, the user has access to a Battery pre-sizing tool which will automatically configure your battery pack function of your cell characteristics (from Simcenter Battery Design Studio for example) and your technical requirements, as shown in this video.
The generated battery pack can then be used in the final system including other multi-physics components as electrical powertrain, thermal management system, electric board net, etc. and their controls. The objective being to predict cell/battery performances at the system level and frontload future interactions between the battery and its environment. Very useful simulation process to improve collaborative work between cell/battery suppliers and OEMs who will easily model, simulate and validate interaction between their products.