5 reasons aerospace companies need model-based Reliability, Availability, Maintainability and Safety (RAMS)
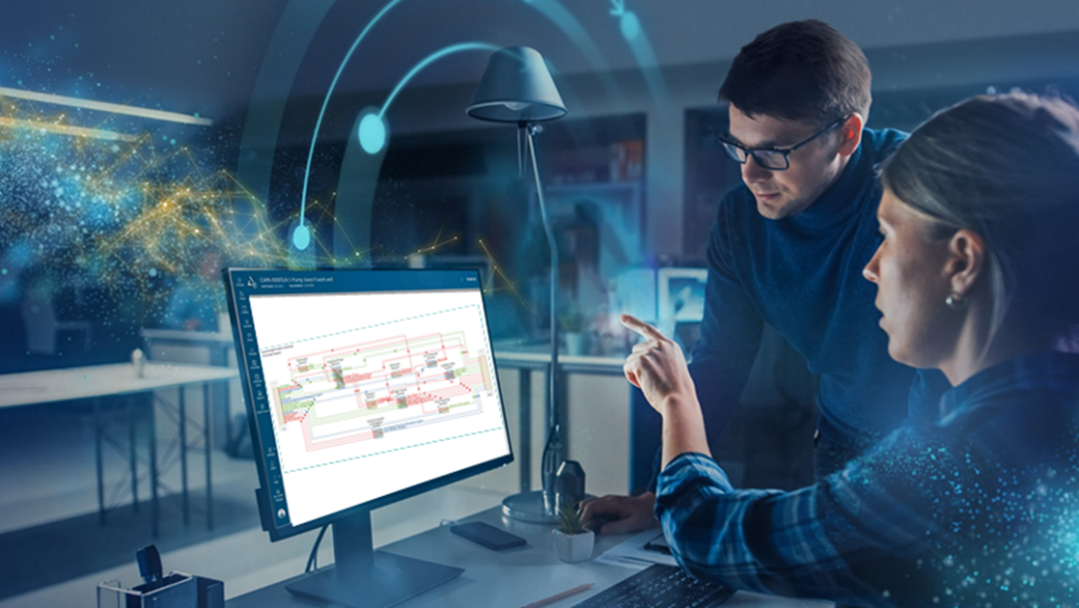
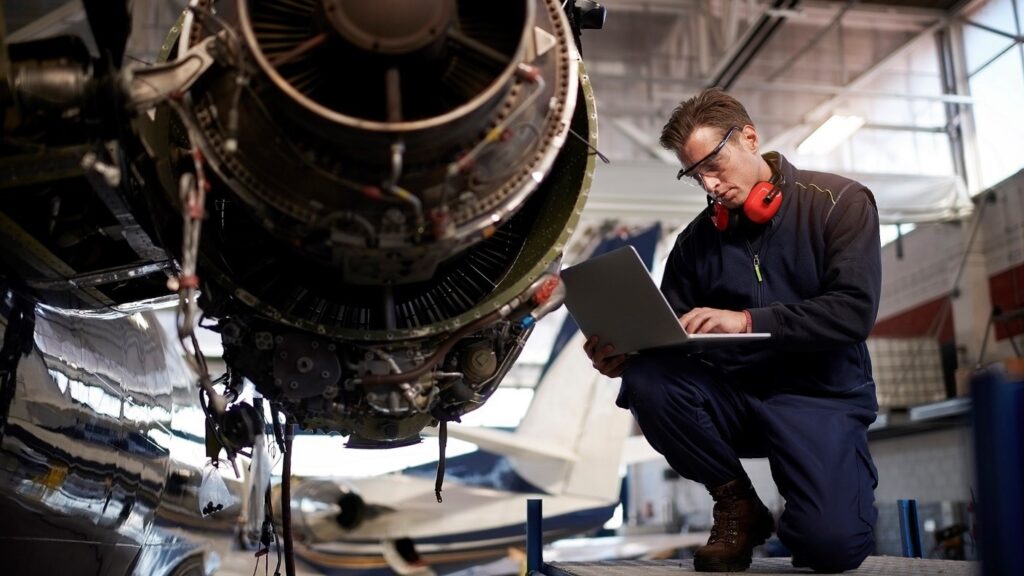
The importance of RAMS in aerospace
Aerospace and defense systems are becoming progressively more complex. It is increasingly challenging to understand how they will perform and when or why they could fail. Meeting these safety and reliability demands requires improved analysis fidelity to support the design process. That means moving away from spreadsheets and manual analysis methods. It means digitalizing your RAMS (Reliability, Availability, Maintainability and Safety) process.
Where operational availability and the cost of ownership are critical determinants of success, organizations developing and operating complex, safety- or mission-critical systems understand the importance of the RAMS function.
Companies must recognize how a digital transformation will impact RAMS. Ultimately, what this potentially means to their current way of doing business. It is essential to validate how a model-based approach that digitalizes the RAMS function can generate significant, demonstrable process and product advantages.
Does your organization need to digitalize RAMS processes?
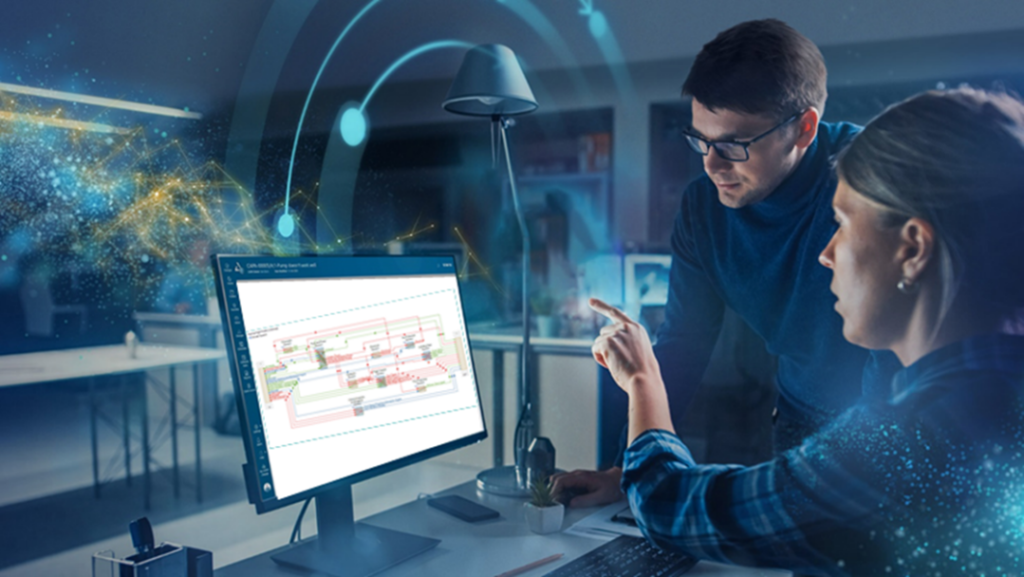
Here are five reasons to apply a model-based approach to RAMS analysis:
1. System complexity: It’s unrealistic to analyze complex systems manually.
With the relentlessly increasing complexity of modern engineering systems, traditional manual methods are no longer practical or realistic. They may not identify and analyze the potential technical risk in a design configuration and then author this into a tool. However, if you don’t efficiently identify and mitigate potential technical risks during the design process, you can’t efficiently design, certify, produce or support your system.
2. Distributed organization structures: Remote workers require digital collaboration.
The pandemic, industry acceptance of segmented design responsibility (‘design enterprises’ involving the supply chain) and the cost advantages of a work-from-home employee base have accelerated the trend to working environments where an engineer may not be physically co-located with colleagues. Successful organizations require technology to ensure that data, analysis methods and processes are consistent, reliable and efficient when used in a distributed work environment.
3. Digital domain knowledge: Learn from your mistakes in previous programs.
If you don’t efficiently capture and then leverage the knowledge and experience of your team, a high-value intangible asset, you lose it when they walk out the door each night or log off in a distributed environment. The ability to integrate domain knowledge into a model-based RAMS solution is crucial in industries where there is an experience gap in the age profile of your team, as well as for long-life programs to communicate design intent and decision inputs.
4. Digital transformation: You are only as digital as the manual elements of your process.
All aspects of a process must be digital to fully benefit from digital transformation (any analog steps limit the expected ‘digital dividends’). Suppose you don’t introduce a model-based approach to RAMS. In that case, it will reduce the overall potential benefits of a digital transformation project. These potential negative impacts increase proportionally with system complexity.
5. Cost benefits and ROI: Realize the demonstrable cost, schedule and technical advantages.
You can achieve demonstrable cost, schedule and technical benefits when your organization applies a model-based approach to RAMS. The specific return on investment and the expected payback period will vary based on the specific circumstances of an organization. Your cost-benefit analysis should reflect the potential cost advantages in the design process (automation reducing resource or scheduling costs for reliability analyses) and during operations (increased system reliability leading to lower maintenance requirements and lower cost of ownership).
Additional benefits of digitalizing your RAMS process
In the push toward industry 4.x, steps in the engineering design process are digitized to move beyond enhanced productivity toward higher agility, real-time opportunities, the development of an innovative capability and genuine innovation.
However, to take full advantage of this trend, organizations must consider the entire product lifecycle management (PLM) process and ensure that every step is digitized, including the RAMS function. Your PLM process is a critical component in designing increasingly complex systems and leveraging the core data of asset operation and performance in the field.
Want to see model-based RAMS in action?
To demonstrate the power of digitalization, we recorded a webinar, where you will learn how a model-based approach helps you speed up aircraft RAMS processes.
Watch the webinar: Achieve aircraft RAMS objectives
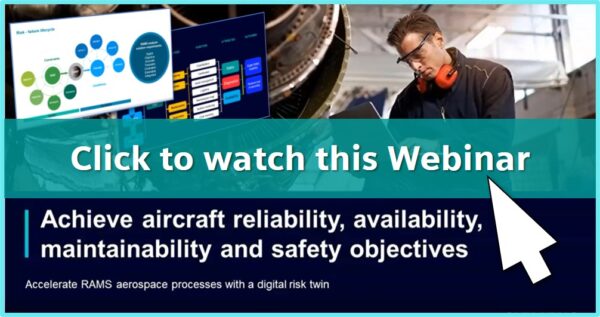
Authors
- Stefan Dutré, Model-based RAMS Product Manager, Simulation and Test Solutions, Siemens Digital Industries Software
- Chris Stecki, Chief Executive Officer, PHM Technology