Hydrogen production, distribution and storage with Simcenter System Simulation – Part 2
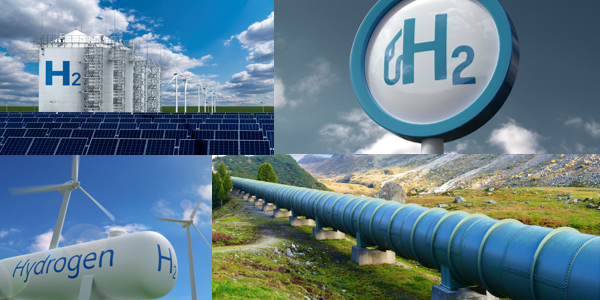
This blog post is the Part 2 of a blog series for addressing industrial Hydrogen challenges with Simcenter System Simulation. It’s focused on the Hydrogen production, distribution and storage. A quick overview is introduced in the previous Part 1 with explanations why Simulation is appropriate to address the Hydrogen challenges. Another Part 3 shows various applications for Mobility or stationary applications.
Well, let’s start with this statement: the Digital Transformation became part of every company’s strategy. But how do you create practical, realizable value from digitalization, that’s the key question to answer.
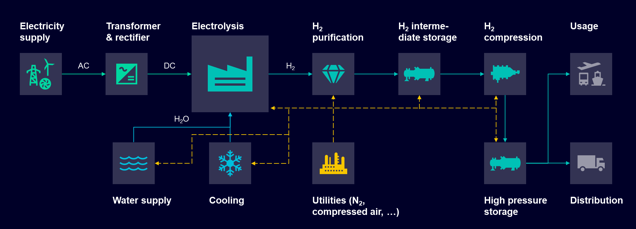
In this blog, let us explore how simulation helps to address the Hydrogen challenges from production to distribution and storage, i.e., everything ranging from compressors, pressure regulators, valves, electrolyzers, Balance of Plant (BoP) and system integration with renewables (solar photovoltaic, wind turbines, …), advanced controls, power electronics and grids. Up to Automation with PLCs (programmable logic controllers) or the energy mix regarding the energy price with trading aspects and weather forecasts. That’s a lot to manage, so the need for System Simulation to tackle all these challenges.
We’ll see how System Simulation enables the fast deployment and integration of sustainable hydrogen technologies. How it helps optimizing the design and operations of hydrogen production, also distribution and storage as key technologies to reach your targets. Hydrogen applications are no more non-discrete systems with continuous processes, but discrete systems reacting to events and advanced controls. The hydrogen applications switched nowadays to mechatronics systems!
While simulation is an important lever to minimize risk and keep project timeline and budget, the right tools for system simulation need to be used to get comprehensive digital twins. So that you can leverage your digital twins for efficiency, integration, and scalability to fully take benefits of your digital assets. Let’s demonstrate how powerful they are through a collection of hydrogen applications.
Green Hydrogen production with renewables
♻️💧⚡💰 For Green Hydrogen production, we can predict in few seconds the Hydrogen production over months thanks to wind turbines, solar panels, wave energy converters and electrolyzers to store energy in the hydrogen tanks. At the end, green energy is produced and it can be used for your plant facilities or production machines, or any usage like mobility (automotive, transportation, heavy equipment) so that your carbon footprint is significantly reduced.
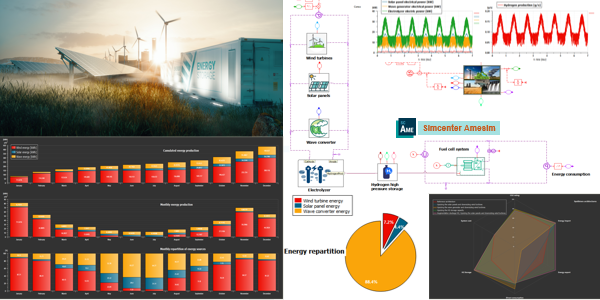
The model shown here predicts the performances of the system depending on the meteorological (weather) conditions and the localization of the system. Advanced post-processing and plots make possible to analyze energy and hydrogen production, or hydrogen volume in the storage system, month by month. After running quick simulations executed in few minutes for the complete 1 year (12 months), several architectures or component sizing choices can be rated to select the most efficient and profitable designs. What a valuable achievement!
Electrolyzers to convert green electricity into Hydrogen
To simulate the production of hydrogen, i.e. the conversion of the green electricity into hydrogen in Simcenter Amesim, the Proton Exchange Membrane electrolyzers (PEMEC) or reversible Solid Oxide Cell (rSOC) capable of operating either as a fuel cell (SOFC) or as an electrolyzer (SOEC), include predictive models based on electrochemical equations together with dedicated polarization apps.
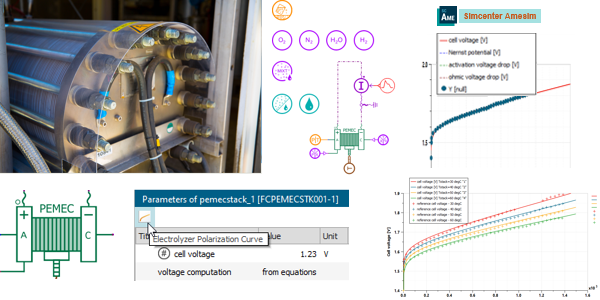
In combination with reformers (methane or methanol), these high-temperature components make it possible to address new challenges in the Hydrogen-related energy sector. Opening doors to high-efficiency systems (> 80%) when the waste heat is utilized.
As for fuel cells, System Simulation is fully appropriate for the integration of the electrolyzer component with its balance of plant (water supply system, H2 and O2 management system, heat/thermal management) or the integration of the electrolyzer within a larger system (renewable energies production, energy storage systems with batteries or other types of storage, grid, fuel cells, H2 dispenser, …).
Hydrogen components and Compressed Hydrogen Storage Systems (CHSS)
To reach the Hydrogen objectives, companies need the appropriate components (pressure regulators, valves, …), heat exchangers (including cooling systems or insulation of the tank walls for temperature control at various locations within the tanks), up to a detailed representation of the hydrogen tanks, which are not just equivalent volume chambers, but high technology components. The tanks for hydrogen applications are like the batteries for electric vehicles, they concentrate a lot of the value and challenges to solve (with temperature evolutions, wall insulation, weight, cost, safety, …) and they finally require a huge effort to fully understand how they behave.
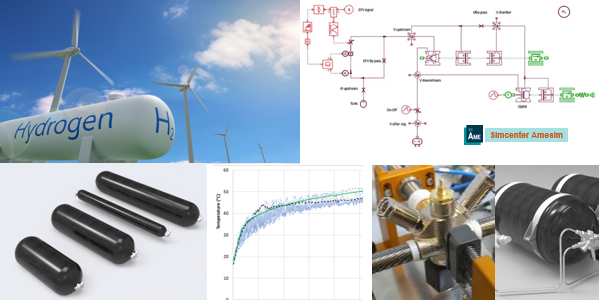
Compressed hydrogen tanks / storage systems (CHSS) typically operate at 700 bar with drastic changes in the temperature evolutions during operations. Let’s consider some key challenges to solve that are fully addressable with System Simulation to find out the best designs:
- 📈🌡 Refueling performances: time, temperatures, pressure, based on standard refueling procedures
- 📉💧 Defueling performances : range on existing driving profiles, temperatures, sensor behavior
- ⏱️ Maintenance operations: purge time estimation, leak test, etc.
- 🧪 Cycling tests : optimize cycling for normative tests or industrial processes
- 💥 Safety assessments: venting time, flame length, pipe breakage, potential leakage impact, etc.
That’s a lot to manage, and System Simulation can help there! Within few seconds of execution, System Simulation can provide metrics about any variables like pressures, temperatures, mass flow rates, power losses, efficiencies or energy saving, so it’s easy to investigate multiple scenarios.
Cryogenic hydrogen tank with LH2 (liquid), GH2 (gas) and BOG (boil-off gas)
✈️💧 In the aviation industry, the preference goes from GH2 (gas) tank storage for small aircrafts and short range to LH2 (liquid) tank storage for larger aircrafts and range. This choice is driven by the much higher energy per unit volume of the LH2 (liquid) tank storage compared to the GH2 (gas) tank storage.
LH2 (liquid hydrogen) is much more complex to manage since it’s obtained at extremely low temperatures such as -253 °C. 🌡 So that thermal insulation of the tank walls becomes mandatory to prevent the boiling of the liquid hydrogen (raising its pressure drastically), also as a side-effect the freezing of the external parts of the cryogenic tank. That’s where System Simulation can help to investigate the insulation performances (number of layers, composite/metal, …) or the refueling/defueling times to get relevant results in few seconds of CPU-time.
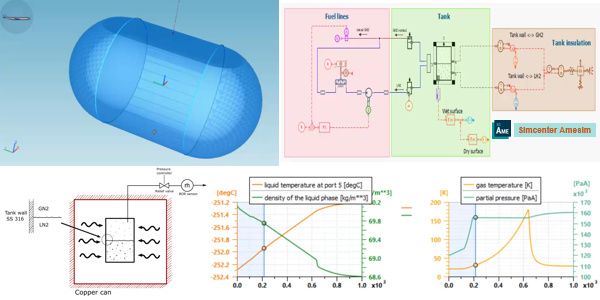
At some point, the discretization of the tank walls, and the inner parts within the fluid, with more complex phenomena (thermal stratification, buoyancy, …) are required to capture the physical phenomena to be well predictive. In the example above, the users define the 3D shape of the tank, then thanks to the thermal management (insulated walls, …), they can get the boil-off gas (BOG – evaporated vapor of hydrogen), so it’s finally easy to define the appropriate strategy to reuse the BOG for the fuel cell.
The goal here is to do the thermal management of the hydrogen tank and to take advantage of the already gasified hydrogen to supply the fuel cell with the necessary quantity of liquid at the targeted pressure. The control allows to bring the right amount of LH2 (liquid) for vaporization in an ideal exchanger. This exchanger therefore gives an estimate of the heat necessary to operate, while new thermal management system requirements can be derived from these results.
Cryo-compressed hydrogen tanks (CcH2) and cooling systems
Let’s now look at another technology for hydrogen tank storage with cryo-compressed hydrogen tanks (CcH2). They are used in some passenger cars. The concept of a cryo-compressed hydrogen (CcH2) storage is to combine the advantages of the gaseous (CGH2) and liquid (LH2) storage, namely loss-free operation and highest storage density.
Actually a big focus is put on the heat exchanges regarding the tank geometry, including the fluid and solid walls with natural and forced convections, as well as conduction in the walls. If needed, 1D-3D coupling can be done with 3D CFD to get more refined simulation for the tank heat exchanger and its temperature distribution all around the tank walls.
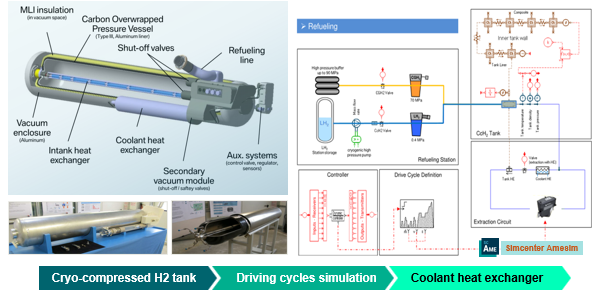
The model allows to implement complicated simulation sequences with repeated driving/refueling cycles until the fluid steady state conditions are reached after refueling. While the density is adjusted to the consumption, to get higher consumption rates with higher densities. On-top, some parahydrogen / orthohydrogen simulations can be implemented for complementary H2 isomers analysis to see the impact of the fluid composition.
Hydrogen transport with long piping networks
Looking at the global picture with the hydrogen transport, we can see it’s quite common to have long pipelines or piping networks for hydrogen distribution. Also for the water networks to go to the electrolysis plant, or for the natural gas networks to go the mixing station. These pipelines are long like several hundreds of meters or several kilometers. That’s why Simcenter Flomaster is appropriate for such investigations.
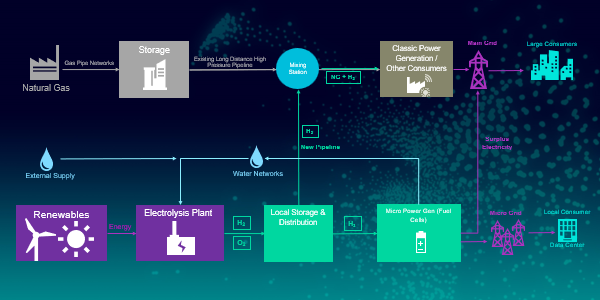
The first option for transporting hydrogen is in its naturally occurring gaseous state. This type of transportation is something the energy industry is already very familiar with thanks to the large network of natural gas pipelines around the world, but it is not without its challenges.
First is constructing the infrastructure, as pipelines can be expensive to build and are often difficult to get regulatory approval on for many reasons. Because of this, many pipeline operators are looking at how existing natural gas pipelines can be used to transport hydrogen. Whether new or existing, the design and operation of these pipelines is somewhere system simulation with Simcenter Flomaster can help by answering questions like:
- What size compressors are required to raise the pressure in a cost-effective manner?
- How many compressors should be added for redundancy?
- What size valves are needed to properly regulate flow rates?
- What diameter piping is optimal to efficiency minimize pressure drop but still give flexibility in delivery requirements
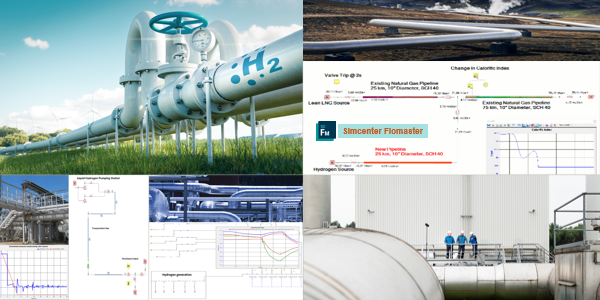
Another option for transporting hydrogen is as a liquid, such as in areas where pipelines aren’t available or not economical. Transporting hydrogen as a liquid allows for a much higher energy density versus as a gas but comes with its own challenges.
First is the need to liquify the hydrogen which means reducing its temperature to -253 °C. This is a very energy intensive process often using about 35% of the total energy content. Ensuring properly size pumps, heat exchangers, and piping during this process is critical to minimizing these energy losses.
System Simulation and Automation with PLCs
🌬️💧⚡Let’s switch now to another application of Green Hydrogen Production from renewable with wind turbines and PLCs (programmable logic controllers) to achieve the virtual commissioning directly in Siemens TIA Portal / PLCSIM Advanced. It’s nice to see here the benefits of Siemens product synergies, being able to couple Simcenter Amesim from “Siemens Digital Industries Software” (Siemen DISW) to the PLC S7-1500 from “Siemens Factory Automation” (Siemens FA), two well-connected entities from our Siemens organization.
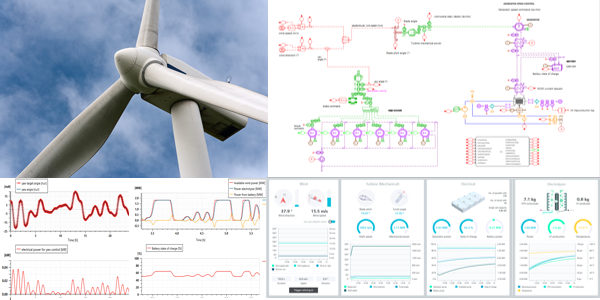
⏱️ It’s interesting to experience automation combined with digital twins. Knowing that when the System engineer and the Automation engineer develop the physical system and its software at the best, each one in their companies and departments, it doesn’t mean that at the end the complete system will meet the requirements 🎯. While the cost of modifications increases exponentially with time, so it’s clear that the errors on the hardware and/or software design need to be uncovered as soon as possible 💰.
🔗 That’s why when the System Engineer can create the virtual simulation model of the real system (i.e. the digital twin), he can immediately collaborate and share it with the Project Engineer to get more insights. On the other side, as soon as the Automation Engineer has completed the software development, he can directly connect the SIMATIC S7-1500 controller to the system simulation model using a dedicated interface. And at the end, the Automation Engineer can do a full virtual commissioning using TIA Portal & PLCSIM Advanced while the Automation Connect interface synchronizes the communication between the tools.
👏 This leads to a really concurrent engineering. And to great successes at the end. For performances, costs, but also for energy management and green hydrogen considerations. ♻️
Green hydrogen micro-grid with PEM electrolyzer
♻️⚡🔌 You can also go more at the electrics side, with this digital twin of a green hydrogen-based microgrid. The goal is to optimize the global system efficiency considering thermal management. You can check your power mix (solar, electrolyzer, fuel, cell, battery, …) over months. To finally verify that it’s compatible with the electric load, and that it can be supplied properly to the grid.
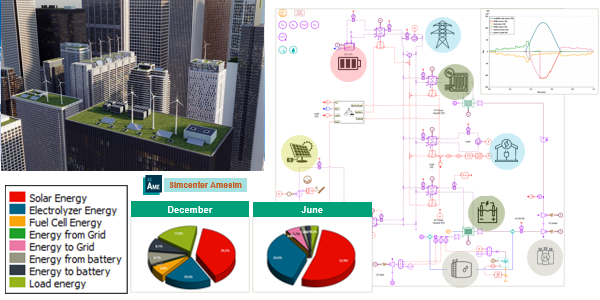
Just to say that System Simulation is perfect and well appropriate to reach nice achievements for sustainability in your company.
Everyone is quite impressed by all these capabilities to get great outcomes. But it’s not only during the product engineering process with “Simulation for Design” that you can benefit from our System Simulation capabilities to achieve your hydrogen goals. It’s also through the “Simulation in Operations” where practical significant gains can be reached directly onsite, close to the hardware devices.
Simulation in operations
The “Simulation in Operations” technique helps to leverage the simulation model built during the design phase to have insights during machine operation or in-services. Either with Edge computing or with Cloud computing.
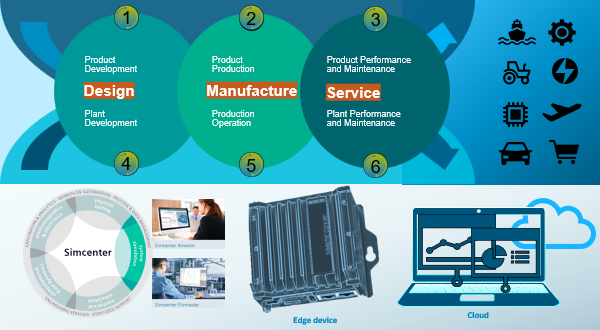
Here’s an example of « Simulation in Operations » with an Executable Digital Twin (xDT). It’s a wind turbine with Model Predictive Control (MPC).
The MPC approach embeds the physical plant models within advanced control strategies. Doing so, it allows predict in real-time the future behavior so one can benefit from the anticipation of what will happen next in a near future 🔮. The value is to combine software (controller) 🎛️ and hardware (plants) 🏭 onto a real system 🌬️ 💧⚡.
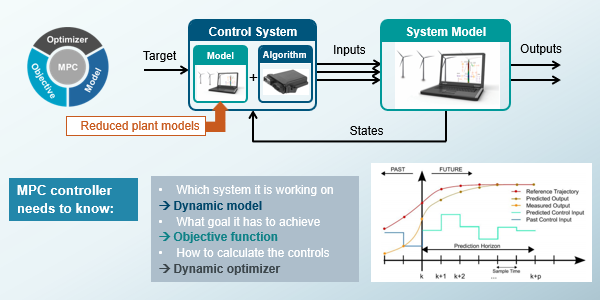
MPC (Model Predictive Control) is an advanced method that is used to control a process while satisfying a set of constraints. Model predictive controllers rely on dynamic models of the process. The main advantage of MPC is the fact that it allows the current timeslot to be optimized, while keeping future timeslots in account. Also MPC has the ability to anticipate future events and can take control actions accordingly.
One step further is to use Artificial Intelligence (AI) with Machine Learning (ML) and Neural networks to get powerful mathematical descriptions executed in few seconds, still being predictive regarding the physical phenomena to capture.
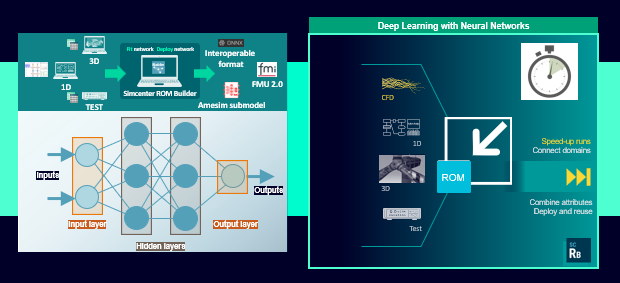
For example, neural networks can mimic the physical system behavior, which are intrinsically dynamic with transients depending on the operating conditions and variations in the inputs. Or the neural networks can at the opposite focus on the economic aspects to forecast the evolution of energy prices two days ahead or during the week depending on the weather forecasts. To ensure backup power, or to enhance the grid stability. This is really beneficial when green hydrogen production is directly used to supply hydrogen to factories, furnaces, green steel production or warehouses with some fleets of hydrogen fuel cell powered forklifts.
To conclude, we can extend the scope of System Simulation to help achieve your hydrogen targets, up to the complete Hydrogen value chain. It goes up to maritime port infrastructure and airport hydrogen infrastructure (with central shared production, liquefaction, apron trucks, cargo lift trucks, hydrogen refueling stations, …) to manage all these subsystems, needed and mandatory, around the main hydrogen applications of interest, which are the fuel cell powered ships or the hydrogen powered aircrafts.

That’s a lot to manage and System Simulation definitively helps there! To drive innovation and to take strategic decisions to transition your legacy plants or facilities to reach your hydrogen targets for carbon neutral operations. What a great objective!
Takeaways
It’s now time to sum-up the main benefits of using Simcenter System Simulation for Hydrogen.
- Capture more physics and go deeper in the design of components of the system such as valves, heat exchangers, compressors…
- Better evaluate the integration of the electrolyzer with fluctuating renewable energies, simulating the complete electrolyzer ecosystem: combining the electrolyzer model with a physical model of solar panels or wind turbines, with the integration of energy storage systems: batteries with BESS (battery energy storage systems) or others like hydrogen tanks …
- Evaluate and optimize virtually the controls, power electronics and grids
- Execute “Simulation in Operations” for services, up to trading aspects and techno-economic analysis (CAPEX/OPEX) of your hydrogen installations onsite.
If you’ve missed it, please read the Part 1 of this blog series to get a general overview how System Simulation helps being successful in your Hydrogen journey thanks to digitalization. Or read Part 3 to better understand how System Simulation is relevant for the Hydrogen usage in Mobility or stationary applications.
Learn more about Siemens Simcenter Amesim
Simcenter Amesim is the leading integrated, scalable system simulation platform, allowing system simulation engineers to virtually assess and optimize the performance of mechatronic systems.