Wind turbine blade xDT wins JEC Award 2024 – Digital, AI & Data Category
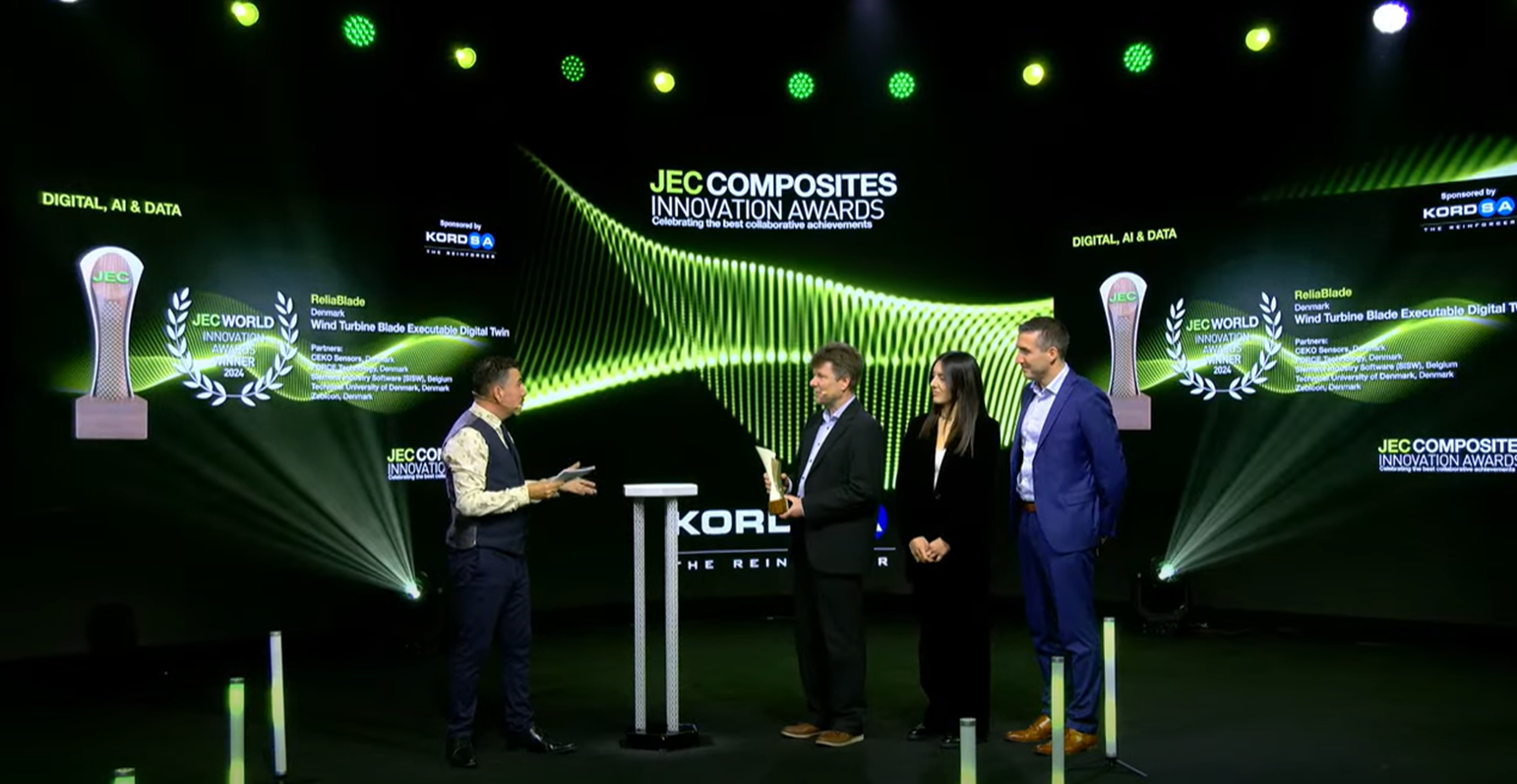
JEC Award winners announced
I was so thrilled to hear that the wind turbine blade Executable Digital Twin (xDT) developed in cooperation with the Technical University of Denmark (DTU) within the ReliaBlade project has been awarded the prestigious JEC Innovation Award for the Digital, AI & data category.
The JEC group is an organization promoting innovations in the field of composite materials. Established in 1963 and headquartered in France, the group is recognized globally for its comprehensive activities in promoting the use of composite materials.
JEC Innovation Award
The JEC Innovation Awards celebrate and promote pioneering advancements in the composite materials industry, highlighting groundbreaking projects and products which demonstrate the potential of composite materials. During last edition, the Digital, AI & data category award has been assigned to the ReliaBlade project for the outstanding work developed on the wind turbine blade xDT.
Back in February 2024, Kim Branner and Philipp Haselbach (DTU) and myself went to receive the award at the JEC Innovation Awards Ceremony. The technology had been showcased on a small-scale blade at the JEC World 2024, the biggest conference and exhibition in the composite industry.
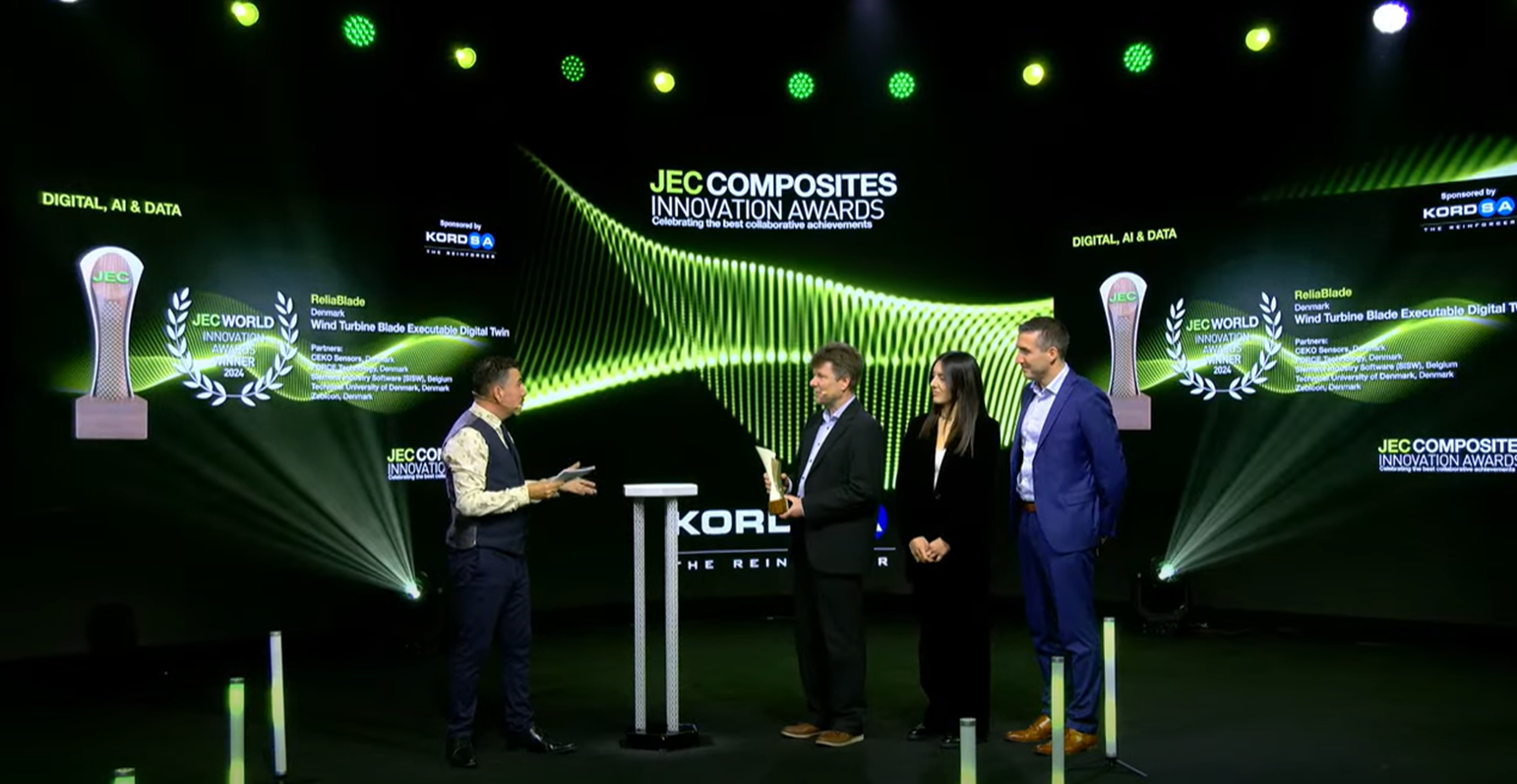
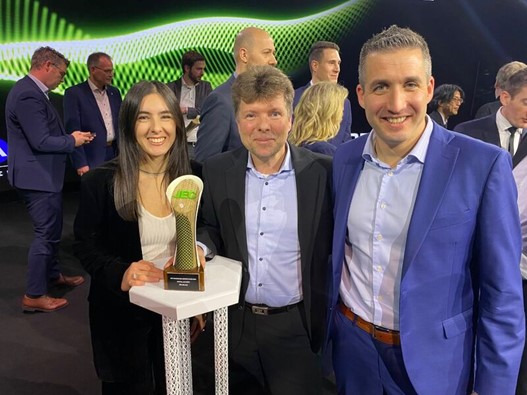
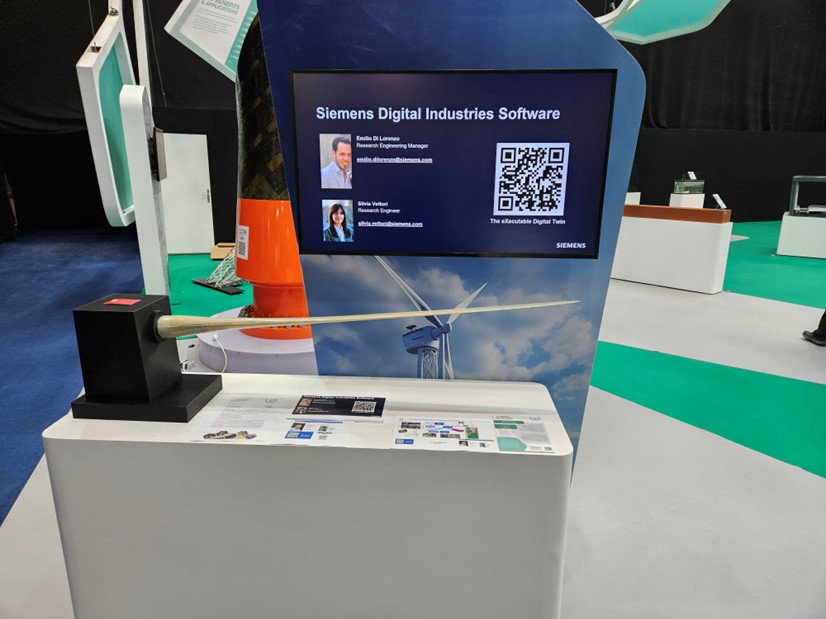
International joint research project
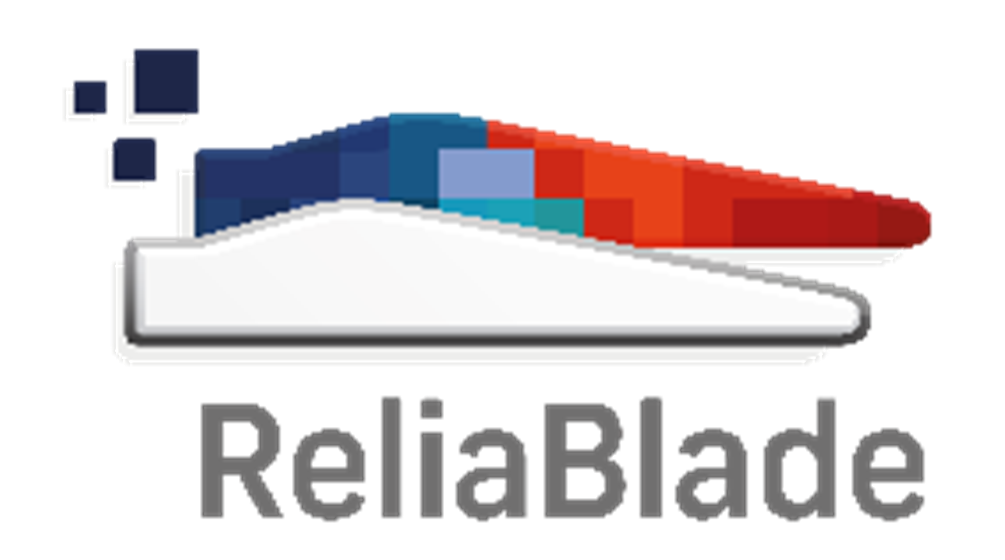
ReliaBlade is an international joint research project which has received national funding from Denmark and Germany. The project aims to revolutionize the wind energy sector by developing more reliable, efficient, and cost-effective wind turbine blades through use of Digital Twins. ReliaBlade develops and demonstrates techniques to create a unique Digital Twin for each individual wind turbine blade with their unique defects and imperfections.
Simcenter solutions used to enhance performance, reliability and efficiency
The wind turbine blade xDT, launched at the WindEurope Electric City conference (23-25 November 2021, Copenhagen, Denmark), is one of the main outcomes of ReliaBlade. This cutting-edge technology is the result of a close cooperation between Siemens and DTU Wind & Energy Systems. It relies on Simcenter solutions to create a high-fidelity and real-time deployable digital replica of a 12.6 m blade designed, manufactured and instrumented by DTU Wind & Energy Systems in the DTU BladeLab and Large Scale Facility.
The tool integrates a reduced order model and real-time data from sensors mounted along the blade to estimate the full-field structural response in real-time. The combination of physical and virtual sensors running in real-time during the operation of the turbine is key to perform Structural Health Monitoring of the blade behavior and to identify critical issues, thus enhancing their performance, reliability, and efficiency.
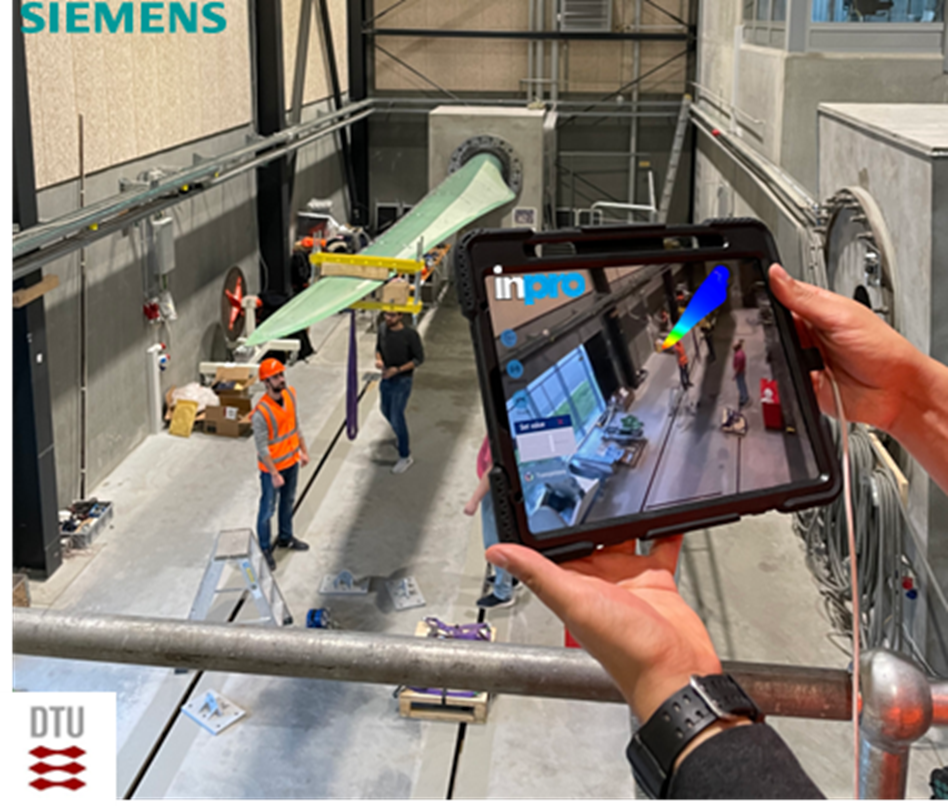
How was the solution built?
The blade Finite Element (FE) model has been developed by DTU and imported in Simcenter™ 3D, where the Smart Virtual Sensing (SVS) technology has been applied to overcome the limits of physical sensors by providing real-time response and load predictions. The SVS tool is used to build an xDT containing the blade Reduced Order Model (ROM) , the estimation algorithm and the indication regarding the available physical sensors as well as the virtual quantities to be reconstructed.
Measurement data is recorded via Simcenter SCADAS™ Mobile controlled via Simcenter Testlab™ and it is then sent to the Simcenter™ Testlab RT platform, where it can be combined with the xDT to build real-time virtual sensors. We can then visualize those real-time virtual channels in the Simcenter™ RT platform web-based GUI dashboard. The Augmented Reality (AR) functionality available in the Inpro Twino app has been adopted to build an overlayed visualization of the blade physical and Digital Twins.
Key benefits:
Being able to augment physical measurements with virtual sensors in real time allows us to predict blade reliability with much greater confidence, and this will impact may aspects of blade operation and maintenance:
- Live monitoring of blade deformations
- Live load monitoring and remaining life
- Predictive maintenance assessment
- Model error reduction
- Remote monitoring and health assessment
Watch the Winners’ interview
Watch the team receiving the award