The maritime industry is looking at electrification – stay plugged in!
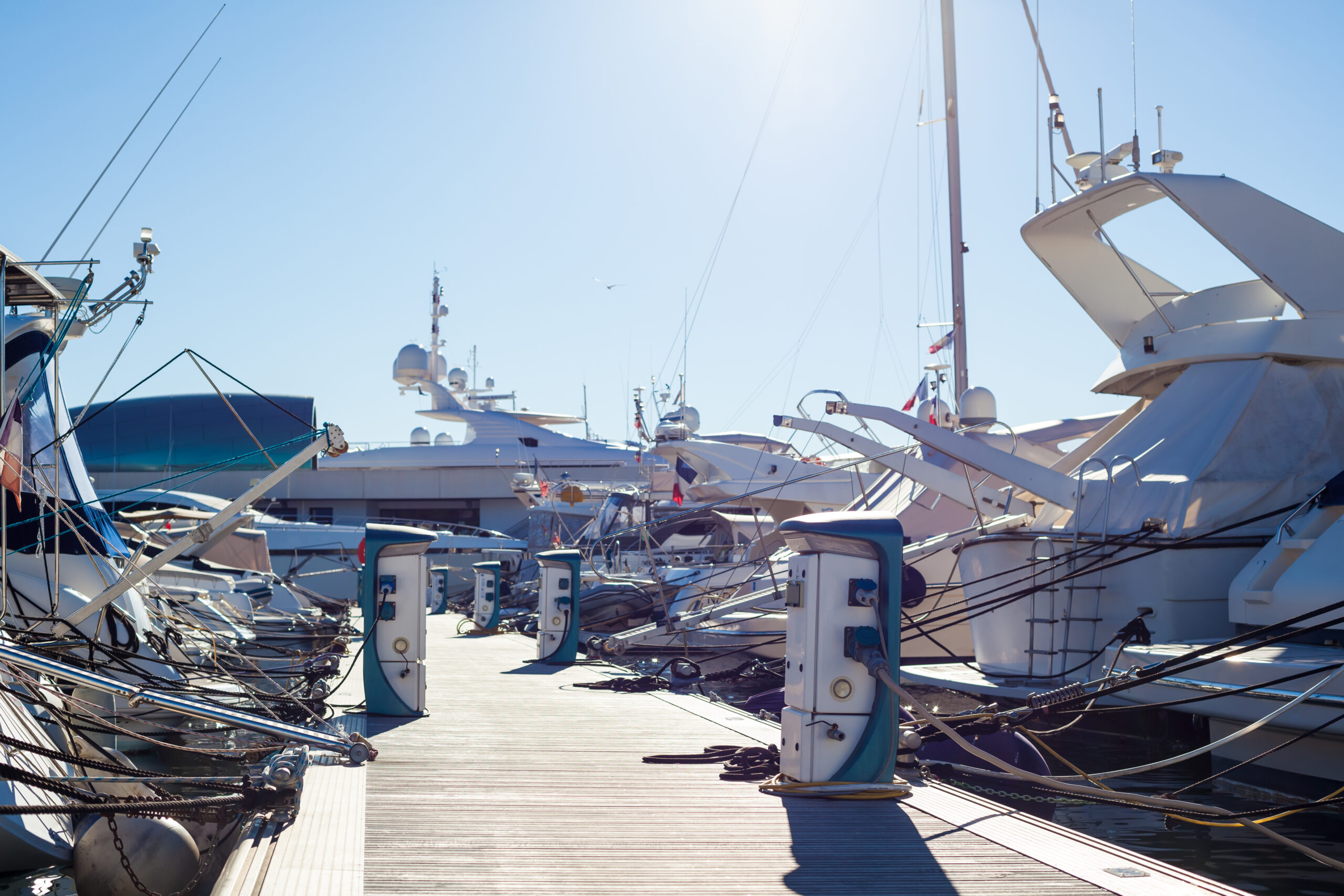
The maritime industry is challenged to reach net-zero emissions by 2050. To achieve this, the industry is looking at alternative fuel solutions to meet the environmental regulations set by the International Maritime Organization (IMO) in 2023. Today, the maritime industry represents around 3% of global pollution, and seaborne transport just keeps on growing.
Electrification is a top possible solution to this problem for vessels operating close to the shore. However, the market for electric ships is not as developed as for electric cars.
Indeed, fully electric ships are not expected to take a significant market share, except for smaller recreational boats and ferries. Bigger vessels rely on hybrid powering solutions, using liquified natural gas (LNG) or ammonia combined with batteries and electric propulsion for instance.
What does that mean in a more holistic view? Making a ship electric or hybrid isn’t as easy as changing the propulsion system and connecting batteries together. The keyword here is integration.
Leading industry players have long recognized the importance of sustainability and have taken proactive measures to align with regulatory standards. While some might perceive the adherence to sustainability regulations as a constraint, major groups view it as a significant opportunity. Collaborating with shipyards to develop electrified vessels marks an essential initial step. However, it is equally crucial to consider the operational side of the business. The charging infrastructure for these electric vessels becomes a pivotal aspect that cannot be overlooked. By taking a broader perspective on market changes, maritime companies are transforming themselves into not just ship owners but also port and terminal operators. This holistic approach allows them to fully embrace the evolving landscape and position themselves at the forefront of the industry’s sustainable transformation.
Easier said than done, right?
Of course, this doesn’t happen overnight. Earlier, we talked about integration.
A big concern today is also how to make ships more efficient than ever, especially energy-wise: consume less while performing at the utmost level.
With these two goals in mind, we need to acknowledge that moving toward full or hybrid electrification impacts the design of the whole ship, from systems through noise and vibration reduction to the hull form and propulsion.
We see a huge increase in fully digitalized shipyards to allow that complete integration. In 2020, semi-digitalized shipyards were the biggest industry segment. However, by 2028, fully digitalized shipyards are expected to be the fastest-growing segment.
By using both simulation and testing, shipbuilding companies can meet clients’ requirements faster while complying with regional regulations. They leverage digital solutions to optimize existing fleets and manage resources and energy consumption. Additionally, they enhance team productivity and reduce overall product lifecycle costs, enabling them to deliver faster time-to-market.
C-Job Naval Architects uses Simcenter to help electrify the European ferry industry
C-Job Naval Architects, an independent ship design and engineering company based in the Netherlands, heavily participated in the electrification of the European ferry industry. Let’s have a look at how they successfully achieved this using Simcenter solutions.
The Texelstroom

Built at the LaNaval Shipyard in Spain, the Texelstroom is one of only two ferries connecting Den Helder to the town of Texel on the Wadden Islands at the northern tip of The Netherlands. Run by TESO and owned by the sustainability-minded island residents and other ferry users, the Texelstroom can carry 1,750 passengers as well as 380 cars or 34 trucks and 261 cars. Its advanced energy management system includes energy-efficient propellers, over 700 solar panels and electric batteries.
Due to its remote and protected location, installing a charging infrastructure wasn’t possible. The Texelstroom needed to run all day/every day where the sea can get rough so just relying on electric power and battery operation wasn’t feasible.
C-Job achieved a groundbreaking milestone in the maritime industry by designing the world’s first passenger ferry to operate on a hybrid propulsion system that includes diesel and dual-fuel engines running on compressed natural gas (CNG). Using Simcenter solutions, C-Job created a digital twin for the electric ferry design, optimizing the number of onboard batteries and meeting energy-saving specifications without compromising passenger requirements. This collaboration exemplifies the successful integration of advanced technology to drive sustainable and efficient solutions in the maritime sector.
Electric ferries for Amsterdam
Following the Texelstroom project, C-Job turned its attention to the electric ferry project for the city of Amsterdam.
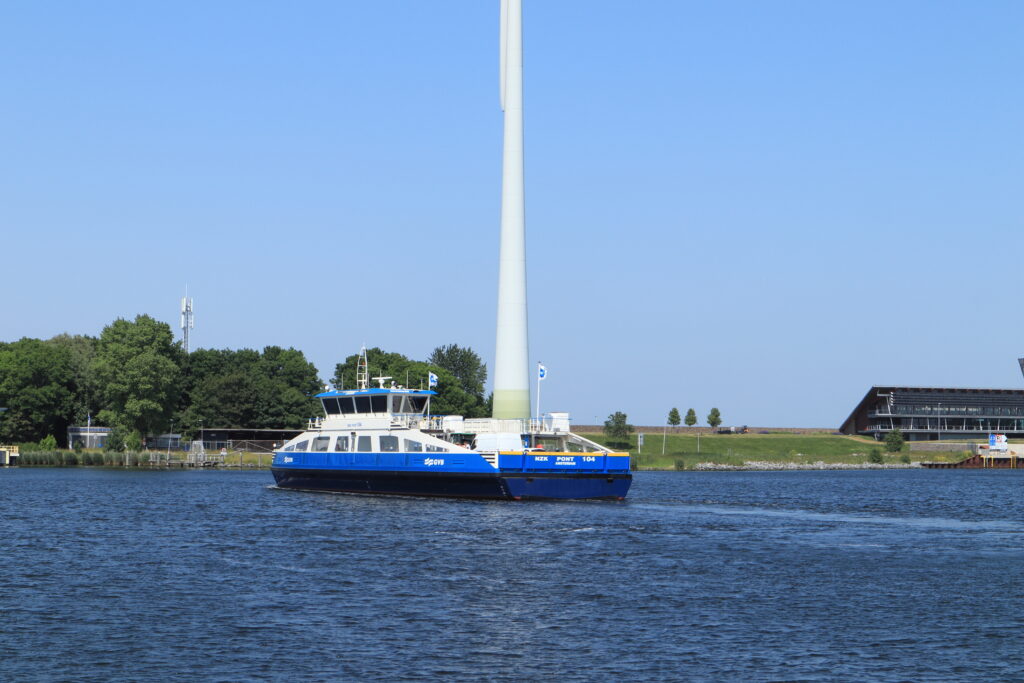
C-Job used Simcenter to optimize the design of a series of five fully electric ferries for Amsterdam. Operated by GVB, the city’s urban transportation provider, these vessels date back to 1930. With Simcenter, they focused on fast charging during loading and unloading stops, ensuring continuous 24/7 service. Simulation enabled C-Job to incorporate lightweight materials, flexible deck space, and a backup diesel generator for enhanced efficiency and passenger safety.
Saronic Ferries
Based on their history with electric ferries in The Netherlands, C-Job was engaged to work on a fully electric, zero-emission ferry for Saronic Ferries in Greece.
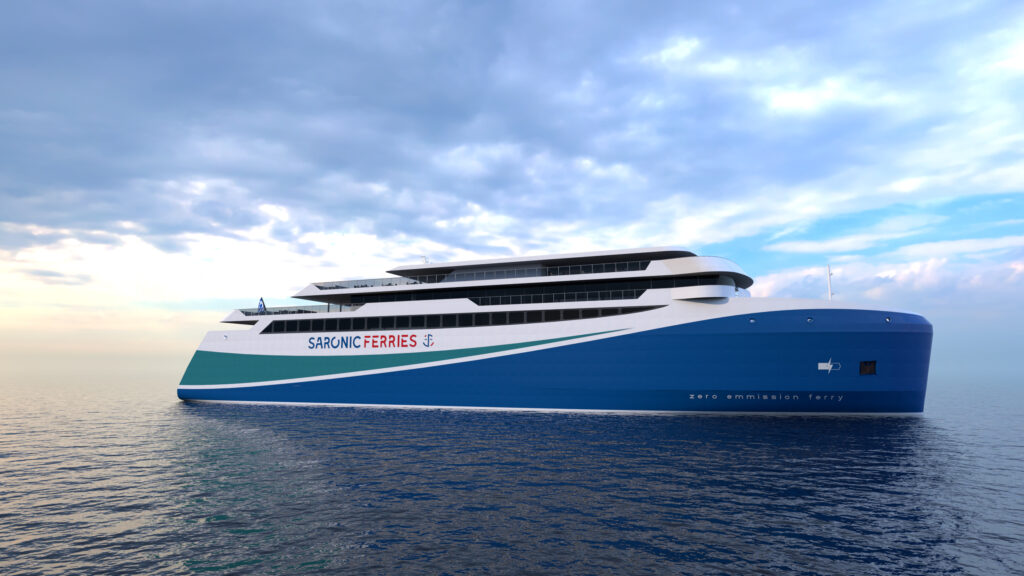
To meet the ship owner’s requirements for a fully electric solution, C-Job had to balance optimized onboard energy usage and sufficient battery power for the longer-haul ferry. With the help of Simcenter solutions, C-Job utilized an in-house optimization algorithm to test different scenarios and develop a digital twin for the final design. Simcenter’s simulation capabilities and the optimization algorithm enabled C-Job to optimize the number of onboard batteries and meet the energy-saving specifications while fulfilling the ship owner’s investment requirements and passenger ferry necessities.
Every vessel needs to be designed from the start with energy consumption and optimized propulsion top of mind. This was a lesson I learned in the early days of my Simcenter CFD work.
Filippo Iliopulos, Former Lead Naval Architect and Marine Engineer, C-Job Naval Architects
Join the movement to digitalization
Whether when developing a new ship or redesigning an already-existing ship, it is challenging to meet environmental regulations while delivering a vessel that ticks all the client’s boxes. The call for new power sources, innovative hull designs and the use of energy-saving devices poses new design and engineering challenges.
Which is why it is essential to introduce an integrated virtual simulation toolkit to maritime engineering, as it serves as a single source of truth in your digital journey, enabling the user to push the boundaries of vessel design.
A holistic digital twin can be used to support engineering efficiency when taking a conceptualization to detailed design. Simcenter helps connect the physical and virtual world, from initial to production design, maritime automation systems or engineering and consultancy services to support deployment. A multiphysics approach is key to integrating hydrodynamics, structural integrity, propulsion systems and environmental considerations.
You might also be interested in…
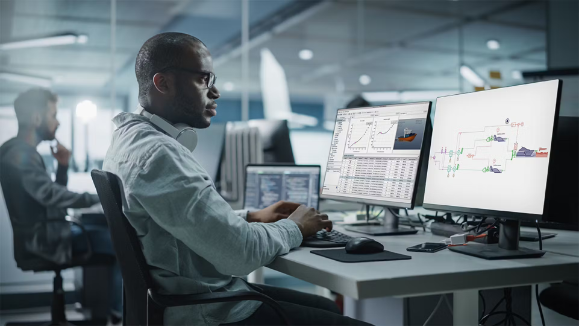
WEBINAR
Designing electric boats: leveraging simulation software