It’s not rocket science, it’s system simulation!
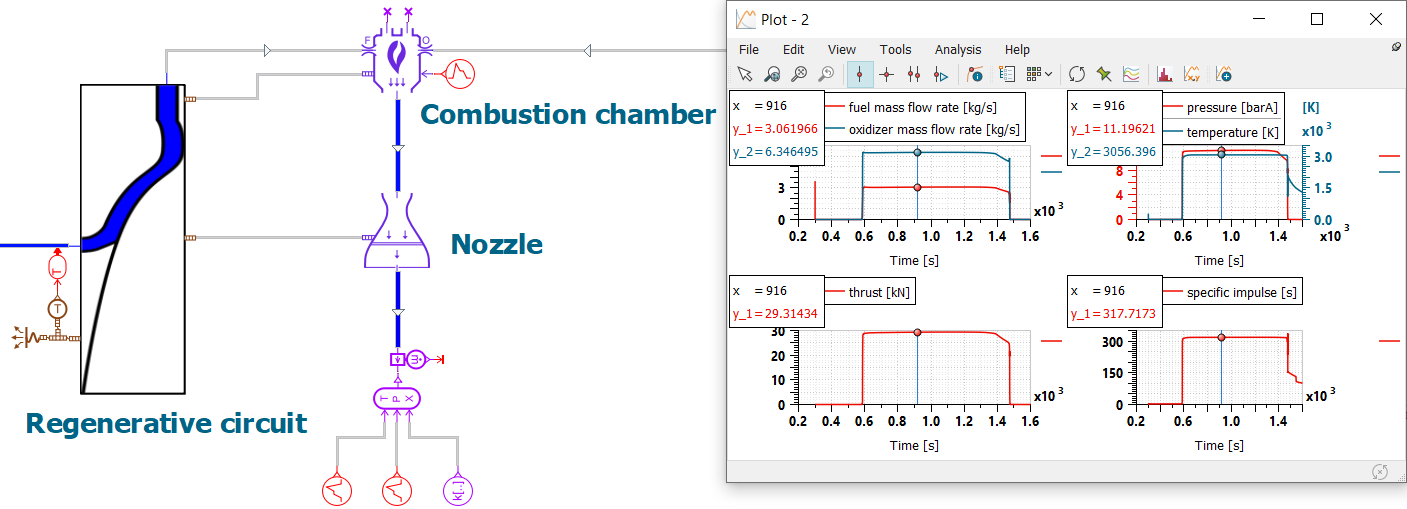
Rockets embody beautiful and fascinating engineering at its finest. Thanks to human ingenuity, they took us beyond our planet and they will take us even further in the years to come. Most modern rockets, namely those in the heavy-lift category, are complex machines embedding millions of lines of code controlling multiple systems and propulsive components (strap-on boosters, first stage and second stage). Each of these propulsive components serves a specific purpose at different times of the mission. They also provide different scales of thrust varying from millions of pounds for the boosters to a couple of thousands of pounds for the second stage.
One of the most critical part of the rocket’s mission is when it places the payload in orbit. That final daunting task is performed by the upper stage. This article will focus on how thermofluid system simulation can help assess the performance of a rocket upper stage and its components – from tank pressurization to chamber thrust computation.
System description
The results shown here are based on publicly-available data of the Ariane 5 upper stage.
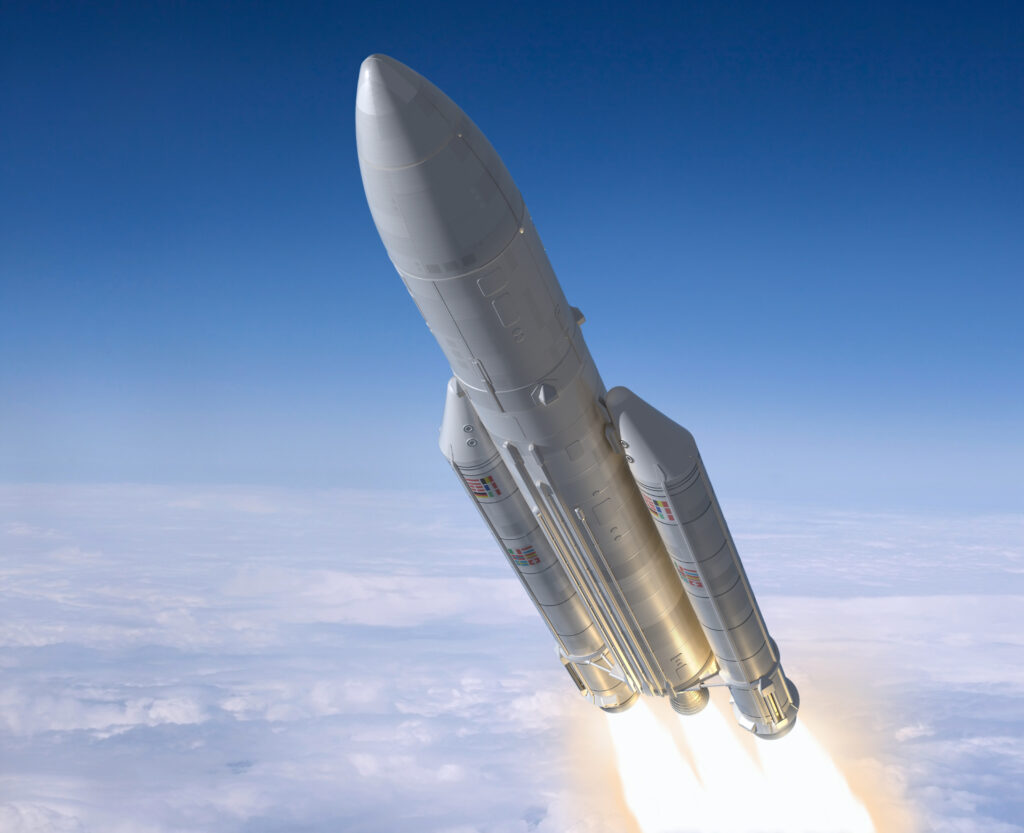
The upper stage (top part of the rocket) has an engine that ignites once the rocket reaches space (above 100 km of altitude) to thrust the payload to orbital insertion.
We can see below an extract of a typical mission profile of an Ariane 5 to get an idea of when the upper stage Aestus engine is ignited and shut down.
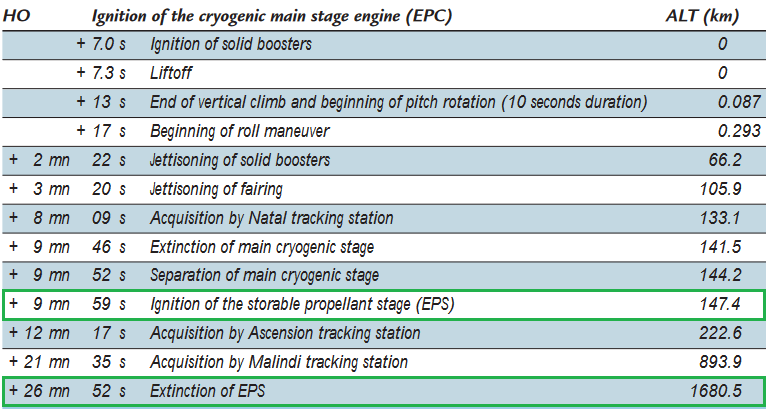
The upper stage main components are the engine (4) and the tanks and their pressurization system (3).
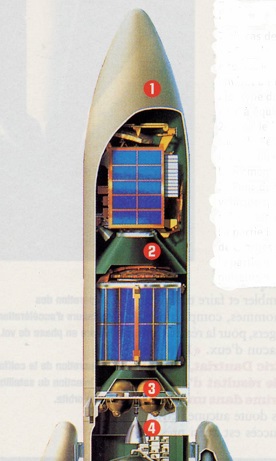
Modeling
This engine is a pressure-fed one so it has no turbopump, instead the propellant feeding system is pressurized using a helium tank. Monomethylhydrazine (MMH) is used as fuel and Nitrogen Tetroxide (NTO) as oxidizer.
To accurately capture the second stage performance, the pressurization gas (helium) and the propellants (MMH and NTO) need to be modeled with accuracy. Simcenter Amesim accounts for variable thermodynamic and transport properties and uses the NASA Glenn thermodynamic database. Using accurate gas properties for helium will allow here for a better assessment of helium pressure, temperature and mass.
Since version 2210, Simcenter Amesim also comes with predefined storable (non-cryogenic) propellants such as RP-1, MMH, UDMH, Aerozine-50, NTO and Hydrazine. Thanks to these fluid properties, propellant pressure and temperature in the tanks can be correctly assessed.
Thrust generation is the result of the combustion taking place in the chamber. This high-temperature combustion involves various phenomena like species dissociation. A chemical equilibrium code such as Caltech Cantera or NASA CEA has to be used to accurately compute species concentration during the combustion. The Simcenter Combustion Map Generation Tool is used to easily set up that chemical equilibrium computation process through a user-friendly interface.
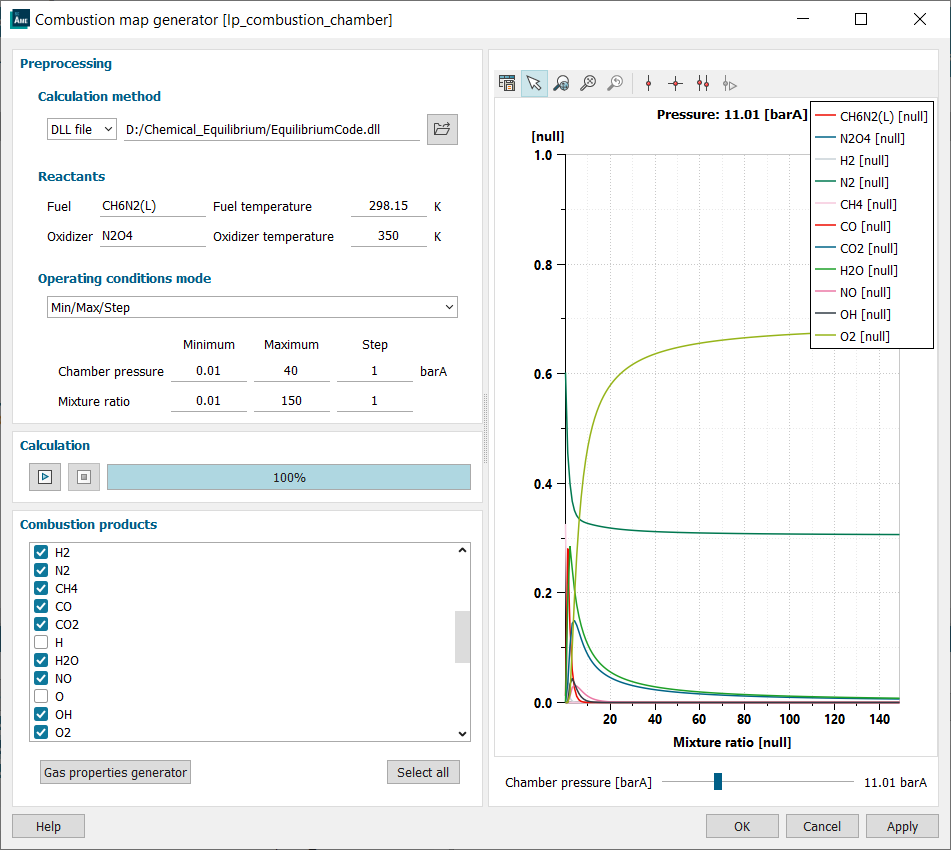
Results
Once we’ve set up the thermofluid simulation model of the upper stage system, we can run a transient simulation for a whole cycle of operation of the engine. Simcenter Amesim comes with a set of post-processing tools that allow for a very user friendly visualization of the results.
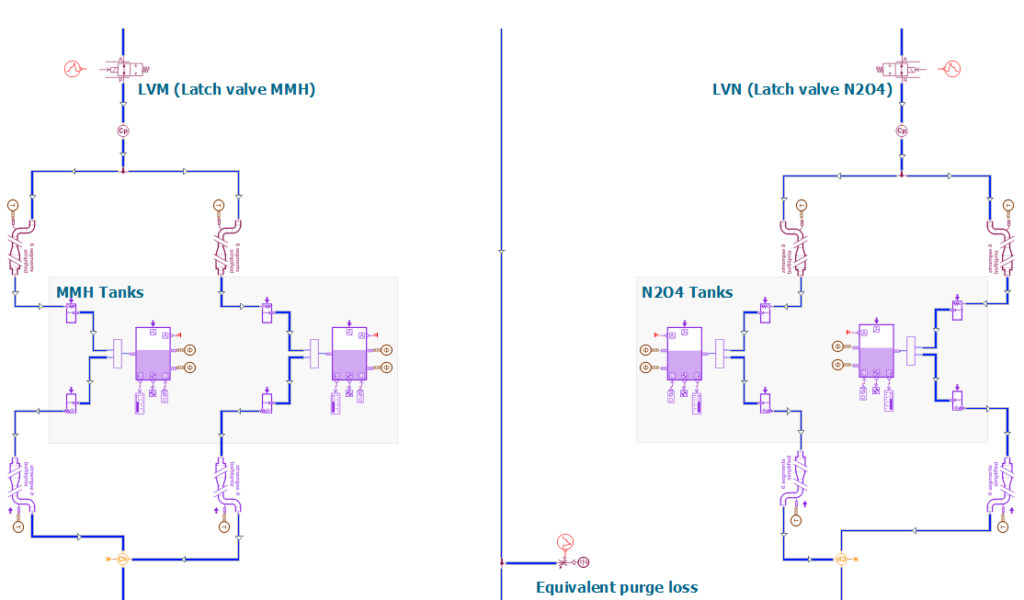
We can see above the fuel storage and distribution. Propellant level in the tanks can be monitored at any time of the simulation.
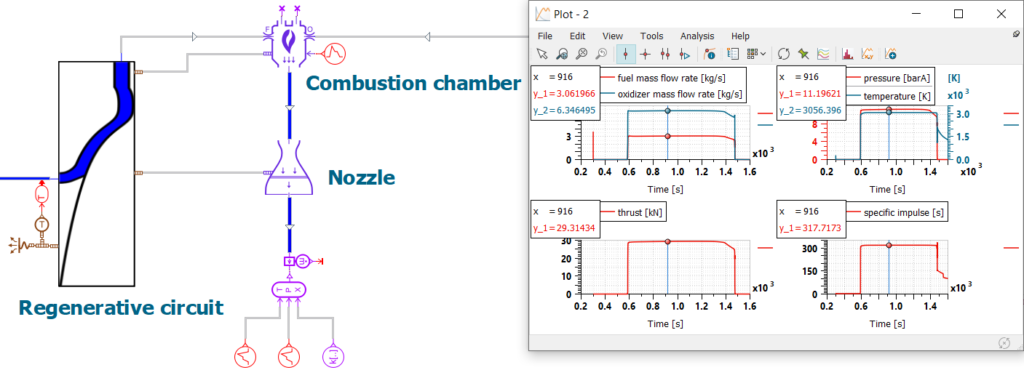
Propellant mass flow rates to the combustion chamber can be visualized and tracked at any time of the mission profile. The model also allows us to capture the impact of the opening sequence of various valves (oxidizer, fuel, purge gas) on the engine transient behavior. Key performance data such as chamber pressure and temperature, but also thrust and specific impulse can be assessed and compared with actual rocket performance.
Conclusion
This article showed how thermofluid system simulation can be used to assess the performance of a rocket upper-stage propulsion system. The transient simulation model obtained can be used to frontload not only rocket power balance but also start/stop and valve opening sequence analysis. That’s the value of system simulation: be a decision-making tool that helps you implement required design changes earlier in the development cycle.
About the author:
Djiby Touré is an advanced technical product manager for Simcenter Systems with the Aerospace, Defense and Marine product management team. His work focuses on electrical systems, clean aviation and rocket engine thermodynamic simulation.
Going further
- How to “How to assess the behavior of a rocket engine with Simcenter Amesim“
- Simcenter Amesim at NASA Thermal and Fluids Analysis Workshop (TFAWS) 2023