“Zero-emissions aircraft” series (Ep. #3): Product Design and Building for Certification
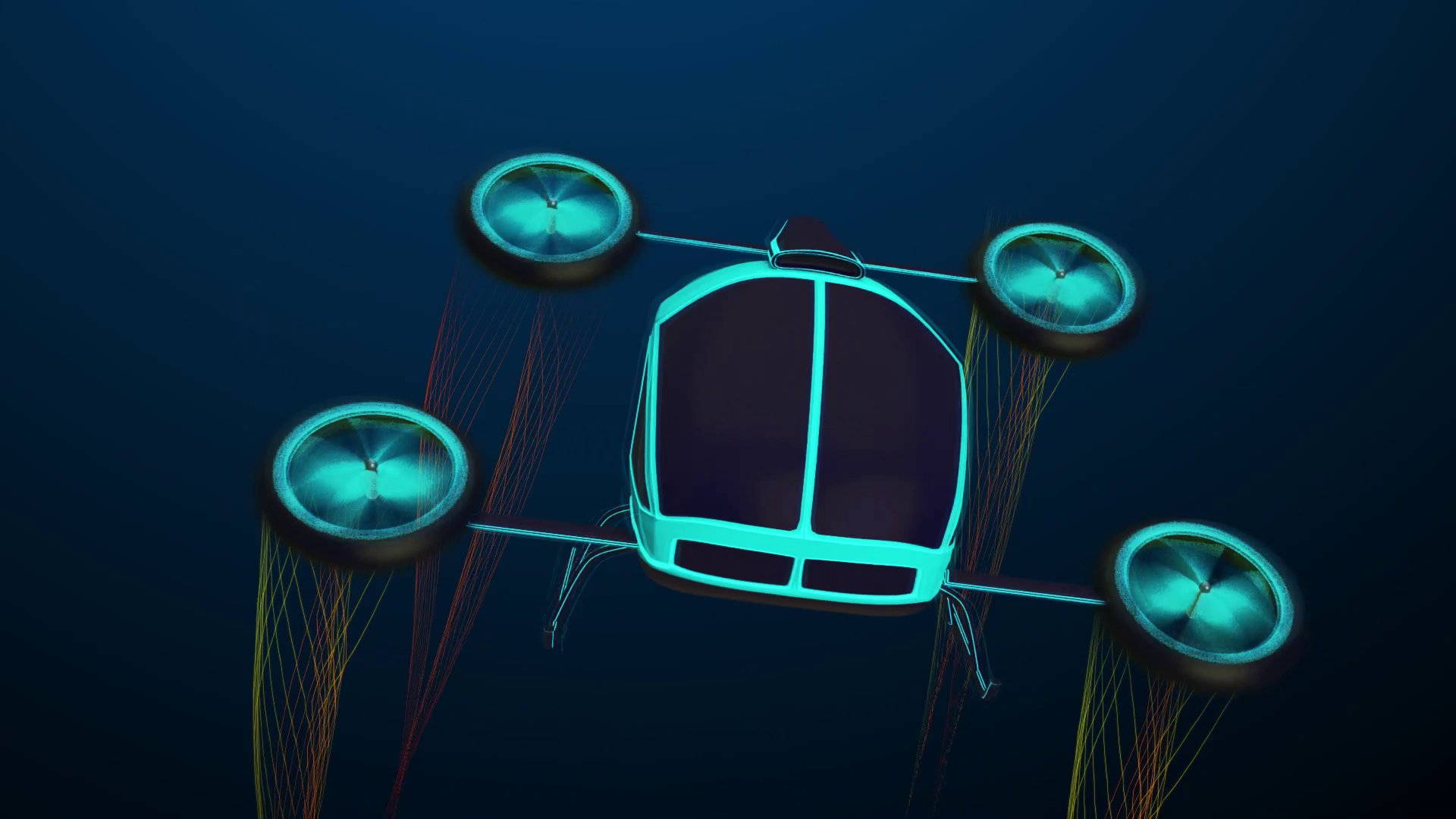
You’ve finalized the preliminary plans for your zero-emissions aircraft… Now what?
Things get interesting in this next stage because this is where product design takes off along with verification and optimization. And yes, manufacturing considerations need to be brought in as well.
And don’t forget, much of what we’re doing here is to ensure a fast and swift certification process.
Welcome to episode three of our five-part series on zero-emissions aircraft. In this episode, we talk about the profound impact the digital transformation can have throughout a number of critical phases in the design and development of an eVTOL aircraft. Understand that pretty much everything we’re talking about is done in serial fashion – all kinds of activities happening in parallel. It’s an exciting time.
Join us as we get into the thick of product development of an eVTOL aircraft.
Listen to the podcast now.
This is episode #3 in a five-part series.
Welcome to Talking Aerospace Today – a podcast for the Aerospace & Defense industry. A place that brings the promise of tomorrow’s technology to the ears of our listeners today.
How do you build a great product and stay within cost and schedule? This is a critical question facing OEMs of zero-emissions aircraft today. And how do you mass produce these things anyway? To build a high-quality air taxi or eVTOL within cost requires the complete optimization of the product – as well as the production process itself.
Today, in our third episode, “The Zero-Emissions Aircraft: Product Design and Building for Certification” we’ll be talking about how to leverage the digital twin to create an optimal design that meets the desired quality and performance standards – and prepares teams for certification. Once again, I am joined by my partner Dale Tutt, vice president of aerospace and defense at Siemens Digital Industries Software.
In our previous podcast, we talked about the variables and trade-offs associated in the early stages of conceptual design. Today, Dale discusses the move out of preliminary design and into the many disciplines and domains associated with product design. We’ll touch on how the digital twin can be leveraged throughout this stage – which includes verification and certification.
I’m your host, Scott Salzwedel, and welcome you to today’s show. In addition to the digital twin, we’ll touch on the digital threads that assist teams during the product design process as we move along deeper product development.
Some really great stuff. I hope you’ll be able to join.
In this episode, you will learn:
- How MBSE digital thread contributes to product design. (07:38)
- The benefits of virtual commissioning. (08:18)
- The role of the digital twin in product optimization. (09:24)
- The processes that should be in place before starting certification. (13:58)
Connect with Dale Tutt:
Connect with Scott Salzwedel:
Resources:
Scott Salzwedel: Hello, this is Talking Aerospace Today, a podcast for the Aerospace and Defense industry. A place that brings the promise of tomorrow’s technology to the ears of our listeners today. And I’m your host, Scott Salzwedel.
Welcome to our new five-part series “The Future of Air Mobility: Zero-Emissions Aircraft.” In our previous episode, episode two, Dale and I discussed conceptual and preliminary design of a zero-emissions aircraft, such as a modern-day eVTOL. We explored various criteria and mission sets required to get our project off the ground.
Well, in this episode we’re excited because we now have the preliminary plans for our new eVTOL. We’re ready for the next stages of product design, verification and optimization. Also, it’s time to get ready for test and certification. How does a company go about doing this in the most cost-effective manner? I read recently where one eVTOL company was planning to spend close to a billion dollars on certification alone, which is just crazy. So, how do you ensure all the requirements are met and that there are no surprises once it’s time for production? What about safety? No surprise that both the digital twin and multiple digital threads are playing a key role here. These are just some of the topics we’ll be covering in this episode “The Zero-Emissions Aircraft: Product Design and Building for Certification.” And I’m pleased to introduce my special guest and partner, Dale Tutt, who is Vice President of Aerospace and Defense at Siemens Digital Industries Software. Welcome, Dale. Thanks for stopping by.
Dale Tutt: Hey, Scott! It’s really great to be here today. Thanks for having me again. I’m always excited to talk to you, but today, I’m really excited because we have our own eVTOL concept, our air taxi. And today we’re going to talk about the product design, optimizing the vehicle and really how to take the necessary steps to make sure that you’re prepared for testing and certification when the time comes.
Scott: It’s going to be a good one. And it’s always a pleasure to have you, Dale. So yeah, speaking of that special little eVTOL of ours, have you thought of a name?
Dale: I’ve been thinking long and hard over this one. But I was going to ask you for the name because usually, we leave that up to the marketing people.
Scott: I gave it a little thought and I’m not sure if any of these names are going fly or not but “DigiSoar”- playing with the digital and soar. But then I thought “DigiSoar” sounds like dinosaur, and we know what happened to the dinosaurs. “eLIFT”, ”Apogee”, of course, “Blade Runner” would be a really cool name.
Dale: That one may be taken by the movie, though.
Scott: Yeah, we’d have to maybe talk to Ridley Scott and see if he’s open for something like that. And then, “Skymate” kind of playing off checkmate, maybe “Skymate?” And then, here’s another one – it was getting late – instead of Siemens, maybe it’s “Airmens?”
Dale: Yeah, maybe you’re right. Maybe it was kind of getting late. Those are some great ideas, we’ll pass those on.
Scott: Yeah, we’ll pass those on. But the good news is we have our aircraft, so we can move forward with product design of our aircraft. And so, it makes sense to turn to the digital threads that we referenced in the previous episode and also the digital twin. We used both the digital thread and the digital twin to extrapolate all kinds of data that we’ll need for this stage.
Dale: Yes, Scott. To start things off, as we start to think about moving to the next phase of program, I really do think we need to think about our Integrated Program Planning and Execution digital thread. And when we think about IPP&E as we call it, how does it pertain to the product design is, you know, the benefit is that the business case and the proposed product plan that was created during the concept design and the preliminary design phase really continue to be the basis for this really robust and executable program plan. You’re not tossing it over the wall and starting over; you’re really building on the foundation that you had established before. And with this, you have a fully integrated plan that incorporates all of the engineering tasks, the tests, the manufacturing tasks, and then incorporates along with that, it includes all of the resource requirements, task durations, the predecessor so that you know the order the tasks need to be worked. And it uses this information to really optimize your resources and really build a schedule with a well-defined critical path that’s been calculated by the system. And so, because you now have this plan in place, you’ve got the details, you have things connected together and integrated together, now you can really get down to work and really focus on executing the program.
Scott: In our previous episode, we were using the MBSE digital thread, which helped us explore the early concepting stage. So, could you share with our listeners how the MBSE digital thread contributes to product design?
Dale: Well, during concept design, as we talked about, we really focused on optimizing the product architecture to really ensure that it met the customer requirements and it could satisfy all the desired mission scenarios that we selected for the vehicle. You know, how far can it fly? How fast? How many people can it carry? And as we moved into preliminary design phase, we really focused on developing the systems architecture. We wanted to make sure that the safety requirements were met, that we had good verification plans and that we were developing the requirements for all of the components that would make up the product – whether they’re structural or electrical boxes, or maybe pneumatic valves that we had requirements for all of those. Now, as we move into the detailed design phase, we really start to focus on component optimization. So, whether it’s designing lightweight structures, maybe defining equipment specs, and the system’s components that make up the aircraft, designing your electronics boxes, the PC boards, developing your software, all of these activities, now, are really the key activities during the detailed design phases. You also, during this phase, you’ll start component qualification and software verification. So you’re verifying that the software and the components work as intended and that the components can survive in the environment that’s intended to operate in. So the temperatures, the vibrations, the altitude – all of these different conditions that the components have to survive in. You’ll probably even start doing some rig testing on a lot of the subsystems. So maybe you do a bench testing on your electric motor to drive the system or the control laws of your software, maybe your testing actuator. So there’s a lot of activities that are really going on during this phase of the program that really support MBSE in the product design.
Scott: I would imagine there are just so many serious issues that need to be addressed. And I would imagine we should also be thinking about manufacturing in this stage. For example, we can start to virtualize the factory floor with the digital twin. Don’t you think that’s a right direction to take at this point?
Dale: Yeah, absolutely. Within this, all of these different systems, there’s thousands of interactions, and there’s thousands of things that are happening. And you need a really great interface management solution to keep track of all the interfaces within the electrical system, all the systems, and all the information that helps define interface. And so, sometimes I think about an interface control document, or the interface is really the contract that maybe you established between suppliers or components, that “box A” and “box B”, they have to talk to each other. They have wires that connect between them. And as odd as this might sound, but you need the same number of wires for both boxes, if they’re going to talk to each other and each box has to have a connector and it has to be the right connector. Sometimes, these physical connections, if you break down there, you have trouble. The signals have to match. If you’re using, say, a CAN bus or an ARINC 429 bus between the boxes, you need to make sure that they’re talking the same language. What words are they using and how’s the data being transmitted? So, people try to manage this manually, but it’s really just not feasible anymore. You just have way too much info. I mean, I think you could do it when you only had a few components and maybe a hundred interfaces. But now you have hundreds or maybe even thousands of components and tens of thousands or millions of interfaces. And you really need to automate how you’re going to manage all of this information.
Scott: Now what about virtual commissioning? Can we touch on that?
Dale: You’re starting to think about the manufacturing piece here, and as we talked about the product digital twin, now we start to move into a little bit of the production digital twin. But the comprehensive digital twin really plays a key role in creating the virtual factory. For companies to be competitive, they need to not only design high-quality products, but they need to be able to produce high-quality products really quickly. And so, they want to manage their production costs and that’s important so that they can competitively price their products. So, with the digital twin, you basically e-build your product long before you ever start building facilities tooling or the product itself. And so, you’re able to get an early look at any issues that you might have before you start committing, say, tens of millions of dollars to a production facility and some of the problems that you might encounter when you start building. So, in this case, with virtual commissioning, you’re avoiding production downtimes that occur when you have to start fixing tools or production line issues or you’re able to avoid unnecessary rework and scrap and have a much more efficient process and a much more efficient line for your production line as your products are going down the production line.
Scott: So as we define our eVTOL more clearly, we kind of begin to optimize for greater efficiency and cost savings. Optimization is just such a critical role here, especially as we get closer to certification and the actual build. Could you talk a little bit about optimization and what that entails at this point?
Dale: Optimization is very critical for an aircraft design and you want to be able to define the best possible product. And so, really, the optimization helps you understand the performance and the safety of your product, of systems, and sometimes even of just individual components. And you want to make sure that it works properly and that you can produce it at the desired cost and also the weight. So, by leveraging the digital twin and using solutions like generative engineering, you’re able to evaluate hundreds of options so you can select the best one. And you’re doing it in so much less time than when you were only looking at a handful of options. And so, the digital twin really helps automate all of the processes that you’re using for optimization between the design and the analysis solutions and the simulation tools – you’re bringing these together, you’re able to optimize them within the digital twin and you’re really reducing the time that’s required to conduct trade studies. You know, in some cases, you’re reducing the time required by an order of magnitude or more, and you’re looking at 10, maybe even a hundred times more options than you did during that time. So, the time savings are incredible with the optimization tools, you end up with a much better, much stronger product.
Scott: And what about the vehicle structure itself? You mentioned generative engineering already, and I’m sure that plays a huge role. There’s just… Composites. That’s very big right now. Have we fully simulated various composites for the strength and weight and cost? And then aerodynamics I’m sure are very critical, very important. With so many domains involved in this phase, in particular, how does all the data stay connected? I mean, how do these teams share and collaborate to make it all work?
Dale: Yes, the processes themselves have been simulated and automated, and they’re very well connected. And you point to, you know, a composite solution. And, really, nowadays, companies are looking at how do they go from the initial requirements throughout the entire composite design process, and then seamlessly transition it into your manufacturing phase. And so, the digital twin plays a very significant role in this process. And it’s that rich, robust understanding of the product that you have – that is provided by the twin – that really allows you to optimize across these many domains faster. So, you mentioned aerodynamics, and strength and weight. And so, to get the aerodynamics you need, you might have some pretty complex shapes. And so, you need to be able to look at balancing the shape with the structure so that you don’t end up with a solution that is too heavy. And I can think of examples in the past where you start making trade-offs between aerodynamic drag and weight, and both of them have an impact on the performance of the aircraft. And so, using some of these generative design tools, and the optimization tools, you’re able to look at different shapes in the drag, and then you’re able to balance that against the weight of the part, and then you’re able to find kind of the optimum solution that produces the aerodynamics that you need to have, but also that gives you the weight that you need to have. So, as you do all of this, though, it’s very important to manage the configurations of the design and all the analysis models, because you need to make sure that everything stays in sync, that you’re analyzing the same thing for aerodynamics and for, say, your stress analysis. And so, you can use a digital thread to help manage all of these configurations, but also to manage the transitions as you move between, say, your CFD models and your stress analysis, and your design all these different applications that are used. And so, you’re able to manage these transitions and really keep them within an integrated solution, integrated multi-domain solution, really. And I guess the last thing I was going to say about that is that you automate these processes with the generative design. Now, you’re freeing up your engineers to really focus on solving these complex problems, really boosting their innovation instead of managing data and wondering if they looked at everything that they needed to look at. And so, because you’re able to look at so many more options and do it so much faster, and have that seamless transition, it really does free your engineering team up to really focus on what they do best, and that’s designing cool products.
Scott: Yeah, that makes a lot of sense. Let’s talk about test and certification. There’s just a lot of complexity going on here and I would imagine we have some rather strict product and manufacturing requirements to follow.
Dale: You need to be able to take and flow all these manufacturing requirements into the design. So, as part of certification, you’re also thinking about your manufacturing requirements because you have to build what you said you’re going to build so that you can actually certify and demonstrate that you have a solid, robust process of designing and building products that you can then deliver with confidence to your customers. And so, there’s a number of processes that you have to have in place as you start to satisfy all these requirements. So, you’ve got to have a very well-established model-based analysis and certification process in place, you have to be able to manage the test execution and keep track of what the configuration of your test article is, their version of your test procedures, your test plans — all of these things need to stay in sync so that you’re testing the right thing. The process for verification management, which we’ve talked about a little bit, is really key. And then, just really being able to manage all these interfaces between all of these different systems on your aircraft, as well as between all your different suppliers. And so, having all that information, you kind of think about all these highways flowing together that come into the same place, and they go through your certification process. And so, it can be a pretty complex process.
Scott: Is there a digital thread that manages all this?
Dale: Maybe it’s a couple of threads in some cases, but a big chunk of this maybe starts with, say, the MBSE digital thread, and also the Verification Management digital thread. So, because you have a good systems engineering process in place, you’re able to use the MBSE digital thread that we started talking about, you know, in the last episodes; you have the requirements and you have verification plans. So, you have product-level requirements, you have system-level requirements, and then you have component-level requirements. And you’ve got verification plans in place for each one. And so, when you think about when those requirements were first written in the concept design phase, they haven’t gone away, you still have to validate them. But because now you’ve digitalized all these different domains, we’re really able to then use this information to go smoothly in the certification. And that’s then where the Verification Management digital thread comes in place because your systems engineering process managed all those requirements and the development of the systems solutions that came out of those requirements. But then the Verification Management solution is now saying, “Okay, for every requirement, I have a plan, and this is how I’m going to show compliance.” And so, it really does tie it all together.
Scott: I would imagine that sets us up for a rather easy transition into production.
Dale: Absolutely. I mean, you have the requirements, you have your product architectures in place, you know what you’re building, you know what you need to go test. And so, as you transition in production, you may still be going through your certification process, but you know that you have consistency and configuration control between what you’re testing in the certification process right now, and what you’re building. So, these are often parallel processes. They’re not serial processes. And so, you’re able to use a Verification Management digital thread even to help manage that process as you go into production. And so, you have continuous verification using digital tools of both your product and your production processes, you’re keeping everything in sync with the digital threads, you’re constantly evaluating all of your systems and solutions to ensure that you’re meeting the intended requirements. And if you have changes along the way, which is inevitable, you find something that has to change, you now have the visibility because you have the digital thread through your test articles, as well as into your manufacturing line, to make sure that you can make the most informed decision possible. So, in every program, you’re going to build a few prototypes that are going to be certified during the production using the production digital twin and the product digital twin. So, when it’s time to move in your production ramp up, you’re going to be able to move smoothly into production because you have all of this information coming together.
Scott: Very nice. Very nice. You hit the nail right on the head there because that’s the topic of our next podcast: production.
Dale: Yeah, precisely. I mean, I think ultimately, every company out there, whether they’re building an eVTOL or they’re building a new electric aircraft, or a new supersonic aircraft, or a new rocket to go into space, they want to build and deliver a product. And while good, solid engineering is a key element to getting there, the end goal is to have a seamless transition from engineering into production so that you can cost-effectively build your product and start selling it to customers.
Scott: Exactly. So, I think the beauty of what we’re talking about here is really the digital feedback loop – it’s like a closed-loop process that includes both digital threads and the digital twin and also, this data that gets built on top of data, on top of data. And it’s all traceable. And then it encourages this collaboration that we’ve been talking about between teams that otherwise might not talk to one another. So it’s really fascinating what’s happening here. And I would imagine a lot of this has to do with what we call the IPP&E digital thread?
Dale: You’ve captured it really well. I don’t know that I could have said it any better myself. There’s a lot of data to manage. Being able to manage the configurations of all of this data is important and really having a robust program management process with IPP&E, it really can make the difference for a program as you go forward.
Scott: Well, Dale, our time is up for this episode. We touched on so many fascinating topics today.
Dale: Yeah, it’s been a great discussion. But, as you said, it’s on to production and on to the factory floor and we’ll even talk a little bit about how we maintain the life of our air taxi once it’s out in the field.
Scott: That’s so very important these days. Really good stuff, Dale. Thank you so much. So, at the top of the show, I mentioned that this is a five-part series on zero-emissions aircraft. If you enjoyed the episode and you’d like to listen to future episodes, please subscribe to Talking Aerospace Today on Apple iTunes, Spotify, or wherever you go to get your favorite podcast. You can also check out the links in this podcast description.
My name is Scott Salzwedel, and this has been Siemens Talking Aerospace Today. I hope you enjoyed the show and that you’ll join us again for our next podcast. Until then, bye for now.
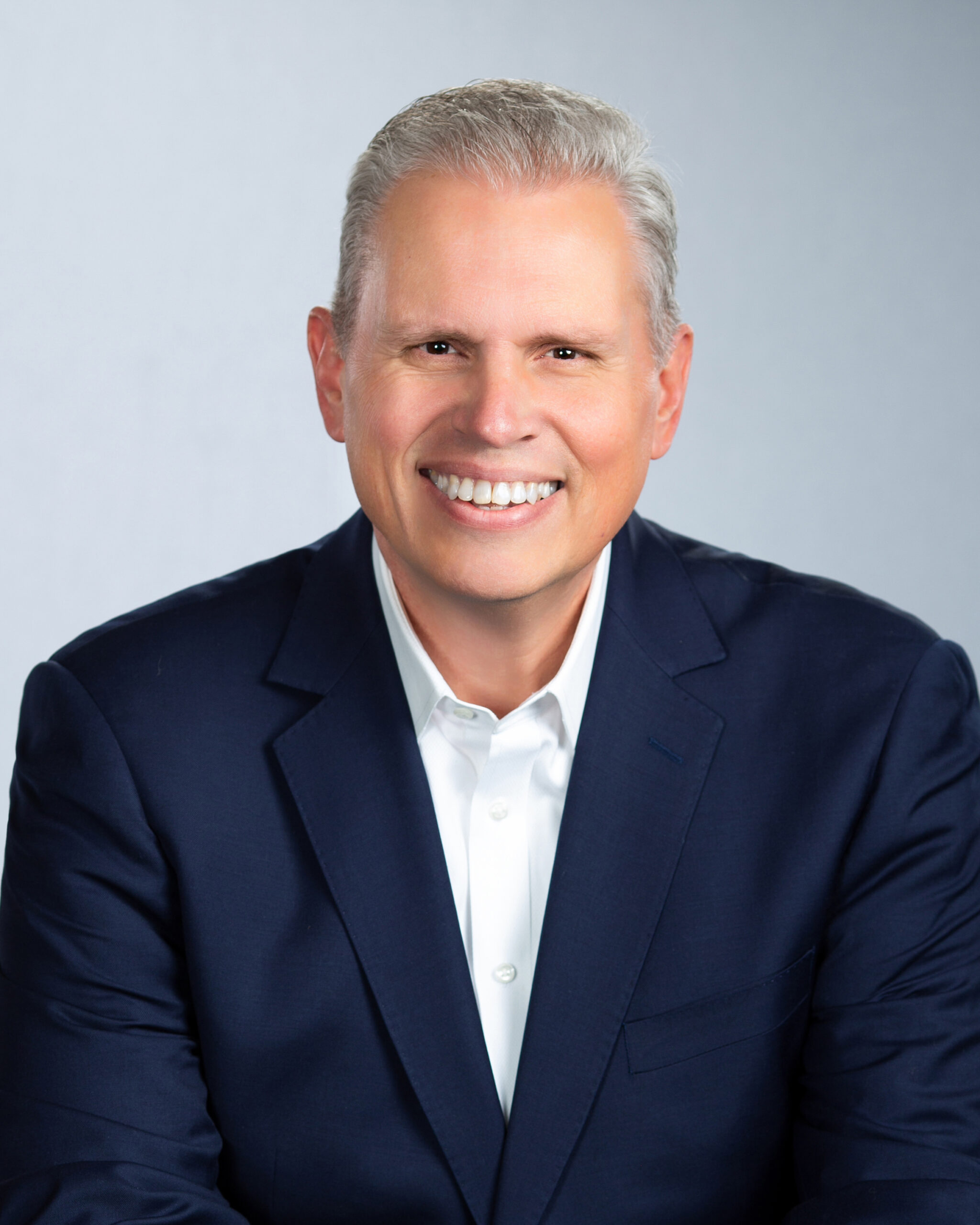
Dale Tutt – Vice President of Industry Strategy at Siemens Digital Industries Software
Dale Tutt is Vice President of Industry Strategy at Siemens Digital Industries Software. Dale leads a team of experts to develop and execute industry-specific product and marketing strategies in collaboration with the global product, sales, and business development teams. With over 5 years of experience in this role combined with extensive experience in the aerospace and defense industry, Dale has a deep understanding of the challenges and opportunities facing companies as they embark on their digital transformation journeys.
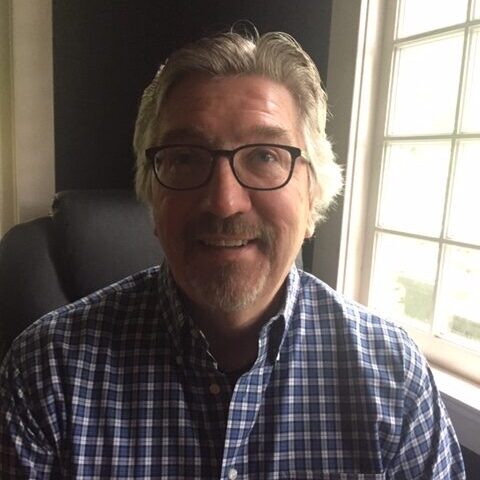
Scott Salzwedel – Host
Scott Salzwedel is senior technical writer and corporate communications writer involved in the Siemens Aerospace & Defense Industry and Siemens Capital. In addition to writer/host of Talking Aerospace Today, Scott is the writer of white papers, articles, blogs, videos and websites at Siemens.
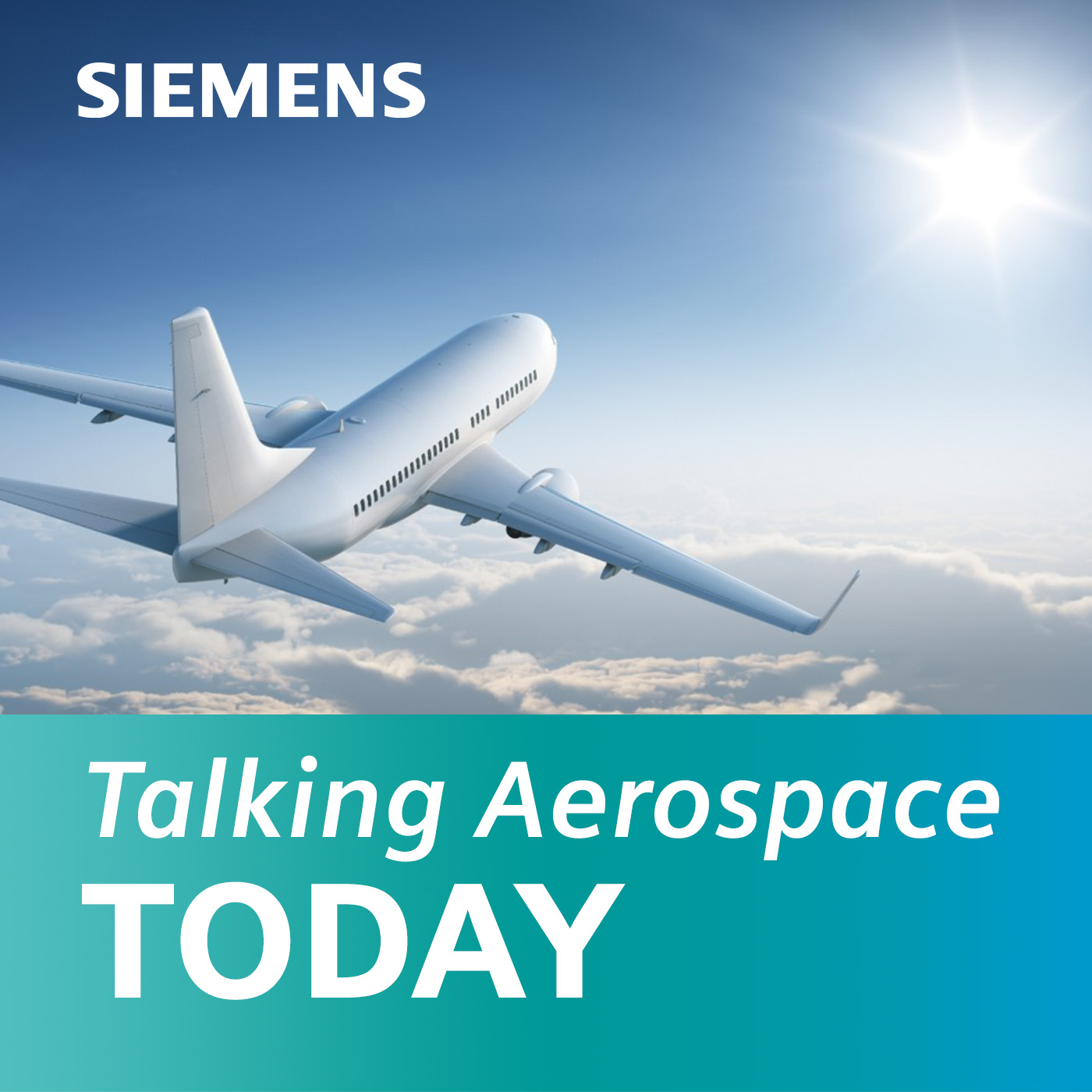
Talking Aerospace Today Podcast
The A&D Industry is at a serious inflection point. Transformation to the digital enterprise has opened up a new era in innovation and technological breakthroughs. However, complexity and compliance continue to hamper the best of efforts.
Join us as we explore how Siemens is turning complexity into a competitive advantage for many of our customers – today and well into tomorrow.